Bluetooth Technology 101
From keyboards to headsets to mobile computing, Bluetooth provides the personal wireless network needed to get around without a bunch of cables entangling our lives. Here's a close look at a key technology that empowers our mobile world.
Hardware, Manufacturing And Host Integration
At the lowest level, a Bluetooth device has two key components: a radio and a baseband controller. Simple enough, right? But the small footprint, interoperability constraints and low-cost objectives of Bluetooth technology make manufacturing modules and devices a difficult engineering task when it comes to RF chip design. The challenge is appreciable enough that companies are fanatic about safeguarding their IP, and will often not provide detailed designs for the base Bluetooth IC/SoC even to the vendor that is manufacturing/integrating the final consumer device.
At the highest level of engineering design, the first decision to make about Bluetooth is its integration with the host product. There are almost as many ways to implement Bluetooth integration in a consumer end-product as there are classes of products. Broadly, they can be classified as:
- Integrated single-chip, where the baseband circuits and Bluetooth radio are completely integrated into the host SoC module. This type of approach is most commonly used in headsets, and the design complexity of a single chip like this is overshadowed by the lower cost of manufacturing and integration.
- Standalone single-chip, where a single Bluetooth SoC containing the baseband circuitry and radio is integrated into a larger system assembly. This is commonly seen on computer peripherals like Bluetooth keyboards and mice, or certain types of smartphones and tablets. Pre-certified Bluetooth modules can be used to save on costs.
- Dual-chip, where the baseband circuits and radio are housed in two separate IC packages. This approach has lost ground to the single-chip approach, and is most often seen when the radio sticks to analog operation and the baseband IC is digital.
The hardware integration is closely (but not always) tied to the partitioning of the Bluetooth protocol stack. Where the Bluetooth implementation is completely integrated with the host, it is the host’s software/firmware and host’s computing resources that are used to manage the upper and lower stacks and the API. In all other cases, the radio and baseband circuits always handle the lower stack (LM, LC and down), so the difference is in where and how the upper stack is managed. For a standalone single or radio-baseband-dual chip, a microcontroller implements the upper stack and there is often no need for the API. When Bluetooth shows up as a host add-on, for example in a Bluetooth adapter for a PC, the Bluetooth plug-in module handles the lower stack, the module communicates with its host through HCI and the host software/drivers handle the upper stack and API. Finally, in the host ASIC case, everything sits on the single Bluetooth chip, and the API on the host machine/device communicates with the module.
Manufacturing
The actual Bluetooth radio and baseband chips (whether single SoC or dual-chip solutions) are manufactured using different technologies based on the application. There are variations on CMOS (complementary metal–oxide–semiconductor) chips, gallium-arsenide (GaAs) chips and the most common—silicon-germanium (SiGe) semiconductors in varying packages turned into modules using LTCC (low-temperature co-fired ceramic) films or PCBs (printed circuit boards).
CMOS variants can include the standard bulk CMOS approach, RF (radio frequency) CMOS and SOI (silicon-on-insulator). Traditional bulk CMOS is used to build the digital-only baseband chip, and then chained to an analog circuit for the Bluetooth radio. RF-CMOS adds the radio directly onto the CMOS chip, and SOI adds an insulator layer between the RF and BB circuits for isolation.
GaAs chips are used in “ruggedized” or military applications, since gallium arsenide devices are more resistant to high levels of electromagnetic pulsed radiation—they can be knocked offline by an EMP, but the component isn't reduced to slag. Since the manufacturing process for GaAs is completely different than CMOS (and far more expensive), most manufactures serving the consumer market no longer develop GaAs chips.
An RF chip made from SiGe has higher efficiency and greater throughput than a pure silicon semiconductor-based radio. The choice of silicon CMOS or SiGe BiCMOS depends on the application—where cost is a factor, a standard CMOS die is used, whereas for applications that require better RX or TX sensitivity/power or low power consumption, BiCMOS is used. The final packaging also depends on manufacturer requirements and final device/application: leaded SOIC (small outline integrated circuit), QFP (quad flat package) or PLCC (plastic leaded chip carrier).
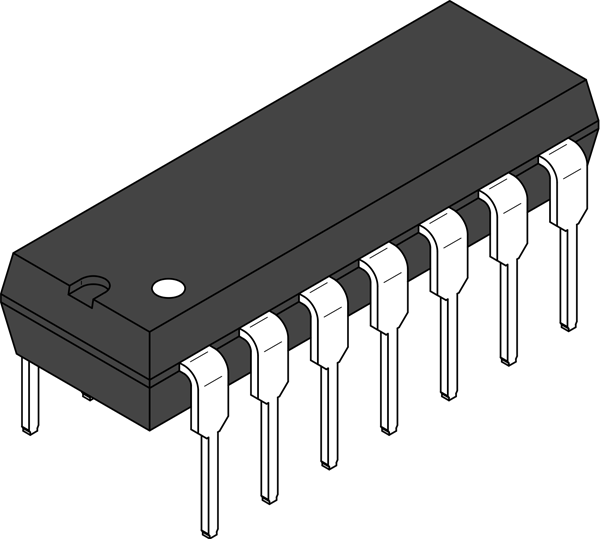

Pictured above are the SOIC package and the BGA package.
Leadless designs (BGA—Ball Grid Array, CSP—Chip Scale Package, WLCSP—Wafer Level Chip Scale Package) are used for devices like smartphones, where small footprints are important and generally present good cost savings over QFP packages.
Qualification, Testing And Certification
Imagine a large room—a conference hall, perhaps—where engineers and representatives from dozens of manufacturers, either collaborators or competitors or sometimes both, bombard each other with Bluetooth signals. This is UnPlugFest, an event organized by the SIG, where manufacturers come to test the interoperability of their devices. Interoperability is a key aspect of the Bluetooth standard, and one of the many tests a device must undergo before it is qualified by the SIG.
The SIG imposes qualification requirements in the form of the Bluetooth Qualification Program (BQP), including product performance and compliance with the Bluetooth specifications. Once it passes the BQP, the product must be certified, by the FCC in the USA, CE in the EU, TELEC in Japan, etc. The entire certification cycle can take more than a year, and may cost up to tens of thousands of dollars in testing and administrative fees.
Given the complexity, length and high cost of designing and certifying Bluetooth modules, many manufacturers choose to use a pre-certified module in their final consumer product—laptops are a good example of this. Essentially, if a product uses a pre-certified module, the certificate comes with a very strict set of guidelines as to its maintenance, but otherwise can be used without further testing or qualification.
Current page: Hardware, Manufacturing And Host Integration
Prev Page Bluetooth Security Next Page Major Bluetooth ManufacturersGet Tom's Hardware's best news and in-depth reviews, straight to your inbox.
-
Fernando_engen Bluetooth is pretty much the future. I have just started developing Bluetooth Low Energy Services/profiles for specific use cases along with the application layer. Its an awesome new world.Reply -
YunFuriku Actually hearing aids with button cell batteries these days can use Bluetooth Smart or to be exactReply
bastardized proprietary version of it by Apple and GN Resound which enables them to have wireless audio streaming from
various devices with Bluetooth. Comes with expense of range naturally because hearing aids need to use low power version of it (1,5V doesn't give much choice on this )
Max 10m in ideal conditions.
Sadly, the audio stack they use is Apple Exclusive so direct connection is Apple devices only.
Non-apple devices require intermediary devices such as TV streamer or Phone Clip to other Bluetooth Capable phones. These devices are relatively cheap compared
to old FM tech hearing aids used to use where transmitter prices were measured in 0,5-2k range, about ~$200-300 at most.
Unfortunate side is that if you want to use it with non-Apple phones you'll have to have intermediary device which serves as bluetooth handsfree mic/answer/volume
buttons too beause of the audio stack which Apple won't license to others.
At the same time Apple is pushing their made for iPhone hearing aid tech to FCC to be recognised as standard.
Here's to hoping hardcore android fan like me won't have to buy iPhone as my next phone if this doesn't come to other phones directly because of silly audio stack :P
-
RIluske Is the graphic about memberships correct? I thought the article said the third tier was free to join, but the graphic has it costing the same amount as second tier.Reply -
zodiacfml I feel WiGig has a better future eventually. Bluetooth will be left to activation or turning on devices or IoT as already mentioned in the article.Reply -
DotNetMaster777 Very useful article !! bluesniping can be done over one km away wow !?!?Reply
Are there any performance tests between wifi and bluetooth ?? -
exnemesis Just give me bluetooth tech that can allow me to walk away 40-50m from my phone and penetrate better through walls and objects and still retain the quality of whatever it is I'm listening to on my phone.Reply -
TripleHeinz This is the best article I've ever read in Tom's. Didn't have a clue that bluetooth was related with Thor the god of thundervolt ;)Reply -
yasminpriya15 Welcome to Bluetooth 101. Here are the top things you need to know about Bluetooth technology.Reply
My Bluetooth doesn’t work. What do I do?
The Bluetooth SIG does not make, manufacture or build any Bluetooth products. We simply support our membership and help them to help make the best products on the market. The best way to solve your problem is to contact the manufacturer directly or start by researching solutions on the Internet.
What is Bluetooth?
Bluetooth is a global wireless communication standard that connects devices together over a certain distance. Think headset and phone, speaker and PC, basketball to smartphone and more. It is built into billions of products on the market today and connects the Internet of Things (IoT). If you haven’t heard of the IoT, go here.
How does Bluetooth work?
A Bluetooth device uses radio waves instead of wires or cables to connect to a phone or computer. A Bluetooth product, like a headset or watch, contains a tiny computer chip with a Bluetooth radio and software that makes it easy to connect. When two Bluetooth devices want to talk to each other, they need to pair. Communication between Bluetooth devices happens over short-range, ad hoc networks known as piconets. A piconet is a network of devices connected using Bluetooth technology. The network ranges from two to eight connected devices. When a network is established, one device takes the role of the master while all the other devices act as slaves. Piconets are established dynamically and automatically as Bluetooth devices enter and leave radio proximity. If you want a more technical explanation, you can read the core specification or visit the Wikipedia page for a deeper technical dive.
Are there different kinds of Bluetooth?
There are actually several “kinds”—different versions of the core specification—of Bluetooth. The most common today are Bluetooth BR/EDR (basic rate/enhanced data rate) and Bluetooth with low energy functionality. You will generally find BR/EDR in things like speakers and headsets while you will see Bluetooth Smart in the newest products on the market like fitness bands, beacons—small transmitters that send data over Bluletooth—and smart home devices.
What can Bluetooth do?
Bluetooth can wirelessly connect devices together. It can connect your headset to your phone, car or computer. It can connect your phone or computer to your speakers. Best of all? It can connect your lights, door locks, TV, shoes, basketballs, water bottles, toys—almost anything you can think of—to an app on your phone. Bluetooth takes it even further with connecting beacons to shoppers or travelers in airports or even attendees at sporting events. The future of Bluetooth is limited only to a developer’s imagination.
What makes Bluetooth better than other technologies?
The short answer is because Bluetooth is everywhere, it operates on low power, it is easy to use and it doesn’t cost a lot to use. Let’s explore these a bit more.
Bluetooth is everywhere—you will find Bluetooth built into nearly every phone, laptop, desktop and tablet. This makes it so convenient to connect a keyboard, mouse, speakers or fitness band to your phone or computer.
Bluetooth is low power—with the advent of Bluetooth Smart (BLE or Bluetooth low energy), developers were able to create smaller sensors that run off tiny coin-cell batteries for months, and in some cases, years. This is setting the stage for Bluetooth as a key component in the Internet of Things.
Bluetooth is easy to use—for consumers, it really can’t get any easier. You go to settings, turn on your Bluetooth, hit the pairing button and wait for it start communicating. That’s it. From a development standpoint, creating a Bluetooth product starts with the core specification and then you layer profiles and services onto it. There are several tools that the SIG has to help developers.
Bluetooth is low cost—you can add Bluetooth for a minimal cost. You will need to buy a module/system on chip (SoC)/etc. and pay an administrative fee to use the brand and license the technology. The administrative fee varies on the size of the company and there are programs to help startups. http://www.traininginsholinganallur.in/qtp-training-in-chennai.html
http://www.traininginsholinganallur.in/primavera-training-in-chennai.html
http://www.traininginsholinganallur.in/big-data-analytics-training-in-chennai.html