AMD Ryzen 8700G delidded – runs up to 25 degrees Celsius cooler and up to 17% faster
Der8auer is impressed with near 7700X CPU performance achievement.
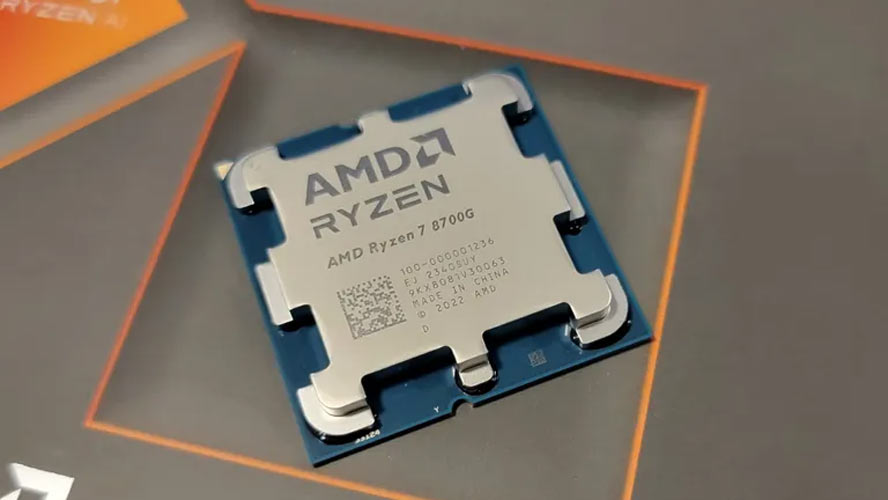
AMD launched a quartet of Ryzen 8000G ‘Phoenix’ APUs for desktops back at CES 2024 but it quickly became apparent that these chips used a thermal paste thermal interface material (TIM). Today, overclocking expert Roman 'Der8auer' Hartung published some tests showing the performance / temperature improvements available from delidding these new APUs, specifically AMD’s top-of-the-range Ryzen 7 8700G (click to read our review). Impressively, moving from a stock sample to one with a Liquid Metal TIM applied could reduce core temperatures by up to 25 degrees Celsius. Processor performance could also be improved by up to 17%.
At the start of his video, Der8auer highlights that as the Ryzen 8000G processors are more closely related to the mobile parts they use thermal paste rather than a solder TIM. This usually means that delidding the processor and switching the TIM for liquid metal will pay excellent dividends.
Before starting his tests, Der8auer thought it useful to compare the new Ryzen 7 8700G with the tried and trusted Ryzen 9 7950X chip. A quick visual inspection reveals a big difference. There are lots of surface mount components visible on the chip substrate between the octopus legs of the 7950X. On the 8700G, you can only see these types of components by peeping under the IHS.
The visual inspection made Der8auer concerned that the Ryzen 7000 Delid-Die-Mate may be incompatible with Ryzen 8000G chips. However, the delidding process worked flawlessly and was even easier due to the paste TIM. The 8700G was delidded with no damage, so the testing plan could go ahead.

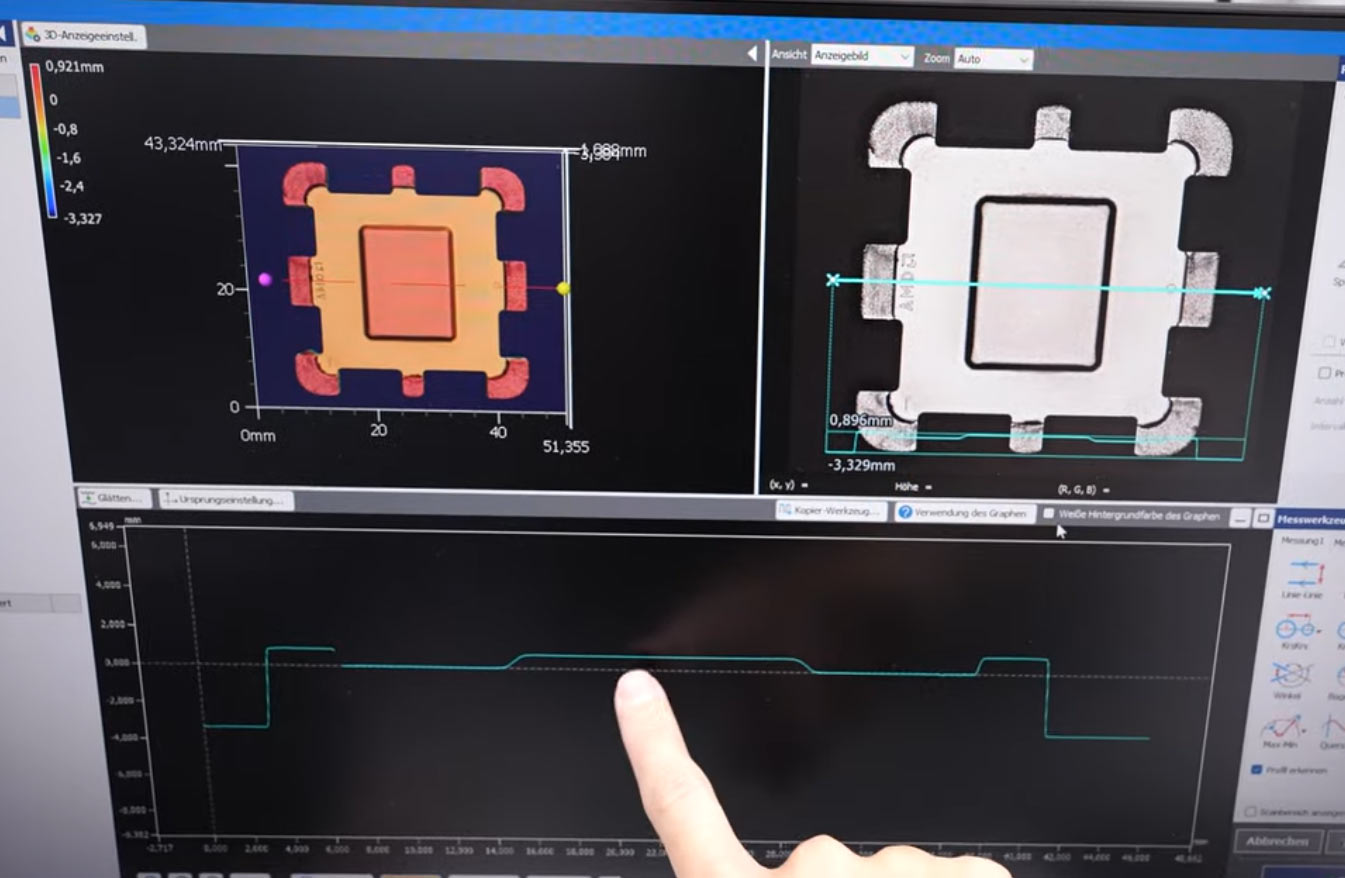
Der8auer tested the Ryzen 7 8700G in three configurations, and with three power / clock strategies. Before delidding he tested a stock 8700G as supplied, with PBO, and with a manual overclock at 5.0 GHz. After delidding he did the same tests using an 8700G which had a KryoSheet between the die and IHS, and finally with Liquid Metal.
He noted that the manually overclocked Ryzen 7 8700G would perform about 5% behind a Ryzen 7 7700X in Cinebench with the 5.0GHz overclock. However, some people will prefer the Phoenix desktop chip due to its strong iGPU.
Seeing the cool performance of the delidded chip using Liquid Metal, Der8auer found that the new sweet spot of the processor for manual overclocking was 5.3 GHz with core temperatures remaining under 80 degrees Celsius. The measured Cinebench performance of this chip was 15 to 17% better than the originally tested stock APU.
Get Tom's Hardware's best news and in-depth reviews, straight to your inbox.
Why delid and test an APU like this? Der8auer says he did go through with this project because he likes doing these kinds of things… However, he also reckons that this kind of tinkering could deliver real benefits in some scenarios. For example, in size-constrained systems, where cooler size and design are more limited and where people tend to seek very quiet performance, being able to use a smaller cooler and / or a slower fan speed could be very attractive.
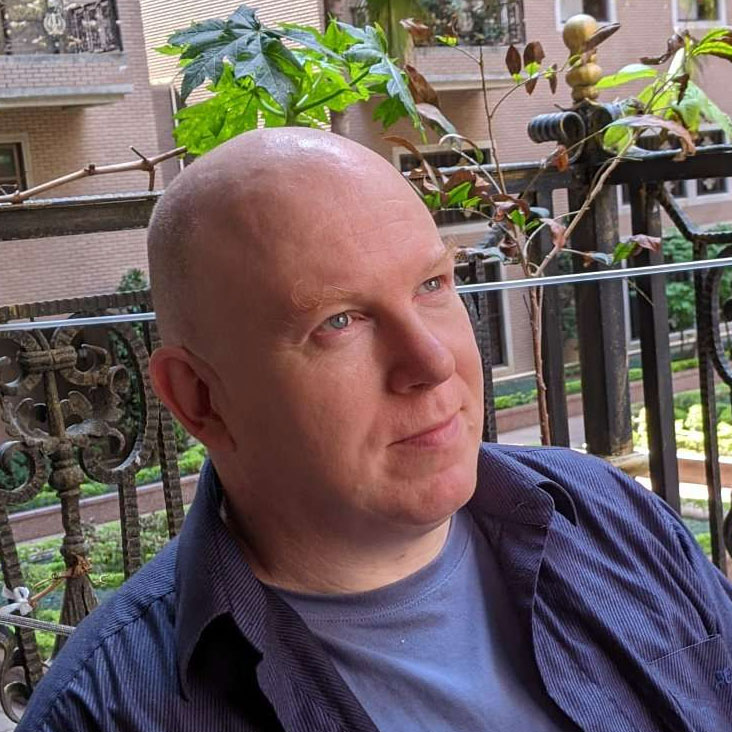
Mark Tyson is a news editor at Tom's Hardware. He enjoys covering the full breadth of PC tech; from business and semiconductor design to products approaching the edge of reason.
-
Kamen Rider Blade
The IHS was meant to be designed for backwards compatibility with existing AM4 HeatSinks.yeyibi said:Δ25 Cº means that AMD packaging design is massively incompetent.
The bad part was the cut-outs that led to less surface area for heat removal. -
Notton
Or it's a laptop chip with TJmax of 95C, and only hitting 85C under heavy load.yeyibi said:Δ25 Cº means that AMD packaging design is massively incompetent.
I figure AMD was too cheap to do the mating with iridium.
Curiously, the 8840HS has aTJmax of 100C. -
The Historical Fidelity
No the bad part is that the IHS is much thicker than the AM4 IHS which degrades thermal conductivity. The cut-outs actually do not degrade heat removal nearly as much in this case since the monolithic die is far away from these areas. The math formula for thermal conductivity states the thickness of the material between the heat source and cooler cold plate greatly affects the amount of heat that can be transferred, with thin material superior to thick. This is also why the cut-outs are not important because the effective thickness of the material between point a (edge of top of die) to point b (edge of top of IHS at cut-out) is so thick that minimal heat energy will travel there compared to the IHS directly above the die. The thickness of the IHS directly above the die has a maximal effect on heat removal in this case.Kamen Rider Blade said:The IHS was meant to be designed for backwards compatibility with existing AM4 HeatSinks.
The bad part was the cut-outs that led to less surface area for heat removal. -
TerryLaze
Everything is always a matter of cost, these APUs are expensive enough as they are, making them even more expensive (and draw a ton more power) isn't worth it.yeyibi said:Δ25 Cº means that AMD packaging design is massively incompetent.
I mean derbauer even shows the differences so you can see that their packaging design skills are fine, they just didn't choose to implement them in this APU. -
Tom Sunday I religiously and always visit all our local computer shows and talking to scores of people behind and fronting the hundreds of folding tables. Even engaging conversations carried in the long line of the excellent Costco style hot-dogs served in the rear of the show. It’s a paradise for conversation and contact and meeting the ‘man on the street’ with real live visceral and eye to eye contact! I am yet to meeting anyone who “Delidded” their CPU!”Reply -
Kamen Rider Blade
But with thicker IHS, you can store more heat inside the IHS before you have to remove it.The Historical Fidelity said:No the bad part is that the IHS is much thicker than the AM4 IHS which degrades thermal conductivity. The cut-outs actually do not degrade heat removal nearly as much in this case since the monolithic die is far away from these areas. The math formula for thermal conductivity states the thickness of the material between the heat source and cooler cold plate greatly affects the amount of heat that can be transferred, with thin material superior to thick. This is also why the cut-outs are not important because the effective thickness of the material between point a (edge of top of die) to point b (edge of top of IHS at cut-out) is so thick that minimal heat energy will travel there compared to the IHS directly above the die. The thickness of the IHS directly above the die has a maximal effect on heat removal in this case.
They went and created a thicker IHS to maintain backwards compatibility, but the cut-outs significantly removed surface area for them to conduct heat away.
Those are the major issues I have with the current setup. -
rluker5
I won't count, but I started delidding with my 4770k in 2013. The temp I gained was less than 25c with the CPU that popularized delidding due to "pigeon poop". LGA 1150 CPUs are so easy to do.Tom Sunday said:I religiously and always visit all our local computer shows and talking to scores of people behind and fronting the hundreds of folding tables. Even engaging conversations carried in the long line of the excellent Costco style hot-dogs served in the rear of the show. It’s a paradise for conversation and contact and meeting the ‘man on the street’ with real live visceral and eye to eye contact! I am yet to meeting anyone who “Delidded” their CPU!”
I blame that AM5 IHS. It is too chonky. AM4 IHS was a real good one. AMD should have made people just buy adapter kits of washers. Probably would have been $5 for name brand ones. -
The Historical Fidelity
Thermodynamics does not care that you think the cut-outs affect thermal conduction to any relevant degree and I demonstrated it to you mathematically in my previous point. And you actually do not want an IHS that is thick enough where the amount of heat generated by the die is greater than the IHS’s ability to conduct the heat to the cold plate. Besides, you would need a 6 inch thick IHS to have enough thermal capacity to last a couple of minutes at full tilt before the die thermal fuses. The key is to get the dies heat moved to the cold plate as quickly as possible because the IHS is the rate limiting step, IE an inefficient IHS at transferring heat to the cooler is the biggest hurdle to controlling heat. This is why direct die cooling is so much better than having any kind of IHS between the die and cold plate. IHS’s are there to protect the die from damage, not to enhance cooling. Many CPU’s back in the day had bare dies, and consumers had a hard time installing coolers on them without chipping or cracking the dies. Laptop CPU’s and GPU’s have never used IHS’s because consumers aren’t meant to be the ones installing coolers on them. Believe me, if IHS’s had any benefit to cooling said dies (like a 500 watt capable strix 4090 comes to mind as a die that needs all the tricks to cool), then they would put them on the dies. But they don’t, because IHS’s reduce thermal transfer out of the die and into the cooler.Kamen Rider Blade said:But with thicker IHS, you can store more heat inside the IHS before you have to remove it.
They went and created a thicker IHS to maintain backwards compatibility, but the cut-outs significantly removed surface area for them to conduct heat away.
Those are the major issues I have with the current setup. -
Kamen Rider Blade
I know, I was around for those Direct Die days.The Historical Fidelity said:Steady state is reached quite rapidly so more material does not equal any real benefit. You would need a 6 inch thick IHS to last a couple of minutes at full tilt before the die thermal fuses. The key is to get the dies heat moved to the cold plate as quickly as possible because the IHS is the rate limiting step, IE an inefficient IHS at transferring heat to the cooler is the biggest hurdle to controlling heat. This is why direct die cooling is so much better than having any kind of IHS between the die and cold plate. IHS’s are there to protect the die from damage. Many CPU’s back in the day had bare dies and consumers had a hard time installing coolers on them without chipping or cracking the dies. Laptop CPU’s and GPU’s have no IHS’s because consumers aren’t meant to be the ones installing coolers on them. Believe me, if IHS’s had any benefit to cooling a 500 watt capable strix and other top shelf 4090s, then they would put them on the dies.
That being said, Direct Die isn't worth the RMA troubles for average DIY or the techs who work at OEM/ODM shops who assemble PC's, so there's that.
And because we have the IHS that we have, I was very upset when AMD took away surface area to conduct heat away with.
I have my alternate IHS idea that I want AMD to adopt, but that requires them to be willing to change the IHS.
Given the "Sunk Cost" of the current IHS, I don't think they'll change until we move to a brand new Socket AM6.