Crimping Might Have Prevented RTX 4090 Adapter Meltdown: Report
Crimping instead of soldering
Igor's Lab has published an article discussing a potential solution to prevent Nvidia's 16-pin power adapter from damaging the GeForce RTX 4090, one of the best graphics cards on the market. According to Igor Wallossek, the publication's editor-in-chief, the solution could be to crimp the connectors, not solder them, since soldering introduces unwanted heat into the connector itself.
Wallossek contends that soldering is the arch-enemy of the 16-pin power connector. Soldering causes several problems that he says can lead to structural failures within the connector. His list of potential issues includes rigid tinning and soldering a stranded wire that is already under tension, processing a stranded wire in a way it will unravel and break, and more. But, one of the biggest problems is the soldering process, even with the best soldering irons air bubbles can form during the process, leading to corrosion.
Ideally, Wallossek believes that the manufacturers should crimp the individual wires in the 16-pin wiring harness, which eliminates all the potential issues involved in the soldering and introduces better structural integrity of the wires.
Igor's Lab says an excellent example of a proper 12VHPWR wiring harness is the one that be quiet!'s Dark Power Pro 12 power supply uses, where two 12-pin plugs convert to a single 16-pin power connection. Each wire consists of very flexible 18AWG cables - which will result in cooler temperatures of the wire itself, and each connector has a total of six 12-volt and six ground wires each. Connecting the two 12-pins from the PSU to the 16-pin that goes into the graphics card is a crimped connection maintained on each cable, where wires from the 12 pins get connected and translated into a single wire.
Wallosek says be quiet!'s design represents one of the safest methods of building a 16-pin wiring harness; the wires are highly flexible and large, which will reduce heat build-up in the wires themselves and also allow users to manipulate the wires freely without significant risk of damaging the connector or the wiring harness itself. Also, the move to crimp the connections removes any thermal or corrosion problems that might occur from soldering.
The solution applies specifically to a 16-pin wiring harness and not Nvidia's power adapter, but the methods implied could easily be used on Nvidia's adapter, particularly that of crimping the connections instead of soldering them.
Get Tom's Hardware's best news and in-depth reviews, straight to your inbox.
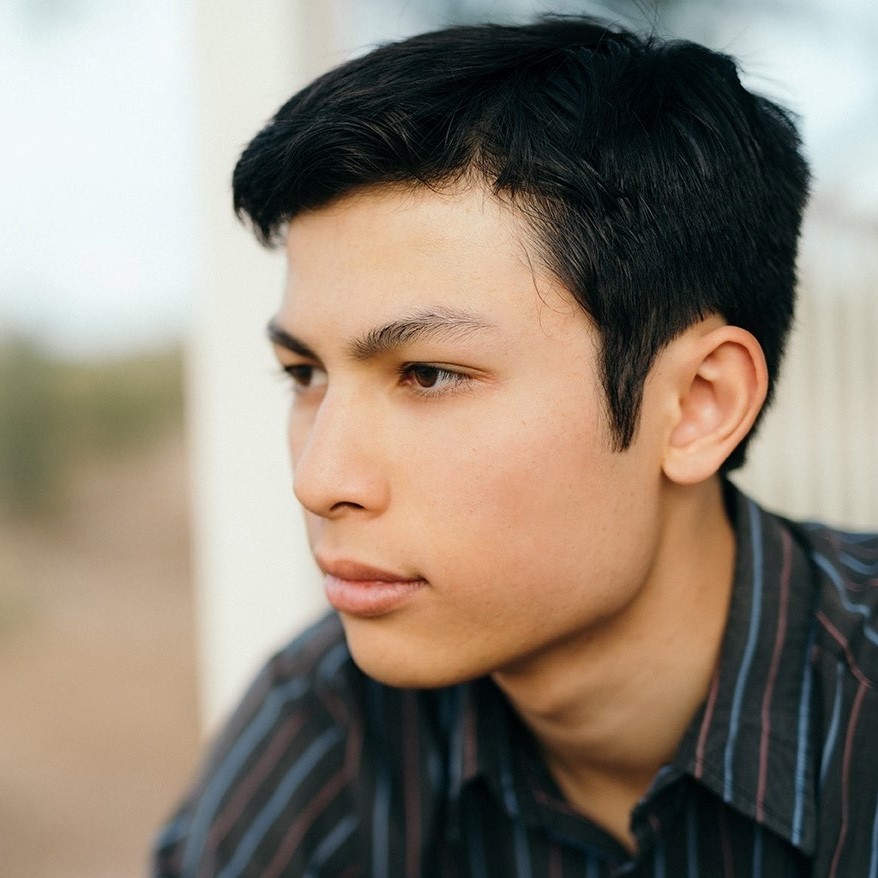
Aaron Klotz is a contributing writer for Tom’s Hardware, covering news related to computer hardware such as CPUs, and graphics cards.
-
Alvar "Miles" Udell Would be interesting to see teardowns of other 12VHP connectors to see if they used this method (which they likely did, especially SeaSonic)Reply -
nimbulan Except as others have noted, the connectors are melting at the end, not where the solder joints are. This suggests that the solder joints are not where the excessive heat is being produced. The most promising theory I've seen is that the barrel connectors inside nVidia's power adapter plug are split along both the top and bottom so there's no structural support horizontally, allowing them to easily loosen up, resulting in poor electrical contact.Reply -
InvalidError I doubt soldering had anything to do with the failures. Crimping onto something that is only 0.2mm thick would likely be every bit as problematic structure-wise. And then you have Igor's piece saying it the split terminals may be the root cause since there is almost no structural integrity keeping the terminals from becoming loose, which crimping would do absolutely nothing about.Reply -
BillyBuerger
The connectors are melting because some solder connections are failing putting more current through the ones that didn't fail which then causes those connectors to overheat and melt. So the issue is the soldered connection that then causes the failure in the connectors.nimbulan said:Except as others have noted, the connectors are melting at the end, not where the solder joints are. This suggests that the solder joints are not where the excessive heat is being produced. The most promising theory I've seen is that the barrel connectors inside nVidia's power adapter plug are split along both the top and bottom so there's no structural support horizontally, allowing them to easily loosen up, resulting in poor electrical contact.
As someone who also likes to dabble in car audio with very thick power wires, I've seen plenty of debates on solder versus crimping. The overall consensus seems to be in favor of crimping. Solder on wires that move or vibrate can fail over time as solder is brittle. A good crimp job can hold very well as it creates pressure holding the wires together instead of the solder itself holding the wires. Not to say a bad crimp couldn't cause these same issues. So either way, the QC of these things failed big time. -
Kamen Rider Blade
The Double-Split terminal analysis was from Buildzoid of AHOC.InvalidError said:I doubt soldering had anything to do with the failures. Crimping onto something that is only 0.2mm thick would likely be every bit as problematic structure-wise. And then you have Igor's piece saying it the split terminals may be the root cause since there is almost no structural integrity keeping the terminals from becoming loose, which crimping would do absolutely nothing about.
yvSetyi9vj8
But I don't understand how much money was nVIDIA saving by going with 4x 14-AWG copper wires in the adapter over 6x 16-AWG copper wires that other vendors would use?
Anybody care to guess what the BOM cost difference would be?
How much would 6x crimped 15-AWG copper wires cost?
I would prefer "Crimped" wires as well and a fundamentally different design than what nVIDIA contracted out to "Astron".
Imagine, instead of 4x seperate 4" cables to 4x 6+2 PCIe Power Receptacles that look like squid tentacles.
How about a Isoceles Pentagonal or Hexagonal PCB that mountes the 4x 6+2 PCIe Power Receptacles & a Aluminium or Plastic housing to protect the PCB.
Then route the power through the PCB & logic chip that nVIDIA used, then through a longer set of proper 6x 15-AWG copper wire pairs w/4 sense wires to the PCB that are properly crimped and strain relieved.
How much longer, say somewhere between 12" & 18" so users can route the adapter to somewhere behind the PC case.
How much more would that have cost to build? -
InvalidError
The reason for 4x#14 for 12V and ground likely had more to do with there being four 8-pins connectors to aggregate into one. If you wanted 2x ground + 2x 12V from each connector going to the GPU, then you'd have to somehow attach 16x #16 to that thing.Kamen Rider Blade said:But I don't understand how much money was nVIDIA saving by going with 4x 14-AWG copper wires in the adapter over 6x 16-AWG copper wires that other vendors would use?
No need for a PCB, just solder all terminals to a single #10 wire to aggregate the 4x6/8-pins, then you only need 2x#10 going to the GPU connector.Kamen Rider Blade said:Then route the power through the PCB, then through a longer set of proper 6x 15-AWG copper wire pairs w/4 sense wires to the PCB that are properly crimped and strain relieved. -
Kamen Rider Blade
ICInvalidError said:The reason for 4x#14 for 12V and ground likely had more to do with there being four 8-pins connectors to aggregate into one. If you wanted 2x ground + 2x 12V from each connector going to the GPU, then you'd have to somehow attach 16x #16 to that thing.
No need for a PCB, just solder all terminals to a single #10 wire to aggregate the 4x6/8-pins, then you only need 2x#10 going to the GPU connector.
I'd rather not have a "Squid" like appendage with extra wires dangling.
That's why I prefer the Pentagonal or Hexagonal PCB box solution with a single set of wires routed from the box to the 12VHPWR plug. -
wmeyer There really is no mystery over which method is better: Solder is only meant to stabilize a mechanically secured connection. Solder is soft; depending on it as a mechanical means of attachment is folly.Reply -
jasonf2 High amperage connection and solder are a bad mix. One of the issues not noted here is the fact that solder has a relatively low melting point. When a solder joint goes hot it has the potential to melt itself and come apart. It is for that reason that soldered joints are all but illegal by code in high voltage systems. (Yes there are a couple of exceptions, but they are related to factory production applications, not field connections). They used to do this back in the knob and spool days and it caused house fires. When you take into consideration the crazy combined wattage on this connector is more than most soldering irons there is no real surprise that things are coming apart. If my rough math is right at 400 watts / 12VDC you have about 33 amps spread across the connectors. You need an RV power connector not a 16 pin connector. LolReply -
InvalidError
Low? Lead-free solder melts at 235C. The connector and PVC wire insulation will be a smouldering mess long before the solder's melting point becomes a concern. The "low" melting point of lead-free solder is only a problem when your application is expected to hit 200+C under normal operating conditions.jasonf2 said:High amperage connection and solder are a bad mix. One of the issues not noted here is the fact that solder has a relatively low melting point.