TSMC's labor practices draw serious concern in Arizona — the company's new chip plant allegedly plagued by worker abuses
TSMC not a hit with American hires
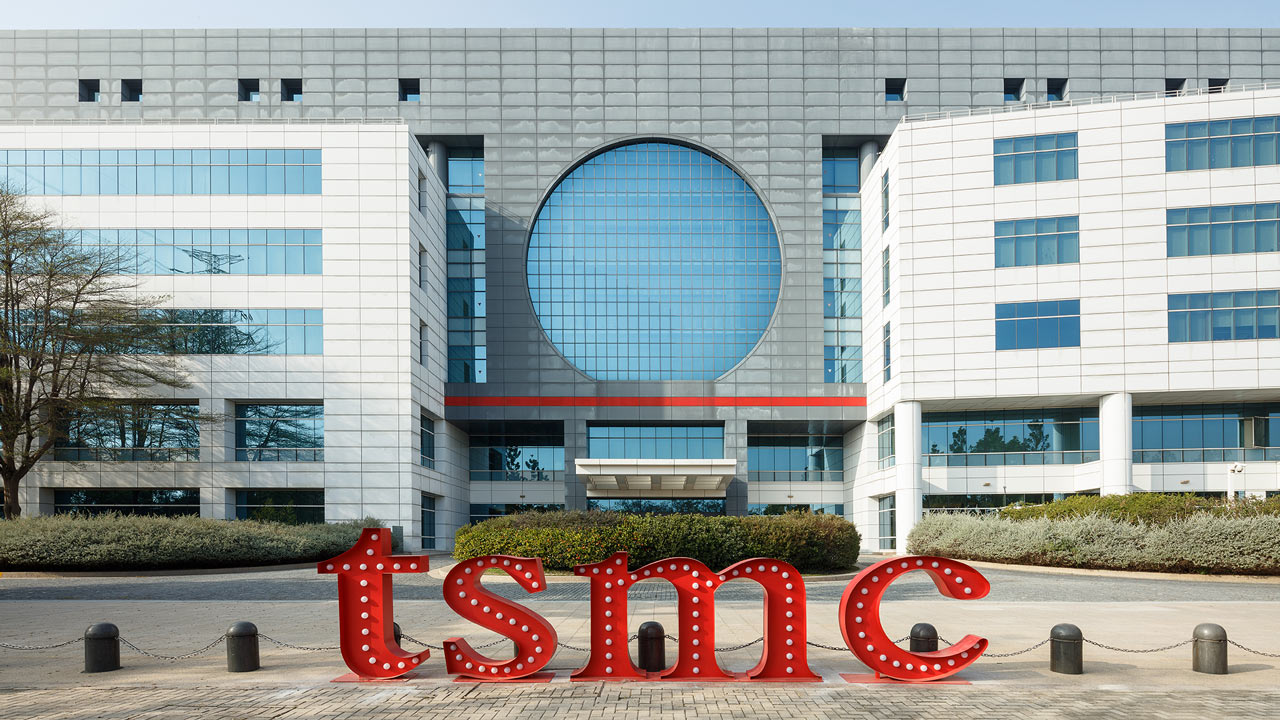
TSMC's new expansion into Arizona has received serious scrutiny from engineers and industry insiders for its myriad examples of poor treatment of workers, reports nonprofit news site Rest of World. The article claims the company's culture of chronic overwork, cruel managerial style, and poor treatment of its engineers in its Taiwanese plants has ported over poorly to an American labor force who are now leaving its new plant over perceived abuses.
Taiwan's darling comes to the US
TSMC, the world's leader in advanced chipmaking, has been a major recipient of the Biden administration's CHIPS Act, receiving billions of dollars from the US government in exchange for bringing semiconductor production to the United States. The corporation's position as the largest company in Taiwan is a concern for Western powers who fear a conflict with China could potentially hurt their ability to source TSMC chips. As a result, the government has been aggressively courting TSMC to open production in the US.
TSMC's $660 billion stature has grown to the largest company in its native Taiwan and has earned it godlike reverence, being called a "divine mountain that guards the nation" by some citizens. As a result, its Taiwanese workforce is more than willing to make sacrifices for the sake of the company. 12-hour workdays that extend into the weekends are common, as is harsh treatment from managers who were expected to call workers out-of-hours and reportedly threaten firing as punishment for relatively minor failures. This work culture can survive in Taiwan, where TSMC is the pinnacle of engineering jobs, but when American engineers are introduced, friction occurs quickly.
Labor abuses drive away new workforce
American engineers were brought to Taiwan back in 2021 to be trained in TSMC chip production for when the two new expansion plants in Arizona (originally set to be opened in 2024 and 2026) would begin operation. The report says American engineers were shocked to encounter the 12-hour workdays and a high-pressure environment; one engineer asked their manager which of his tasks was of the highest priority, which was met with the response, "Everything is a priority."
The inability to prioritize jobs and instead expect furious intensity on every task, no matter how large, was decried by Americans as poor management, which leads to inefficiency. But these intense expectations are a feature of company culture according to its founder, Morris Chang. Chang was quoted by Rest of World as saying, "If [a machine] breaks down at one in the morning, in the U.S., it will be fixed in the next morning. But in Taiwan, it will be fixed at 2 am." This marriage to impossible timelines was pounded into visiting American engineers with stress tests; assignments announced on the same week or even day to ensure American engineers could sacrifice personal time like a Taiwanese worker.
Once production on the Arizona fabs progressed far enough, American workers were brought back stateside along with their Taiwanese coworkers. But construction ran into many delays, with both fabs currently around a year behind schedule. Many Americans left TSMC in their training phase in Taiwan, and retention fell further after returning to America and finding that the company work culture remained even at the new plants. Engineers who expected to work on the production lines found themselves being tasked with taking out the garbage of construction workers. Taiwanese managers even reportedly had to receive training on not yelling at workers in public, which didn't stick. The workers claim that engineers found that they had to fake test results on production wafers in order to meet their impossible expectations.
TSMC's future in the US
Taiwanese workers who have become accustomed to such workforce rights violations and American workers used to complaining or quitting over the same conditions have not been able to fully mesh. Americans complain about "Asian culture" on Glassdoor, and Taiwanese engineers consider their native coworkers arrogant and carefree. This friendly fire between workers is heartbreaking to those who know that the only enemy in such a situation is not their fellow workers but the corporation that enables such workplace abuse.
Get Tom's Hardware's best news and in-depth reviews, straight to your inbox.
TSMC is not expected to slow down anytime soon, even with such worker rights abuses drawing ire. It will be able to charge consumers higher prices for its made-in-America parts, and the 12-figure CHIPS Act funding alone will provide ample incentive to keep trying to make the Phoenix expansion work. Hopefully with time comes a better workplace for engineers. For more on this situation and direct quotes from the engineers in question, read the Rest of World's original story here. For more on TSMC, consider reading about how TSMC has been helping Taiwan in the wake of its recent earthquakes.
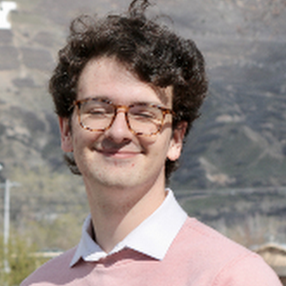
Sunny Grimm is a contributing writer for Tom's Hardware. He has been building and breaking computers since 2017, serving as the resident youngster at Tom's. From APUs to RGB, Sunny has a handle on all the latest tech news.
-
hannibal And then we wonder why work places goes to East...Reply
It is compete or die... And competition is lost in most places in the Western world.
Not sure if there is any good solution to this problem. A company that takes most out of its workers... wins the price competition. Unless people decide to pay more, for less good products that are made in the west.
Or the laws protecting the workers has to be so strict that Eastern companies are not interested in investing in western countries...
First it was low tech industry... not it is high tech also... USA car manufacturers are also losing the race... Soon no workplaces outside cafe shops and crockery markets. -
TechLurker I'm of 2 minds on this.Reply
On one hand, Asian work ethic IS very strict, head to the grinder, and somewhat rigid, but it gets the job done efficiently and on-time with few defects. Foreign workers should have expected this going in, knowing it's going to be run Asian style instead of Local style, especially for a high profile Asian company looking to quickly ramp up after delays.
On the other, America does have its own unique work ethic, and depending on who you ask, is either seen as better or worse when it comes to the end product. And given that the facilities will be in the US, TSMC should have had some leeway to accept lower performance/output from the US side both due to cultural differences and the usual teething issues with new staffing.
It seems that TSMC is already predicting lower output, hence their upcoming premiums on anything made not in Taiwan effectively limiting said facilities to only producing government chips (which was the main point anyway).
As well, based on a few samles of the complaints from both sides, the Taiwanese employees complain the Americans are acting entitled and complaining too much about working hard or wanting a lower bar of standards to be held against, while the Americans are complaining that TSMC is basically too strict, borderline abusive, and demanding too much for 12 hours of focused work.
All that said, I'm reminded again of why there aren't that many companies that can cross the East/West culture/work gap (heck, it's hard enough to cross the American/European culture/work gap), and this wouldn't be the first time this happened either. It took Sony decades to make leeway for Western culture and they had their own fair share of internal issues, but they did eventually adapt and get a Westerner to become CEO for their Playstation division. -
35below0 The inability to prioritize jobs and instead expect furious intensity on every task, no matter how large, was decried by Americans as poor management, which leads to inefficiency. But these intense expectations are a feature of company culture according to its founder, Morris Chang.
That's one way of doing it. Our western parents and grandparents went through excesses of capitalism. That's why the work day was shortened, people were not worn out and broken down by the age of 25, and worker unions formed to put employer power under control.
Morris Chang might have built up a huge company but he still has a lot to learn and probably to answer for.
Chang was quoted by Rest of World as saying, "If breaks down at one in the morning, in the U.S., it will be fixed in the next morning. But in Taiwan, it will be fixed at 2 am."
It will be fixed by 2 am anywhere. Anywhere the engineer is paid to be on call. It has nothing to do with company "culture", only with the work agreement.
Of course, there are lazy good for nothings coasting and doing as little as possible in every company. Instilling a "culture" of rewarding hard work and punishing laziness is not itself wrong.
Building a massive complex and hiring engineers only to later find out the work conditions are unacceptable is a slap in your own face Mr. Chang. It's YOUR job to see it coming and fix it before it happens.
Responsibility must be taken up at all levels.
It really irks me that people in positions of authority resort to blaming their underlings when those underlings, no matter how clumsy, lazy or left handed are their own responsibility. -
hotaru251
not really.TechLurker said:And given that the facilities will be in the US, TSMC should have had some leeway to accept lower performance/output from the US side both due to cultural differences and the usual teething issues with new staffing.
most of the $ is out of their pocket.
If they accept less than expected results they lose $ every day.
Theres no benefit to of even making the fab at that point.
If someone got a job at an authentic Chinese food place and didnt know how to use a wok...are the bosses suppsoed to accept that? no as again they are a business & it harms them.
While it does suck (on both sides) US will have to accept the asian culture for the job and if they cant don't apply. (simple even if not the ideal outcome) -
bluvg This type of work environment wasn't uncommon in the West during the Industrial Revolution also. And it's quite different when a company plays a big role in the existential threat of an entire country. Certainly culture plays a role, but there are plenty of other factors at play.Reply
At the end of the day, though, what are TSMC's results vs. Intel, Samsung, etc.? There is little connection between the consumer and the unseen plight of a product's builders. If Intel achieves their goal of being back on top of the manufacturing heap without having to treat workers this way, it will undermine Chang's argument and management style. -
King_V If your company cannot succeed without abusing workers, then your management is poor.Reply
If your company cannot prioritize tasks, making EVERYTHING as "top priority" and leaving it to the workers to make "do everything right now" happen, then your management is poor.
It appears that TSMC's success is based heavily on operating in a nation where worker abuse is acceptable. Making a fortune by running workers ragged is easy. Anyone can do that.
TSMC thinks American worker protections are too generous? They'd never survive Western Europe! -
DavidLejdar At my first job after school, 14-hours shifts were common, except on Fridays, Saturdays and Sundays, when it was around 16 hours, and for very little money (in Europe). In that context, "12-hour workdays", sounds progressive. :) And currently having 9-hour workdays (including lunch), but considering to find a time-part job in addition, just to earn a bit more - which would add 10-15 hours to weekly worktime.Reply
And why don't I apply at TSMC then? Very simple really. The instilled work culture "work until you drop, possibly even at quite a young age, so that the owner can purchase several luxury cars and stuff", meant that there wasn't time for anything else, such as learning to read, to be able to decipher road signs to find my way to TSMC. I would have work experience as foreman though, which it sounds that TSMC could do with to have that position in the middle, and someone qualified for exactly that. -
Elk4806 The total salary compensation for their engineers isn't great, which is another reason why retention is terrible. Who wants to put up with an abusive work environment when you can go somewhere else and get paid the same or more. Only a matter of time before we see them getting investigated and fined for violations. Mr Chang's ego and bad habits have been able to flourish in a small country where he lines the pockets of people in his government.Reply -
thestryker
Until Intel's non-technical management opted to not spend the money on EUV machines they were completely dominating the fabrication market. What's happening with TSMC has absolutely nothing to do with the end product but rather a toxic workplace environment fostered in a country without worker protections.hotaru251 said:While it does suck (on both sides) US will have to accept the asian culture for the job and if they cant don't apply. (simple even if not the ideal outcome)
Nobody in the US is going to work for TSMC when there are other companies paying the same, or more, without the toxic management and culture. This is probably why TSMC is having problems getting enough engineers in AZ and Intel isn't. TSMC will either change their ways or be relegated to not having leading edge in the US and it seems like they've chosen the latter. -
nameless0ne The article did not mention that there is a skill issue. The job can be done just not at the same pace as in Taiwan. If everyone needs to works 12 hours per day then they need 1.5x the workers to retain the same performance. And this is a manufacturing sector. If they work 24/7 then they need 3 shifts 8 hours each. They cannot expect to hire 2 shift of workers and just expect them to constantly work 12 hour shifts.Reply
12 hour shifts are permissible but then they don't work 5 days a week.
And the mindset of "profit at all cost (meaning at the expense of workers)" has finally caught up with China. A lot of businesses are leaving China for Vietnam, Indonesia in search of cheaper labor. At some point these places will simply run out.
This is the same discussion as "why the iPhone cannot be made in USA" all over again.