Der8auer admits he 'messed up' with underperforming Thermal Grizzly Heatspreaders and Direct Die coolers
Affected products have been delisted until a fix is found.
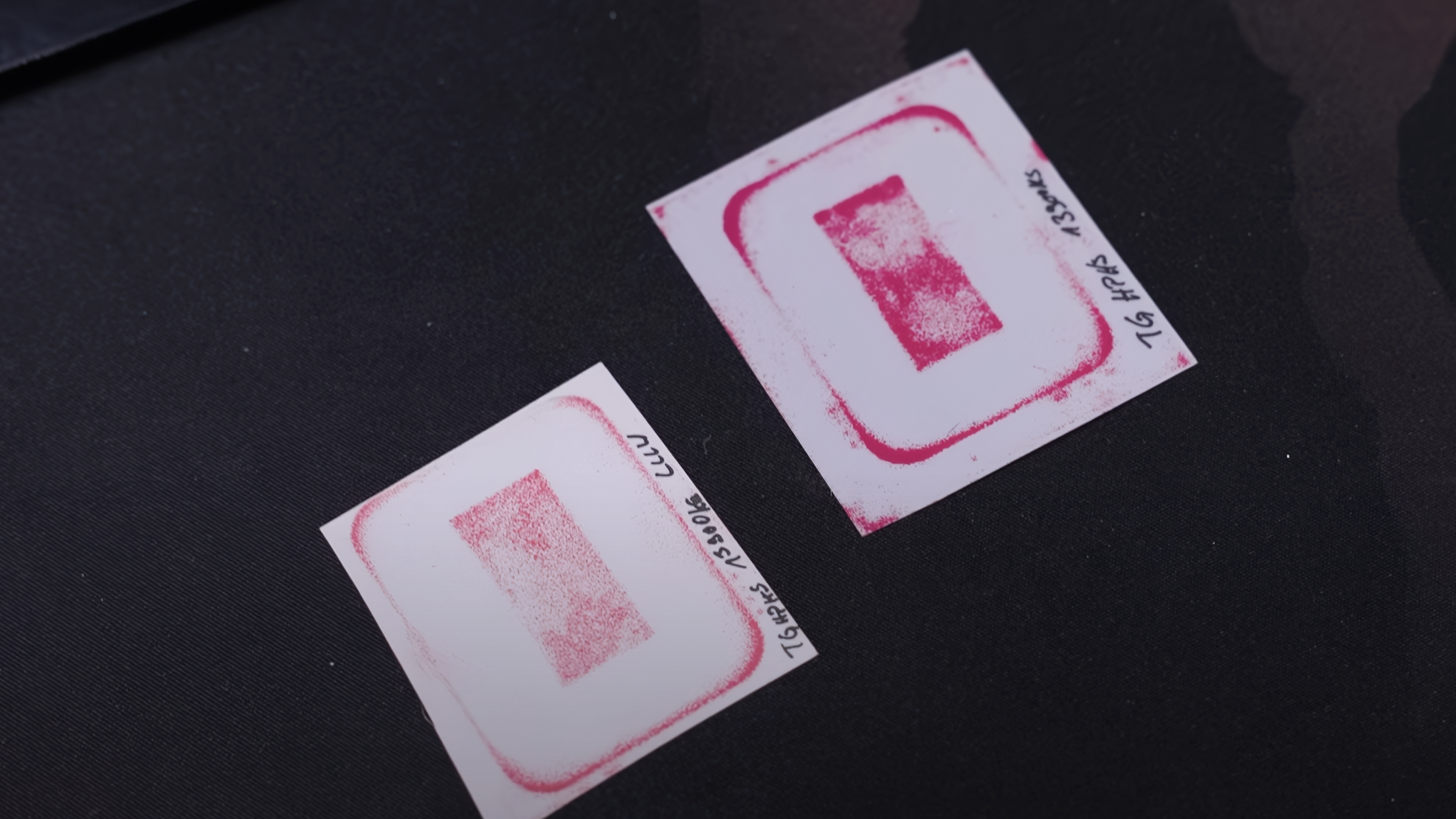
Yesterday, der8auer speaking in his capacity as CEO of Thermal Grizzly, released a statement on YouTube apologizing for the underperforming Intel High Performance Heatspreader (HPHS) V1 and Intel Mycro Direct Die V1 units, which were recently released touting cooling improvements of up to 15 degrees Celsius. Some defective units, however, precipitated thermals even warmer than the default CPU configurations.
In the video, Der8auer immediately apologizes for the underperforming products and signals his hopes of finding the underlying reasons why. The description of the original video also immediately directs those who have experienced these issues to the official Thermal Grizzly support page. Until the issues are resolved and Der8auer figures out the exact cause, the products are no longer available to purchase.
As the video progresses, Der8auer gives viewers a deeper view of the manufacturing process behind their latest Intel HPHS and Mycro Direct Die units. The manufacturing floor is where diagnostics are being run on the designs to help iron out what caused these issues, and Der8auer highlights having tested over 50 different designs with the same underlying backplates/bottom structures.
As it turns out, Thermal Grizzly Heatspreaders and Mycro Direct Die liquid cooling surfaces share bottom structures, whether they are made for AMD or Intel. The contact frames for both are also made from aluminum.
Quality control methods shared in the video include placing the copper bottoms of Heatspreaders and Direct Dies under a device used to measure exact height differences and evenness and the use of pressure-sensitive paper to verify good contacts between the CPU and cooling surface. While Der8auer is able to express confidence in the Heatspreader and Mycro Direct Die V1 for things like thermal paste distribution, he makes clear that these products won't be sold again until the exact cause of the underperforming units is determined.
Fortunately, most users who would even consider buying these products shouldn't have too much trouble working around technical difficulties, especially if Thermal Grizzly lives up to its CEO's words and makes impacted customers whole. After all, delidding your CPU is about as far from an amateur's project as it gets. At least it isn't a truly disastrous issue threatening the functionality of the chips in question.
In any case, it's unlikely that we'll be seeing the proposed RGB or AMD versions of these products until the issues with the original Intel models have been confidently identified and fixed.
Get Tom's Hardware's best news and in-depth reviews, straight to your inbox.
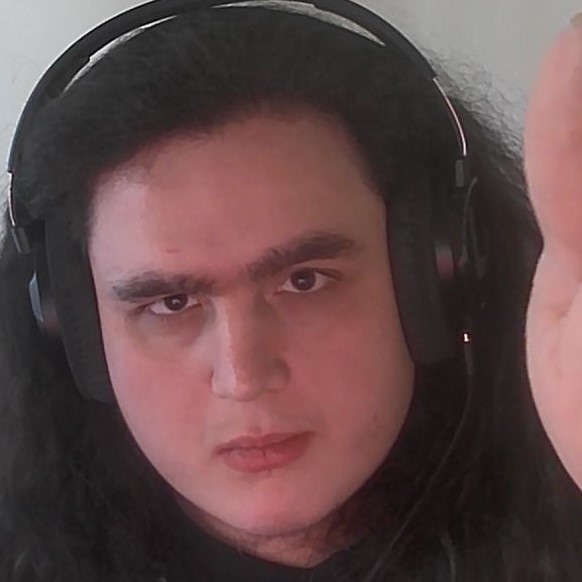
Christopher Harper has been a successful freelance tech writer specializing in PC hardware and gaming since 2015, and ghostwrote for various B2B clients in High School before that. Outside of work, Christopher is best known to friends and rivals as an active competitive player in various eSports (particularly fighting games and arena shooters) and a purveyor of music ranging from Jimi Hendrix to Killer Mike to the Sonic Adventure 2 soundtrack.