TSMC's Arizona Fab 21 mass produces 4nm chips at a higher price than Taiwan
But customers are willing to pay extra, says TSMC.
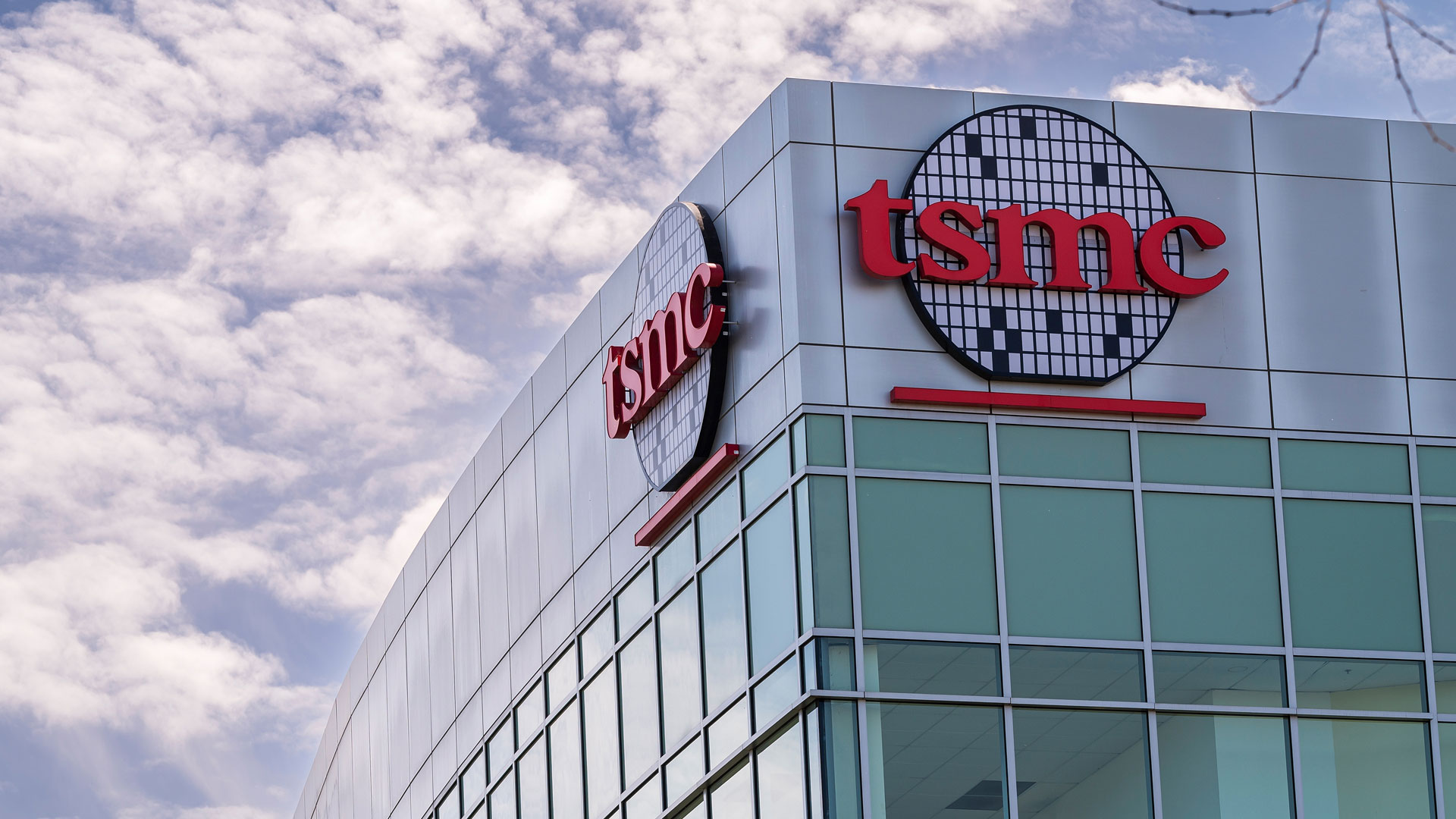
TSMC on Thursday officially confirmed that its Fab 21 near Phoenix, Arizona, had begun high volume production of chips after months of rumors and a confirmation from the U.S. Commerce Secretary earlier in January. The company emphasized that it is producing chips on one of its N4 process technology (4nm-class) and yields in Arizona are comparable to those in Taiwan. However, chips fabbed in the U.S. are more expensive than the same products made in Taiwan.
"We were able to pull ahead the production schedule of our first fab in Arizona, [it] already entered the high-volume production in Q4 2024 utilizing N4 process technology with a yield comparable to our fabs in Taiwan," said C.C. Wei, chief executive and chairman of TSMC, at the company's earnings conference call (via SeekingAlpha). "We expect a smooth ramp-up process and with our strong manufacturing capability and execution, we are confident to deliver the same level of manufacturing quality and reliability from our fab in Arizona as from our fab in Taiwan."
One interesting aspect of TSMC’s Fab 21 in Arizona is that TSMC charges more for N4 production in the U.S. than it does in Taiwan, so a processor made in America costs more than the same chip made in Taiwan. This is not unexpected, as chips produced by TSMC in Arizona cost more due to a more expensive fab that requires depreciation, smaller-scale production, a not-fully-developed ecosystem, and the necessity of shipping silicon back to Taiwan (or somewhere else) for packaging. However, it appears that TSMC also charges for ‘geographic flexibility.’ This does not mean that TSMC earns more from producing chips in the U.S., though.
"Do we charge a little bit higher? Yes, we do because we have a value of geographic flexibility," said Wei. "You guys know, [made in] USA is a premium product. Yes, we discussed [this] with our customer and they all agree and happy to work with TSMC. Because of the cost structure over there, so it is a little bit higher price over there."
Another interesting point revealed during the conference call was that TSMC is converting its N4/N5 capacity to N3 capacity as demand for 3nm-class products increases. While TSMC’s N4/N5 capacity is unknown, and kept confidential, it is evident that it is shrinking in Taiwan, so the U.S. fab could become instrumental in meeting demand for N4 and N5 production under certain circumstances.
Unverified reports suggest that TSMC's Fab 21 in Arizona is producing at least three types of processors: the A16 Bionic chip powering Apple's iPhone 15 and iPhone 15 Plus, the main processor in Apple's S9 system-in-package featuring two 64-bit cores and a quad-core neural engine for smartwatches, and a CPU from AMD's Ryzen 9000 series. It is rumored that for now only Fab 21 Phase 1A is mass producing chips and the current production capacity of the facility is around 10,000 wafer starts per month. TSMC's Fab 21 Phase 1B is reportedly 'facing tooling bottlenecks' and is expected to be fully equipped later in the quarter, which will add 14,000 WSPM capacity to the production facility.
Get Tom's Hardware's best news and in-depth reviews, straight to your inbox.
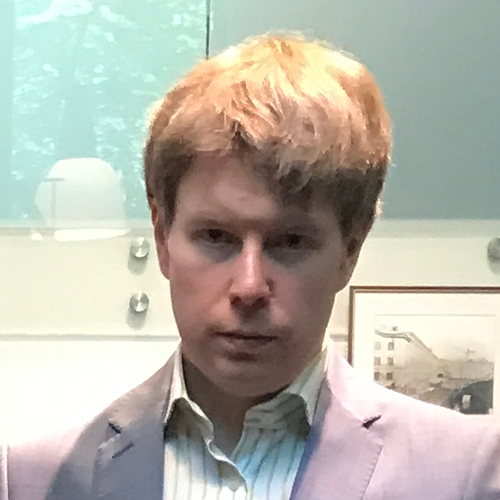
Anton Shilov is a contributing writer at Tom’s Hardware. Over the past couple of decades, he has covered everything from CPUs and GPUs to supercomputers and from modern process technologies and latest fab tools to high-tech industry trends.
-
usertests The amount makes all the difference. If it's +5%, I don't think companies care if their priority is getting a chunk of the additional wafer capacity. Made in USA printed on the chip doesn't matter too much, since most users will never see it.Reply
There may be smaller cost of shipping if they can be kept in the US, but if they need to be shipped to Taiwan for packaging then back to the US or something stupid like that, then it's a waste. That was something I heard early on, does anyone have any insight into the journey these wafers will take? -
Zaranthos I'll pay more for "Made in the USA" stamp alone. We can't outsource the production of literally everything to other countries just so we get cheaper stuff. If we want to reduce production costs we can start by cutting needless regulations that make even planing to build production like this cost money. In some cases you have to do an environmental impact study before you can start laying a foundation and you have to apply for who knows how many permits (that all cost fees and licenses or whatever). Then if you can even build it you have to contend with an army of lawyers and unions competing for ways to increase your labor costs. We just can't rely on everyone else to build the things we need for so many reasons.Reply -
watzupken In times where prices of practically everything are going up at a rapid pace, any increase in prices is not going to help most people. I don't really think the "made is the US" chip is going to be just 5% more expensive. There may be savings when it comes to shipping of the chip produced since it is produced locally, but given that most resources are sourced from Asia, you incur shipping fee on these resources instead. Furthermore, the cost of operating in US should be comparably higher than in Taiwan. So I think a premium upward of 10% to around 15% is the more likely scenario.Reply -
EricFromMinnesota The anti-regulation whiners complain when TSMC was able to build a fab that is now making world class 4nm chips within about 3 years. They also had to procure the machinery (99.99% chance it's from ASML in Europe) and hire or bring in the engineers to run it. I find it impressive and a good thing that some of these chips are now made in USA. Hopefully we'll also get some packaging manufacturing as well since it seems very ineffient and environmentally costly to ship twice for packaging.Reply -
BloodLust2222 Yea, I'm not willing to pay more. The "Made in the USA" chip means nothing. Things are too expensive already, We don't need more reasons for companies to raise prices all in the name of profits.Reply -
phead128 CHIPS ACT costs taxpayers $185,000 per new semiconductor job created per year, double the average semiconductor salary, according to Peterson report. (Source)Reply
But the government subsidies behind the expected chip manufacturing boom mean that each job created will cost taxpayers about $185,000 a year, the Peterson report found.
That’s twice the average annual salary of U.S. semiconductor employees, according to the report
Good luck scaling this beyond the token symbolic capacity at Arizona TSMC. -
OldAnalogWorld
The Intel example shows that not everything is so simple, as I have written in detail above and here...tamalero said:Translation:
The USA somewhat protects environment and somewhat forbids sweatshops. -
thestryker
TSMC has no advanced packaging within the US and I don't believe they're going to open one. There is the early stages of a deal with Amkor to bring advanced packaging solutions to the US. Amkor hasn't broken ground on the facility which would be doing this yet so it's a long way off.usertests said:There may be smaller cost of shipping if they can be kept in the US, but if they need to be shipped to Taiwan for packaging then back to the US or something stupid like that, then it's a waste. That was something I heard early on, does anyone have any insight into the journey these wafers will take?
That's a weird angle to take on the CHIPS Act as it was designed to increase silicon manufacturing within the US rather than being a jobs bill.phead128 said:CHIPS ACT costs taxpayers $185,000 per new semiconductor job created per year, double the average semiconductor salary, according to Peterson report. (Source)
Good luck scaling this beyond the token symbolic capacity at Arizona TSMC.