How We Test Power Supply Units
Our methodology, testing equipment, and benchmarks.
We use several fully equipped Chroma stations. They can deliver more than 4 kW of load and consist of two 63601-5 and one 63600-2 mainframes. The mainframes mentioned above host ten 63640-80-80 [400 W] electronic loads, along with a single 63610-80-20 [100 W x2] module.
Chroma loads are widely used by all PSU manufacturers and are pretty much the standard for PSU measurements. Finally, all of our equipment is controlled and monitored by a custom-made software suite that's highly sophisticated.
In addition to the Chroma loads, we also use two Chroma AC sources (6530 with 3kW and 61604 with 2kW max power), Kesight DSOX3024A and Rigol DS2072A oscilloscopes, several Picoscope 4444 oscilloscopes, and TC-08 thermocouple data loggers, two Fluke multimeters (models 289 and 175), a Keithley 2015 THD 6.5- digit bench DMM and four lab-grade 3-phase power analyzers (three N4L PPA1530 and a single PPA5530). We recently acquired some Rohde & Schwarz HMC8015 power analyzers.
To protect our Chroma AC sources, we use high-quality online (meaning that they always run off the battery providing the best possible protection and line filtering) UPS systems with 3000VA/2700W capacity each. Two from FSP (Champ Tower 3k), and the other two by Cyberpower (OLS3000E).
Our testing gear also includes hotboxes, which allow us to test PSUs at high ambient temperatures. Finally, we have a Class 1 Brüel & Kjaer 2250-L G4 Sound Analyzer equipped with a type 4955-A low-noise and free-field microphone that can measure down to 5 dB(A) (we also have a type 4189 microphone that features a 16.6-140 dBA-weighted dynamic range). We also have a Class 1 Brüel & Kjaer 2270 Sound Analyzer, equipped with a type 4955-A microphone.
The infrared camera is a high-end Fluke model, the Ti480 Pro. Using an IR camera is not so straightforward, especially in a PSU, since you have to apply a special coating or paint to the parts you want to check. In any case, we also double confirm our findings through temperature probes.
We have several soldering and desoldering stations that we use during the dismantling process of every PSU we test. Test results are one thing while checking out the build quality of a PSU is another. Finally, if we encounter any unusual results during the testing process, we examine the internals of a PSU to find out what is causing the issues.
Get Tom's Hardware's best news and in-depth reviews, straight to your inbox.
MORE: Best Power Supplies
MORE: All Power Supply Articles
MORE: Power Supplies in the Forums
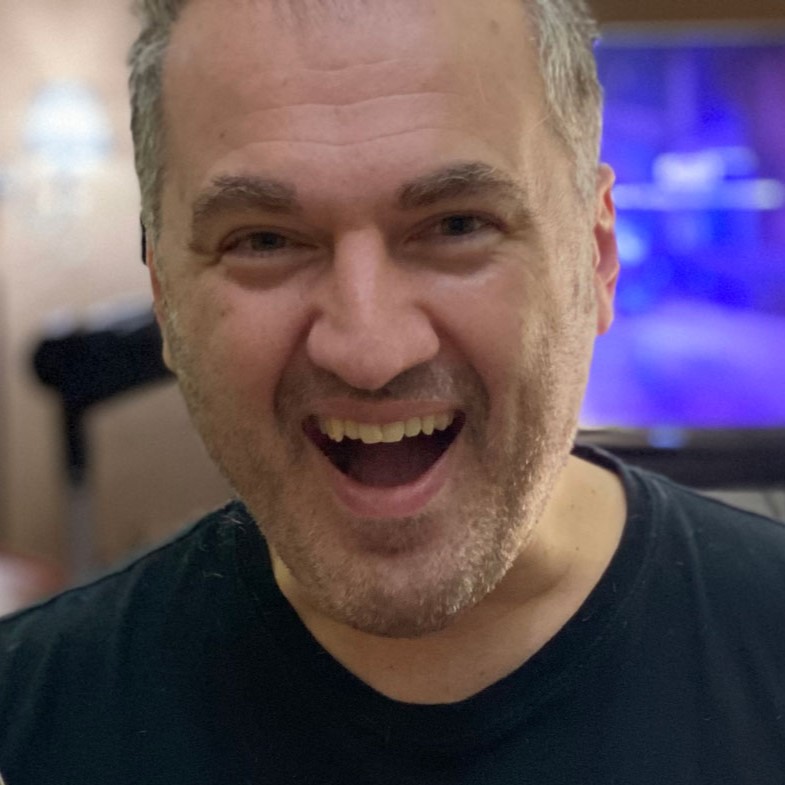
Aris Mpitziopoulos is a contributing editor at Tom's Hardware, covering PSUs.
-
JPNpower Nobody can fault you guys for not being thorough enough! All we can wish for is that you do these tests a bit more often. I'm at a loss how to navigate the PSU field, and a "Best Picks" section for PSU's would be tremendously helpful.Reply -
Nuckles_56 Really good article, it is now nice and clear how you guys go and test the power supplies, and as JPNpower said, no one can fault you guys for not being thorough enough.Reply -
ykki @JPNpower= I also think a best psu for the money article would be nice but the power supplies in the market pretty much stay the same. We may go for months before seeing any change in the list.Reply -
damric Looks legit, Aris.Reply
THW used to be the laughing stock of PSU reviews, but your recent reviews have changed all of that.
Keep up the good work! -
damric Nobody can fault you guys for not being thorough enough! All we can wish for is that you do these tests a bit more often. I'm at a loss how to navigate the PSU field, and a "Best Picks" section for PSU's would be tremendously helpful.
@JPNpower= I also think a best psu for the money article would be nice but the power supplies in the market pretty much stay the same. We may go for months before seeing any change in the list.
I'll make one and submit it through bb-71 to get stickied. -
ykki 15570872 said:I'll make one and submit it through bb-71 to get stickied.
OK. If someone makes a psu list I'd rather see it from you (or the mods). Good luck. -
damric 15570891 said:15570872 said:I'll make one and submit it through bb-71 to get stickied.
OK. If someone makes a psu list I'd rather see it from you (or the mods). Good luck.
It will be a group effort for sure :) -
iam2thecrowe It would be nice if all manufacturers could do this testing and publish results when they build the things, or even better for it to be a requirement. Then at least there would be less junk PSU's on the market.Reply -
ykki
Or more fake reviews.15571045 said:It would be nice if all manufacturers could do this testing and publish results when they build the things, or even better for it to be a requirement. Then at least there would be less junk PSU's on the market.