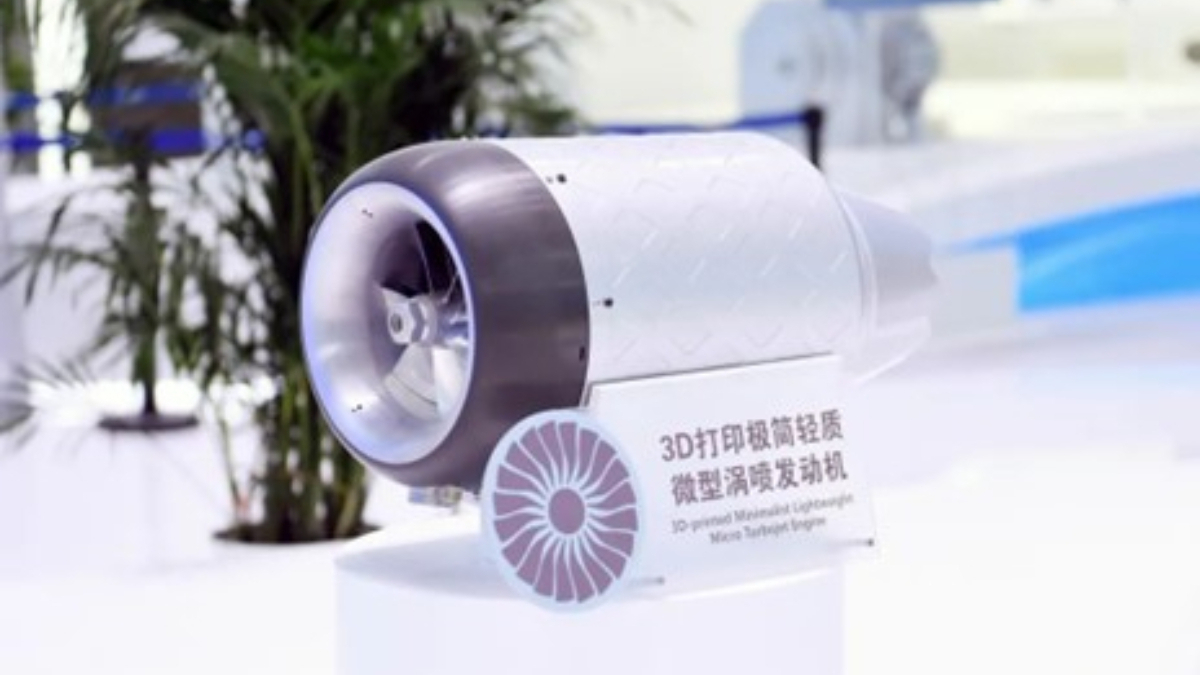
The Aero Engine Corporation of China (AECC) has 3D printed what it calls a micro turbojet engine. This isn't a model or replica print—this is the real deal. This 3D printed micro turbojet engine actually works and successfully flew when recently tested. This information comes to us from Global Times, which shared details from the official AECC WeChat page.
The announcement came on Wednesday when AECC confirmed the test flight took place in North China’s Inner Mongolia Autonomous Region. According to Global Times, the engine was developed independently, but details are sparse. We know that some of the unit is 3D printed, but we aren't sure how much of it is and which components.
According to the developers, the key to the engine design was "multidisciplinary topological optimization." The overall weight of the engine had to be reduced, which was something that could be better managed when 3D printing by changing certain print parameters. This proved to be crucial in reaching certain performance goals.
When testing the 3D printed engine, it managed to reach 4,000 meters (nearly 2.5 miles) of altitude above sea level. The setup also managed to launch with a thrust level of 160kg (over 350lbs). The team believes they are the first to successfully fly a test run using their 3D-printed engine.
The team hopes that future projects are in the works for other areas and that this project serves as proof that 3D printing can be a flexible manufacturing asset. In the meantime, however, this 3D printed turbo engine shows some serious potential in the ways of aerospace and 3D printing. The successful test flight is just icing on the cake.
Unfortunately, we aren't sure what type of 3D printers were used to create this 3D printed micro turbojet engine or what type of filament (or resin) was used when creating the 3D printed components. That said, we have a good idea when it comes to picking out the best 3D printers for the job, and imagine the process took quite a bit of trial and error, but the end results speak for themselves.
Follow Tom's Hardware on Google News to get our up-to-date news, analysis, and reviews in your feeds. Make sure to click the Follow button.
Get Tom's Hardware's best news and in-depth reviews, straight to your inbox.
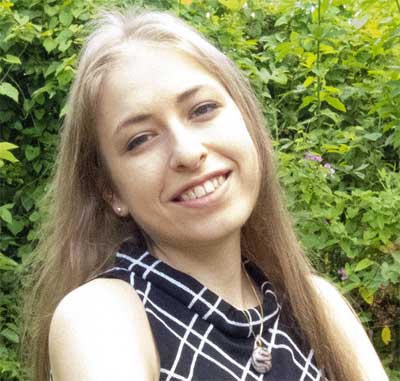
Ash Hill is a contributing writer for Tom's Hardware with a wealth of experience in the hobby electronics, 3D printing and PCs. She manages the Pi projects of the month and much of our daily Raspberry Pi reporting while also finding the best coupons and deals on all tech.
-
Dementoss
Face it, you don't even know if the 3D printed parts are plastic.Admin said:Unfortunately, we aren't sure what type of 3D printers were used to create this 3D printed micro turbojet engine or what type of filament (or resin) was used when creating the 3D printed components. That said, we have a good idea when it comes to picking out the best 3D printers for the job, and imagine the process took quite a bit of trial and error, but the end results speak for themselves. -
Hooda Thunkett I'm assuming they used some kind of laser sintering 3D printing, or something else using metal.Reply -
theverge
I can see what appears to be layers on the plastic cowling. The rest is entirely metal and not 3d printed.Hooda Thunkett said:I'm assuming they used some kind of laser sintering 3D printing, or something else using metal.
Typical CCP propaganda. -
TheMaddScientist Commercial metal 3D printers are available in sizes up to a meter squared with bigger ones on the way. Metal 3D prints are often post-processed to polish the surface, so surface finish is not a good indicator a metal part was 3D printed. I have a captured gear key fob that was printed in inconel (a super nickel alloy), then polished to a near mirror finish. A huge number of current aerospace components (SpaceX anyone?) are 3D printed, in both metal and plastic. This jet engine is certainly possible using 15 or 20 year old technology. That said, the CCP is certainly not above a bit of exaggeration.Reply
Full Disclosure: I am an industrial physicist currently working for the oldest 3D printer company in the world, 3D Systems. I started working at a different 3D printing company in 1993. I designed the laser system (software and some of the hardware) of the machine which made my key fob. In the late 90s, I worked with the software engineer who eventually went back to China and helped start their 3D printing industry. He is a very smart guy and now the CEO of Farsoon. -
husker I'm no expert, but it seems to me that pretty much anything manufactured can be 3D printed at small scales, so there is no need to press release each use case as it happens. It's just a matter of deciding to spend the time and money. If the 3D printing process allowed for some improvement of the product, however, that would be of interest.Reply -
Tanakoi
Clearly you are correct and this engine wasn't printed from plastic or resin, as the author suggests. I rather doubt, though, that a simple metal sintering print could produce turbine blades capable of operating at the required temperatures. I assume they might instead be using SLM (or perhaps electron-beam melting) to fabricate single-crystal blades. I don't know, though, how much progress China has made on this front. Thoughts?TheMaddScientist said:Commercial metal 3D printers are available in sizes up to a meter squared with bigger ones on the way. Metal 3D prints are often post-processed ... -
acadia11 Most of the world including the US in about 20 years!Reply
vlKFTWQhX08View: https://m.youtube.com/watch?v=vlKFTWQhX08&pp=ygUYRmlyZWZseSBhcGVha29uZyBjaGluZXNl -
BFG-9000 Maybe the exhaust turbine blades need to be made of some high-temperature material but the intake centrifugal impellers in hobby turbojets are just aluminum.Reply
Yes, centrifugal impellers like the earliest jet engines used are more practical for very small jets than axial fans. These small RC hobby jet engines have been made for decades and now have a bearing life of about 100 hours which is about the same as the design life of the earliest jet engines in real aircraft (though materials substitution due to shortages led to an actual life as low as 10 hours in service during WW2).
Even if 3D printing reduces the lifespan, the purpose of these engines is for kamikaze drones on one-way trips so cheaper is better. This is just the CCP warning everyone that they can make tons of these for cheap now, so don't mess with us! But while 3D printing suggests cheaper because of the reduced human labor required, it may not be so if some exotic sintering method is needed instead.
It's not if you can make something, but if you can make it cheaply enough to sell for a profit. Those hobby jets can cost thousands of dollars plus bearing replacement every 25 to 100 hours. If they can make a disposable engine so the hourly cost is about the same even if it doesn't last as long, then I can see many people wanting one as the upfront cost would be lower. -
zorkomatic It never ceases to amuse me when young people swallow Chinese propaganda hook, line and sinker. Additive manufacturing technology for turbine engines has been around for decades. it's not even classified.Reply -
zorkomatic
And you seem to think plastic can survive in the confines of a turbine engine. You are more clueless than the admin.Dementoss said:Face it, you don't even know if the 3D printed parts are plastic.