Measurement Science: Taking Accurate IR Thermal Readings
If you thought that buying and unpacking an expensive infrared camera was all that it took to perform professional-level measurements, then it's time for a little lesson. We’ll share some of the knowledge that goes into generating accurate results.
Doing It Right
Nothing Beats Resolution
The resolution of many of conventional infrared cameras is actually quite low. Since the surfaces we want to measure are often large, and may include many tiny elements like pins, it's easy to see how this is a problem. Measurements with IR cameras simply can't be all that precise, even if they look like they are. So let's start by taking a look at a graphics card front and back at different resolutions.
Unfortunately, it's just not possible to get close enough to the board's surface to capture all of the details. The camera's optical components set a clear limit, which is in turn dictated by physics. We're using distances between 20 and 150cm, depending on the measured object, detail level and lens.
Even cameras with a resolution of 320p can produce reasonably useful measurements, as long as the optics and distances are set correctly. The rectangle below shows the measurement area for which a camera like this can provide a usable average.
Significantly lower resolutions are problematic, though. If the entire graphics card is supposed to be covered, then areas with substantially cooler temperatures like pins and soldering eyelets, which have lower emissivity, skew the average temperature downward.
Comparing a handheld camera with its stamp-sized picture and a high-resolution camera yields a difference of up to 10 degrees Celsius over the VRM in spite of the provided emissivity setting. Even many of the better infrared thermometers aren't useful for our type of measurements due to their resolution, which is to say due to the size of the measurement diameter. Only the average temperature is captured by these devices, and details are unfortunately lost.
Before getting into the problems caused by the emissivities of different surfaces and how we deal with them, let's focus on more general mistakes that lead to imprecise or even completely unusable results.
Mirror, Mirror
There's no doubt that handheld infrared cameras are convenient. They are both portable and easy to use. Unfortunately, your body can almost always be found behind them. Many surfaces "mirror" heat, which is to say that they reflect it back. As a result, you end up measuring your own body heat.
Get Tom's Hardware's best news and in-depth reviews, straight to your inbox.
Some surfaces, especially metals, reflect heat very well, even after being covered with lacquer. The thinner the lacquer cover, the higher the transmittance, and it can easily become high enough to cause these types of errors.
Ambient Temperature
It's not just the camera that needs to be calibrated on a regular basis. The environment needs to be kept consistent as well. We're always keeping the temperature of our room at 22 degrees Celsius during benchmark runs, yielding the most comparable results possible. Naturally, we need to cool or heat the room constantly depending on the benchmark and outside temperature.
Apart from measuring the system's temperature before turning it on and starting our first benchmark, we also use a second reference in the form of a lacquered copper box that's positioned close to the test system.
The Right Angle
It's tempting to just point the camera at the right spot in a way that doesn't necessitate unscrewing a bunch of things. However, this generally gets you measurement results that are too low. So, you have to do it correctly or not bother at all. The following example shows measurements from two different angles: perpendicular at 90 degrees and acute at 30 degrees.
In spite of our special lacquer, which we'll talk about below, the results just aren't right at the acute angle.
Unfortunately, we can't just use the lens to increase the depth of field like we would with a normal camera. This is because the emissions aren't the same strength in every direction. Below 15 degrees Celsius, all we get from our measurements this way is garbage.
Current page: Doing It Right
Prev Page Our Infrared Camera Equipment Next Page Emissivity And Transmittance In Practice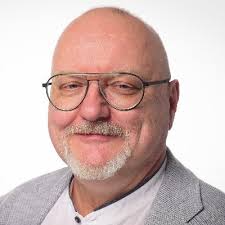
Igor Wallossek wrote a wide variety of hardware articles for Tom's Hardware, with a strong focus on technical analysis and in-depth reviews. His contributions have spanned a broad spectrum of PC components, including GPUs, CPUs, workstations, and PC builds. His insightful articles provide readers with detailed knowledge to make informed decisions in the ever-evolving tech landscape
-
samopa Do they have some kind of API, to be connected to other system without using their proprietary software ?Reply -
dmnwlv Respect to tomshardware in its quest here to form a more complete picture in hardware tests and for presenting verifiable (factual) data in its reviews.Reply
I never bothered with all other sites' temperature charts/reviews on gpus ever since toms started doing this. -
FormatC 17594187 said:Do they have some kind of API, to be connected to other system without using their proprietary software ?
They have an API and a helpful documentation too. :)
-
Flying-Q I like all the isolation and standardisation you use for consistent, repeatable and accurate measurement. I have a question though: would a cowl over the CPU, chipset and memory make any difference to preventing reflected heat contribution from those components?Reply -
FormatC Only, if the waves goes in the same direction. Upgoing heat is no problem (90° crossing).Reply
I tried it to cover it with a thick, black foam plate - no difference. :) -
dr3cks4u Very good article, thanks for that. I´m sure a lot of people don´t know how time-consuming this kind of measurement is. Question @ Igor: Is the emissivity of the used lacquer constant across the electromagnetic spectrum (=grey body) or is it just known for the camera´s spectral range (7,5-13,0 microns)?Reply