Samsung’s Answer to Gorilla Glass Is 'Unbreakable’
Earlier this month, Corning announced Gorilla Glass 6, a new iteration of the glass it makes for smartphone makers and other tech companies. Gorilla Glass 6's claim to fame is that it can survive 15 drops onto hard surfaces from 1 meter or higher without breaking. Now, Samsung is doing one better: it's revealed a new display panel that has been certified as unbreakable by the Underwriters Laboratories testing company.
Instead of using the glass found in most smartphone displays, Samsung "developed the flexible OLED panel with an unbreakable substrate and an overlay window securely adhered to it." Samsung Display's general manager of the communication team, Hojung Kim, said this fortified plastic window is similar to glass in terms of weight, transmissivity and hardness, so it should be able to replace glass without too much hassle.
Underwriters Laboratories helps develop standards for pretty much any industry you can imagine, and it also tests new products to make sure they meet those standards. Samsung noted in its announcement that Underwriters Laboratories is the official testing company for the Occupational Safety and Health Administration.
The South Korean firm described the methodology it and Underwriters Laboratories used to determine the new panel's endurance:
"After a drop test administered at 1.2 meters (nearly 4 feet) above the ground 26 times in succession and accompanying high (71 degrees) and low (-32 degrees) temperature tests, the Samsung unbreakable panel continued to function normally with no damage to its front, sides or edges."
The panel "operated normally with no sign of damage" after a 1.8 meter drop test, too, though we don't know how many times it was dropped from that height. According to Samsung, that means this unbreakable panel is more durable than even the U.S. Department of Defense requires. We suspect that means it should be able to survive everyday use--and potentially the many at-home drop tests people will inevitably perform.
Samsung made this panel for smartphones, but the company said it might also find use for it in other devices, from tablets and portable game consoles, to military devices and vehicle display consoles. Meanwhile, Corning wants to put Gorilla Glass in seemingly every product--and many companies are happy to oblige because glass is in vogue. But this new unbreakable panel shows that Samsung isn't monkeying around.
Get Tom's Hardware's best news and in-depth reviews, straight to your inbox.
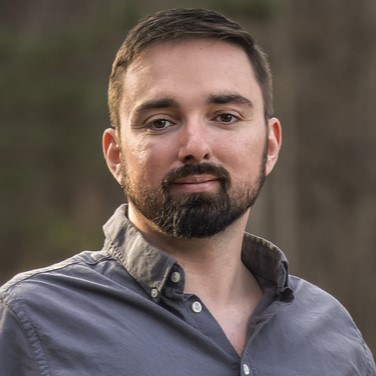
Nathaniel Mott is a freelance news and features writer for Tom's Hardware US, covering breaking news, security, and the silliest aspects of the tech industry.
-
ingtar33 the main reason why glass was used instead of plastic is because plastic breaks down from sunlight and high temps, causing it to turn milky and lose it's opaqueness (as well as losing integrity). If Samsung figured out how to stop that from happening and the quality of the screen display isn't strongly affected by scratches then this is indeed quite a breakthrough.Reply
I'll maintain a healthy skepticism though. -
The Paladin After a drop test administered at 1.2 meters (nearly 4 feet) above the ground 26 times in succession and accompanying high (71 degrees) and low (-32 degrees) temperature tests, the Samsung unbreakable panel continued to function normally with no damage to its front, sides or edges."
I want to get one, stick It on the dash of my car, and leave it in my car while I work for a month, and see how it handles the car heat of Texas and if it has not changed colour, as you notice above, nothing mentioned about discoloration. -
stdragon Corning knows, (as well as other material scientists) that there's a trade-off between 'hardness' (Mohs' scale) and 'toughness'. So what is seems to me that Samsung has fantastic toughness, but could also scratch more easily.Reply
Now, one might argue that having a combo of really tough screens combined with a disposable screen protector might be the best match. But again, short of lamination, you can't have both maximum hardness and toughness. The closest to that is Diamond; and I'm not sure we're going to see CVD (chemical vapor deposition) of synthetic diamond mass-produced anytime soon. If so, we'd already have Apple's sapphire glass they'd sunk so much money into already. -
stdragon 21177689 said:But will it blend?
https://www.youtube.com/channel/UCnFP0IU4gpnmcLnVzDLUtfw
will is shred?
https://www.youtube.com/watch?v=kSHV3kxV5bc -
Lutfij This is all that came to mind after seeing this article:Reply
https://www.facebook.com/permalink.php?story_fbid=183057402563834&id=100025787251548
:D -
Solandri
Well if we're going to get that nitpicky, diamond is a crystalline structure, and vulnerable to fast fracture mechanics. A crack ends up concentrating stresses at the endpoint of the crack, causing the crack to to grow by "unzipping". That's why you can cut diamonds by hitting them with a chisel at certain angles.21177590 said:But again, short of lamination, you can't have both maximum hardness and toughness. The closest to that is Diamond; and I'm not sure we're going to see CVD (chemical vapor deposition) of synthetic diamond mass-produced anytime soon.
Glass as we all know is also extremely vulnerable to fast fracture. Plastics are too (why it's easy to tear shrink wrap once you've cut a small notch in it), but less so than glass. Metals (whose grains slide, then interlock) tend to resist it well. As do fiber-reinforced composites like fiberglass and pykrete (combination of ice and sawdust). The substrate (resin or ice) experiences fast fracture, but the fracture eventually hits the reinforcing material (glass fibers or sawdust), which halts the "unzipping" process.
If so, we'd already have Apple's sapphire glass they'd sunk so much money into already.
It's not Apple's. It's corundum (aluminum oxide) crystals grown to sufficient size and thickness to be used as glass. Researchers figured out how to grow artificial corundum crystals (adding slight impurities turns them red or blue - which we call rubies and sapphires) back in the 1990s. The company making the corundum glass commercially had been producing them as bullet-resistant windshields for the U.S. military before Apple pulled their bait and switch on them. The technology existed and was developed long before Apple ever got involved. Heck, the aluminum foil in your kitchen drawer has a natural layer of corundum on it stopping it from oxidizing further. -
stdragon 21178074 said:The company making the corundum glass commercially had been producing them as bullet-resistant windshields for the U.S. military before Apple pulled their bait and switch on them. The technology existed and was developed long before Apple ever got involved.
That I wasn't aware of. I thought Apple invested in the technology that could mass-produce corundum in sufficient quantities cost effectively. If I recall, it was originally intended to first be used for the Apple Watch, but it will shatter on impact (as indicated on corner impact tests). However, with a hardness of 9, it would withstand abrasions such as from sand and other debris. Apparently something happened (of which I know nothing about), but I do believe corundum production was limited to just the Apple iPhone camera lenses.