MSI’s new PinSafe Design motherboard promises no more pricked fingers
Set to debut on the first AMD chipset MPOWER motherboard from MSI, the B850MPOWER.
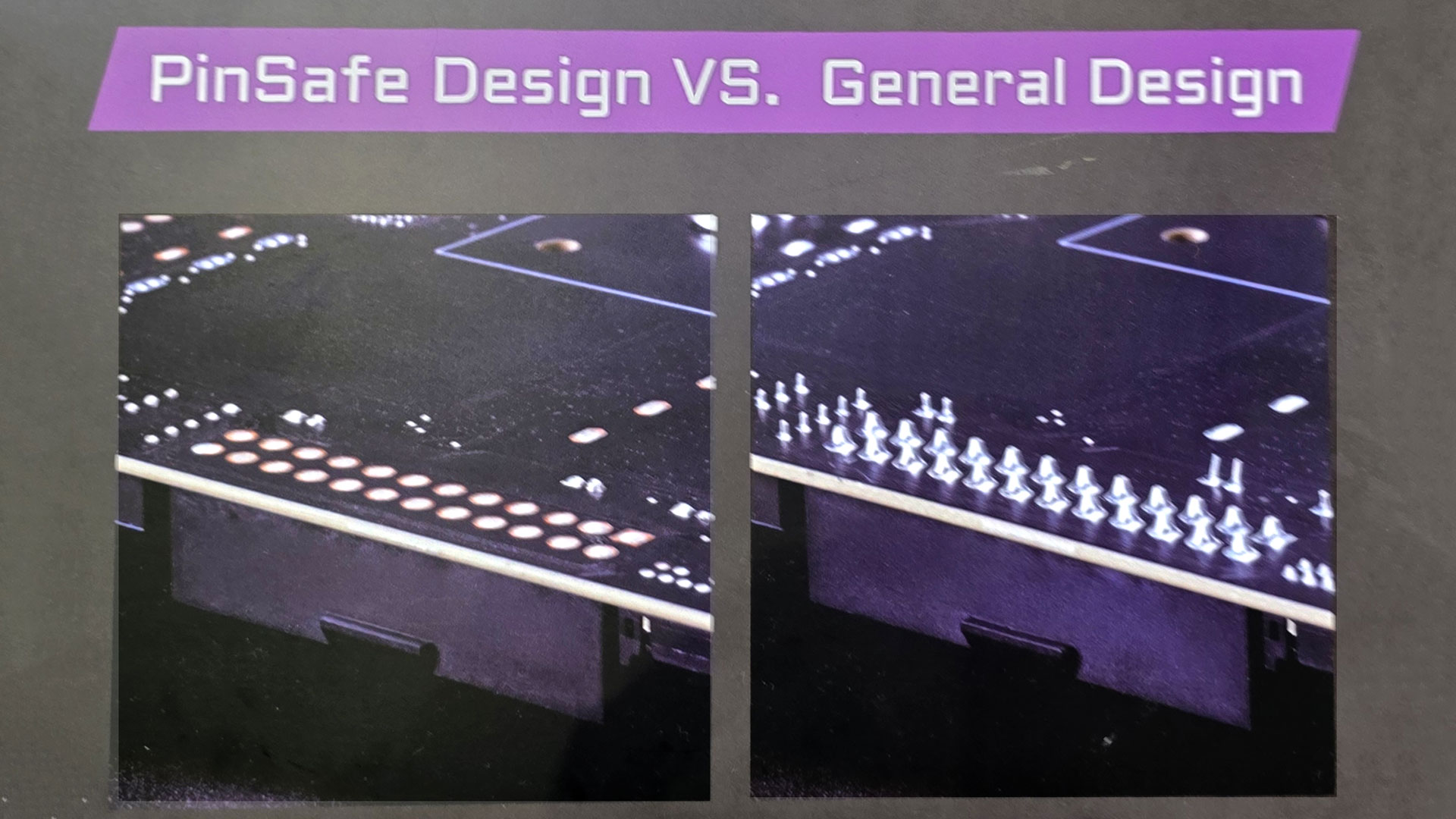
Seasoned PC DIYers have always had to wear dexterity-stifling gloves or put up with pricked fingers when upgrading a motherboard or putting together a new PC build – until now. MSI showcased a series of motherboard design tweaks at Computex 2025, including a feature dubbed ‘PinSafe Design’ which enables users to “avoid injury caused by sharp pins during the assembly process.”
The concept here isn’t difficult to grasp, unlike a traditional prickly motherboard. MSI’s mobo manufacturing arm appears to be adopting a far tidier component soldering technique, which results in elegantly flat pads on the reverse of the PCB, rather than forests of spikes.
Admittedly, this isn’t the greatest of technological achievements, Nevertheless, there might have been some component strength, reliability, or stability concerns preventing such a manufacturing change. So we have a baby step here, which should be welcomed as long as the finished product doesn’t suffer in any way compared to a traditional design.
Other touted PinSafe Design benefits
Saving your fingers from pricks and lacerations isn’t the only benefit of PinSafe Design, according to MSI. Likely the result of fevered brainstorming, threaded with some thin strands of truth, MSI says that the PinSafe Design boosts system stability and ESD protection. We think the lack of protruding pins might also give foreign objects less chance of getting caught or jammed between contacts, reducing the potential to create shorts.
MSI's first MPOWER motherboard for AMD processors
The above PinSafe Design looks set to debut on MSI MPOWER series motherboards, designed for enthusiasts and overclockers. MSI is preparing new MPOWER boards, and the B850MPOWER sample we saw was actually the first AMD-based motherboard from MSI to use this set of features.
Standard MPOWER features include; leveraging the Dragon Alliance collaboration with memory brands, using only 2x DIMM slots for reliable DDR5 overclocking, and the equipping of the EZ Dashboard which integrates power, reset, clear CMOS, and a debug LED on the board for simpler troubleshooting.
Follow Tom's Hardware on Google News to get our up-to-date news, analysis, and reviews in your feeds. Make sure to click the Follow button.
Get Tom's Hardware's best news and in-depth reviews, straight to your inbox.
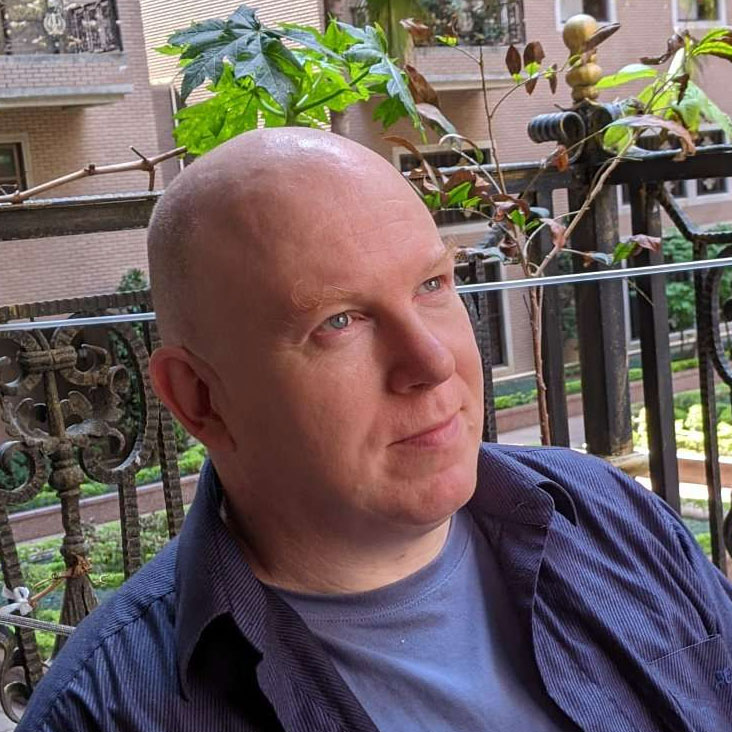
Mark Tyson is a news editor at Tom's Hardware. He enjoys covering the full breadth of PC tech; from business and semiconductor design to products approaching the edge of reason.
- Paul AlcornEditor-in-Chief
-
The Historical Fidelity Can’t say that I have ever experienced any of the so called reasons listed to need this “Pin-Safe” technology. Marketers doing what they do best, reminds me of those “As Seen on TV” infomercials lolReply -
Findecanor There is a saying in Maker circles: "It isn't a real project unless you've shed blood for it". ;)Reply
This looks to me more as if the last through-hole components have been replaced with surface-mounted ones as a cost-saving measure, and the "Pinsafe" moniker is not much more than a marketing spin for it. -
helper800
As far as I am aware, all through hole components can be installed without a large lead poking out the other side of the board. The soldering just has to be cleaner and more precise.Findecanor said:There is a saying in Maker circles: "It isn't a real project unless you've shed blood for it". ;)
This looks to me more as if the last through-hole components have been replaced with surface-mounted ones as a cost-saving measure, and the "Pinsafe" moniker is not much more than a marketing spin for it. -
Co BIY I don't think the goal of this was originally "anti-poke safety".Reply
More likely they can use 50% less solder and save $0.10 per board.
Thinner MB would work well in a laptop or mobile device where space matters.
Maybe with less lead to heat and solder to cool you can process the boards faster or visualize and detect a quality problem better.
I'd be interested to know the real purpose. -
jimday
I think you're right.Co BIY said:I don't think the goal of this was originally "anti-poke safety".
More likely they can use 50% less solder and save $0.10 per board.
Thinner MB would work well in a laptop or mobile device where space matters.
Maybe with less lead to heat and solder to cool you can process the boards faster or visualize and detect a quality problem better.
I'd be interested to know the real purpose. -
The Historical Fidelity
One could make an argument that the pins sticking out of solder points could act like antennae to introduce interference into the system, but capacitors naturally filter out direct current and other components filter out of phase and unnecessary frequency alternating current.jimday said:I think you're right. -
The Historical Fidelity
I have always found the thought dynamic between engineers and marketers when looking at the same object fascinating hahaCo BIY said:I don't think the goal of this was originally "anti-poke safety".
More likely they can use 50% less solder and save $0.10 per board.
Thinner MB would work well in a laptop or mobile device where space matters.
Maybe with less lead to heat and solder to cool you can process the boards faster or visualize and detect a quality problem better.
I'd be interested to know the real purpose. -
abufrejoval I don't think that mechanical strenght would suffer much by not having the pins extend beyond the mainboard.Reply
I seem to recall that DDR5 DIMM sockets went from PCB vias to SMD mounting, which had a much bigger impact on stability or potential damage from people rocking DIMMs to ensure a proper seat.
Reducing capacitance or just having a finer control over signal reflection or degradation may just make this a necessity, while the assembling and soldering robots would just be redesigned to match.
I welcome anything that somehow manages to achieve the quality and speed of soldered connections while maintaining swappable parts, e.g. socketed LPCAMM.
As for blood on my hands, cases were far more greedy than boards. -
bit_user I have a motherboard where the pins from some of the VRM components poked through the other side, like this. I wanted to put a heatsink underneath the VRM (insulated by a thermal pad), to transfer some of that heat to the case. So, I had to grind down the pins. It was a little harrowing and not quite as easy as I thought.Reply
As for getting poked by such pins, I've certainly felt it, but never caused me much distress. I guess it could be different, if you're handling such boards somewhat frequently and maybe have more delicate hands.