$10,000 AI-generated, 3D-printed liquid nitrogen container tested — supercools CPUs up to 3 times faster than standard pots
Supercool, super fast.
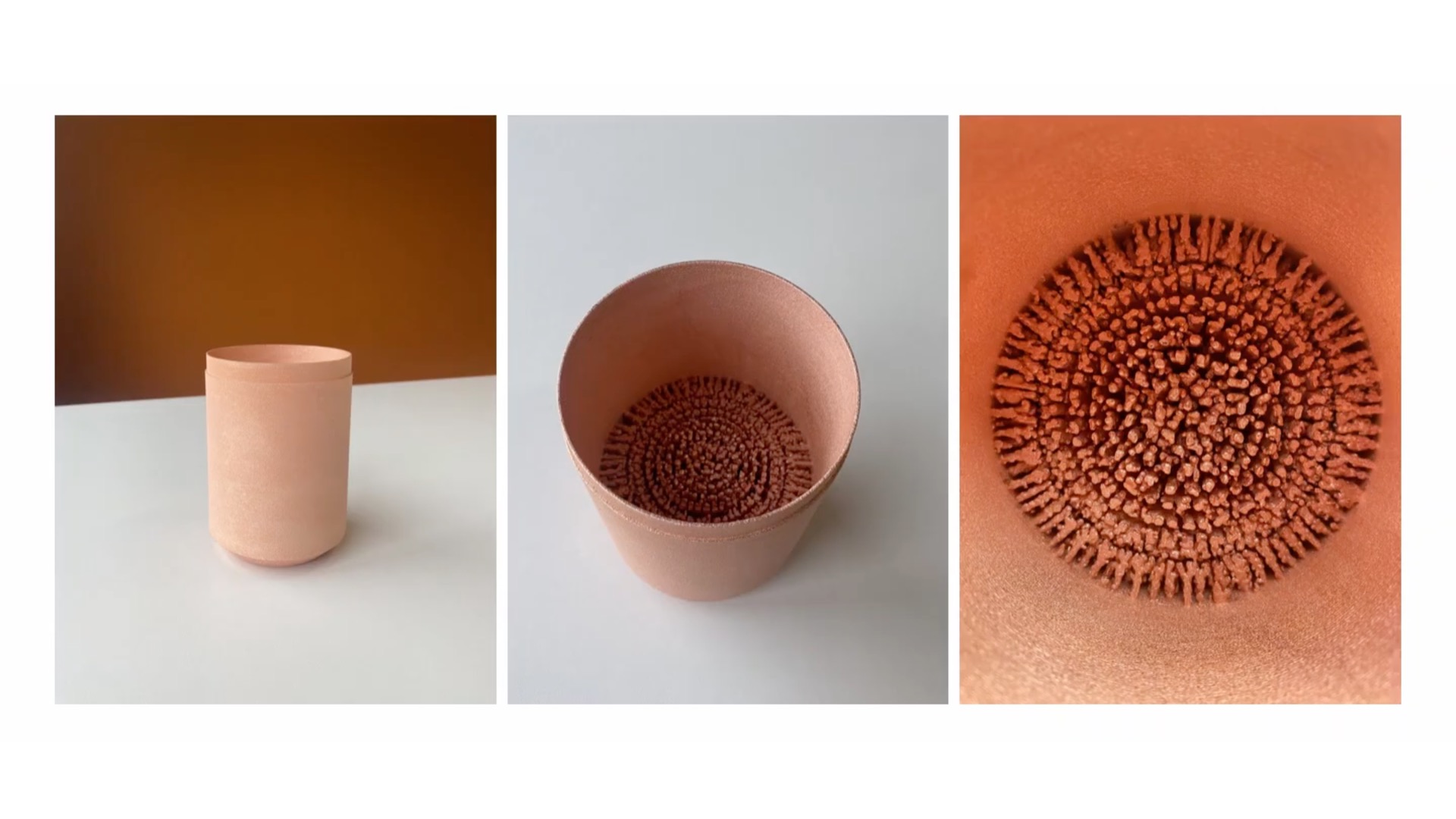
Skatterbencher and three industry-leading partners have completed a feasibility study to see if it’s possible to build a liquid nitrogen (LN2) container using generative AI and additive manufacturing techniques, also known as 3D printing. In a blog post and YouTube video, the partners show that it’s possible, but perhaps not financially wise, for the benefits obtained.
Pieter of Skatterbencher is an expert in overclocking and teamed up with three industry-leading companies to explore the possibilities of AI and 3D printing for LN2 cooling. These included Diabatix, a Belgian company pioneering the use of generative AI in thermal solutions, and 3D Systems, an expert in additive manufacturing. Rounding out the partnership was ElmorLabs, a well-known name in overclocking.
The project used the ElmorLabs Volcano CPU LN2 container as a reference design. It tasked Diabatix’s ColdStream Next AI platform with designing a new LN2 container to improve the reference design. Once the design was complete, the team sent it to 3D Systems to produce a prototype using oxygen-free copper powder.
The prototype's design and manufacture cost $10,000. In comparison, the ElmorLabs Volcano CPU LN2 container used as a reference design sells for just $260.
The base performance tests compared the AI-designed LN2 container with the ElmorLabs Volcano in three categories:
- Cool-down time, how long it took the liquid nitrogen to cool the container from an ambient temperature of 28º Celsius to -194º Celsius.
- Heat up time, the time required to bring the chamber from -194º Celsius to 20º C using a 1,250W heat load.
- 500mL efficiency, the temperature delta between 28.4º Celsius and the lowest achieved temperature, using 500mL of liquid nitrogen.
In testing, the AI-generated LN2 container blew away the Volcano in the cool-down test. It reached -194º Celsius in just under 56 seconds. The Volcano took almost three minutes — three times as long as the prototype. The heat-up test also went in the AI design’s favor, but not as dramatically. The container heated to 20º Celsius 1.2 times faster than the Volcano, more than 30 seconds faster.
Finally, the AI-designed LN2 container proved 20% more efficient than the ElmorLabs design. Using 500mL of liquid nitrogen, the Volcano cooled down to just -100º Celsius, while the AI-designed prototype went down to -133º Celsius.
Get Tom's Hardware's best news and in-depth reviews, straight to your inbox.
Those tests don’t reflect practical considerations, so the team also conducted further tests of a more practical nature:
- An overclocking performance test using Cinebench 2024.
- Checking the temperature delta between the CPU container base and the CPU heat spreader, to see which design most efficiently transferred heat from the CPU.
- An all-out stress test to see how well the CPU fared powered by more than 600W for a couple of minutes.
The team found that while the AI-designed container did beat the ElmorLabs Volcano in real-world tests, the improvements were not nearly as pronounced. Given the dramatic price difference between the AI design and the existing product, the AI design is not a cost-effective alternative.
With the initial testing out of the way, SkatterBencher and its partners may look into performance and cost optimizations and perhaps change the intended use to be for even higher-power CPUs, like the AMD Ryzen Threadripper. The team would also like to commercialize the design but likely has a fair bit of work ahead of it to make it commercially viable.
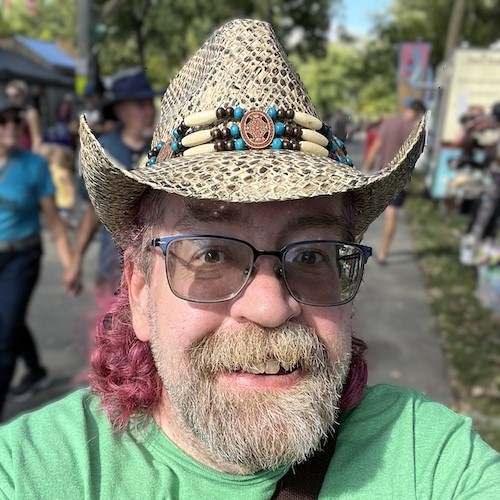
Jeff Butts has been covering tech news for more than a decade, and his IT experience predates the internet. Yes, he remembers when 9600 baud was “fast.” He especially enjoys covering DIY and Maker topics, along with anything on the bleeding edge of technology.
-
bit_user To be fair, genetic algorithms are also pretty good at this sort of design problem - possibly better. All you really need is a sufficiently accurate simulation where designs can be evaluated, so the parameters can be "evolved".Reply
Also, if a simulation let either a human or an AI easily test & refine their designs, I'm sure it would benefit them as well. -
Alvar "Miles" Udell It's not unsurprising if you compare the stock (top) to the "AI" generated (bottom). The "AI" generated version has much more surface area compared to what appears to be a machined copper cylinder.Reply
-
CmdrShepard That's a great example of pointless design "optimization".Reply
Sure, you reach lower temperature faster, but you also heat up faster and heat transfer from the CPU to the base is unchanged so no actual improvement in performance. -
bit_user
Huh?CmdrShepard said:Sure, you reach lower temperature faster, but you also heat up faster and heat transfer from the CPU to the base is unchanged so no actual improvement in performance.
If you remove heat from the heatsink faster, then the heatsink maintains a steeper thermal gradient. That in turn allows a higher rate of heat transfer from the CPU into the heatsink. Ultimately, it translates into lower die temperatures. -
CmdrShepard
The AI design has higher rate of heat transfer from heatsink to LN2, but the transfer rate from the CPU to heatsink hasn't improved almost at all according to real overclocked CPU test.bit_user said:Huh?
If you remove heat from the heatsink faster, then the heatsink maintains a steeper thermal gradient. That in turn allows a higher rate of heat transfer from the CPU into the heatsink. Ultimately, it translates into lower die temperatures.
I am not a physics expert, but I'd say it has something to do with small die surface limiting heat transfer ability from the CPU into the heatsink. If they tested with Xeon 4677 socket perhaps the results would have been better because of larger die surface. -
bit_user
Thank you for the clarification.CmdrShepard said:The AI design has higher rate of heat transfer from heatsink to LN2, but the transfer rate from the CPU to heatsink hasn't improved almost at all according to real overclocked CPU test.
Yes, I tend to agree.CmdrShepard said:I am not a physics expert, but I'd say it has something to do with small die surface limiting heat transfer ability from the CPU into the heatsink. If they tested with Xeon 4677 socket perhaps the results would have been better because of larger die surface. -
Wimpers
Yup, this is the equivalent of seeing how fast a supercar goes on a straight or oval, you only get those circumstances over there and after 15 mins you're out of fuel or your tires are spent.CmdrShepard said:That's a great example of pointless design "optimization".
Sure, you reach lower temperature faster, but you also heat up faster and heat transfer from the CPU to the base is unchanged so no actual improvement in performance.
No practical usage whatsoever, ever!
So this is neither interesting nor exiting... :cool: -
bit_user
That sounds to me like an indictment of oval racing, rather than building a winning race car. Given that oval racing (or, in this case, LN2 overclocking) exists, I think it's not pointless to try and gain an advantage by improving various aspects of the design.Wimpers said:Yup, this is the equivalent of seeing how fast a supercar goes on a straight or oval, you only get those circumstances over there and after 15 mins you're out of fuel or your tires are spent.
No practical usage whatsoever, ever!
I do wonder how knowable it was that their design improvement would have so little effect on die temperature without actually trying it. Maybe Intel has sophisticated thermal modelling packages which could've predicted the outcome of something like this, but that's probably not practical for the parties involved to have used such a package. I think a lot of what overclockers do is just trying stuff.
I think it's interesting that AI produced that design. It suggests the AI understood something about heat transfer, both within the base of the pot and at the interface with the LN2. I don't know if it's the AI's fault that it failed to address an apparent bottleneck at the die -> pot interface.Wimpers said:So this is neither interesting nor exiting... :cool: -
CmdrShepard You can't address that bottleneck without changing CPU die size. Even if you delid the CPU, the die surface is still way too small for dissipating 600W it consumes at that clock speed and core voltage.Reply -
bit_user
I mostly agree, but I can't help but wonder if it wouldn't have helped to make the bottom of the pot thinner or something. If you think about a vapor chamber, the base plate is pretty thin, because boiling off the working fluid has higher heat conductivity than even solid copper.CmdrShepard said:You can't address that bottleneck without changing CPU die size. Even if you delid the CPU, the die surface is still way too small for dissipating 600W it consumes at that clock speed and core voltage.
Also, I think there's probably some untapped potential for backside cooling.