Study Shows How Fragile Semiconductor Industry Still Is
It's a global problem.
The Semiconductor Industry Association (SIA) and Boston Consulting Group (BCG) published a report today detailing the, well, semiconductor industry's weaknesses as the entire world attempts to figure out how to respond to the ongoing chip shortage.
Many enthusiasts probably know the biggest issue: The semiconductor industry relies on many companies around the globe, but most operate within a very specific niche, giving them significant influence over their domain. This results in a supply chain that is both dangerously small and dazzlingly large, geographically speaking.
"There are more than 50 points across the supply chain where one region holds more than 65% of the global market share," SIA and BCG said in their report, adding that manufacturing is "a major focal point when it comes to the resilience of the global semiconductor supply chain." They went on to explain:
"About 75% of semiconductor manufacturing capacity, as well as many suppliers of key materials — such as silicon wafers, photoresist, and other specialty chemicals — are concentrated in China and East Asia, a region significantly exposed to high seismic activity and geopolitical tensions. Furthermore, all of the world's most advanced semiconductor manufacturing capacity — in nodes below 10 nanometers — is currently located in South Korea (8%) and Taiwan (92%). These are single points of failure that could be disrupted by natural disasters, infrastructure shutdowns, or internal conflicts, and may cause severe interruptions in the supply of chips."
We've seen numerous examples of those dangers in the last few months. Natural disasters? See the December 10 earthquake that shut down two Micron fabs in Taiwan or the February storm that shut down a Samsung fab in Texas. Infrastructure shutdowns? See the ongoing water rationing in Taiwan caused by record droughts.
Those examples alone have already resulted in supply issues for flash memory, in Micron's case, as well as SSD controllers in Samsung's. The droughts in Taiwan have threatened production related to CPUs, GPUs, single-board computers, and display panels, among other things, despite manufacturers' efforts to mitigate their effects.
There are significant barriers to reducing that risk, SIA and BGC said, one of the most important being the fact that those companies have very complicated specialties. They explained in the report:
Get Tom's Hardware's best news and in-depth reviews, straight to your inbox.
"Specialization across the supply chain allows the deep focus required to innovate, often pushing the boundaries of science. There are more than 30 types of semiconductor product categories, each optimized for a particular function in an electronic subsystem. Developing a modern chip requires deep technical expertise in both hardware and software, and relies on advanced design tools and intellectual property (IP) provided by specialized firms. Fabrication then typically requires as many as 300 different inputs, including raw wafers, commodity chemicals, specialty chemicals, and bulk gases. These inputs are processed by more than 50 classes of highly engineered precision equipment. Most of this equipment, such as lithography and metrology tools, incorporates hundreds of technology subsystems such as modules, lasers, mechatronics, control chips, and optics. The highly specialized suppliers involved in semiconductor design and fabrication are often based in different countries. Chips then zigzag across the world in a global journey."
The Argument Against Self-Sufficiency
The chip shortage has prompted governments around the world to question their reliance on this global network. The European Commission said in December that it planned to invest $170 billion (145B€) to increase its production, for example, and U.S. President Joe Biden ordered a review of critical supply chains in February.
China has also pushed its chip industry towards independence and enjoyed a series of wins despite U.S. restrictions on chip-making equipment meant to impede its progress. In recent months it's announced its first DDR4 memory, first domestic SSDs, and first 7nm data center GPU; it's also made progress on a chip fabbing tool.
Yet true self-sufficiency is nearly unattainable, per SIA and BGC, at least to governments that aren't willing to spend a lot more than they are now. Just check out the estimate SIA and BGC shared in the exhibit below:
That's a global upfront investment of somewhere between $900 billion and $1.2 trillion accompanied by an incremental annual cost between $45 and $125 billion. SIA and BGC said the annual cost alone "would all but wipe out the profits of the industry, which amounted to $126 billion across the entire value chain in 2019."
SIA and BGC said this could lead to "an average increase of 35-65% in the price of semiconductors" if the manufacturers' higher costs are fully passed on to their customers. That would almost certainly lead to higher costs for consumers, too, so you still wouldn't be able to buy the best CPUs or best graphics cards on the cheap.
But the real cost would be even higher. "Furthermore, it is also likely that siloed domestic industries shielded from foreign competition and deprived of global scale would lose in efficiency and ability to innovate," SIA and BGC said. "Ultimately, it would reverse the decades-long trend of making increasingly powerful and more affordable electronic devices access fo consumers around the world."
And that's assuming various governments simply wanted to meet the demand for chips in 2019. SIA and BGC estimated that "the industry will have to almost double its capacity by 2030 to keep up with the expected 4% to 5% average annual growth in semiconductor demand." That would make self-sufficient supplies even more costly.
A Proposed Solution
SIA and BGC proposed an alternative solution to fully self-sufficient supplies for major regions: targeted investments. They called for the U.S. to implement a $20 to $50 billion program, for example, that would support domestic production of semiconductors used in devices critical to national security and other vital areas.
They also said that "governments with significant national security concerns related to control over semiconductor technology should establish a stable framework for restrictions on semiconductor trade" that clearly defines policy goals, restrictions, and "the expected second-order impacts on industry players" that could result.
Their final plea was for policy makers to "significantly step up the efforts to address the looming shortage of high-skill talent that threatens to constrain the semiconductor industry's ability to keep the current pace of innovation and growth." It turns out that we haven't yet developed an autonomous chip industry — and probably never will — which means the human factor can't simply be ignored.
Will any of those solutions help in the short term? Not really. Increasing production capacity is an incredibly expensive process that also takes time to complete. TSMC didn't make a plan to spend $100 billion over the next three years for no reason; if it could reduce either the financial investment or the length of time it needs, it would.
But at least now it's clearer than ever why this chip shortage is happening, why it's not going to be solved over night, and how industry players think it can be addressed in the near future.
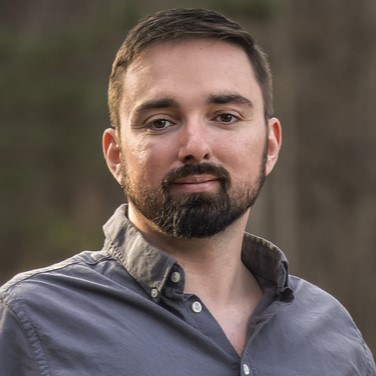
Nathaniel Mott is a freelance news and features writer for Tom's Hardware US, covering breaking news, security, and the silliest aspects of the tech industry.
-
Giroro You know these semiconductor companies really love to complain how expensive it is to build a fab when begging for taxpayer dollars, but I don't think I've ever seen one publicly justify why these prices are so incomprehensibly high. I really mean incomprehensibly. The human brain is not capable of understanding of the massive amount of labor and resources that a billion or ten or a thousand billion dollars truly represents.Reply
Where are they getting their manufacturing equipment? Is it sourced from a monopoly? Is every single nut and bolt used on their lines painstakingly handcrafted with a thousand hours of artisan labor? What makes fab equipment so special? I know they've said a hundred times that we must take their word on it being hard and expensive, but why is it so hard and expensive. What are the expensive parts, why are they so expensive, and what can a govenment do to get the costs down to a realistic level?
What prevents new companies from getting into the business of "selling a single assembly line to the silicon cartels, built from equipment valued at more than the entire lifetime output of 10,000 engineers".
Is the answer to all this is just a mountain of IP/patents/copyrights/licensing? Not every part of the world cares about such things. -
Co BIY Giroro said:You know these semiconductor companies really love to complain how expensive it is to build a fab when begging for taxpayer dollars, but I don't think I've ever seen one publicly justify why these prices are so incomprehensibly high. I really mean incomprehensibly. The human brain is not capable of understanding of the massive amount of labor and resources that a billion or ten or a thousand billion dollars truly represents.
Where are they getting their manufacturing equipment? Is it sourced from a monopoly? Is every single nut and bolt used on their lines painstakingly handcrafted with a thousand hours of artisan labor? What makes fab equipment so special? I know they've said a hundred times that we must take their word on it being hard and expensive, but why is it so hard and expensive. What are the expensive parts, why are they so expensive, and what can a government do to get the costs down to a realistic level?
What prevents new companies from getting into the business of "selling a single assembly line to the silicon cartels, built from equipment valued at more than the entire lifetime output of 10,000 engineers".
Is the answer to all this is just a mountain of IP/patents/copyrights/licensing? Not every part of the world cares about such things.
Well the equipment has to be built in part from parts built in the fabs that are in short supply!
Read just a bit about EUV lithography machines and you can see how the cash burns easy.
https://www.asml.com/en/products/duv-lithography-systems
I have never heard the companies tell us we have to take their word on the expense. I do hear them put out these big numbers especially when presented with over simplistic critics.