Almost a Month Later Contaminated WD, Kioxia NAND Fabs Resume Operations
Almost a month after the contamination was detected.
Western Digital and Kioxia have issued an update, via EE Times Japan regarding the contamination issues that hit their Japanese NAND fabrication plants earlier this year. The event resulted in around 7 exabytes of 3D NAND memory being contaminated, and thus unfit for shipment and integration in actual products. The companies have now announced that the impacted facilities - namely the Yokkaichi Plant (Mie Prefecture) and Kitakami Plant (Iwate Prefecture) have now resumed their normal operations - almost a month after they were brought offline.
Following the contamination and factory closures, Western Digital has already revised its revenue and profit estimates for Q3 2022. Western Digital now expects to bring in around US $ 4.2 billion to US $ 4.4 billion, down from original estimates of US $ 4.45 billion to US $ 4.65 billion - a $250 million impact (around 6%) in the company's bottom-line for the quarter.
That still doesn't include the estimated $250-$270 million cost of trying to recover the affected NAND dies - remember that the companies already invested in the required materials and manufacturing processes. Recovering as much of the affected NAND as possible seems to be the smarter, most economical move - even if it does bring about additional, unplanned expenses in bringing them back towards usability.
The 7 exabytes of unusable 3D NAND represents around 3.38% of the total annual NAND production for 2021, which came in at a mind-boggling 207 Exabytes spread over 333 million SSDs. But that only refers to the actual contaminated NAND, and doesn't take into account the 21 days the factories were offline. Due to the contaminated NAND, guidelines for NAND pricing have been revised - those 7 exabytes alone account for around 13% of global NAND production for Q3 2022 (January-March); market analytics firm TrendForce expects NAND pricing to increase anywhere from 5% to 10% due to the lowered supply.
It's unclear much more impact could be seen in NAND supply and pricing when one takes into account the factories' downtime - NAND chip fabrication might be simpler than fabricating CPUs or other highly-complex semiconductors, but production times from the beginning of the process until a finalized NAND chip leaves the factory floor still take anywhere from two to three months. Semiconductor manufacturing is a fickle process; even with redundancies and a number of quality control checks between receiving prime materials and processing them until an actual wafer is finished, any impurity has a disproportional impact on yield and production.
Get Tom's Hardware's best news and in-depth reviews, straight to your inbox.
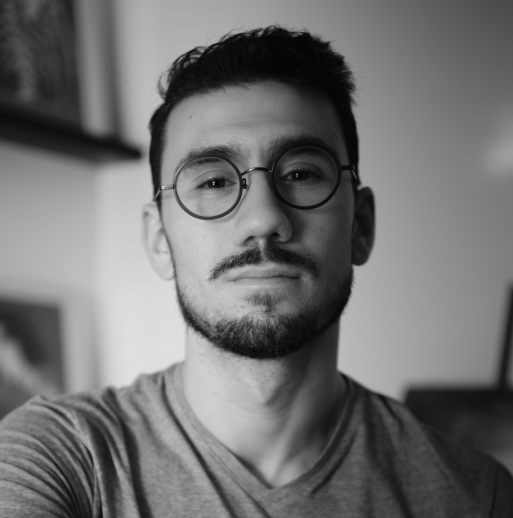
Francisco Pires is a freelance news writer for Tom's Hardware with a soft side for quantum computing.