Core i9 14900KS heatspreader transformed into CPU water block - clever machining yields a functioning water block
Direct to chip cooling taken literally.
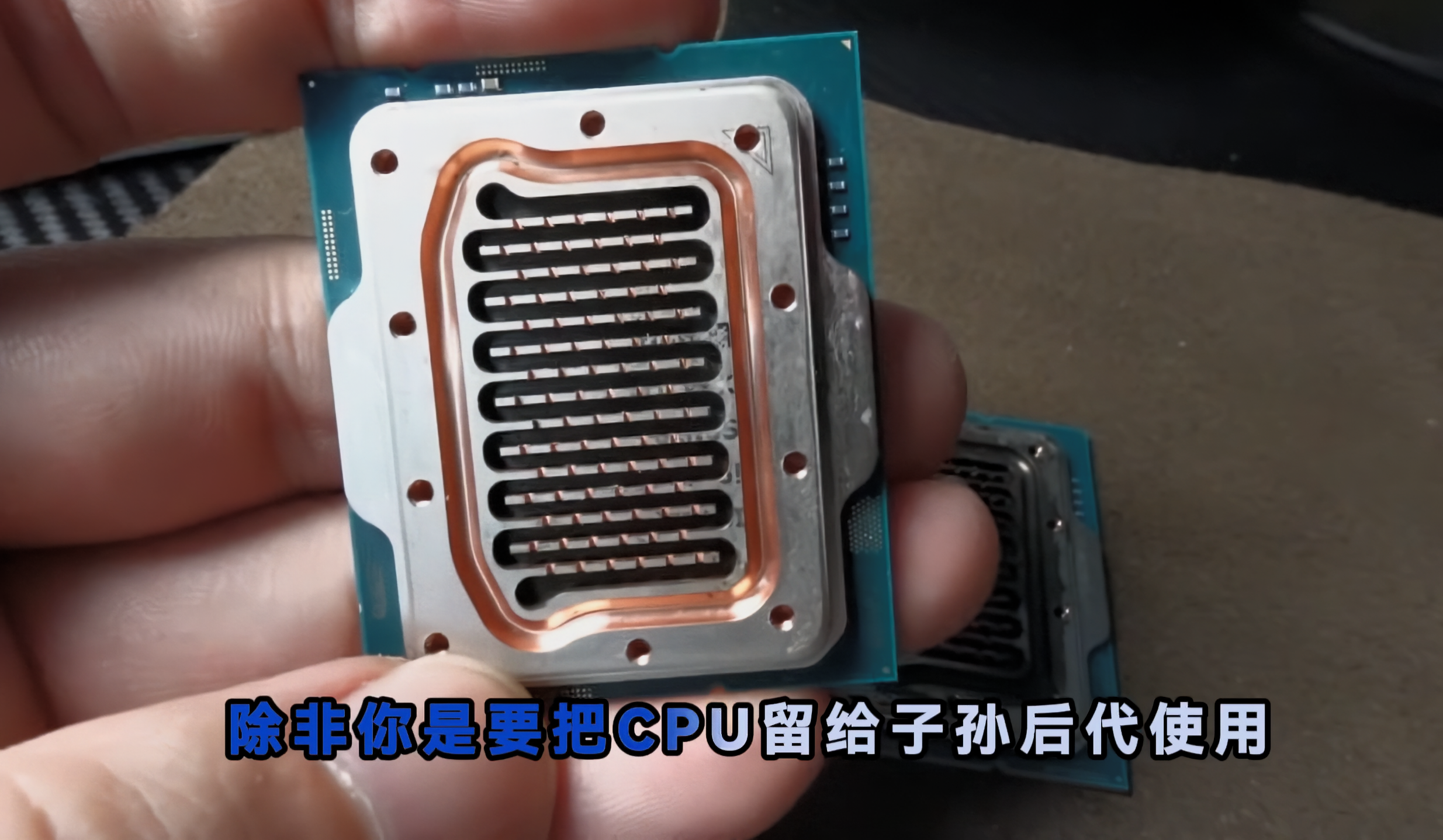
Where most would buy a dedicated water block for their processor, crafty Chinese YouTuber octppus machined a cold plate directly from their CPU's IHS, via UNIKO's Hardware at X. Testing this approach to yield tangible data required some rather unwieldy strategies, like drawing water from a bucket to ensure a controlled environment. While the idea of carving a water block from your IHS seems ingenious, it carries the obvious risk of destroying your CPU and presents some quirky thermal characteristics.
Why would you even do this in the first place? Your CPU's die is connected to the IHS (Integrated Heat Spreader) by STIM or thermal grease. To liquid cool your CPU, a metal block (or cold plate) is essential to conduct heat from the IHS. Water blocks contain intricate microchannels or streams, where the heat from the block's metal is transferred to the coolant via convection. Since each interface or surface increases thermal resistance, serious overclockers typically remove the IHS and mount the water block directly onto the die.
What if you took this the other way around, and removed the external waterblock instead? With the help of CNC machines, in collaboration with a viewer, the modder was able to carve a series of interconnected channels or streams in the IHS of their Core i9-14900KS for the coolant. There are also visible areas for the inlet and outlet fittings, and the entire structure is enclosed in a screwed-in gasket to ensure a leak-proof design.
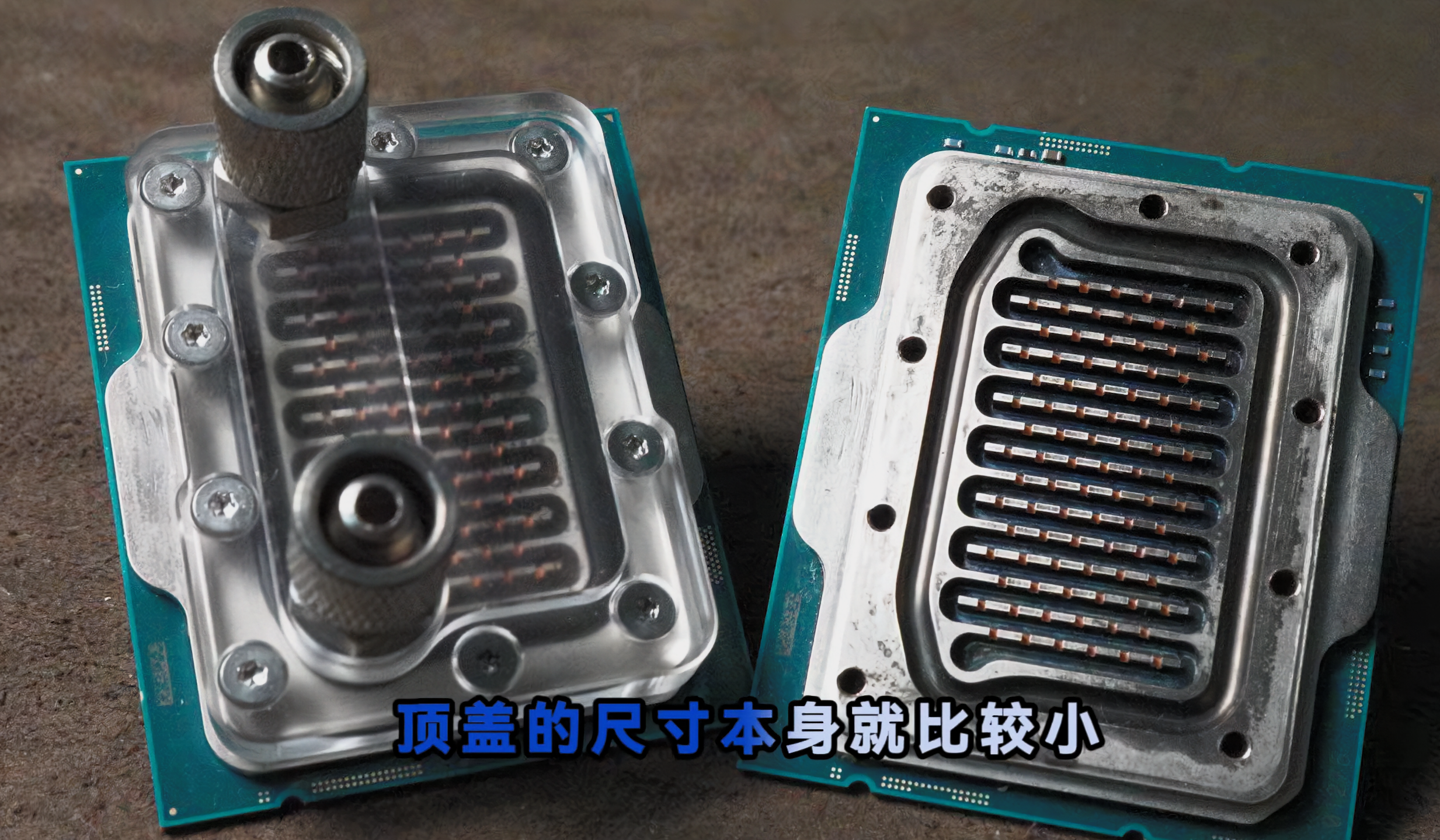
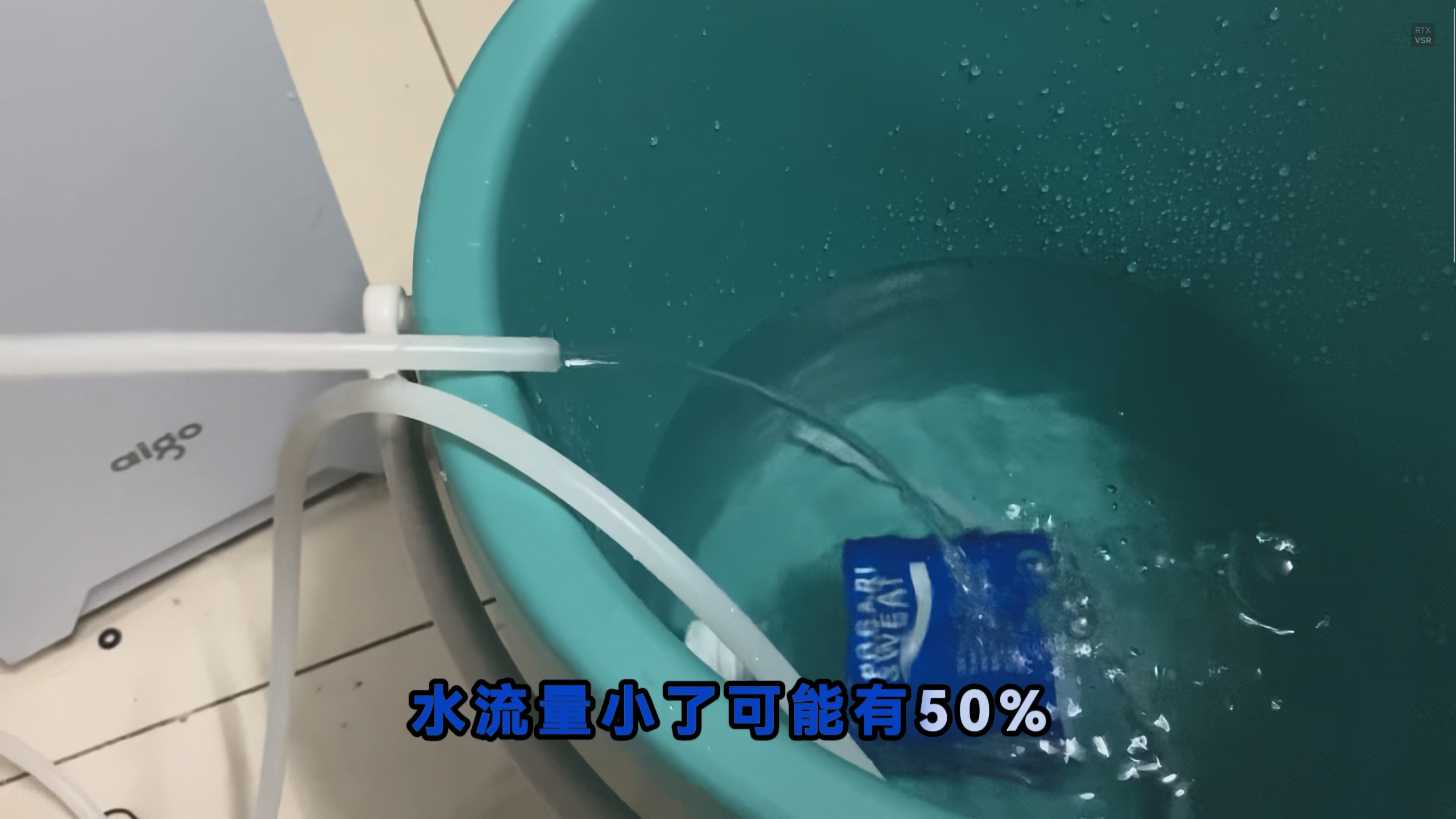
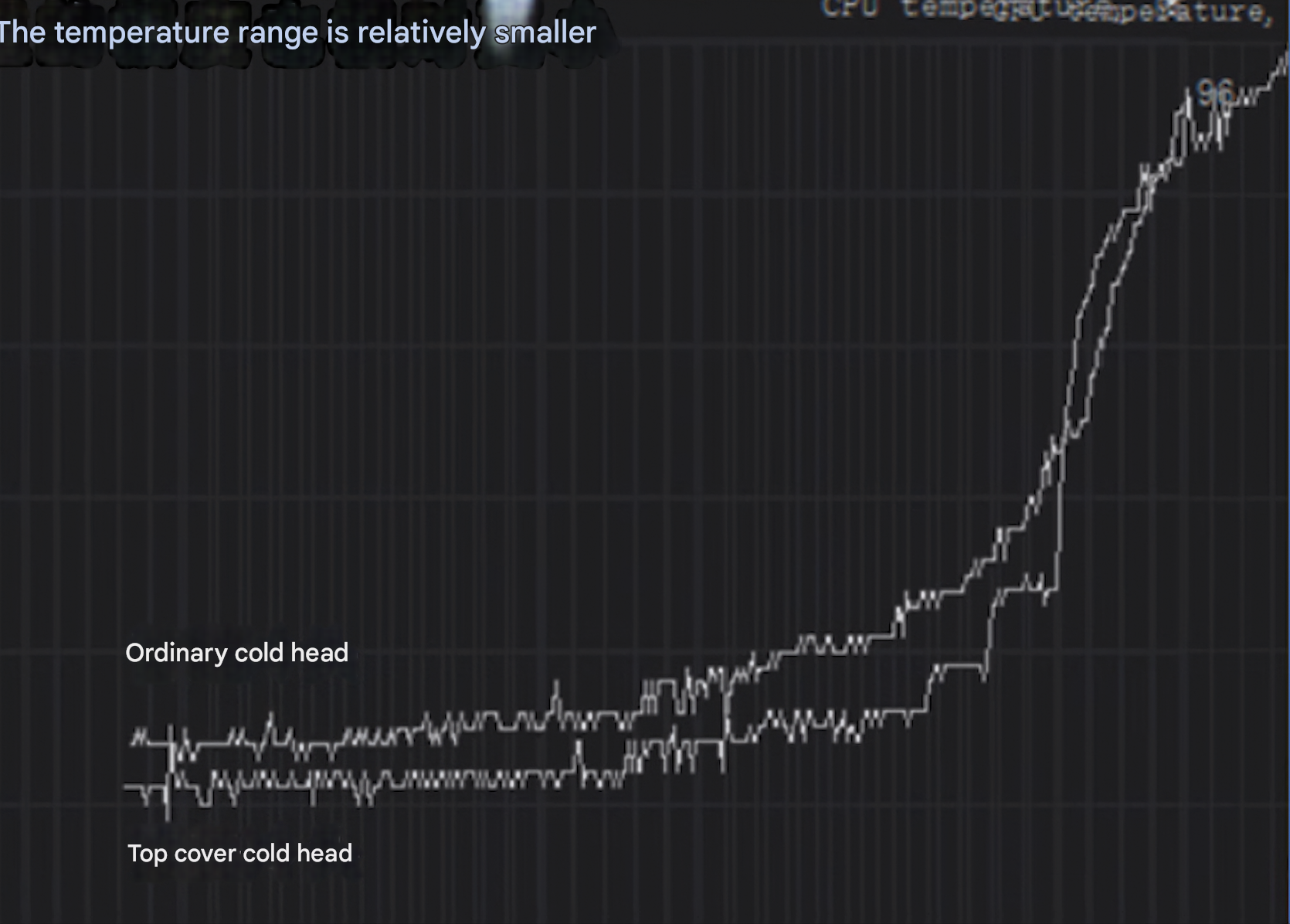
To maintain a constant temperature for the coolant, it was poured into a bucket, which served as the reservoir. After each pass, the coolant was discharged into a separate bottle. That's one way of doing things, I guess. Either way, the pump speed was gradually lowered, and the user plotted the temperature of their modified IHS and a standard liquid cooler on a temperature-time graph. While idling and under a 60W load, the custom IHS cold plate ran cooler. Yet, as the pump speed was reduced, the temperature immediately began to climb, exceeding the conventional liquid cooler.
There's likely a good reason why this happens. The custom IHS solution, per the modder, shortens the distance from the CPU's die to the coolant by a factor of four. And that will have a noticeable impact. However, the tradeoff comes in the form of a smaller surface area and a design that's likely less optimized than traditional water blocks. Unlike cold plates, which spread heat, this approach focuses it in one area, which could explain the rapid temperature increase as shown in the graph.
That being said, for those who live on the edge, machining an IHS into a water block might still prove a viable method, as long as the coolant flow rate is kept in check. This really isn't practical for the average user, and even seasoned veterans might have a tough time getting the execution right. However, it would be great to see a follow-up with a more thorough examination and potentially better designs.
Follow Tom's Hardware on Google News to get our up-to-date news, analysis, and reviews in your feeds. Make sure to click the Follow button.
Get Tom's Hardware's best news and in-depth reviews, straight to your inbox.
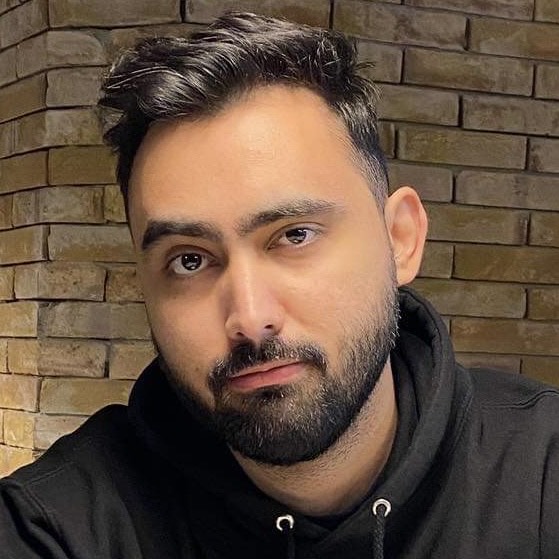
Hassam Nasir is a die-hard hardware enthusiast with years of experience as a tech editor and writer, focusing on detailed CPU comparisons and general hardware news. When he’s not working, you’ll find him bending tubes for his ever-evolving custom water-loop gaming rig or benchmarking the latest CPUs and GPUs just for fun.
-
A Stoner You would want the water to enter at the center of the die and work its way outward where it then discharges.Reply -
bit_user An obvious problem I can see with the concept is that removing material from the IHS impairs its ability to distribute the heat. I'd expect an additive approach to work better, where channels are built up atop the IHS. Or, at the very least, don't remove (much) material right above the die, itself.Reply
Also, I don't know much about water block design, but the path cut for those channels seems non-optimal. -
bit_user
I think that's not what waterblocks typically do and I think I understand why. If you recall Newton's Law of Cooling, the rate of heat transfer is proportional to the temperature difference. If the center of the IHS is at 70 degrees and the edges are at 55 degrees, then having water hit the center first will quickly warm up the water (let's say to 50 degrees), which is almost the same as the edges. At this point, contact with the edges of the IHS won't extract much additional heat from it.A Stoner said:You would want the water to enter at the center of the die and work its way outward where it then discharges.
On the other hand, if you pump in the water at the edge and let it work its way up to the center, then it's extracting a more constant amount of heat, the whole way. So, maybe it gets to 40 degrees at the edge and reaches 45 degrees by the center. At this point, the delta is still enough for good heat extraction, but it's already taken heat from the edge.
Which scheme is better probably depends on a lot of specifics and would require proper modeling to know for sure. -
A Stoner
I do not think the water warms up anywhere near as fast as you think it does. And, once the system has been running for a while, the water temperature should settle at a near specific delta over room temperature. Typically about 8 to 10 degrees depending on volume of air circulation and whether or not the whole gets any fresh air. Basically, if your case is not expelling the heat out, the ambient temperature inside the case will be higher and will increase whole system temperature accordingly.bit_user said:I think that's not what waterblocks typically do and I think I understand why. If you recall Newton's Law of Cooling, the rate of heat transfer is proportional to the temperature difference. If the center of the IHS is at 70 degrees and the edges are at 55 degrees, then having water hit the center first will quickly warm up the water (let's say to 50 degrees), which is almost the same as the edges. At this point, contact with the edges of the IHS won't extract much additional heat from it.
On the other hand, if you pump in the water at the edge and let it work its way up to the center, then it's extracting a more constant amount of heat, the whole way. So, maybe it gets to 40 degrees at the edge and reaches 45 degrees by the center. At this point, the delta is still enough for good heat extraction, but it's already taken heat from the edge.
Which scheme is better probably depends on a lot of specifics and would require proper modeling to know for sure.
If your room temperature is typical 22C/72F then you can expect the water temperature in a well sized cooling loop to be about 32C and even under load that should remain constant. A typical computer system will pump 0.04 liters of water per second. A CPU putting out an exceptional 320 watts would warm that water by 2C as it passes over. Not really a huge delta from internal to external.
The reason to have the water coming in at the center is not to use the delta, but the force of the flow coming in will reduce the amount of 'SKIN' that is present at the hot spots. As liquid flows through channels, the liquid in the center of the channel flows the fastest and that at the boundaries of the channel flow the slowest. Slower moving fluid is less capable of absorbing thermal energy and moving it away from the hot spots. So, you want the most turbulent flow in the heat spreader to be happening at the hottest spots. -
ElMoIsEviL
The water replaces the copper material that is removed. The surface area thus remains the same.bit_user said:An obvious problem I can see with the concept is that removing material from the IHS impairs its ability to distribute the heat. I'd expect an additive approach to work better, where channels are built up atop the IHS. Or, at the very least, don't remove (much) material right above the die, itself.
Also, I don't know much about water block design, but the path cut for those channels seems non-optimal.
High performance waterblocks do target the hot spot area as water atoms colliding with the copper will absorb more heat due to the vortex created. This is a lesson waterblock engineers learned a long time ago. DangerDen started with their Maze series, which is what this waterblock here does, and where beaten soudly by the Storm series of blocks which injected the water right at the center of the block with a restriction plate causing the water to have the same effect as placing your thumb at the end of a water hose to cause restriction and a strong stream of water. The temperature difference of the water is not relevant because it's a closed loop system. The entire water in the loop reaches an equilibrium.bit_user said:I think that's not what waterblocks typically do and I think I understand why. If you recall Newton's Law of Cooling, the rate of heat transfer is proportional to the temperature difference. If the center of the IHS is at 70 degrees and the edges are at 55 degrees, then having water hit the center first will quickly warm up the water (let's say to 50 degrees), which is almost the same as the edges. At this point, contact with the edges of the IHS won't extract much additional heat from it.
On the other hand, if you pump in the water at the edge and let it work its way up to the center, then it's extracting a more constant amount of heat, the whole way. So, maybe it gets to 40 degrees at the edge and reaches 45 degrees by the center. At this point, the delta is still enough for good heat extraction, but it's already taken heat from the edge.
Which scheme is better probably depends on a lot of specifics and would require proper modeling to know for sure. -
Pierce2623 This is a really cool idea but I think he should’ve left more material and gone from the center out just based on what I know of chip cooling best principles. That being said, as far as this is from my true “wheelhouse”, even though I have an engineering degree, I’m probably wrong lol.Reply -
bit_user
That's not how it works. Water isn't nearly as heat-conductive as copper. I'm reading it's like 0.6 W/mK, whereas copper is about 400 W/mK. So, when you remove copper from the IHS, you're impeding its ability to spread out that heat.ElMoIsEviL said:The water replaces the copper material that is removed. The surface area thus remains the same.
The idea of a heat spreader or a water block is to spread the heat over the greatest surface area, so that heat can transfer more efficiently into the water. -
YSCCC This looks like a fun project. But since it tis warranty void I woud thinkg it's better just to delid and get what better optimized jet channels a direct die water block can do. at leaset you don't try drill channels into the IHS which can accidentally cut into the die anywayReply -
ElMoIsEviL
No you're not. You are removing the heat with the water. Having a thick IHS doesn't help if you have no mechanism to remove the heat. It may take longer for a thicker piece of metal to become saturated with heat but it will nonetheless become saturated with heat. The water removes the heat. Your calculation doesn't take into consideration the constant flow of water. You're also comparing Copper to the Water when you should be comparing Water to Air.bit_user said:That's not how it works. Water isn't nearly as heat-conductive as copper. I'm reading it's like 0.6 W/mK, whereas copper is about 400 W/mK. So, when you remove copper from the IHS, you're impeding its ability to spread out that heat.
The idea of a heat spreader or a water block is to spread the heat over the greatest surface area, so that heat can transfer more efficiently into the water.
If what you say is true, then "delidding" (removing the IHS) wouldn't lead to better cooling performance. In fact direct water contact, if such a thing was possible, with the CPU die would cool better than having a copper medium in between. In the waterblock, you generally want a "heatsink" like set of fins over the area sitting atop the CPU die. This improves the surface area of the metal making contact with the water. Then you want a restrictive mechanism (Jet impingement) to constrict the flow of water over those fins to spread the water over the fin area in a more even fashion. Water takes the heat away from the CPU die and dumps it into the radiator. The constant flow of water is key.
This is how modern waterblocks are designed. The "Maze" design, by this user, is ancient and from the early days of watercooling.