Building a chipmaking fab in the US costs twice as much, takes twice as long as in Taiwan
U.S. and Europe need to adopt new construction techniques to be competitive.
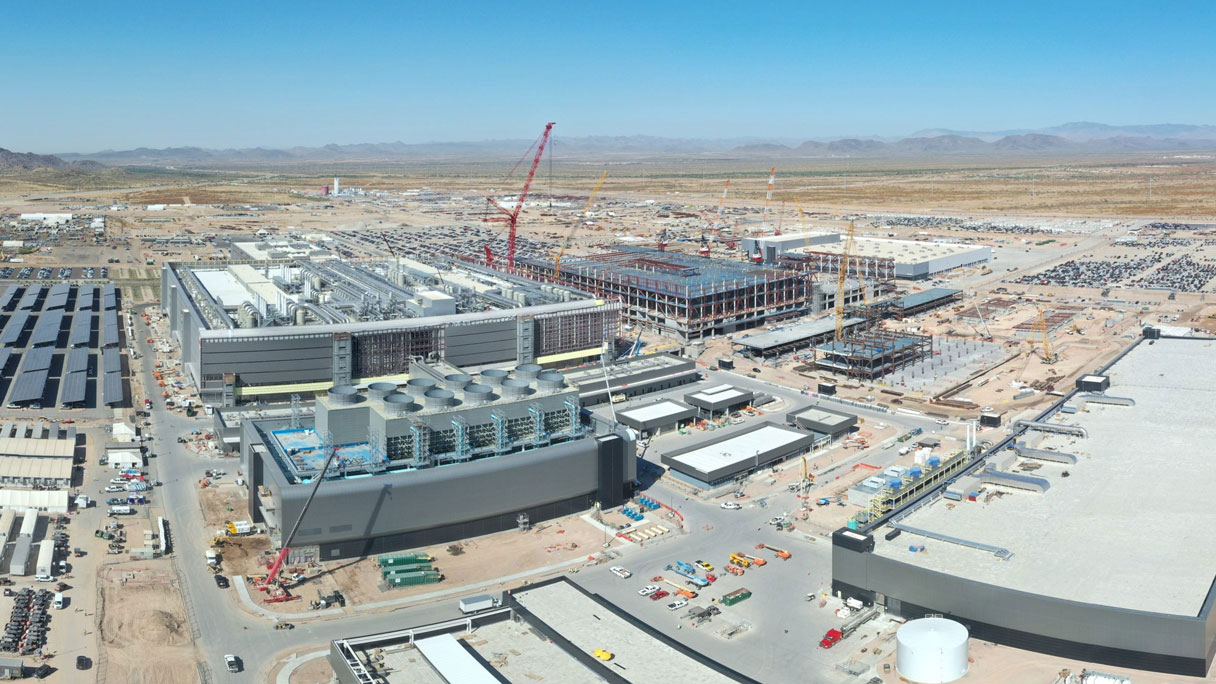
The semiconductor industry is expanding rapidly as countries race to build new fabs. While it takes around 19 months to build a fab in Taiwan, it takes a whopping 38 months to build a fab in the U.S. due to the extensive time it takes to get a permit and because fabs are not constructed 24/7, according to Exyte, a leading engineering, construction, and design company that specializes in high-tech facilities like chip production plants, reports Semiconductor Digest.
Region | Permit & Design (Months) | Construction Start (Month) | Construction Duration (Months) | Total Duration (Months) |
USA | 14-20 | 14 | 24 | 38 |
Europe | 10-18 | 10 | 24 | 34 |
SEA (Singapore & Malaysia) | 7-15 | 7 | 16 | 23 |
Taiwan | 6-13 | 6 | 13 | 19 |
Taiwan completes fabs in around 19 months, followed by Singapore and Malaysia at 23 months. European projects take 34 months, while the U.S. is the slowest at 38 months. A key reason for this is Taiwan's streamlined permit process and round-the-clock construction, whereas the U.S. and Europe face delays in approvals and do not construct 24/7. The U.S. has enacted a law that exempts certain U.S. fabs from federal environmental assessments, but that is obviously not enough to be on par with Taiwan.
Costs also differ widely. Constructing a plant in the U.S. is about twice as expensive as in Taiwan, despite similar equipment costs, according to Exyte. This discrepancy arises from higher labor costs, extensive regulatory requirements, and inefficiencies in supply chains. Also, Taiwanese workforce is highly experienced, so Taiwanese builders require fewer detailed blueprints because they are familiar with every step of the process, which speeds up completion of fab projects, according to Herbert Blaschitz, an executive at Exyte.
To compete efficiently with Taiwan — which has a well-integrated supply chain, experienced workforce, and efficient regulatory processes — the U.S. and Europe must streamline permitting, optimize construction techniques, and adopt advanced planning tools like digital twins. Blaschitz suggests adopting 'virtual commissioning,' where a digital model of the plant is created before physical construction begins. This allows potential problems to be identified early, reducing costs and environmental impact while improving speed and efficiency.
Modern semiconductor production facilities are huge, both in terms of dimensions and investments. A leading-edge fab — such as those operated by Intel, Samsung Foundry, or TSMC — requires investment exceeding $20 billion, with $4-6 billion allocated just for the structure itself, according to Blaschitz, who highlighted Taiwan's advantages at the SEMI Industry Strategy Symposium.
The construction process involves 30-40 million workhours, using 83,000 tons of steel, 5,600 miles of electrical wiring, and 785,000 cubic yards of concrete, according to Blaschitz. A typical fab may include a 40,000-square-meter cleanroom with 2,000 production tools used for lithography, deposition, etching, cleaning, and other operations. Each of the tools requires around 50 individual utility and process connections.
Get Tom's Hardware's best news and in-depth reviews, straight to your inbox.
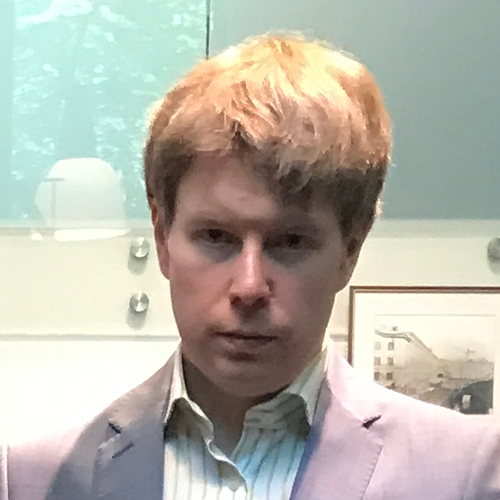
Anton Shilov is a contributing writer at Tom’s Hardware. Over the past couple of decades, he has covered everything from CPUs and GPUs to supercomputers and from modern process technologies and latest fab tools to high-tech industry trends.
-
Shiznizzle I did recently read on this matter.Reply
The extra time, some of it, can be attributed to environmental regulations which are not really worried about in Taiwan. At least not on the same level as the US worries about it.
The weird thing is that fab in Arizona still has to ship its chips back to Taiwan to "finish". Whatever that means. Packaging? Attaching the IHS and packaging? Only for the chip to be shipped back again? Seems silly, all this shipping.
You have a fab but still cant make it on your own. -
A Stoner Florida recovers from hurricanes 98% faster than non-coastal states. I am sure the USA can gain some efficiencies once we start actually building enough fabs and when it becomes a large enough part of our economy to matter much.Reply
Taiwan's GPD is 15% chip manufacturing. Obviously they are going to have the best efficiencies there are on these.
For reference, if the United States took 100% of Taiwan's current chip manufacturing into its GDP it would be about 0.7% of our GDP. -
A Stoner
The shipping will end once America has enough fabs to keep the packaging plants busy and we build some, at double the cost and twice the time.Shiznizzle said:I did recently read on this matter.
The extra time, some of it, can be attributed to environmental regulations which are not really worried about in Taiwan. At least not on the same level as the US worries about it.
The weird thing is that fab in Arizona still has to ship its chips back to Taiwan to "finish". Whatever that means. Packaging? Attaching the IHS and packaging? Only for the chip to be shipped back again? Seems silly, all this shipping.
You have a fab but still cant make it on your own. -
bit_user
Is this before or after "the U.S. enacted a law that exempts certain U.S. fabs from federal environmental assessments"? That article is dated Oct. 2024, so I'd guess the law is a response to whatever you read about.Shiznizzle said:I did recently read on this matter.
The extra time, some of it, can be attributed to environmental regulations
It seems to me like 24/7 construction has got to account for a lot of the difference.
There's been talk of TSMC building a packaging plant in the USA. This, I think:Shiznizzle said:The weird thing is that fab in Arizona still has to ship its chips back to Taiwan to "finish". Whatever that means. Packaging? Attaching the IHS and packaging? Only for the chip to be shipped back again? Seems silly, all this shipping.
https://www.tomshardware.com/tech-industry/amkor-and-tsmc-team-up-for-advanced-packaging-in-the-u-s-cowos-and-info-to-make-ai-and-hpc-cpus -
lmcnabney The environmental regulations are there on purpose you know. Chipmaking is pretty much the most toxic industry on Earth if you exclude the nuclear industry.Reply -
kcw It is more interesting to know why it is the case.Reply
What is the average size of fab in each region? Also what are the average duration for other type of buildings?
Does it attribute to the distance that construction materials and utilities have to travel? -
Giroro According to Google's AI, the average construction worker in Taiwan gets paid between $10,800 - $11,880 per year. In America the average construction worker gets paid $52,333.Reply
So with over 4x the money going to workers and much more regulatory oversight, they are only paying twice as much for construction? I'd say they're getting a tremendously good value for their dollar. Each employee would have to be getting a lot more work done to cut those costs. American employees must be performing more efficiently to get the same amount of building done with what must be fewer workers - which is a win. The longer amount of time overall is just a matter of limiting the building to daytime hours - which is more humane, saves cost on lighting, and safer.
Besides, if it takes longer to build the building, who cares? The equipment inside the buildings need to be bleeding edge, not the steel and concrete of the building itself. -
bit_user
One thing I've heard is that big public works projects are just a lot more expensive in the USA that just about anywhere else in the world, including Europe! That's been cited as one of the reasons we tend to have worse public transportation, for instance.kcw said:It is more interesting to know why it is the case.
What is the average size of fab in each region? Also what are the average duration for other type of buildings?
Does it attribute to the distance that construction materials and utilities have to travel?
I do have to wonder how much of it is to do with organized crime. Probably not much, but there are certain types of business, like cement, which have long been havens of mob and other corrupt dealings. Certainly, in places like NYC, you basically can't do any sort of construction or sanitation without a certain amount of the money going to the mob. -
bit_user
Needs a proper source. Not to mention the fact that the types of construction workers used to build fabs are likely very experienced specialists and making well above what the average home builder makes, for instance.Giroro said:According to Google's AI, the average construction worker in Taiwan gets paid between $10,800 - $11,880 per year. In America the average construction worker gets paid $52,333.
If that fact is wrong, you're building on a rotten foundation. Garbage in; garbage out.Giroro said:So with over 4x the money going to workers and much more regulatory oversight, ...
It has to do with financing these projects, I think. The longer it takes to achieve a return on investment, the more difficult it is to raise capital and the more expensive that financing becomes.Giroro said:Besides, if it takes longer to build the building, who cares? The equipment inside the buildings need to be bleeding edge, not the steel and concrete of the building itself.
Also, the longer it takes to build new capacity, the harder it is to time against demand. Semiconductor manufacturing is a very cyclical business. If you bring a lot of new capacity online at the bottom of a business cycle, it could be disastrous, because that production has only a short time to pay for itself before it becomes obsolete. Similarly, if you can't get new capacity online to take advantage of the top of the business cycle, then you lose out on the gravy train. -
husker The additional time and cost do come with benefits as well; although not to the project itself but to society in general. Yes, I'm sure there is some waste, but things like wages, safety, environment also play a role.Reply