3D Printer Uses Magnets To Break Speed Limits, Print at a Table-Shaking 800 mm/s
Magneto X “levitates” the tool head on magnetic linear motors

Resin printer company Peopoly created quite a buzz with the unveiling of a prototype beltless FDM 3D printer, the Magneto X, at the East Coast RepRap Festival. The new printer is a desk top machine with a huge 400 x 300 x 300 mm build volume and print speeds up to 800mm/s. It borrows a design feature seen on CNC machines: magnetic linear motors. Normally, 3D printers move their components with rotating stepper motors attached to gears and pulleys. The linear motor can be thought of as a flat, unrolled motor with the “rotor” attached to the moving component – the tool head – and the stator forming a track along one axis.
Dubbed the “MagXY” system, the tool head seems to levitate across the gantry without obvious means. It has a top print speed of 800 mm/s with a max acceleration of 22,000 mm/s², which would make it faster than modern Core XY printers from Bambu Lab.
Peng said the Magneto X was conceived during a lockdown in 2022 when his company’s lab in Shenzhen, China was shut down for 21 days. No one was able to go home, so to pass the time they started watching YouTube, particularly videos about Voron 3D printer builds. Since they could still order delivery through local AliExpress, they decided to order parts and build a few FDM printers for fun. Peng said this naturally lead to seeing how they could improve the machines and thus the Magneto X was born.
Peopoly is using and supporting both Klipper firmware and OrcaSlicer, which founder Mark Peng said greatly helped speed up their development time.
Demonstrations at ERRF were sadly limited, as the printer’s hotend had been damaged in shipping. Peng was only able to run the machine dry, so we were unable to judge its print quality firsthand. Tom’s Hardware is on the list for a review unit and will put the machine through it’s paces later this year when it becomes available.
Peopoly is known for high end, large scale, liquid resin 3D printers and the Magneto X will be it’s first plastic pushing printer. The printer will likewise be a premium machine with a price tag starting at $1999, currently on sale for $1399 during the pre-order phase. The optional enclosure will cost $79 more. Printers are expected to begin shipping in late November.
Peopoly said that the simplified design of the MagXY linear motor system has less friction and less need for calibration. The system will be able to monitor and adjust the motor's position for high quality prints.
Get Tom's Hardware's best news and in-depth reviews, straight to your inbox.
All this speed is backed by a custom extrusion system with 90 Newtons of force, a pull speed of 30 mm/s, and an optimized melt zone with a peak flow rate of 60 mm^3/s. For comparison, the Bambu Lab X1 Carbon has a max flow rate of 32mm^3/s.
Peopoly is leaning hard into the Open Source community. Not only have they become backers of Klipper firmware, they are also using – and supporting – Open Source OcraSlicer. The Magneto X’s nozzles are compatible with the popular E3D’s V6 volcano which suggests the machine will be open to modification by users. Peopoly also states its machine can be used without joining a cloud-based system and promises customer data will not be collected.
The 3D printer will have a load cell sensor for precise auto leveling and four independent Z-axis stepper motors for dynamic adjustments. The hotend is rated to 300 degrees Celsius, and with an available enclosure will be able to print engineering grade materials. Prints will be monitored with an included camera which can also take time lapses.
MORE: Best 3D Printers
MORE: Best Budget 3D Printers
MORE: Best Resin 3D Printers
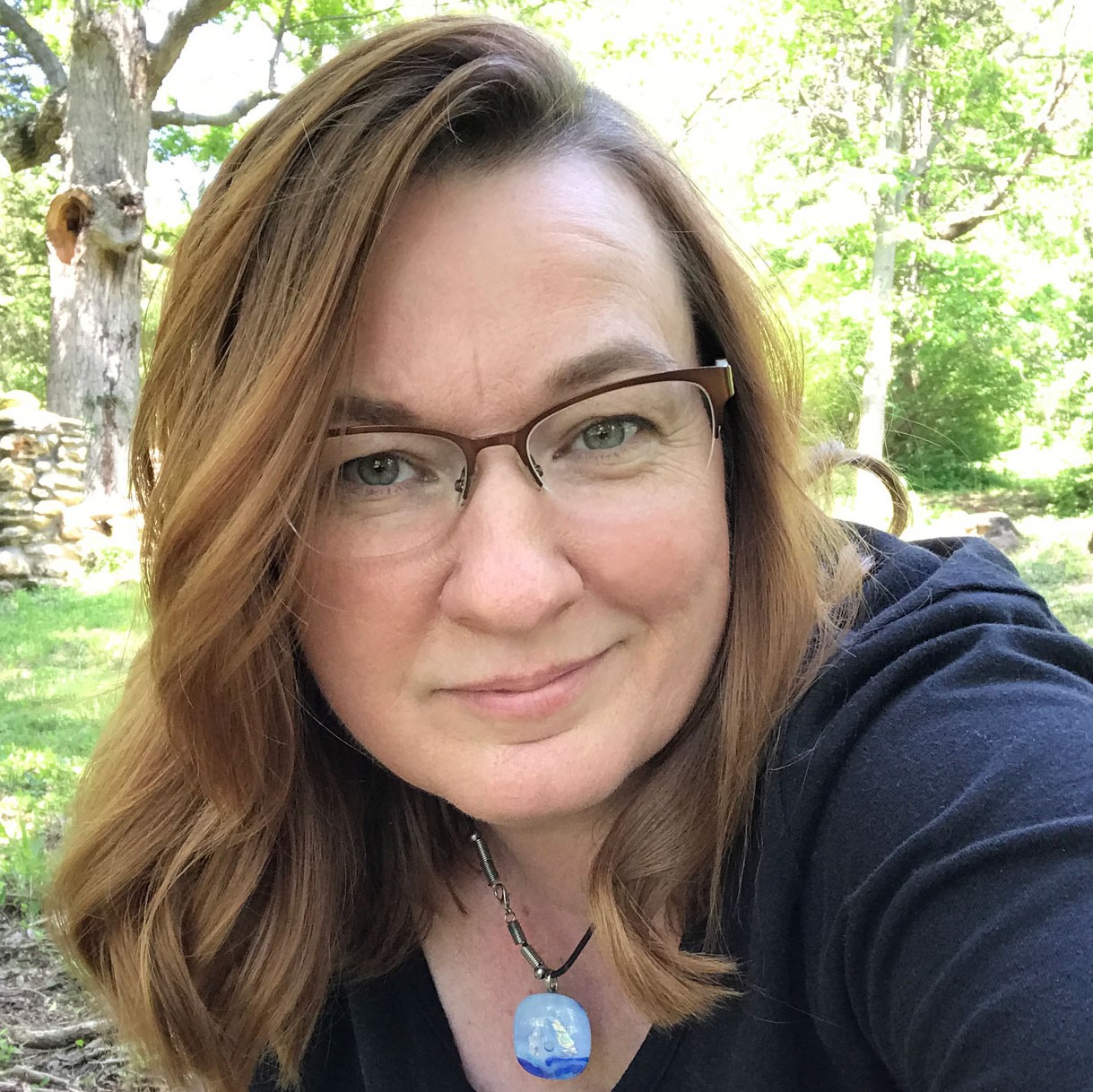
Denise Bertacchi is a Contributing Writer for Tom’s Hardware US, covering 3D printing. Denise has been crafting with PCs since she discovered Print Shop had clip art on her Apple IIe. She loves reviewing 3D printers because she can mix all her passions: printing, photography, and writing.
-
Kamen Rider Blade This could be the next big thing for Filament Printers.Reply
I'm sure every 3D printer company will copy the idea of using MagLev motors to boost speed along with faster nozzles. -
peachpuff
Creality is on the case, introducing the M1...Kamen Rider Blade said:This could be the next big thing for Filament Printers.
I'm sure every 3D printer company will copy the idea of using MagLev motors to boost speed along with faster nozzles. -
peachpuff
Doesn't matterthisisaname said:Table shaking and 3d printer are two things that do not go well together.
D-eLhKdKAdkView: https://youtu.be/D-eLhKdKAdk?si=CJ-SjoXF_dofmWvk -
virtual_axolotl This is not as innovative as it might seem. Stratasys has already done this. As a matter of fact they did this and then switched back to servo motors because the increased costs of magnetic drives did not have a justified increase in performance.Reply
We can almost certainly make faster linear systems then CoreXY. Doing it while maintaining desirable print qualities is another thing. The greatest limitations here are not with mechanical systems, they are with the material itself. -
jp7189
I don't disagree with you, but I recall working with ABS 10 years ago and it was "common" knowledge that it could be printed only so fast before quality suffered. Today my printer slings ABS way faster than I ever dreamed back then and with better quality too.virtual_axolotl said:
We can almost certainly make faster linear systems then CoreXY. Doing it while maintaining desirable print qualities is another thing. The greatest limitations here are not with mechanical systems, they are with the material itself.
You could argue that motion compensation is more about electronics, sensors, and processing power than mere motors and rails, but I would still put all that under the "mechanical" umbrella.