How to Polish Acrylic Edges for Your PC Case Mod
Let more light into your PC mod by polishing the acrylic edges.
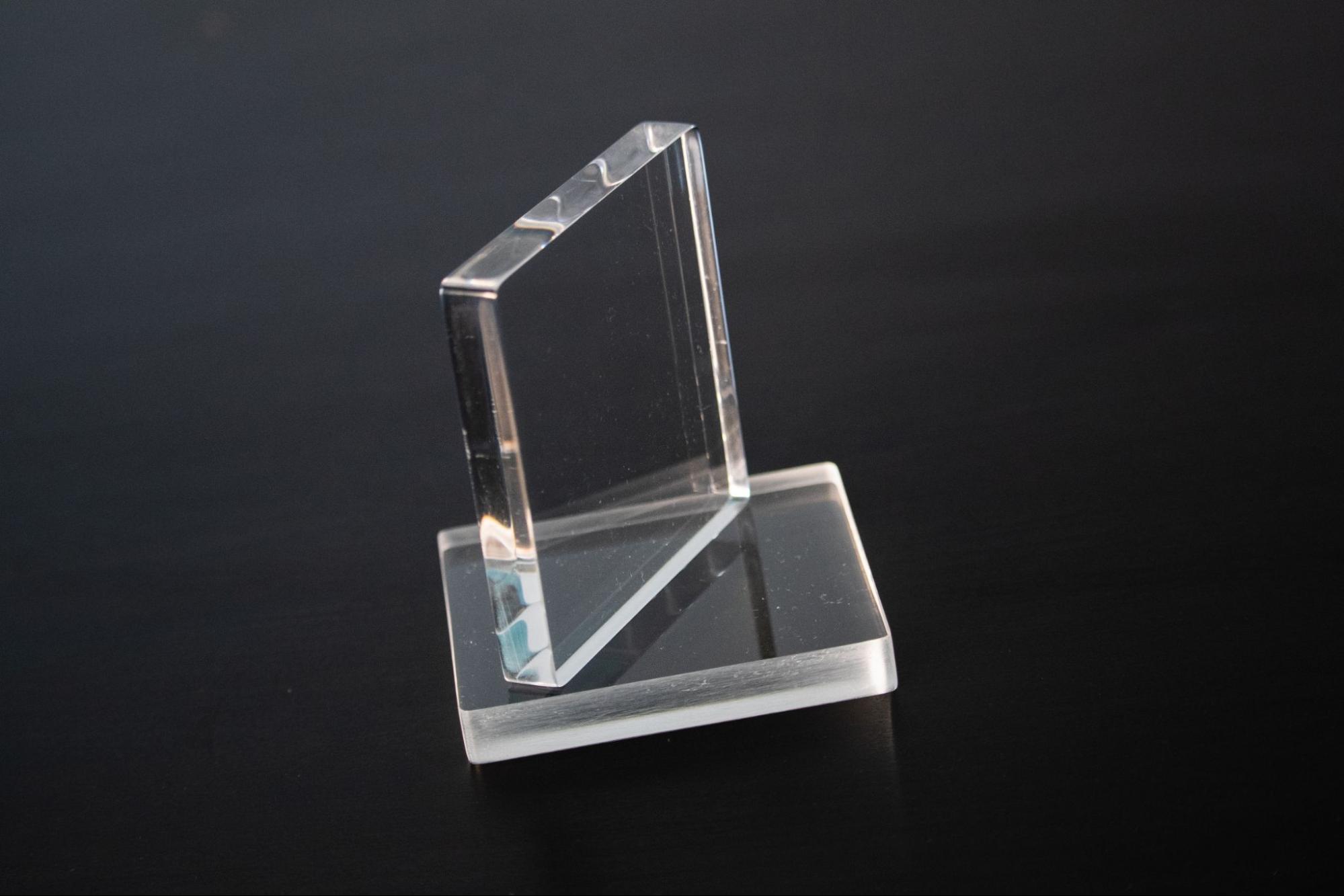
Acrylic is probably the most common material in PC Modding. It is widely used to make custom clear side panels, or any kind of custom panel because it can be painted to any finish and colour, it’s easy to work with and it doesn’t require expensive tools to cut. It can also be cheap, but that depends on the type of acrylic.
Of course, to use acrylic, you need to cut it and, after you cut it, you need to do some polishing to get the look that you want. You normally need to only polish the edges since standard acrylic is already clear on the surface. As a rule of thumb, any kind of cutting work on acrylic won’t leave a clear finish, and that’s why the edges are the most common part to polish. Below, I’ll explain how to polish acrylic for your case mode in order to get the best results.
If you have a CNC router to cut acrylic, like I do, the best solution is to use cast acrylic, because it has a higher melting point, compared to the extruded variant. If you’re using hand tools, like a hacksaw or even a scroll saw, you’ll be fine whichever type of acrylic you get. I’m going to use 10mm cast acrylic for this tutorial, but the same method should be applicable to any variant.
The method requires you to grab some different grits of sandpaper, ranging from 240-320 to 3000. The lowest starting point depends on how rough your edges are, but I generally don’t suggest going lower than 240 grit, since the scratches created will be more difficult to get rid of.
Examples in Custom PCs
Here you have a couple examples of polished edge acrylic parts I made for my modding projects:
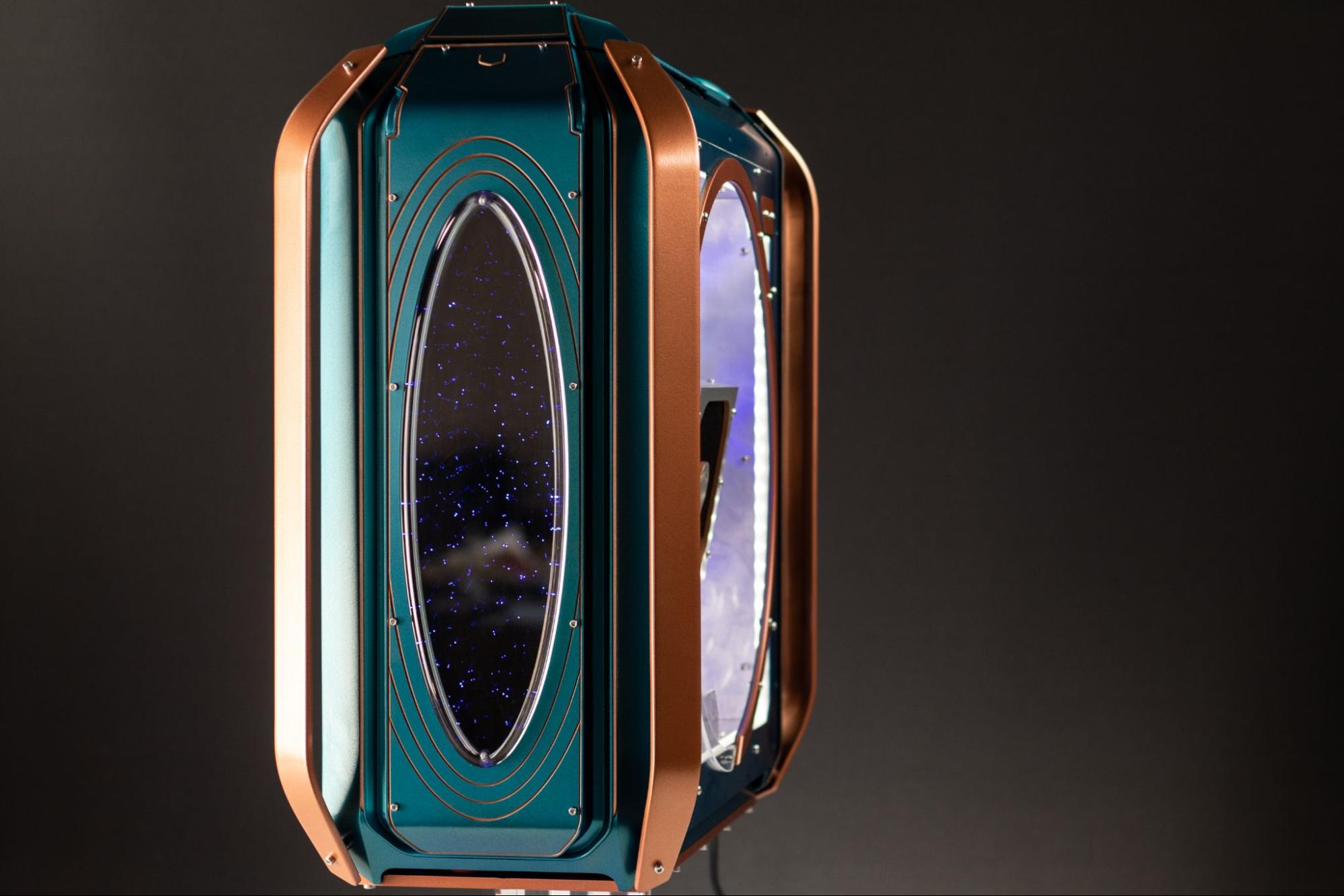

Well then, let’s get started!
Prepping the Parts for Sanding
First thing to do is cut two test squares, I purposely used a cheap end mill to cut them in order to get an opaque finish which is closer to what a hand cut piece would look like.
Get Tom's Hardware's best news and in-depth reviews, straight to your inbox.
If you want to get any kind of smooth finish on acrylic edges, you will have to sand them down with a thick grit, so you remove any flaws left from the cut.
Step 1: 320 Grit
In this case, I’m starting with a 320 grit which is already quite high for a rough sanding, but starting like this will give you less headaches later when you get to the higher grits, because you will have a less -scratched surface.
Make sure to be consistent on all areas of the edge because after polishing, because any flaw will show up even more. After the 320 grit, the edge should look uniform but obviously a bit scuffed up and rough to the touch.
Step 2: 600 Grit
For the next step go up to 600 grit sandpaper. After this step, the edge will show fewer scratches and will already feel pretty smooth to the touch.
At this point, the edge would be ready for something like a flame polishing, which is achieved by passing a torch along the edges and melting them. This will give you a very smooth and polished edge, but I personally don’t like this method because it can damage the acrylic if you don’t move the torch consistently and at the right power and distance. The sanding method I’m showing you takes a bit more time and elbow grease, but it’s much safer, consistent and it will give you a less distorted clarity, since you’re not melting the edge.
Here’s where I stop sanding one of the two test squares, to show you a different take on sand polishing towards the end of the tutorial.
Step 3: 1000 Grit
For standard polished edges, let’s go ahead and grab the 1000 grit sandpiper.
This step will start to show some kind of clarity on the edges. As always, remember to be consistent and sand every spot evenly.
Step 4: 2000 Grit
You could use 1500 grit after the 1000 one, but this time I’ll jump right to 2000 grit sandpaper, just to show you that it’s not necessary to go through ten different grit levels to get a super smooth and clear finish.
Step 5: 3000 Grit
I like to use 3000 grit sandpaper as the final step. I went up to 7000 grit in past works but it doesn’t really make a difference in this kind of application.
And this how it looks after all the sanding is done. The final touch will be polishing paste, which is also the most important and satisfying step.
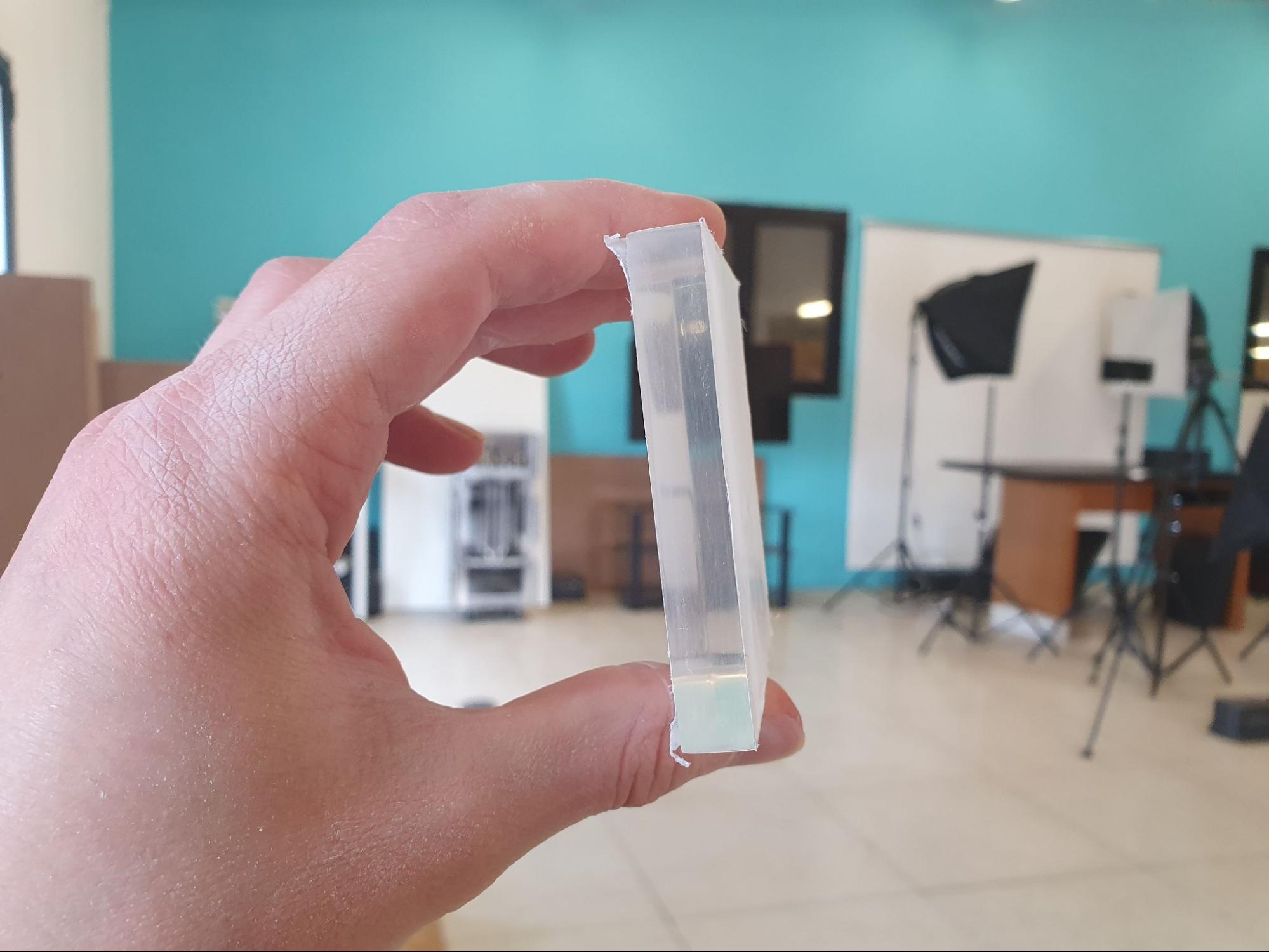
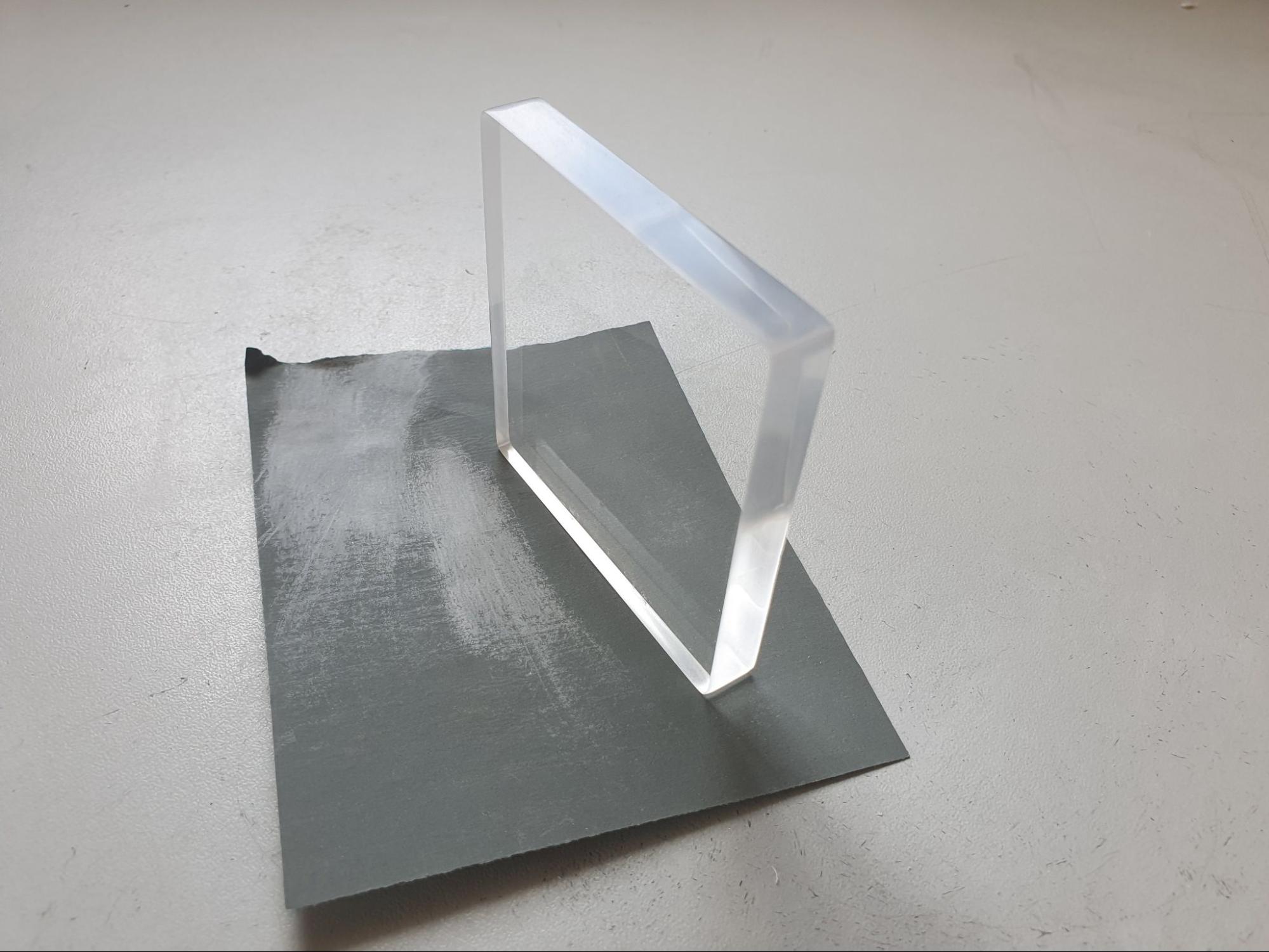
Step 6: Polishing Paste
I use a Mirka Polarshine 10 polishing paste, which is recommended for polishing epoxy resin, but I also used pastes for metals, so any kind of polishing paste will get the job done, if you’ve followed every step up until now. Obviously, there will be some more expensive ones that may give you a slightly better result, so make sure to do some research on what you find.
I use a microfiber cloth to apply the paste, which is the best way to do it for edges in my opinion, since the surface is so limited.
Pour a little paste on the edge and start rubbing it with the microfiber cloth, applying some force and speed to the movement.
Wash the piece with some water and soap to get rid of the residues from sanding and paste, and here you have an extra-shiny piece of acrylic!
A Bonus Option
Now, as I mentioned before, I’ll take the other test square, left by itself after applying the 600 grit, and I’ll just run the polishing paste on it! Why? If you think this won't give you a clear polished finish, you’re right. Fully frosted edges are usually the other main option for finishing acrylic, and this is kind of a “best of both worlds” solution.
The 600 grit will give you a smooth enough surface, not as clear, but that’s the important part! The slightly frosted edge will catch more light than a clear polished edge, and that will create a very cool looking effect, called “edge lighting”.
Applying polishing paste in this case will still make the surface shiny and a little more see-through, so the effect will tend to shift depending on light conditions and angle. Pretty cool if you ask me!
The next picture shows the first polishing piece on top, and the frosted/polished piece down below. You can clearly see how the second one has the edges lit up by the light coming from the softbox.
I hope this guide helps you give your custom parts some new light.