TSMC's second Japanese fab reportedly delayed, mass production pushed to 2029
But the company's American projects have nothing to do with it.
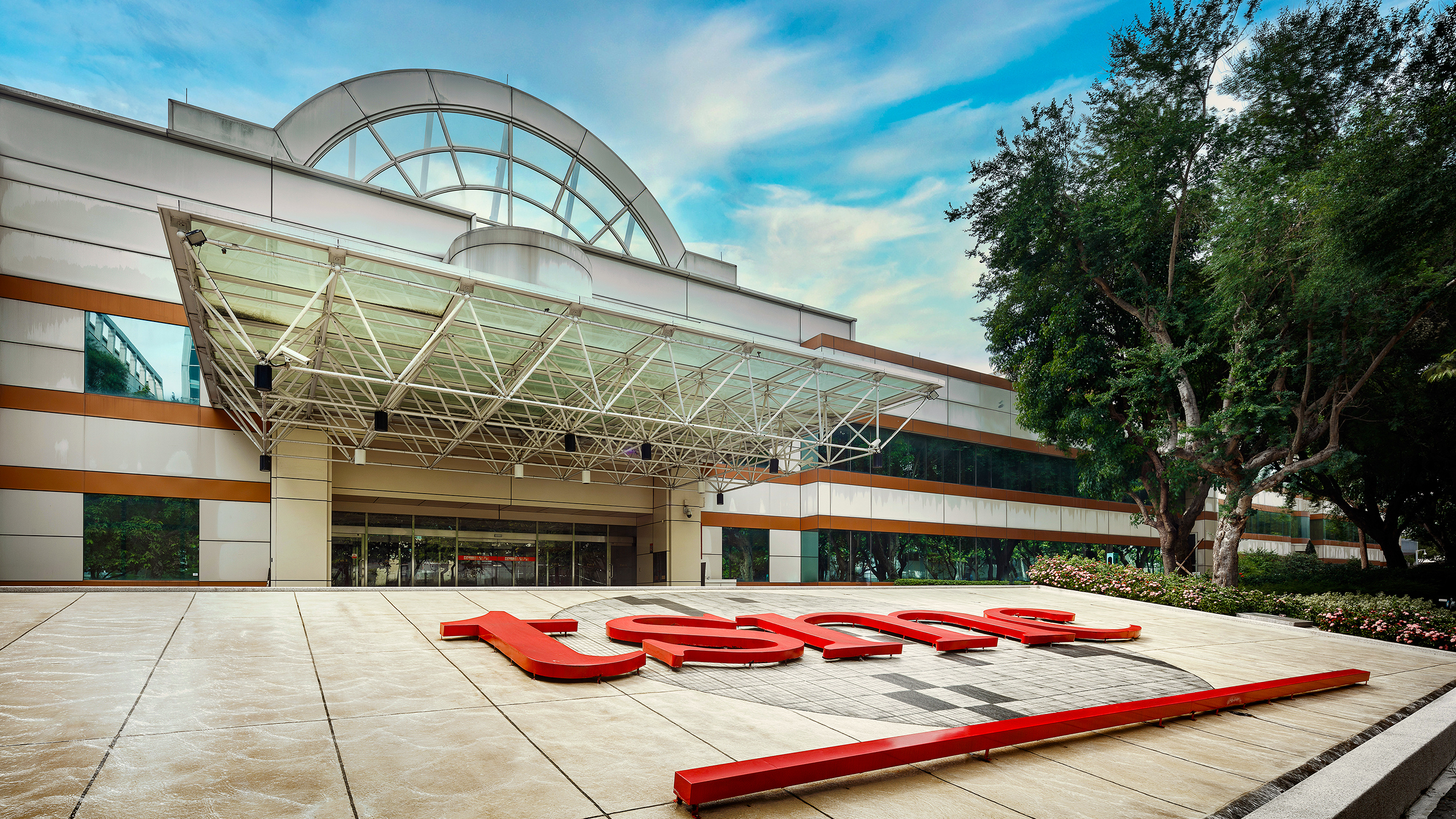
TSMC may have to delay the construction of its Fab 23 phase 2 (JASM phase 2) near Kumamoto, Japan, by up to 18 months. The delay would push the start of mass production to 2029, according to a report by Nikkan (via @DanNystedt).
TSMC began mass production at its first Japanese fab, Fab 23 phase 1, in late December 2024. Construction of Fab 23 phase 2 was supposed to start earlier this year, but was delayed due to inadequate local infrastructure, with the Wall Street Journal reporting traffic congestion as a contributing factor. Typically, it takes about 18 to 24 months from pouring the foundation to the first test wafers running around the fab. Hence, if JASM phase 2 experiences a 1.5-year delay (i.e., in mid- or late-2026), then it is entirely possible that the first commercial products will be manufactured at the fab in 2028–2029.
"The construction of our second specialty fab is scheduled to start later this year, subject to the readiness of the local infrastructure," said C.C. Wei, chief executive officer of TSMC, in a conference call with analysts and investors last week. "The ramp schedule will be based on our customers' need and market conditions."
A Japanese government official noted in an interview with the WSJ that they had not been directly informed by TSMC about traffic being the cause and questioned that explanation. Still, the government expected the fab's production schedule and capacity targets to largely stay on track.
Traffic congestion can indeed delay massive construction projects, such as semiconductor production facilities. Fabs require transportation of thousands of tons of materials, including steel, concrete, piping, and eventually cleanroom components. Fab construction and tool installation operate on tight, coordinated schedules. Delays in any delivery can cause cascading effects across multiple contractors and installation phases, which not only affect production but also increase costs if equipment or workers spend hours stuck in traffic.
TSMC's Fab 23 phase 2 is expected to be N7/N6-capable and will therefore install Low-NA EUV tools. These are massive pieces of equipment that may require special logistics, which can be challenging to organize in congested areas, potentially pushing back installation timelines. Additionally, congestion increases the risk of accidents during the transportation of delicate equipment, which in turn drives up costs.
Finally, fabs are 24/7/365 facilities that consume high-purity chemicals that must be delivered safely (to avoid opposition from locals) and on time (to avoid extremely costly production disruptions). To that end, poor infrastructure may affect TSMC's decision to postpone the construction start, allowing local authorities to build the new infrastructure. However, building infrastructure in congested areas takes a long time, which is why reports about a 1.5-year delay emerge.
Get Tom's Hardware's best news and in-depth reviews, straight to your inbox.
Follow Tom's Hardware on Google News to get our up-to-date news, analysis, and reviews in your feeds. Make sure to click the Follow button.
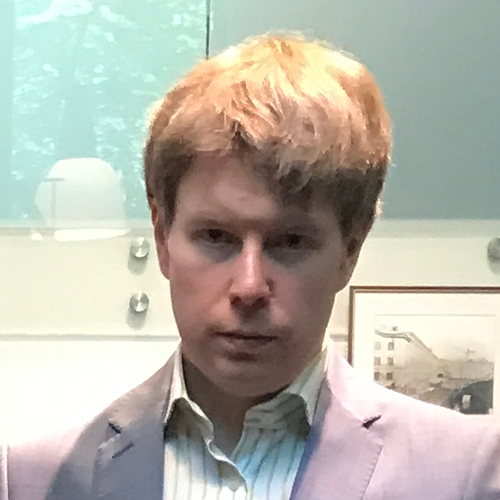
Anton Shilov is a contributing writer at Tom’s Hardware. Over the past couple of decades, he has covered everything from CPUs and GPUs to supercomputers and from modern process technologies and latest fab tools to high-tech industry trends.