Researchers 3D print wood objects from sawdust ink – texture, appearance, and smell similar to the real thing
A great new use-case for wood waste.
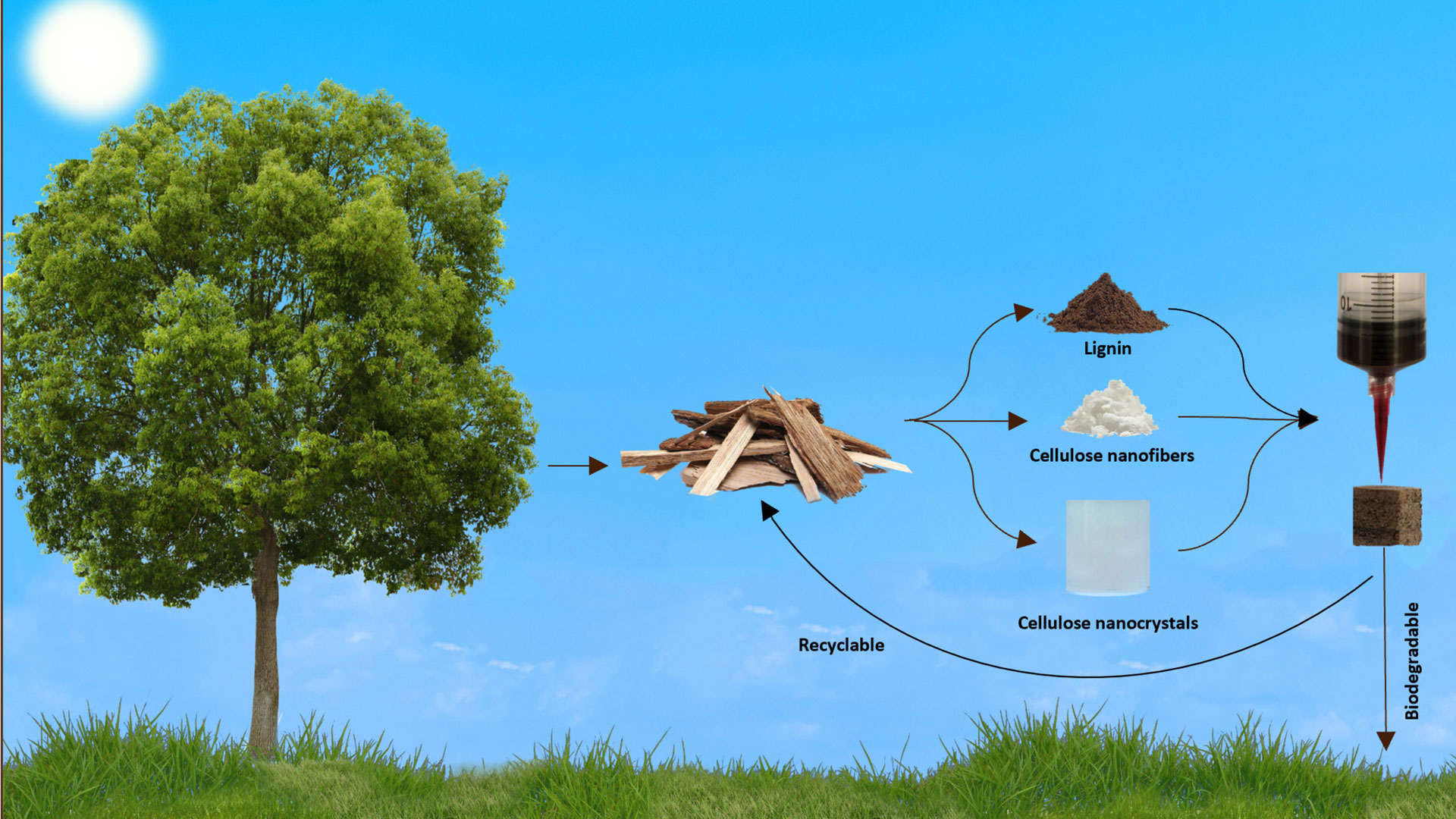
Researchers from Rice University and Oak Ridge National Laboratory have developed a new 3D printing technology that recycles wood waste material. According to the paper Three-dimensional printing of wood in Science Advances, the new methodology results in 3D printed objects with the texture, appearance, thermal stability, and smell of natural wood. Also, in contrast with some other 'wood' 3D printing filaments available today, the new material is simply a water-based ink made of lignin and cellulose, the primary building blocks of natural wood – no plastics here.
The researchers were inspired to develop their wood ink after pondering over the inefficiency of traditional carpentry. They still, however, were attracted to some of the defining qualities of wood – specifically its visual, textural, olfactory, and mechanical properties. They wanted to mix the latest manufacturing technology of 3D printing, or additive manufacturing, without losing the attractive qualities of wood in the process.
Entirely wood-based
Current wood filaments for 3D printers aren't up to scratch in this regard, being around 70% PLA. Pleasingly, the new 3D printing wood ink uses "entirely wood-based constituents and is devoid of any binder or foreign polymeric phase." No chemicals such as acetone are used in the waste wood processing either. Last but not least, using sawdust and wood scraps to make this wood ink uses the substantial waste created by traditional wood manufacturing processes.
To get an optimal wood ink that would work well using a 25-gauge nozzle under reasonable syringe pressure at ambient conditions, the researchers came up with the following mix: 25% by weight lignin (same as natural wood), a 37.5% by weight mix of cellulose nanofibers (CNFs) and cellulose nanocrystals (CNCs), and water. Apparently, the material handles a lot like clay and is just right for direct ink writing (DIW) style 3D printing.
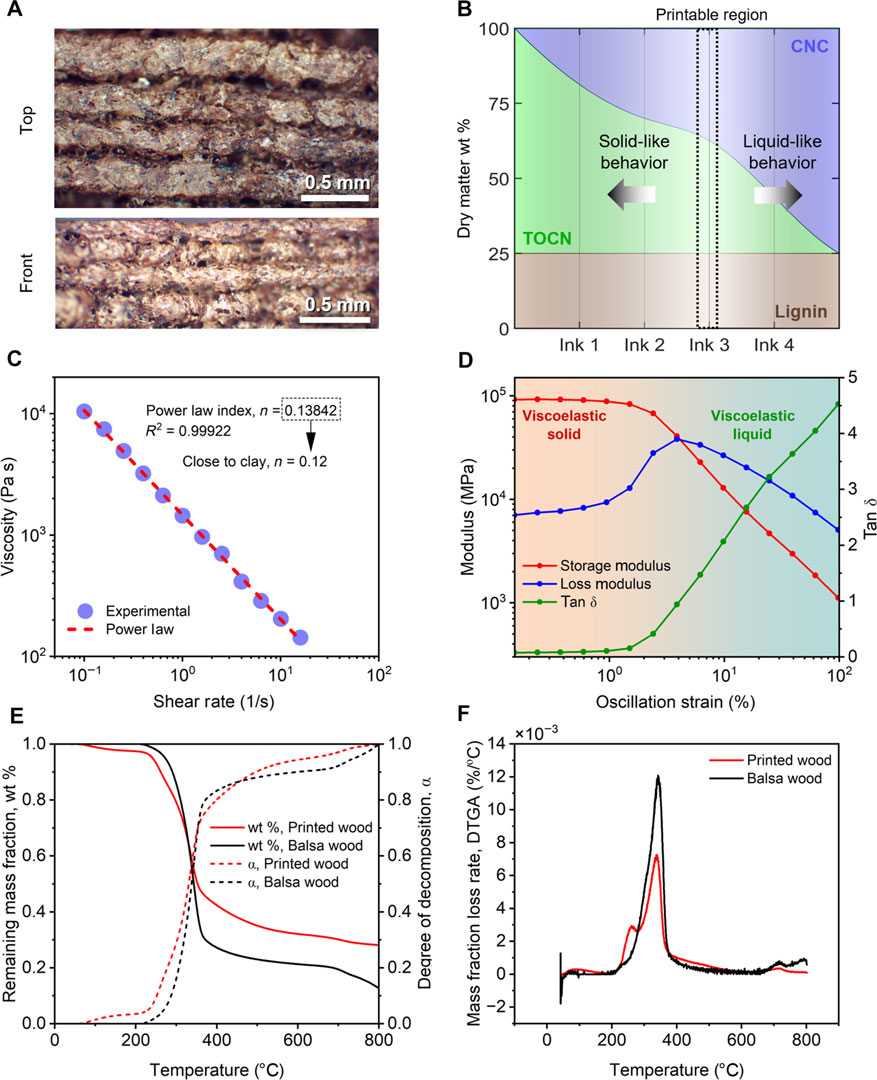
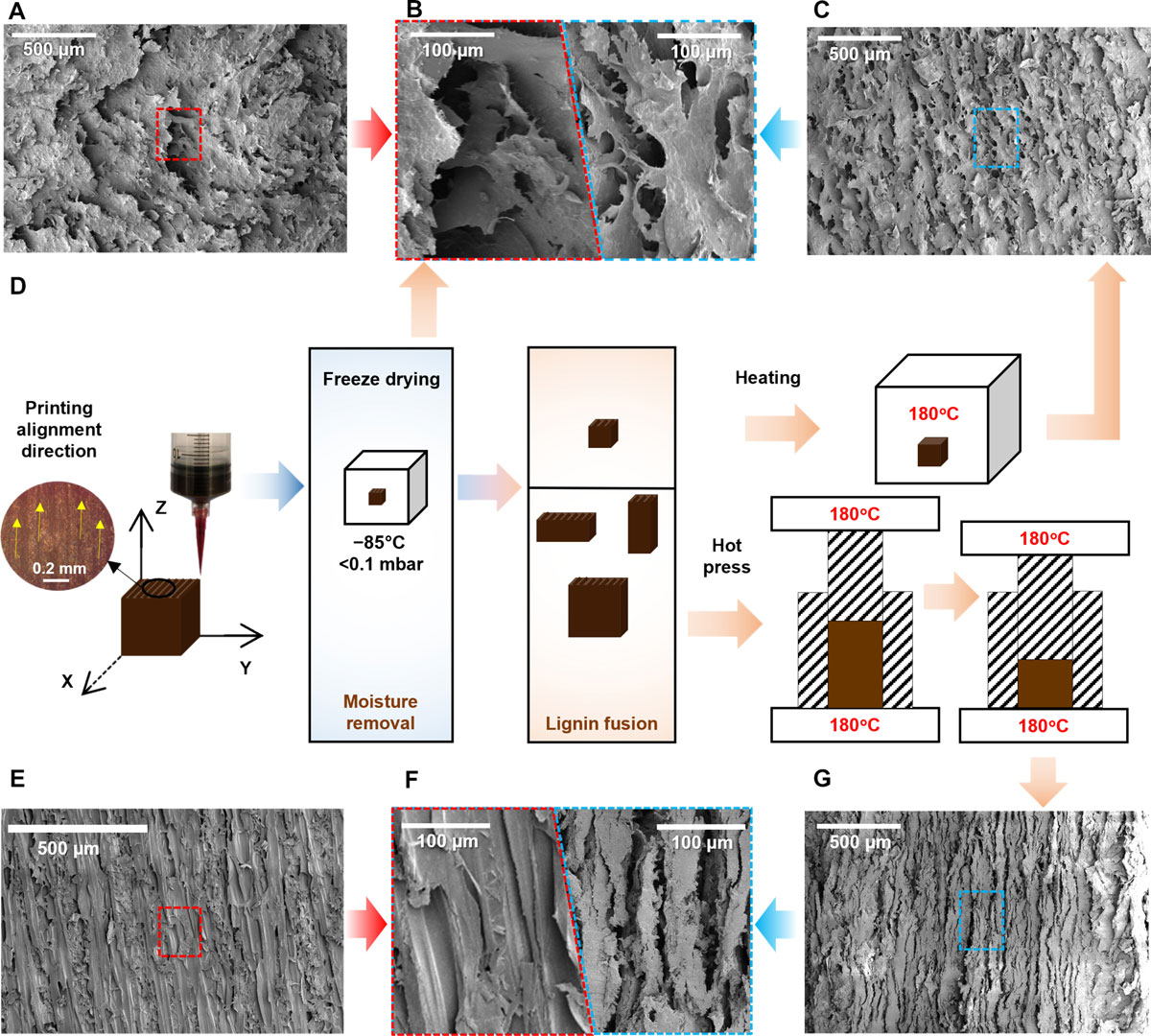
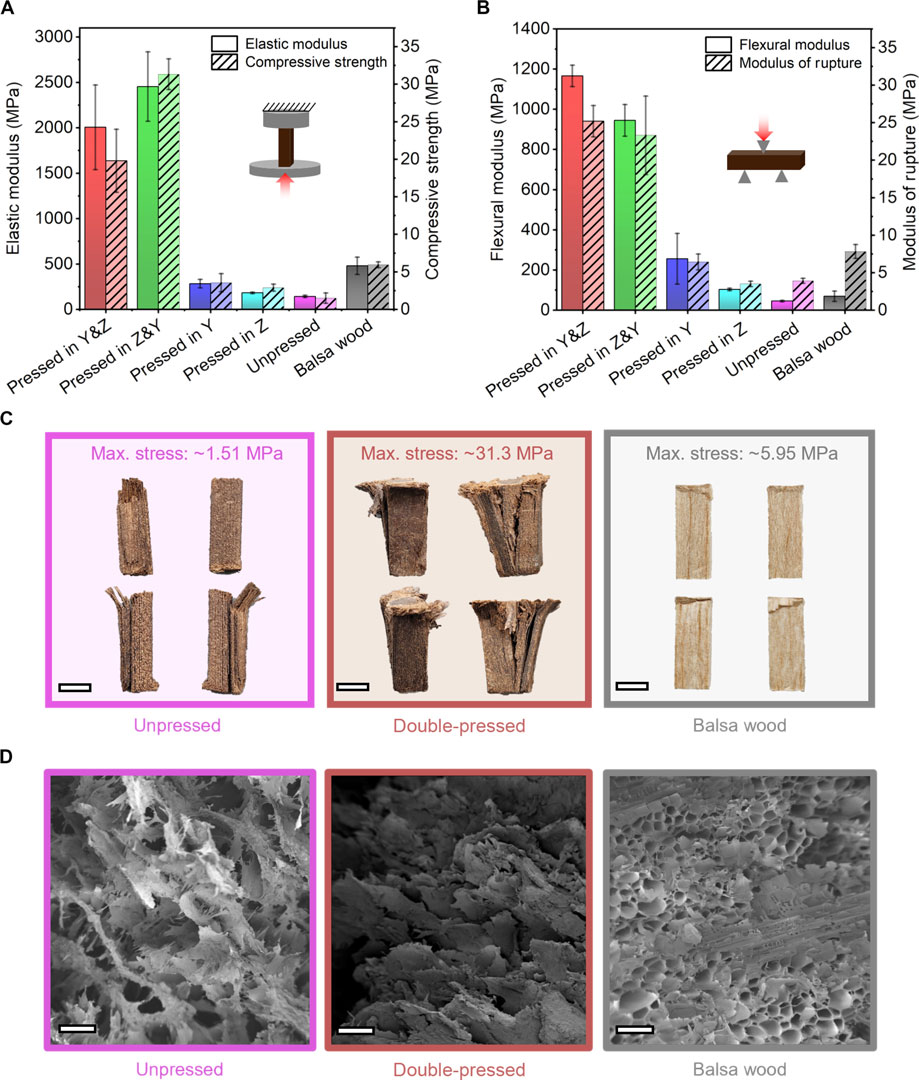
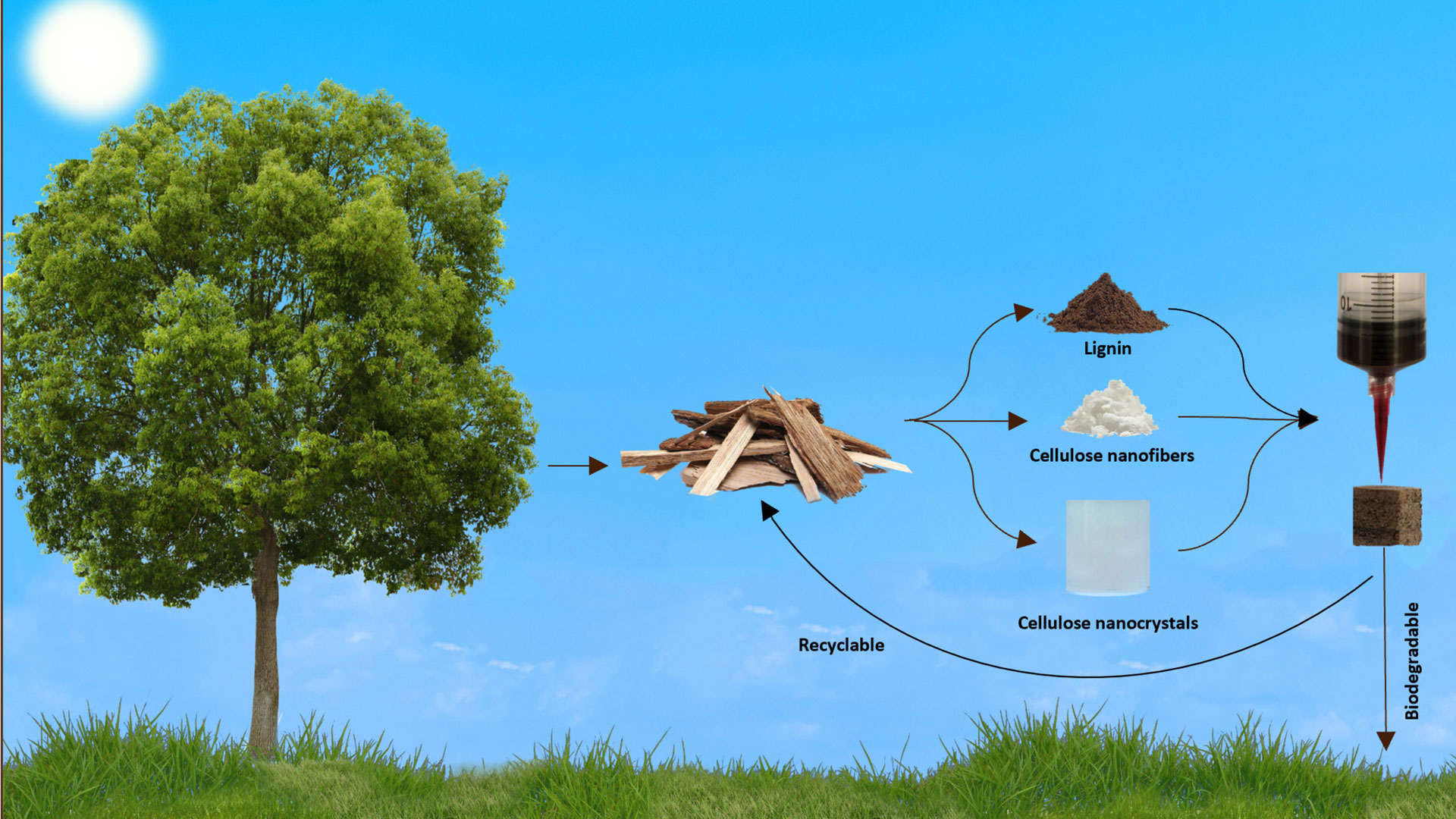
Freeze and bake
The process of making the wood ink material and printing it may seem straightforward, and even logical, for those familiar with 3D printing. However, squirting the wood ink clay into a 3D shape is far from the end of the process. The researchers have outlined some specific freezing and heating steps required to deliver an optimal finished product.
First, the freezing step: printed samples were put under dry ice for 30 minutes, then freeze-dried at -85 degrees Celsius at 0.1-mbar pressure, for 48 hours. Heat treatment followed immediately after taking the samples out of the freeze, and placing them into a 180 degrees Celsius oven for 20 minutes. When objects required hot pressing, this step was added to the oven baking process – pressing the item for 10 minutes in the heat.
Sadly, after all the sustainable steps in making the wood ink, using natural materials, and no additives – the freezing and heating steps are notable for being rather energy-intensive. This part of the production process makes it all the more important to complete a thorough techno-economic and environmental analysis, before using this 'wood ink' for big projects.
Get Tom's Hardware's best news and in-depth reviews, straight to your inbox.
MORE: Best 3D Printers
MORE: Best Budget 3D Printers
MORE: Best Resin 3D Printers
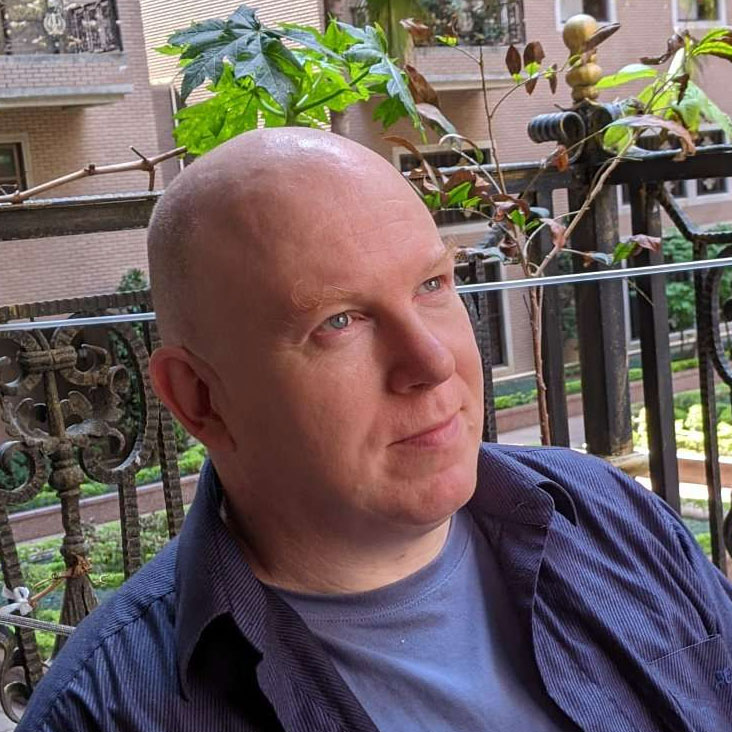
Mark Tyson is a news editor at Tom's Hardware. He enjoys covering the full breadth of PC tech; from business and semiconductor design to products approaching the edge of reason.
-
FoxtrotMichael-1 This probably has some pretty neat implications for manufactured wood products and the industries that apply them (think IKEA furniture). However, for those who love working with wood, nothing will ever replace actual wood. It’s just nice to know that sawdust and wood waste can be made into a useful material.Reply -
OneMoreUser
For sure it will not be like working with real wood, so I totally agree with you about working the stuff.FoxtrotMichael-1 said:This probably has some pretty neat implications for manufactured wood products and the industries that apply them (think IKEA furniture). However, for those who love working with wood, nothing will ever replace actual wood. It’s just nice to know that sawdust and wood waste can be made into a useful material.
Only I also think the use will be limited to decorative bits, as I notice the article has no mentioning of the strength of the printed "wood". That has me thinking what is printed is likely more like some fiber product, ie. not really something you build stuff from unless you have a structure to support it. -
gg83
Absolutely! I wonder if the strength will be similar to grown wood. With the grain and whatnot. And with no polymer binders!!!! It's a great concept.FoxtrotMichael-1 said:This probably has some pretty neat implications for manufactured wood products and the industries that apply them (think IKEA furniture). However, for those who love working with wood, nothing will ever replace actual wood. It’s just nice to know that sawdust and wood waste can be made into a useful material. -
georgebaker437 Sounds like a very complex way of making cardboard to me! At best, it is just particle board with a lignin based glue.Reply -
Eximo This won't get adopted by companies like IKEA, it doesn't scale well. Minimizing manufacturing time is how they make cheap things, not slowing down to 3D print parts.Reply
I can see this replacing complex wood carving in the hobbyist space, or making things out of a wood like material that are impossible through normal wood working techniques. -
slightnitpick Apparently, the material handles a lot like clay and is just right for direct ink writing (DIW) style 3D printing.
Now I need to know whether this is something potters and sculptors will shape by hand.