Copper Conformal Coating Tech Allegedly Crushes Traditional Heatsinks in Efficiency
Researchers coated entire devices in poly and copper layers.
Heatsinks are a staple of PC cooling technology as we know it. Both passive and active coolers make use of heatspreaders and heatsinks, but a team of researchers from the University of Illinois at Urbana-Champaign and the University of California, Berkeley (UC Berkeley) recently found what looks like a far better, all-encompassing, and sleeker solution.
The researchers describe their experiments and findings in a paper entitled "High-efficiency cooling via the monolithic integration of copper on electronic devices," as spotted by Science Daily. Highlights of the new copper conformal coating technology are that it takes up little in the way of physical space in a device and that it is much more efficient than current copper heatsinks. The researchers demonstrated a 740% increase in the power per unit volume.
There are three main issues with conventional heatsinks, explained Tarek Gebrael, the lead author of the paper and a UIUC Ph.D. student in mechanical engineering. First, the most advanced heatsinks using exotic and highly efficient conducting materials can be expensive and difficult to scale up. Gebrael mentioned heatspreaders containing diamonds as one rival tech, clearly illustrating his point.
Secondly, conventional designs combine a heatspreader and heatsink in tandem, and "in many cases, most of the heat is generated underneath the electronic device," lamented Gebrael. Thirdly, the best heat spreaders can't be installed directly onto electronics but require a thermal interface material, inhibiting optimal performance.
So, how does the new technology address all the above drawbacks of current heat sinking methods? The new heatsink coating covers the entire device, creating a large cooling surface area.
"The approach first coats the devices with an electrical insulating layer of poly(2-chloro-p-xylylene) (parylene C) and then a conformal coating of copper," says the research paper. "This allows the copper to be in close proximity to the heat-generating elements, eliminating the need for thermal interface materials and providing improved cooling performance compared with existing technologies."
This coating technique does away with any large outcrops of copper or aluminum, so it is a much more compact solution to wick heat away from fast-running processors and memory. According to the researchers, the thin conformal coating and lack of a bulky traditional heatsink deliver a much higher power per unit volume, up to 740% better. "You can stack many more printed circuit boards in the same volume when you are using our coating, compared to if you are using conventional liquid- or air-cooled heat sinks," asserted Gebrael.
Get Tom's Hardware's best news and in-depth reviews, straight to your inbox.
The researchers next plan to verify the coating's durability, which is an important step to industry acceptance. Additionally, the researchers plan to test with immersion cooling and in high voltage environments. For their initial tests, the researchers used "simple" PCBs, but they hope to scale up testing of the cooling tech on hotter running electronics like "full-scale power modules and GPU cards."
In summary, the technology sounds promising without being too expensive or complicated for component makers to consider for practical use. Until this new heat sinking tech arrives, you will have to contend with conventional CPU cooling and GPU cooling.
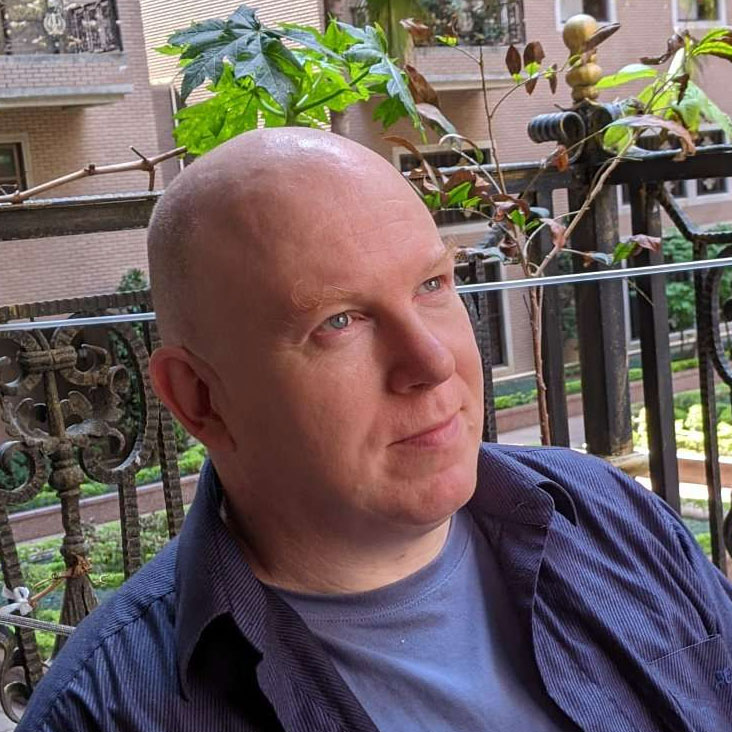
Mark Tyson is a news editor at Tom's Hardware. He enjoys covering the full breadth of PC tech; from business and semiconductor design to products approaching the edge of reason.
-
A Stoner Where does the heat go? That is always the limiting factor. When you have a heat sink, it increases area to air contact, the heat goes to the air. This can be increased by forced airflow over the surfaces. Here all you have for surface area is the component, which is a reduced surface from a heat spreader or a heat sink. You can increase the heat dissipation by running more air over it just like a heat sink.Reply -
Pytheus I see several problems with this. First being capacitance. Thin sheet of copper hanging closely over soldered components? Second being arcing currents from high voltage sources. Third, if you layer boards on top of this you're not dissipating the heat into the air then. Instead you're transferring heat between components which may cause issues with heat sensitive components. For example the value of a capacitor can change with applied heat. This may help with cooling certain components but also introduces other engineering challenges.Reply -
hotaru.hino I'm assuming this is all for consumer grade electronics.Reply
It wouldn't be any different than adding another ground plane on the PCB. If your electronic device is that sensitive to capacitance, it's probably not a consumer device anyway.Pytheus said:First being capacitance. Thin sheet of copper hanging closely over soldered components?
Breakdown voltages are typically in the kilovolt range. I don't know about you, but if my computer is generating kilovolts somewhere, I'd stay clear away from it.Pytheus said:Second being arcing currents from high voltage sources.
Which is why manufacturers design electronics based around an expected temperature range, along with some wiggle room. If you design your circuits to exact tolerances, your design sucks.Pytheus said:Third, if you layer boards on top of this you're not dissipating the heat into the air then. Instead you're transferring heat between components which may cause issues with heat sensitive components. For example the value of a capacitor can change with applied heat.
Also the PCB is already absorbing and distributing quite a bit of heat anyway through the aforementioned ground planes. -
Fates_Demise A Stoner said:Where does the heat go? That is always the limiting factor. When you have a heat sink, it increases area to air contact, the heat goes to the air. This can be increased by forced airflow over the surfaces. Here all you have for surface area is the component, which is a reduced surface from a heat spreader or a heat sink. You can increase the heat dissipation by running more air over it just like a heat sink.
Your not fully understanding the article, they are eliminating the solder, heat spreader and thermal paste and creating a direct contact heat transferring coating.
On top of that most heat is generated downward and this allows a full coating around the object rather than just on top.
This makes the thermal transfer much better.
Adding more air flow does not mean it will get better and better cooling, airflow has its limits, your contact transfer point is what is being improved here.
For example, if I had a component that was only 1 inch, and it generated 5000 watts of heat, I don't care what you do. You will never be able to cool that component with a current day air cooler setup.. even if you made a heat sink the size of a house, the object would still be overheating.
However if you somehow made a system that could pull heat off the object into the heatsink faster.... -
Sippincider hotaru.hino said:If you design your circuits to exact tolerances, your design sucks.
We won't mention a certain fruit-brand, running their processors with just enough cooling, so they hover just below thermal throttling, so they can just make base performance. All so it can be a fraction mm thinner.
Same company is probably salivating over this. -
TwoSpoons100 I see so many limitations with this. Clearly created by someone who has never designed a PCB. Ah yes - PhD in mechanical engineering. Willing to bet controlling that first insulating layer thickness will be a nightmare, meaning any boards with controlled impedance are out ( thats things like USB, or ethernet, or DDR memory).Reply
From a heat flow perspective this idea that heat is generated downward is nonsense - heat flows everywhere. And the cross-section of that copper coat must be pretty thin - which limits heat flow.
Frankly this is not much different to relying on the heat spreading ability of the PCBs second copper layer, which is often attached to by thermal vias.
TLDR limited usefulness, hardly revolutionary. -
dk382 Jesus, guys, it's a research study with more studies planned to explore many of the aspects you're all worried about. If we never explored the boundaries of what seems possible or practical, we'd never get anywhere.Reply -
Alvar "Miles" Udell This could work great in CPUs where the IHS is literally formed directly on top of the CPU instead of using Indium solder or even thermal paste, both of which have a fraction of the thermal conductivity of copper.Reply
It's not going to replace the actual heatsink in a desktop or laptop, or even server, though because of the very poor thermal conductivity of air. It needs that large surface area. Immersion cooling is a different story. -
Pytheus hotaru.hino said:It wouldn't be any different than adding another ground plane on the PCB. If your electronic device is that sensitive to capacitance, it's probably not a consumer device anyway.
At least with a ground plane you have a layer of substraight between the layers. This coating will presumably be right on top of the components. If it's truly grounded then it may not be a problem.
Breakdown voltages are typically in the kilovolt range. I don't know about you, but if my computer is generating kilovolts somewhere, I'd stay clear away from it.
Being is such close contact with components I don't think it would not take much to jump the gap. In the kilovolt range you could see the arc, that doesn't mean there aren't leakage currents your can't see in the low voltage range.
Which is why manufacturers design electronics based around an expected temperature range, along with some wiggle room. If you design your circuits to exact tolerances, your design sucks.
True, which is why I said this would add design challenges.
Also the PCB is already absorbing and distributing quite a bit of heat anyway through the aforementioned ground planes.
True, but like I said, there are insulating layers between the ground plane and components. The ground plane doesn't have near direct contact with the components. Its a difference of having your component on top of a hot stove or in the stove.