Issues with Chip Packaging to Affect Supply of Client Processors in 2021
Insufficient wirebonding capacities and ABF substrate supply might hurt PC market.
Demand for client PCs, consumer electronics, servers, and other high-tech equipment is driving sales of various processors and in the recent quarters semiconductor supply chain has failed to meet demand for chips. Not only do foundries not have enough capacity to build silicon for their clients, but lead times at packaging houses have also increased significantly. Based on media reports, issues with chip packaging will affect supplies of client CPUs and GPUs as well as various consumer-grade electronics throughout the whole year.
Different chips use different types of packaging. Small integrated circuits (ICs) that do not require a complex power supply and do not need many input/output pins tend to use cheap wirebond packages. More complex devices use leadframe packages (quad flat packages (QFP), quad/dual flat no-lead packages (QFN/DFN), thin small outline profile packages (TSOP), etc.), which are generally wirebond packages encapsulated into plastic or other types of mold for added rigidity and reliability.
Chips that use many power and I/O pins — such as CPUs, GPUs, and SoCs — typically use laminated flip chip ball grid array (FC-BGA) packages that provide fine pitches, low inductance, ease of surface mounting, and excellent reliability among other things. Meanwhile, there are BGAs that continue to rely on wirebonding and there are BGAs that use flip chip packaging.
Insufficient Wirebonding Capacities
Wirebonding packages are used by such popular commodity chips as display driver ICs as well as TDDI (touch with display driver integration) chip solutions. Insufficient supplies of DDICs as well as TDDIs affected shipments of monitors and notebooks last year, as some PC makers complained back in the fourth quarter.
By now, OSAT (outsourced assembly and test) houses like ASE Technology (the world's No. 1 chip packaging company), Greatek Electronics, and Lingsen Precision Industries have stretched their lead times for wirebonding packages to two, three, or even more months because of insufficient capacities, reports DigiTimes. OSAT companies did not comment on the news story.
Adding equipment for wirebonding is a relatively straightforward task, but because of high demand manufacturers of such tools, namely Kulicke & Soffa as well as ASM Pacific Technology, have increased their delivery lead times up to nine months. Meanwhile, Advantest, which makes test equipment for DDICs and TDDIs, has also extended its lead times to over six months.
Without sufficient wirebonding capacities, at least some display and PC makers will continue to suffer from shortages of various crucial components, such as display driver ICs, for at least two quarters. Alternatively, they will have to find additional sources of components, or their suppliers will have to find alternative assemble and test partners. In both cases, the actions will take time.
Get Tom's Hardware's best news and in-depth reviews, straight to your inbox.
Not Enough ABF Substrates
Laminated packages are used by a wide variety of semiconductors ranging from cheap SoCs for client PCs all the way to complex high-end CPUs for servers and 5G equipment. Chips that use laminated packaging often use IC substrates featuring insulating Ajinomoto build-up film (ABF), which are made by only one company, Ajinomoto Fine-Techno Co. Apparently, some suppliers of ABF substrates experience yield issues with their products.
Yield rate for ABF substrate production at Taiwan-based suppliers Unimicron Technology, Nan Ya PCB, and Kinsus Interconnect Technology is now about 70% or lower for high-end offerings, according to DigiTimes. The companies are trying to gradually expand production, but they will only be able to boost it by around 10% from 2021 to 2022, the report says.
In particular, Unimicron is reportedly considering repurposing one of its damaged production facilities to make ABF substrates, but the plan has not been finalized, so it unlikely that the new factory will go online earlier that at least a year from now. Neither of the companies has confirmed or denied the story. To a large degree such a small increase is a consequence of the fact that delivery lead time for ABF substrates manufacturing tools are now at now are four to three quarters, the article claims.
Since demand for advanced chips is increasing across the board, processor developers naturally give priority to higher-end products, such as those for supercomputers, datacenters, servers, and advanced client PCs. ABF substrates suppliers have to satisfy demands of their customers, which is why they naturally give priority to higher-end substrates in their production too. As a result of shifting priorities of both chipmakers and substrate suppliers, capacities for entry-level and midrange processors for laptops are shrinking, which creates further shortages on the market.
Not a Catastrophe?
It is not the first time in recent memory when the industry experienced shortages of crucial components.
In recent years, the industry also faced a tight supply of Intel CPUs as the company could not meet demand for parts produced using its 14 nm fabrication process. The company naturally prioritized supply of its higher-end Xeon Scalable as well as Core i5/i7/i9 processors over entry-level Core i3, Pentium, or SoCs for midrange and low-end PCs. While PC makers were not exactly happy with undersupplies, they did not really struggle. This time around, the situation is different as companies like Dell or HP cannot get enough a variety of components.
Insufficient packaging capacities at some manufacturers and assembly and test services create a tight supply of ABF substrates and an unpleasant situation for the industry. Yet, it is not unfixable.
Increased delivery lead times for equipment makers indicate that there are companies, which have acquired necessary tools and which will obtain them earlier than others. These companies will use this equipment to assemble and test chips, which will reduce load on other OSAT providers. Alternatively, integrated device manufacturers (IDMs) could at least produce chips needed by the industry.
In either case, high demand for PCs, electronics, servers, and other types of equipment means higher prices, so for the next couple of quarters many products will continue to cost more than their MSRP.
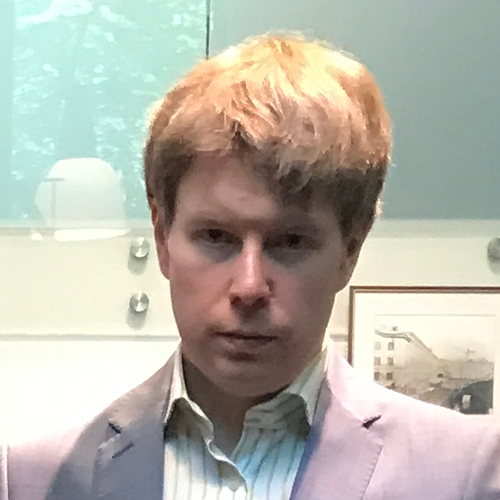
Anton Shilov is a contributing writer at Tom’s Hardware. Over the past couple of decades, he has covered everything from CPUs and GPUs to supercomputers and from modern process technologies and latest fab tools to high-tech industry trends.