Tom's Hardware Verdict
The large build volume and fast print speed of the Anycubic Photon Mono impressed us, but our issues with the built-in WiFi and the slicer app kept this printer from rising to the top.
Pros
- +
+ Large build volume (almost 10 inches on the Z)
- +
+ Rigid dual-Z gantry and hefty metal frame
- +
+ Photon Workshop software is easy to use
Cons
- -
Build platform is difficult to clean
- -
Included WiFi feels a bit clunky
Why you can trust Tom's Hardware
The Anycubic Photon Mono X is the largest printer in the Photon family of printers and offers a lightning-fast, 2-second per-layer cure time thanks to the included 4K Mono LCD used for masking. An impressive printer that doesn’t compromise between speed and size, the Photon Mono X offers the best of both worlds while remaining at the sub-$600 price point. The XY resolution of .05mm is comparable to smaller 3D printers that use lower-resolution screens such as the Anycubic Photon Mono or the Elegoo Mars 2 Pro. Despite a few quirks that require some attention to get the most out of the Photon Mono X, the included Photon Workshop software is relatively easy to use.
Anycubic Photon Mono X Specifications
Machine Footprint | 10.63" x 11.42" x 18.7" (27cm x 29cm x 47.5cm) |
Build Volume | 7.55" x 4.72" x 9.84" (192mm x 120mm x 245mm) |
Resin | DLP Photopolymer Resin |
UV Light | 405nm UV LED |
Masking LCD Resolution | 3840 x 2400 px |
Masking LCD Size | 8.9-inch |
Interface | 3.5-inch LCD Touchscreen |
XY Axis Resolution | .05mm |
Included in the Box of Anycubic Photon Mono X
The Anycubic Photon Mono X ships in a reinforced box with all of the included accessories nested inside the printer. All of the accessories required to use the printer as well as enough consumables to get you through a couple of prints are included in the box. This includes a bag with several rubber gloves for handling the resin, a hospital-style fabric mask, a plastic scraper for stirring resin, a metal scraper for removing parts from the build platform, a few paper funnels for recycling the resin after printing and a few extra screws. I appreciate that Anycubic includes a paper copy of the assembly instructions with the printer, which is always a nice touch when first getting the print up and running.
Design of Anycubic Photon Mono X
The Anycubic Photon Mono X looks like a standard resin 3D printer from a distance, but take a closer look and you’ll see a machine that is built with high-throughput in mind. A bright and distinct yellow color, the UV-resistant lid feels solid but not brittle, and the base of the machine has a groove that runs along the edge which mates up perfectly with the lid. The metal base of the machine feels sturdy and bottom-heavy, which inspired confidence that this machine was made with high-performance components.
The large build platform of the Photon Mono X means that the amount of force required to pull the build platform up will be higher than machines that cure smaller cross-sections of material. To avoid bending or any wobbling in the Z axis, Anycubic has built a rigid Z-stage that uses a threaded rod and a pair of linear rails to move the build platform up and down between layers. This is a solid mechanical system, and I was impressed with the overall fit and feel of the all-metal gantry.
The build platform has a taper on two sides which is designed to allow resin to drip back into the vat after it has lifted clear of the resin. It works reasonably well, but the resin has a tendency to pool around the edges and has to be scraped back into the vat manually with the plastic scraper between prints. The surface of the build platform has a brushed aluminum surface which has a high level of adhesion and is easy to clean.
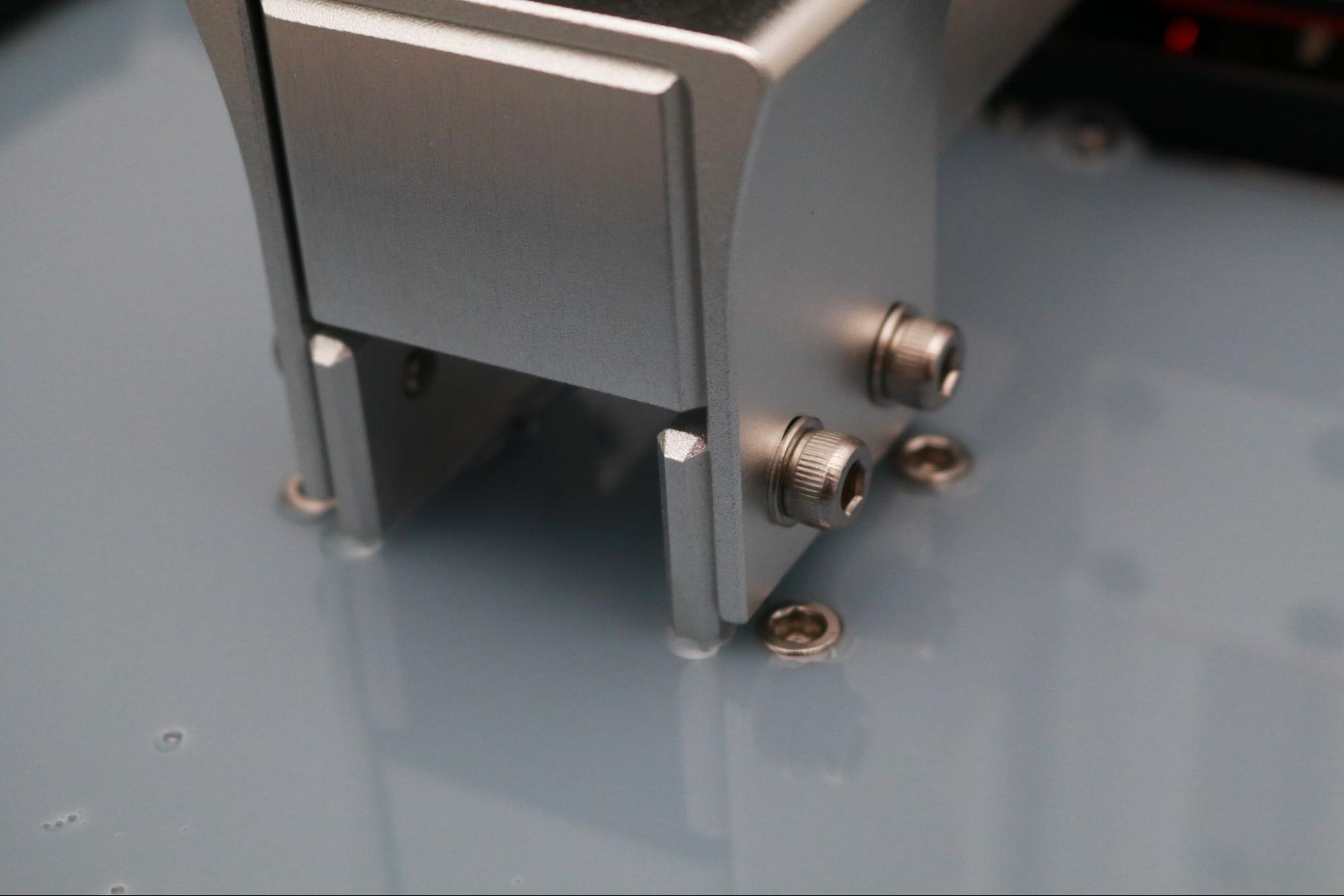
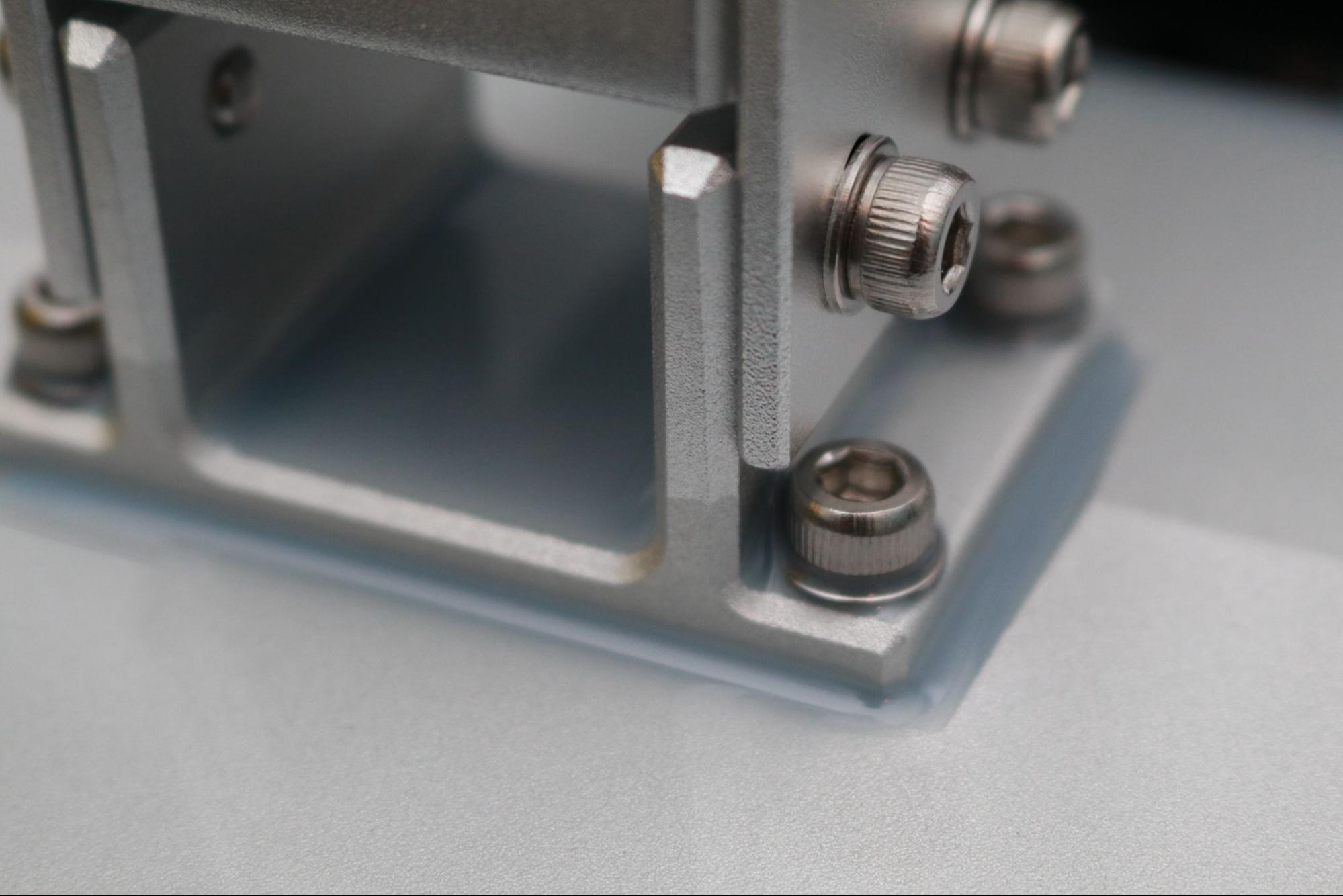
Unfortunately, the design of the build platform includes four upward-facing bolts which can submerge into the resin vat during printing. The build platform bracket also has a slot cut in the center which fills with resin during printing and is difficult to clean. This is a poor design choice, as the flooded area drips uncured resin into the groove cut between the bracket and the platform. This build platform design is difficult to fully clean manually, and requires a lot of scrubbing to get into the various nooks and crannies to remove uncured resin when switching materials or colors.
The Photon Mono X uses a resin vat with a removable FEP film liner on the bottom, unlike the proprietary FEP assembly found on the Photon Mono. This means you can replace the FEP film (a consumable) with either a direct replacement from Anycubic or any number of aftermarket replacements. The FEP film is held in place with 14 rear-mounted bolts and 22 smaller bolts that keep tension on the film after mounting. My favorite feature of the resin vat on the Photon Mono X is the four small studs at the corners of the vat which elevate the FEP film above whatever surface it’s sitting on. Puncturing the vat can be a messy experience, so keeping it suspended above a flat surface will keep it above anything that might make an indentation.
Get Tom's Hardware's best news and in-depth reviews, straight to your inbox.
The base of the Photon Mono X has four locating holes which the vat uses to click into place. This means the vat is held in place while it’s being tightened down with the two included thumbscrews. The vat also has a pour spout integrated into one of the corners, so draining resin back into a bottle doesn’t result in a mess.
Included with the Photon Mono X is a small antenna to enable the built-in WiFi capability, which attaches to the base of the printer on the upward-facing surface directly behind the resin vat. The WiFi on the Photon Mono X was a disappointing experience since the connection isn’t actually used by the Photon Workshop app. Using the WiFi requires a complicated set-up that involves putting your password into a .txt file and manually uploading it to the printer. The WiFi is only used to communicate with a mobile app that lets you monitor the print, view the printer history, and adjust a few parameters while printing.
I was able to get the mobile app working, which felt like a major victory after the half hour I spent fiddling with the .txt file to get the printer to recognize my network. The Anycubic 3D iOS app currently has a 2.5/5 rating on the iOS App Store and multiple complaints from users who weren’t able to get it working with the Photon Mono X.
Despite getting it working, I had a hard time finding any real reason to use this app instead of just checking on the printer directly. Without a webcam, a progress bar doesn’t actually inform you how much of the print has finished, only how much of the print should have finished. In addition, the lack of an ability to upload, process, and send a file to the printer means that this app isn’t likely to see a lot of use.
The Photon Mono X uses a 3.5-inch color LCD touchscreen as a primary interface. The UI feels a little dated (it reminds me of the default WinAmp skin), but it contains all of the functionality required to calibrate the printer and start a print. You can also use the LCD touchscreen to pause, stop, and monitor the parameters of the print during a print job. The printer has the USB input, power switch, and power input located on the side of the machine which makes it easier to access than reaching behind the machine to turn it on and off between jobs.
Leveling the Build Platform on Anycubic Photon Mono X
Like most resin 3D printers, the Anycubic Photon Mono X requires a manual calibration process to ensure the build platform is perfectly level with the masking LCD. This allows each layer to cure evenly between the build platform and masking LCD while only adhering to the platform. The included printed user manual and the digital .PDF included with the USB drive cover this process in detail, and also include pictures to show the calibration process step-by-step.
This calibration process is the same as the process used by the smaller Anycubic Photon Mono, and it works about as well. I’m not a fan of the four bolt process, as over-tightening the bolts can cause the build platform to shift slightly during leveling. The two bolt ball-and-socket build platform leveling used by the Elegoo Mars 2 Pro and Elegoo Saturn is easier to use, and provides a very consistent leveling experience with less manual input required.
Printing Safety with Anycubic Photon Mono X
The Anycubic Photon Mono X uses 405nm UV resin, a material that you need to handle safely when in an uncured state to avoid injury. The resin can be harmful when making contact with skin, so make sure to wear gloves when pouring, cleaning up, or handling uncured resin. I also make sure I’m wearing gloves when removing the build platform after a print, as the resin tends to pool on top of the platform and can drip off while the platform is being removed.
Make sure you use the Photon Mono X in a well-ventilated room to minimize the danger from inhaling fumes. Any spills or uncured resin stuck to a surface should be cleaned using 99% Isopropyl Alcohol and the container for the resin should be kept closed and secured when not actively pouring material.
Anycubic sent a bottle of their Plant-Based Eco Resin for testing this printer. This material is advertised as being made from soybean oil and is a biodegradable eco-friendly alternative to other thermoset resins. The exposure times for this resin are similar to standard photopolymer resins, so I didn’t make any modifications to print settings for this material. Another advertised feature of this material is the low odor; something I did notice and appreciate during printing.
Printing the Included Test Print on the Anycubic Photon Mono X
The Anycubic Photon Mono X includes a prepared test model on the USB thumb drive, and it’s the same model that is included with the smaller Anycubic Photon Mono. The model is a thin lattice structure in the shape of a cube with the Anycubic Photon logo suspended internally. I opened the file in Photon Workshop to see what settings were used, and I was surprised to see a 1.5-second per-layer cure time and a 45-second bottom exposure time, as opposed to the default 2 second per-layer cure time and 40 second bottom exposure used by the Photon Workshop.
The leveling of the printer wasn’t dead-on for this first print, and you can see the bottom few layers of the cube have been compressed together and formed a ring around the base. Despite this slight compression, the base of the model measured 35.05mm in diameter at various points, which is within the advertised .05mm / 50 micron accuracy of the machine. Printing a lattice structure like this is always an ambitious test for most 3D printers due to the thin walls and lack of support structure, but the Photon Mono X printed the model without any defects or issues.
Preparing Files for Printing with Photon Workshop
The Anycubic Photon Mono X is compatible with Anycubic’s slicer app, called Photon Workshop. Photon Workshop allows users to import 3D models, hollow them, add support structures, export 3D printable files, and more. Interestingly enough, the USB drive included with the Photon Mono X doesn’t include any software, so I downloaded the latest version (2.1.24) from the Anycubic site. While I appreciate the fact that this would encourage a user to download the latest version of the software, it might be an issue for anyone who is expecting the printer to ship with the software already loaded on the drive.
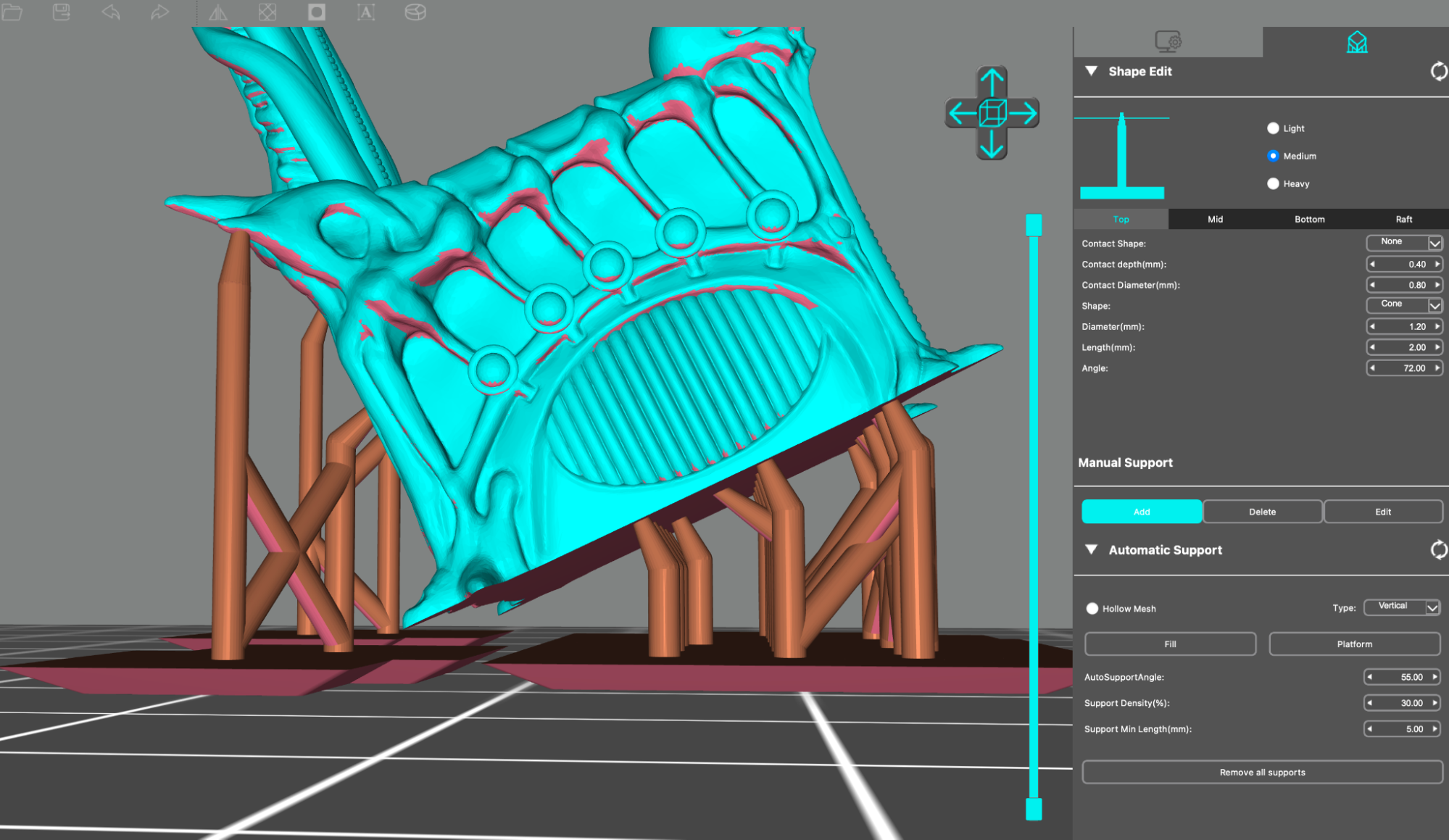
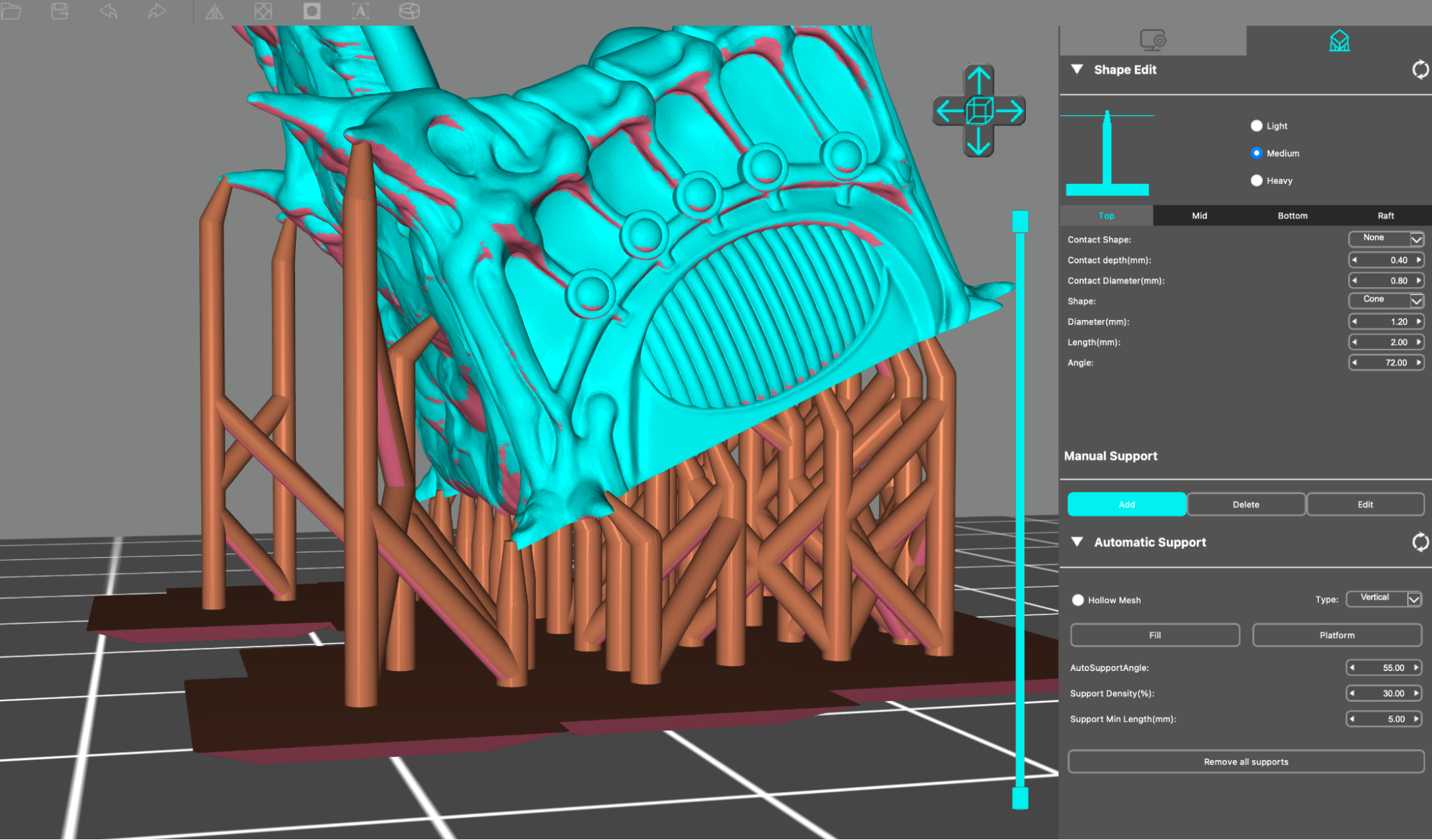
Adding a support structure to a resin 3D print is a critical step, and the overall experience of generating support structures with Photon Workshop left me underwhelmed. Unlike the support structure on an FDM printer where the support keeps the model from collapsing, the support structure on a resin printer keeps the part suspended from the build platform without falling. Resin printers lift the part between layers, so the thicker the cross-section of the part, the more force is required to separate it from the FEP film on the bottom of the vat.
To combat these peel forces, adding a tilt of 45 degrees or so will minimize the cross-sectional width and make a part easier to print. Unfortunately, Photon Workshop doesn’t lift the part after this tilt is added, so models will typically need to be manually raised on the Z axis to add supports underneath the model. This operation is performed automatically in Chitubox, a similar slicing app used by the Elegoo resin 3D printers like the Saturn and the Mars 2 Pro. This seems like a small step, but the lack of support generated on those initial layers can be the difference between a successful print and an unsuccessful one.
I used the 32mm miniature Throne 3D model from Loot Studios as a benchmark piece for testing the latest release of Photon Workshop. I’m using the Anycubic Plant-Based Eco Resin, so I selected ‘Plant-Based’ as resin type in Photon Workshop. Changing this setting doesn’t seem to change any print settings and I’m not sure that it makes any impact in the finished print. With a per-layer cure time of 2 seconds and a bottom exposure of 40 seconds for the first 6 layers, the Throne model had an estimated print time of 3 hours and 42 minutes. After exporting the 3D model, I transferred the file via USB and started the print on the Photon Mono X.
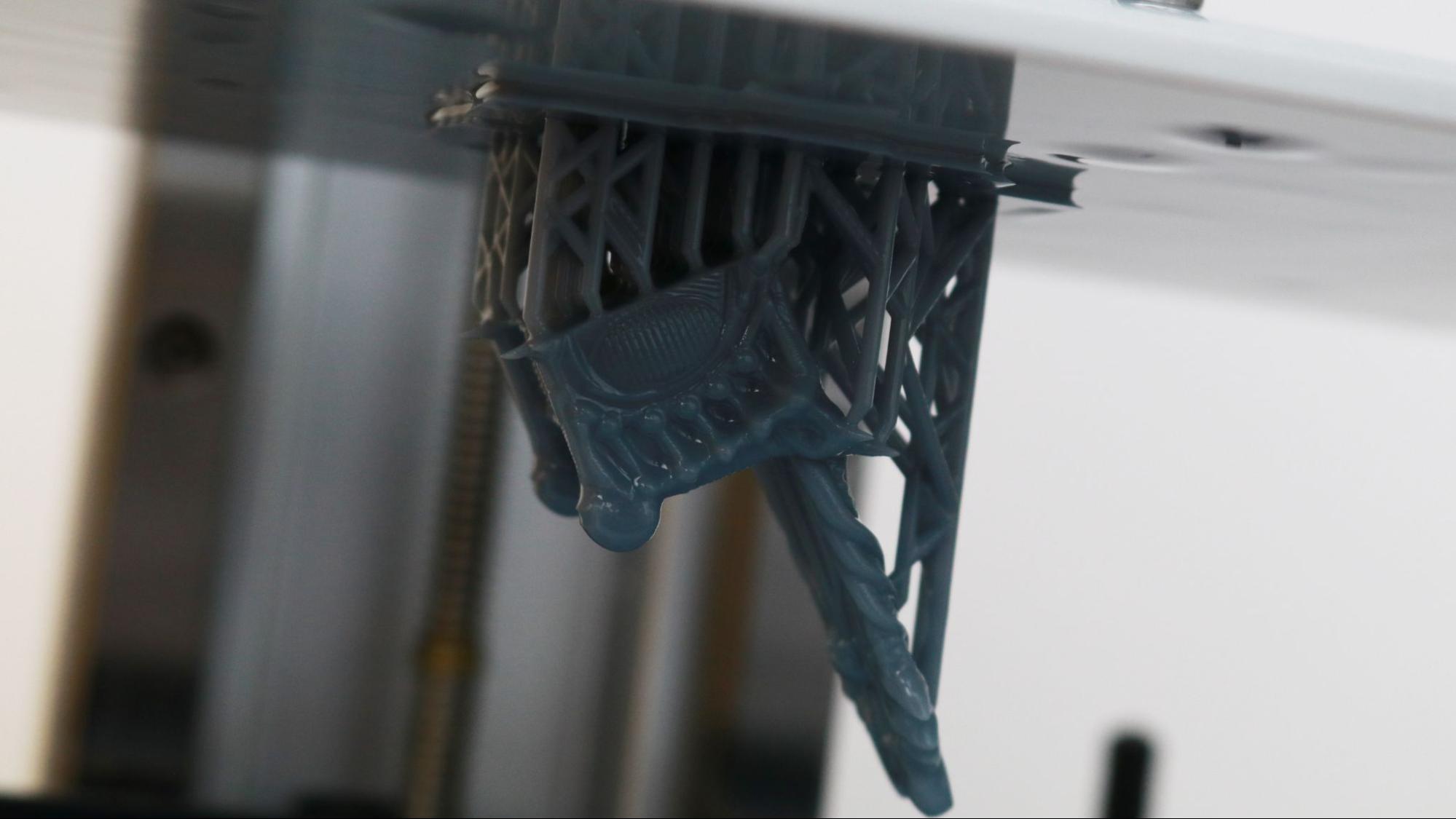
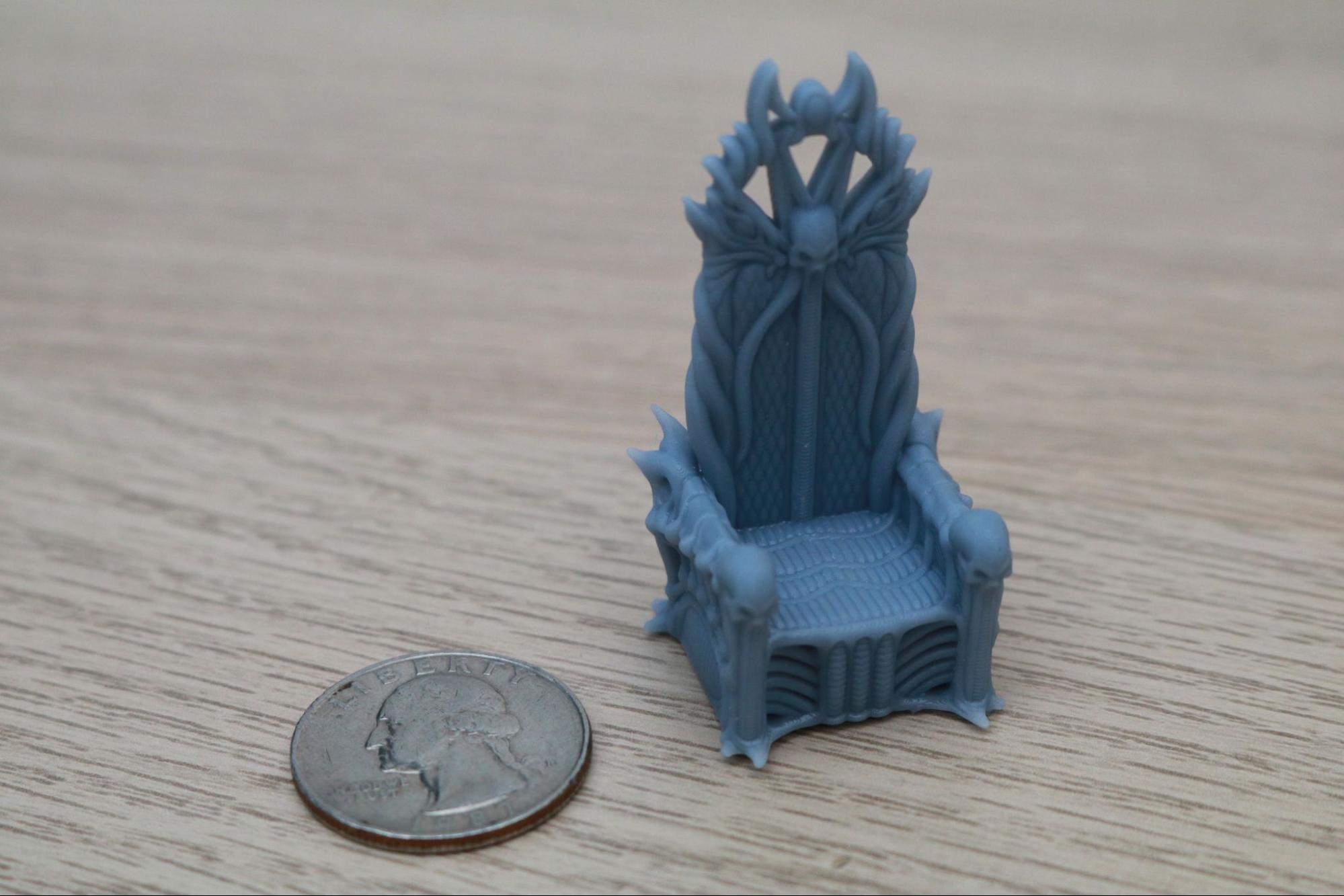
The model printed perfectly, and the hybrid automatic/manual support structure held the model firmly to the build platform. After washing the model using the Anycubic Wash and Cure Plus, I easily removed the support structure and put it back in the Wash and Cure Plus for a cure cycle. Despite the small size of the part, the fine details and thin structures were strong enough to stay attached to the model while the support structure was being removed.
The detail on the model is crisp and in-focus, and the even the fine detail on the fabric of the seat of the throne is easily visible. This level of detail is what I would expect from a printer with an XY accuracy of 50 microns, and it is equivalent to the results I’ve seen from other resin 3D printers with a similarly advertised accuracy.
Washing and Curing Models with Anycubic Wash and Cure Plus
The Anycubic Wash and Cure Plus is an accessory designed to complement the Anycubic Photon Mono X and make post-processing resin 3D prints a clean and easy process. After printing a model on a resin 3D printer, there are three important follow-up steps. First, the part has to be rinsed of excess resin using an isopropyl alcohol solution. Second, the support structure must be manually removed from the model. Third, the model must be cured in a UV chamber to fully polymerize and solidify the resin. This can be a really messy process, and the Wash and Cure Plus provides a clever solution to this problem. Anycubic sent us the Wash and Cure Plus along with the Photon Mono X, so we could test the full workflow from liquid resin to finished part using these two machines.
After a print is finished on the Photon Mono X, the build platform will lift clear of the vat. This allows you to remove the build platform and clean the part, and also gives any accumulated resin time to drip back into the vat without spilling onto the printer. I printed the bust of Alexandra Uthgrade from Loot Studios, which prints in two pieces and is also hollow to reduce the amount of resin required for printing.
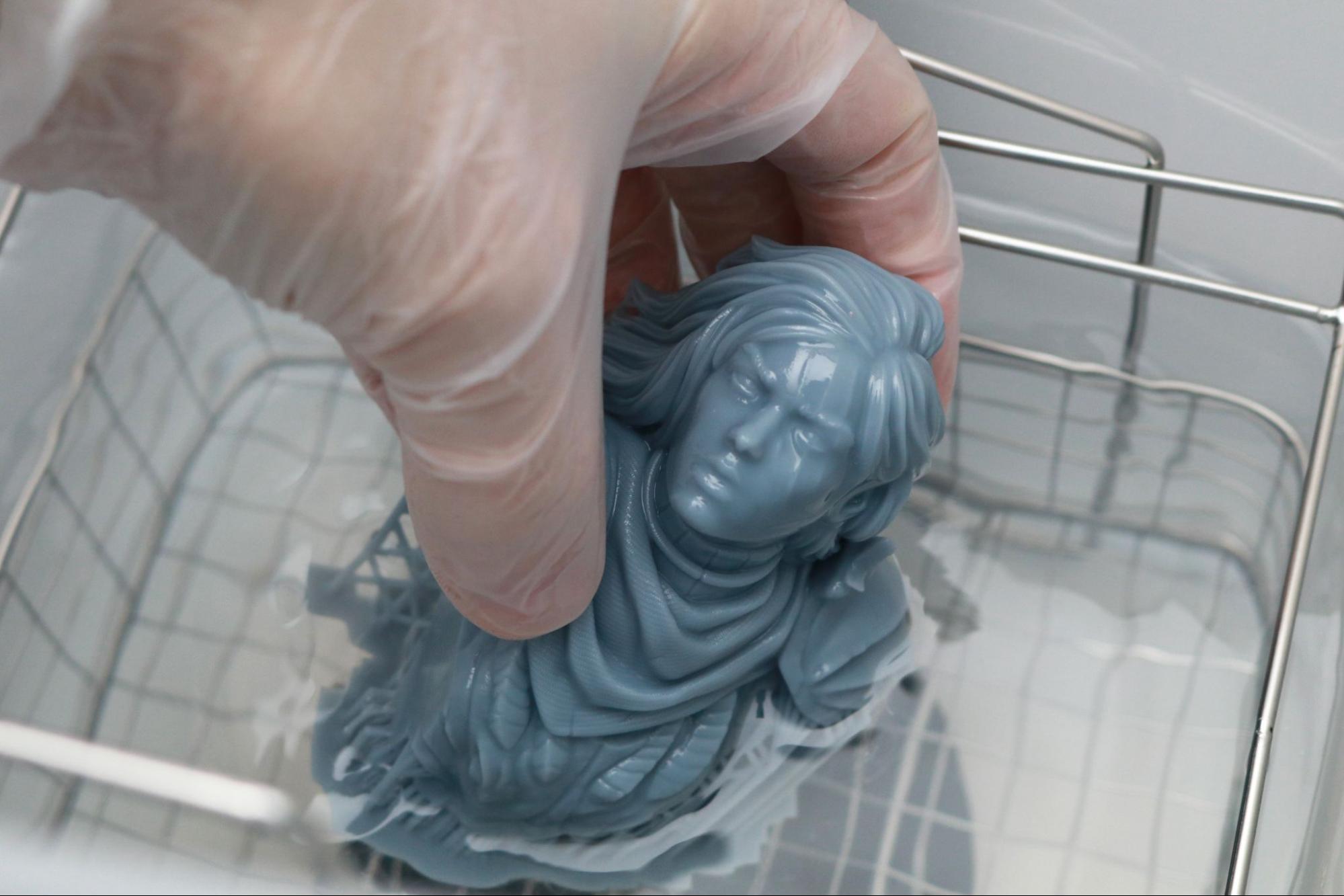

The Wash and Cure Plus uses a plastic basket with a magnetically-driven impeller at the base and a metal basket that safely holds the parts above the impeller. After placing the parts in the basket, I ran the wash cycle for 4 minutes, which created a vortex in the basket and did a thorough job rinsing the excess resin from the part. The magnetic impeller ramps up in speed and changes direction during the wash cycle, so the part is evenly rinsed of excess resin.
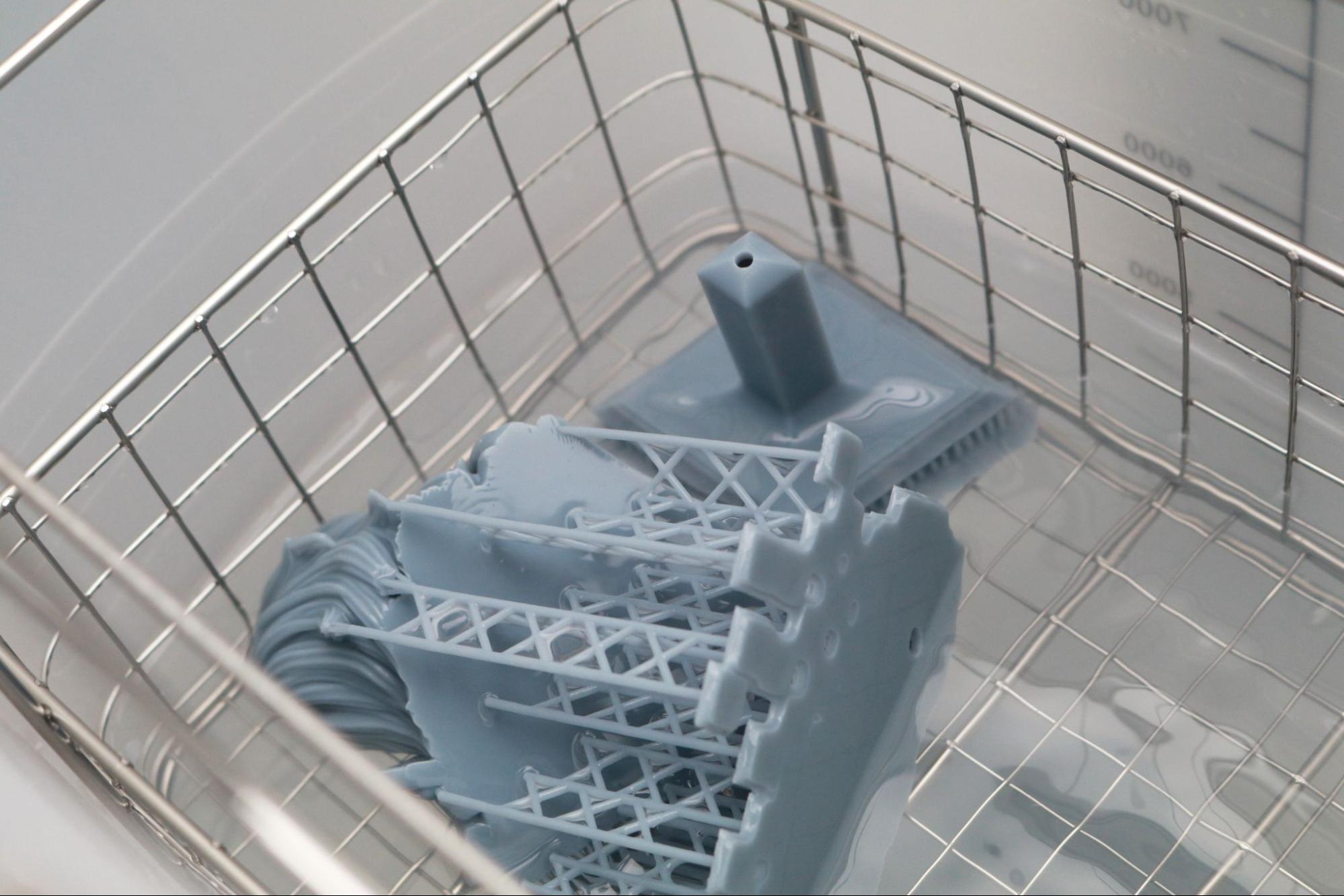
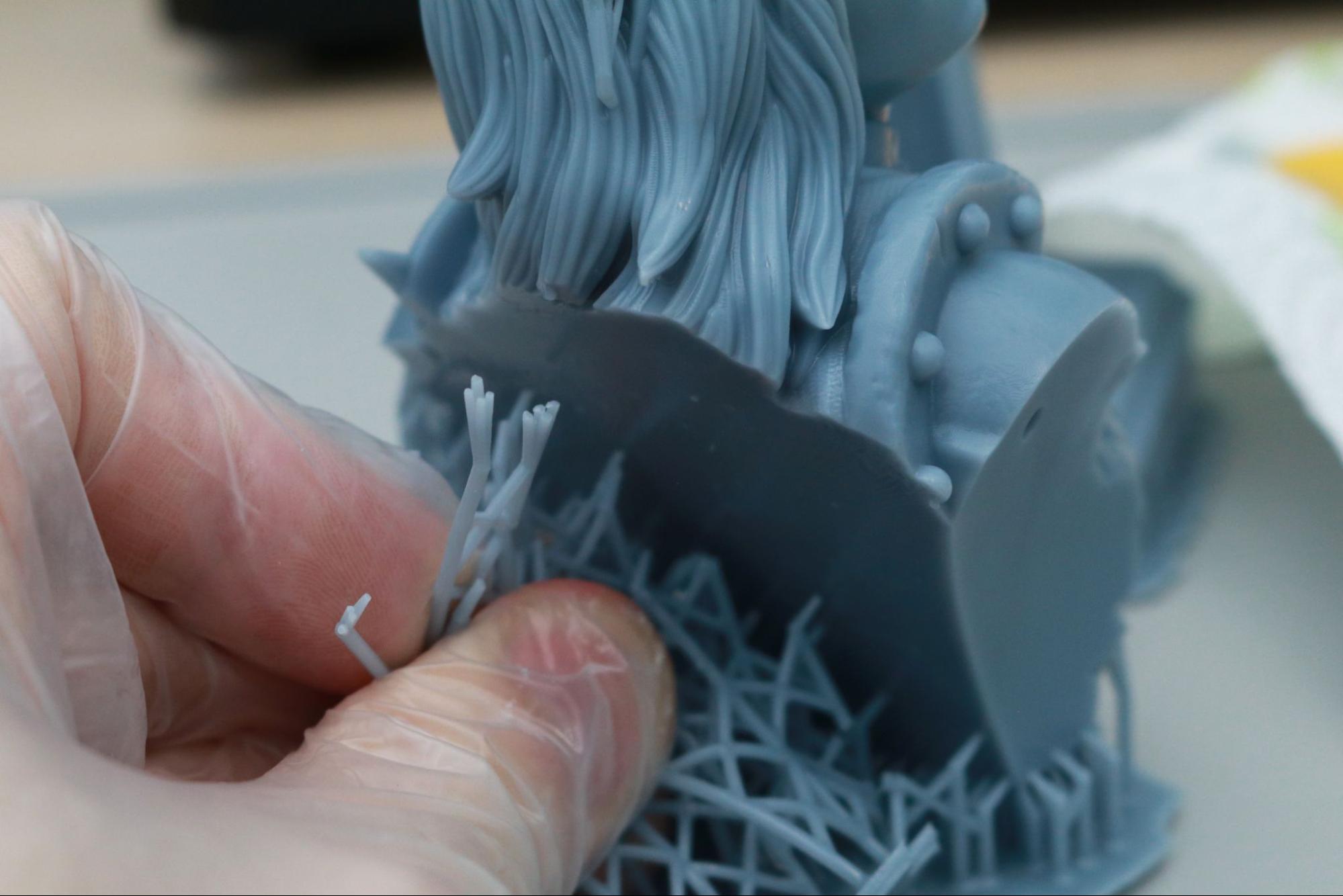
The basket can be lifted from the tank without touching the isopropyl alcohol, which is something that I really appreciate Anycubic designing into the machine. After letting the alcohol air-dry from the parts, I removed the support structure from the part by peeling it off. The support structure wasn’t difficult to remove in the semi-cured state, and the alcohol wash got rid of the film of resin on the part.
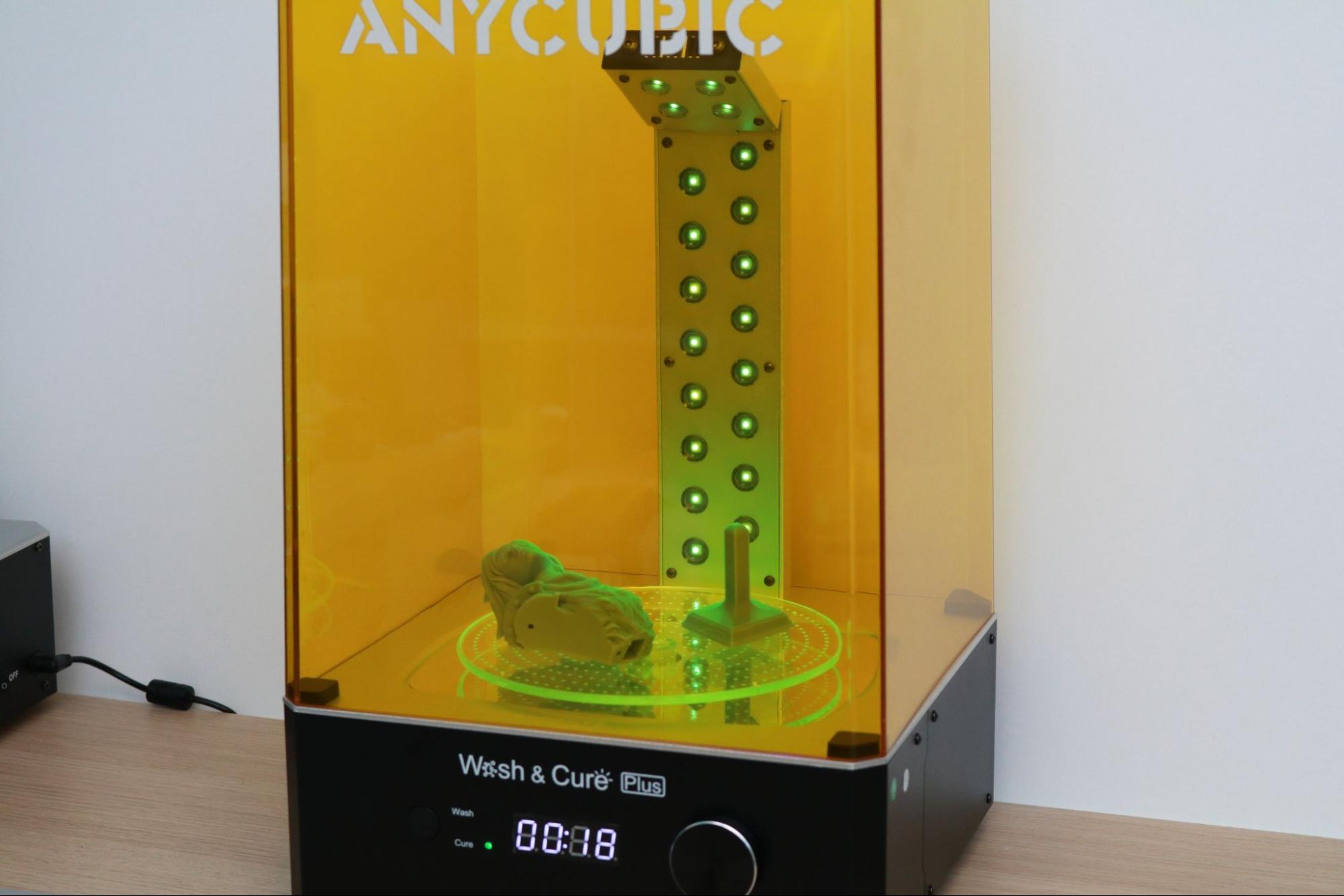
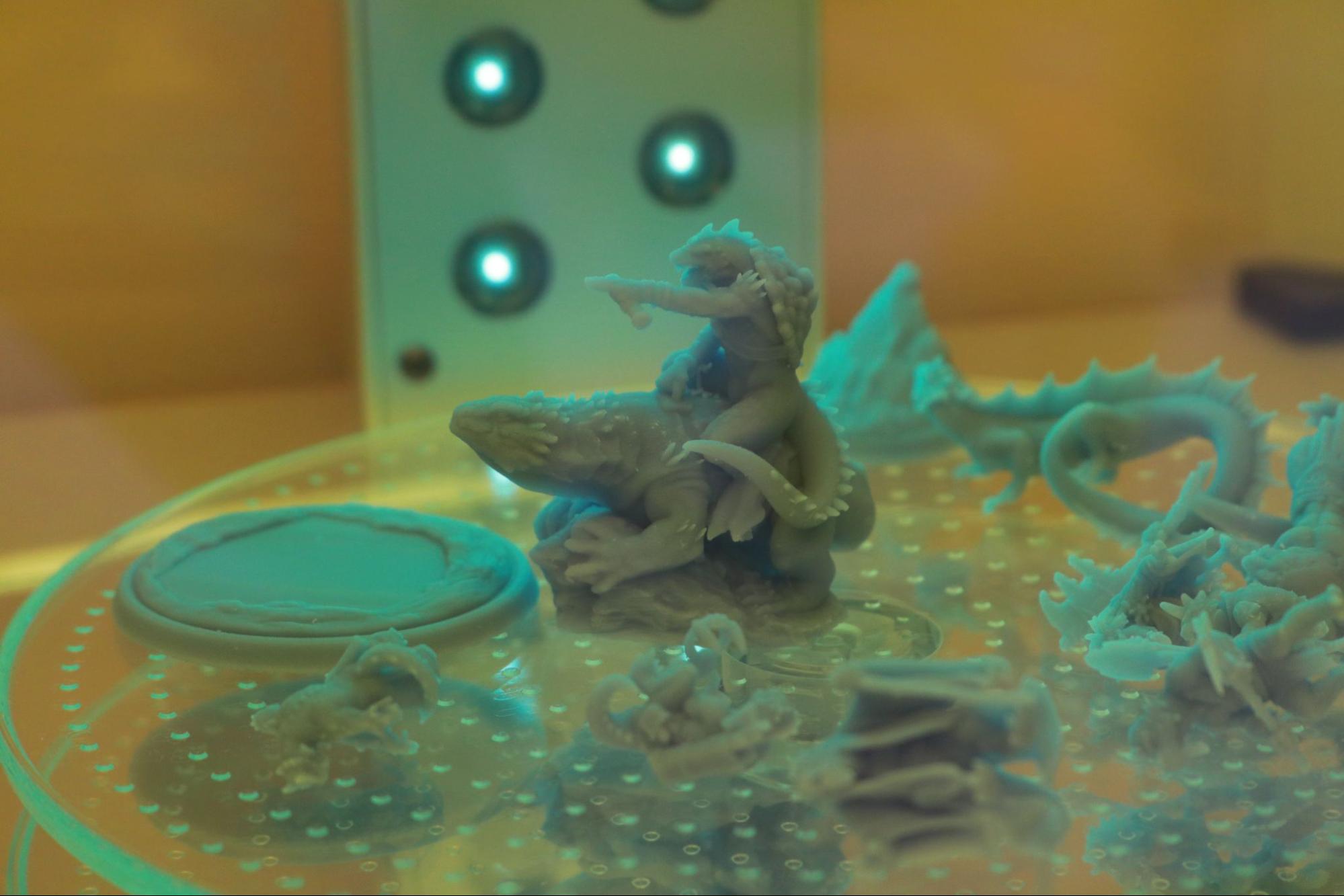
Once the model has been rinsed and the support structure has been removed, the model needs to be cured before it can be safely handled. The Wash and Cure Plus features a strip of LED lights that fully cure the resin and the very top of the strip can be angled down to cure the top of the model as well as the sides. The Wash and Cure Plus uses a reflector strip underneath the transparent spinning base to cure the underside of the model, which means the model is being cured fully as the plate rotates.
Once the curing process is complete, the model can be painted, sanded, coated, or simply left as-is. The grey color of the Anycubic Plant-Based Eco Resin is a favorite of mine because it shows a lot of detail and contrast without being difficult to photograph. The completed bust looks impressive, with a high amount of detail visible on the armor and even individual hairs visible on the eyebrows.
Printing a Full Build Platform on the Anycubic Photon Mono X
With an 8.9-inch 4K masking LCD, the Anycubic Photon Mono X has a strong advantage when compared to most resin MSLA 3D printers due to the large XY footprint of the machine. Resin MSLA 3D printers operate by curing a single layer at a time, so for the most part, printing one part or 10 parts takes about the same amount of time. The large build volume of the Photon Mono X is ideal for printing multiple parts, so I printed 11 parts simultaneously to test out the throughput of the machine.
Photon Workshop easily handled all 11 models and didn’t slow down during slicing, despite the ~20 MB file size per part. Photon Workshop gave an accurate estimate of 3 hours and 26 minutes to print all of these models simultaneously. This type of throughput is beneficial for anyone printing large quantities of parts. The Photon Mono X is capable of making lots of small parts in a short period of time, especially when compared with an FDM 3D printer like the Elegoo Neptune 2 which has a print time that is tied to the amount of material usage (doubling the number of parts roughly doubles the amount of time).
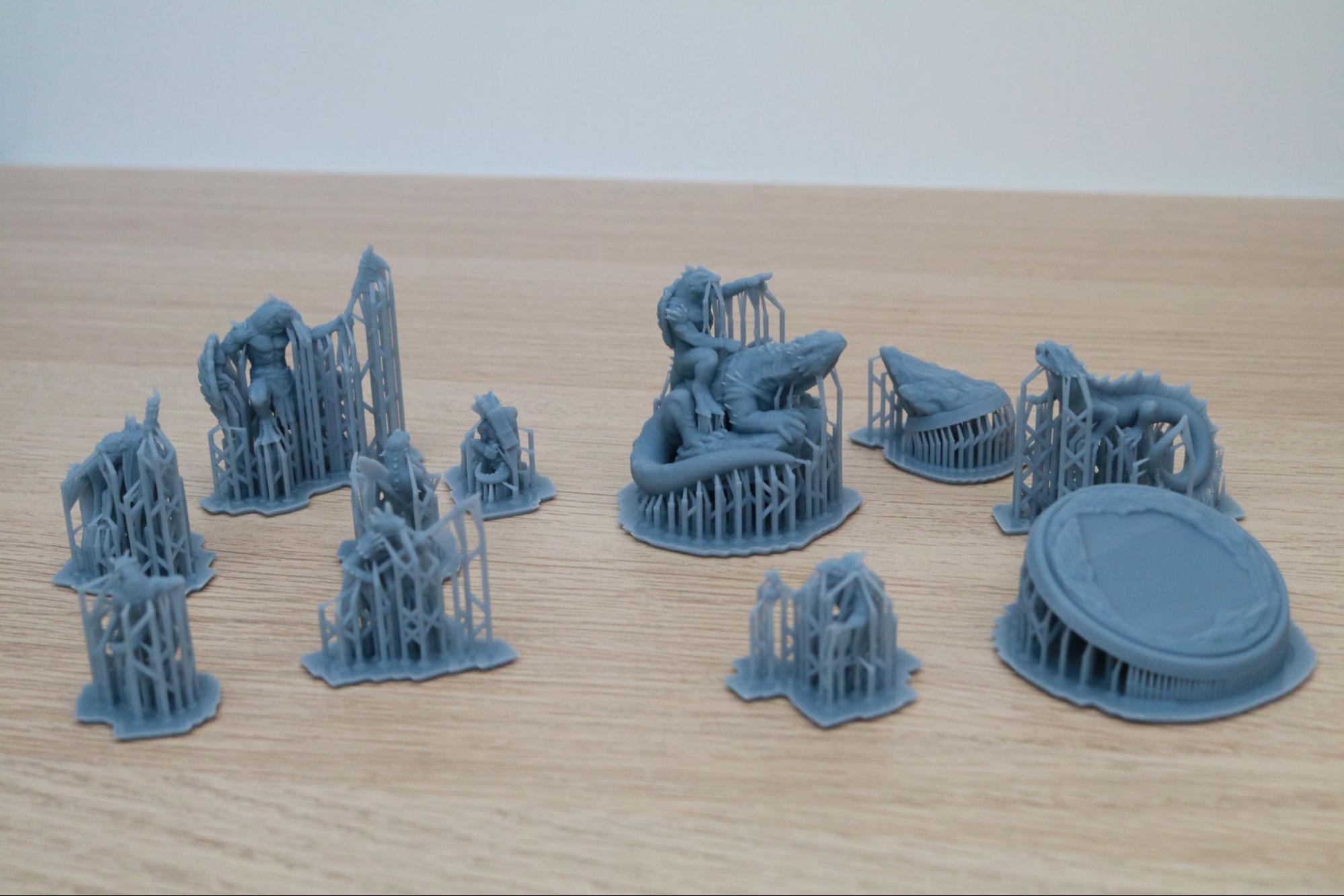
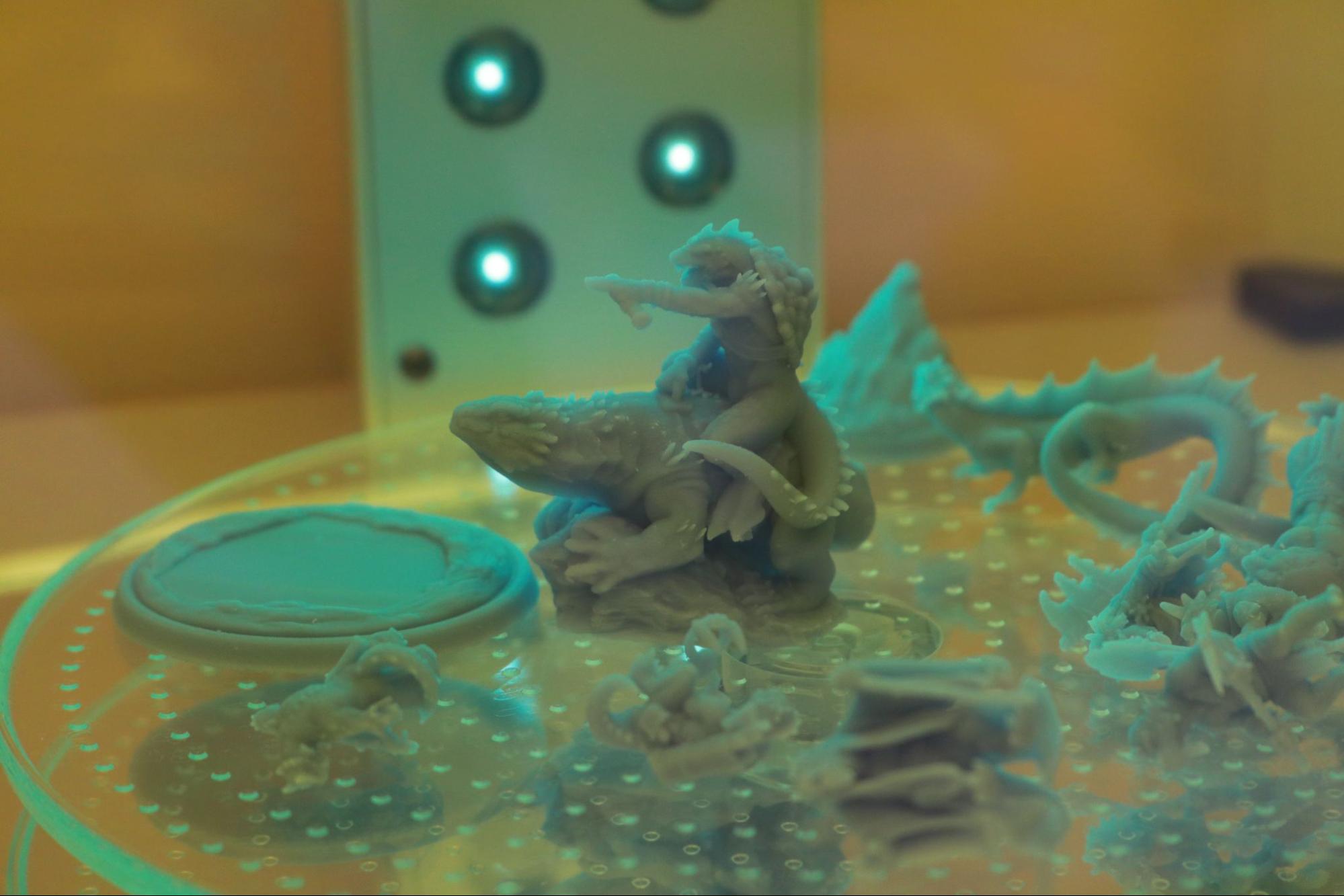
Another benefit of using a post-processing station like the Anycubic Wash and Cure Plus is that the parts can be processed as a batch. I put all of these parts in the wash basket of the Wash and Cure Plus and rinsed them as a single batch, which offered substantial time savings when compared with rinsing each model individually. After removing the support structure, the parts could also be cured in a single batch, which again reduces the overall amount of time from liquid resin to finished part.
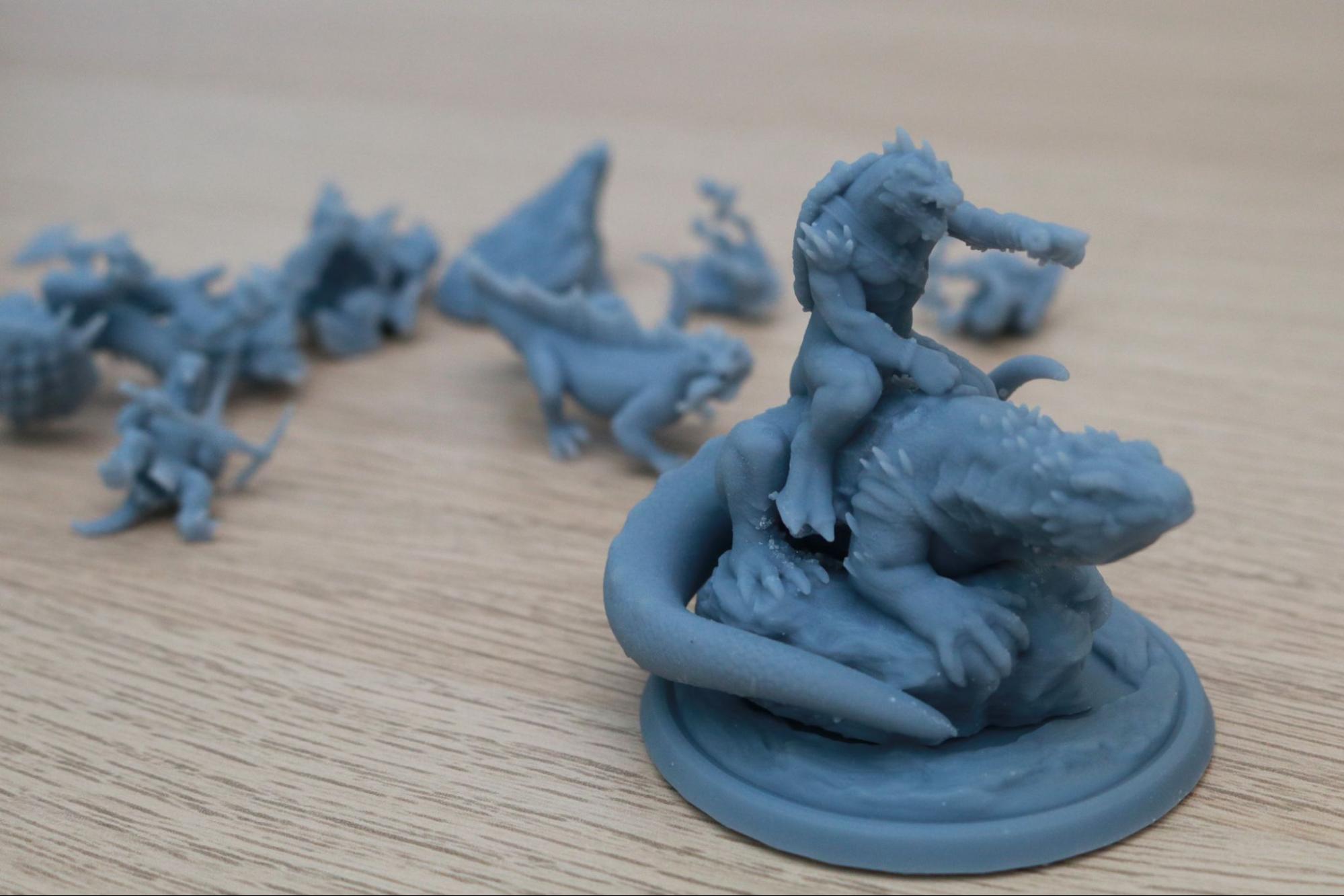
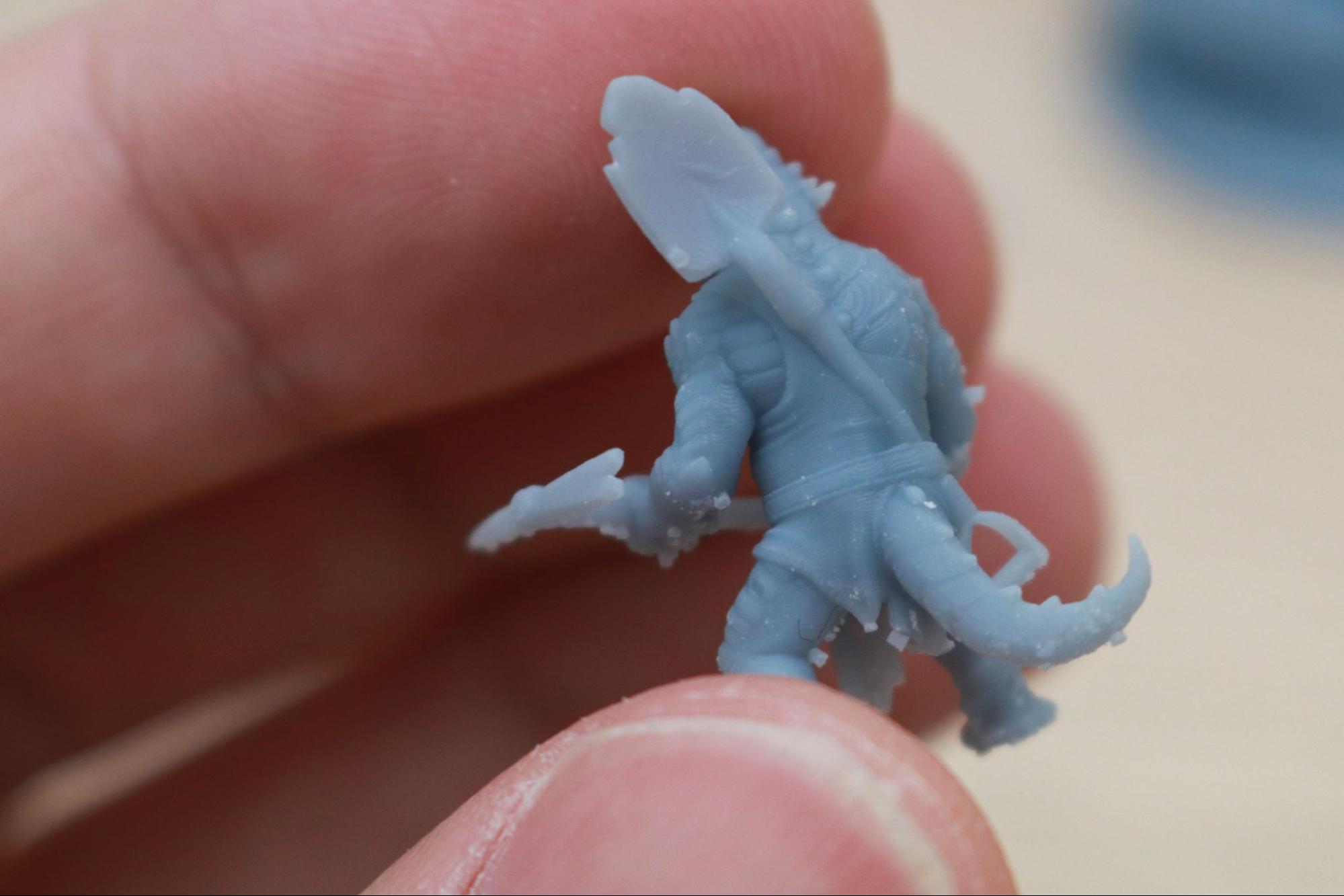
Printing 32mm miniatures can be a challenge due to the amount of detail present on the models and the difficulty in removing the support material typically present. For instance, one of the models had a shovel on his back, which had a handle that was about the same thickness as a column of support. The Anycubic Plant-Based Eco Resin separated easily from the model and I didn’t have any issues with the models being too brittle or breaking during printing. There are some small marks left on the model from the support removal process, but they didn’t seem to be any better or worse than similar marks left on models printed by the Elegoo Saturn.
Comparison of the Anycubic Photon Mono X vs. Elegoo Saturn
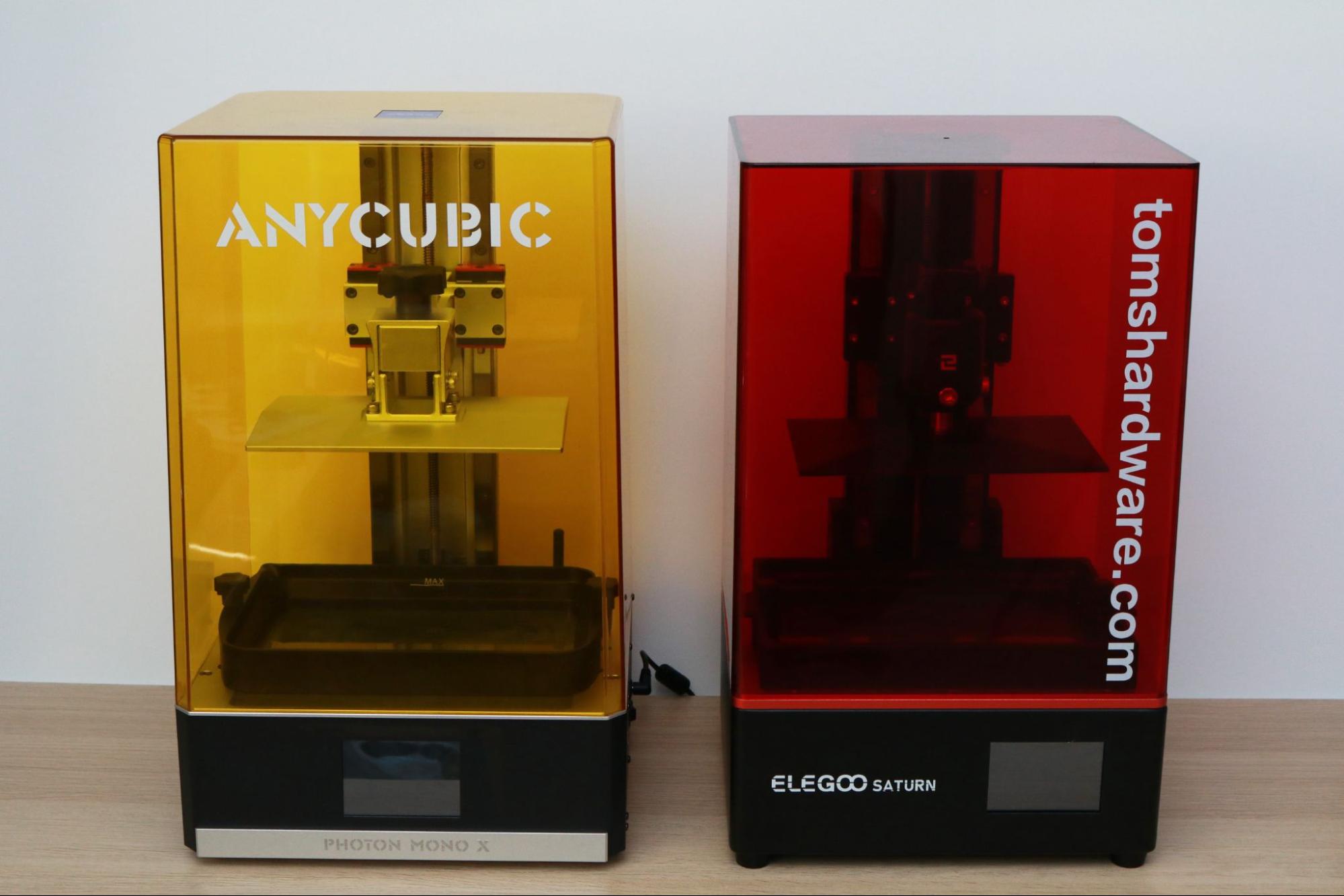

The Anycubic Photon Mono X shares enough similar features and specs with the Elegoo Saturn to make the two machines direct competitors, so it’s worth examining the two machines side-by-side. The Photon Mono X has a much larger overall build volume than the Saturn, but it’s also a physically larger machine which will take up more space on a desk or table.
Header Cell - Column 0 | Anycubic Photon Mono X | Elegoo Saturn |
---|---|---|
Masking LCD Resolution | 3840 x 2400 | 3840 x 2400 |
XY Resolution | .05mm | .05mm |
Build Dimensions | 7.55 x 4.72 x 9.84 inches | 7.55 x 4.72 x 7.87 inches |
Build Volume | 350.66 cubic inches | 280.46 cubic inches |
Printer Dimensions | 10.63 x 11.42 x 18.7 inches | 11.02 x 9.44 x 17.55 inches |
Printer Volume | 2270.08 cubic inches | 1825.71 cubic inches |
Build / Footprint Ratio (higher is better) | 15.40% | 15.40% |
The specs of these two printers are similar, but the numbers don’t tell the entire story. While the Elegoo Saturn uses a ball and socket leveling process for the build platform which is easier to use, the scarce availability of this machine means that it will take some luck to find for sale at the standard retail price of $499. The additional two inches of Z height on the Photon Mono X could also be a make-or-break feature for anyone interested in printing long or tall parts in a single piece.
Bottom Line
The Photon Mono X is currently available for $529 directly from Anycubic or $599 with free shipping from Amazon. This price point and feature set is directly comparable to the Elegoo Saturn, which has a smaller build volume but similar XY resolution and per-layer cure times. The Saturn has a reputation for being difficult to find and is frequently sold out (it’s currently sold out on Amazon as of the writing of this review), so the availability of the Photon Mono X as well as the extended Z height make it an appealing option in the sub-$600 price range.
The large build volume of the Anycubic Photon Mono X makes it an easy decision for anyone interested in a high-throughput 3D printer or just a machine that is capable of making large parts in a single print. If you’re more interested in ultra-high resolution for making miniatures and a large build volume isn’t important, the Phrozen Sonic Mini 4K uses similar technology but offers higher resolution.
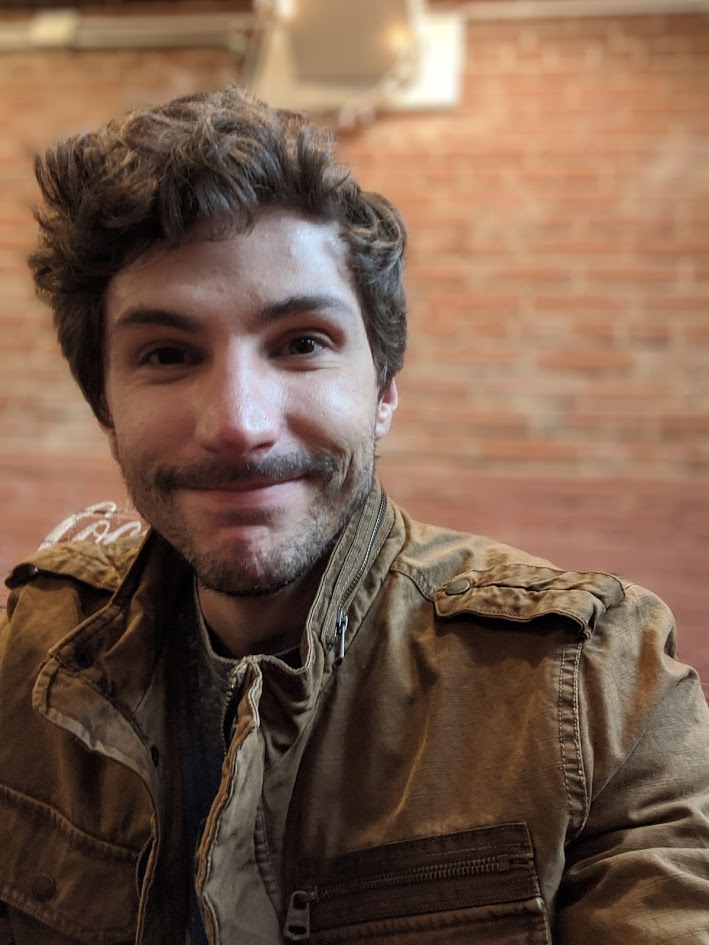
Andrew Sink first used a 3D printer in 2012, and has been enthusiastically involved in the 3D printing industry ever since. Having printed everything from a scan of his own brain to a peanut butter and jelly sandwich, he continues to dive ever more deeply into the endless applications of additive technology. He is always working on new experiments, designs, and reviews and sharing his results on Tom's Hardware, YouTube, and more.