Silicon Who? Researchers Develop Arm Microprocessor Built out of Plastic
Truly bendable devices pave the way for the Internet of Everything
Researchers with Arm and PragmatIC have developed the first true microprocessor that employs plastic — not silicon — as its base material. The 32-bit PlasticArm microprocessor concept is based on the company's M0 design and features around 18,000 logic gates, a processor, memory, controller, and inputs and outputs. The development, published in Nature, will allow a new era of truly bendable, flexible microchips that are also cheaper to produce than silicon.
Silicon has been the base element for semiconductor manufacturing since the dawn of computing, which began over 50 years ago with the introduction of Intel's 4004 CPU. That packed an at the time astonishing 2,300 transistors. Silicon's rise to power is predicated on two fundamental characteristics. First, it's the second most common element on Earth (which means it's both cheap and readily available). Second is the capability to function as either an energy conductor or an energy insulator, depending on its implementation.
However, silicon does have some caveats that are becoming more and more limiting in regards to the scope of its applications. For one, it's brittle and rigid, meaning that it can't be easily integrated in actual biology — nature has a way of not enjoying straight lines when it comes to cooking up life. The second important caveat is that while it may be cheap to produce, it's certainly not cheap enough to be used in everyday, expendable products in a cost-effective way. Enter the PlasticArm development, which aims to enable plastic as a medium with which processing chips can be built, skirting both those limitations.
This is not a replacement for silicon, mind you. The researchers point out that silicon presents advantages in terms of performance, density, and power efficiency. Instead, the two technologies are expected to complement each other according to the application requirements.
The researchers point out possible applications in bottles (for smart milk or juice bottles that analyze whether or not the product has gone rancid), food packages, garments (imagine a sweater that smartly detects body or outside temperature and increases the space between fibers for better cooling), wearable patches, bandages, and so on. Other possible applications include biomonitors. Imagine a thin plastic, computing-capable film that's placed on internal organs or tissue for diagnostics and early signs of trouble. Wearable electronics patches that can display information directly on your skin another option, or less-invasive diagnostics for wildlife monitoring.
Researchers predict scaling capabilities of up to 100,000 logic gates before power consumption becomes a problem and additional materials are required for the manufacturing process. Even so, the test chip only consumes around 21 milliwats of power — most of it wasted in idle states — which could easily be provided solar cells smaller than postage stamps. Eventual charging mechanisms will look toward wireless charging technologies, enabling true self-contained chips.
The PlasticArm prototype further garners attention due to the fact that it was manufactured with well-known technologies used in mainstream silicon manufacturing, allowing it to benefit from years of innovation.
Get Tom's Hardware's best news and in-depth reviews, straight to your inbox.
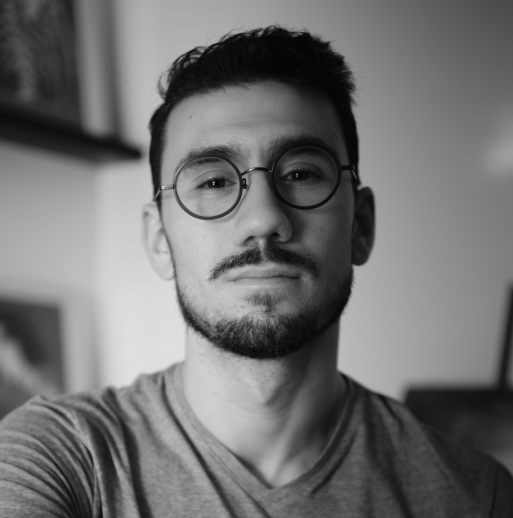
Francisco Pires is a freelance news writer for Tom's Hardware with a soft side for quantum computing.