Intel Core i9-14900KS runs at all-core 6 GHz with direct die cooling - with headroom to spare
With great power comes great cooling.
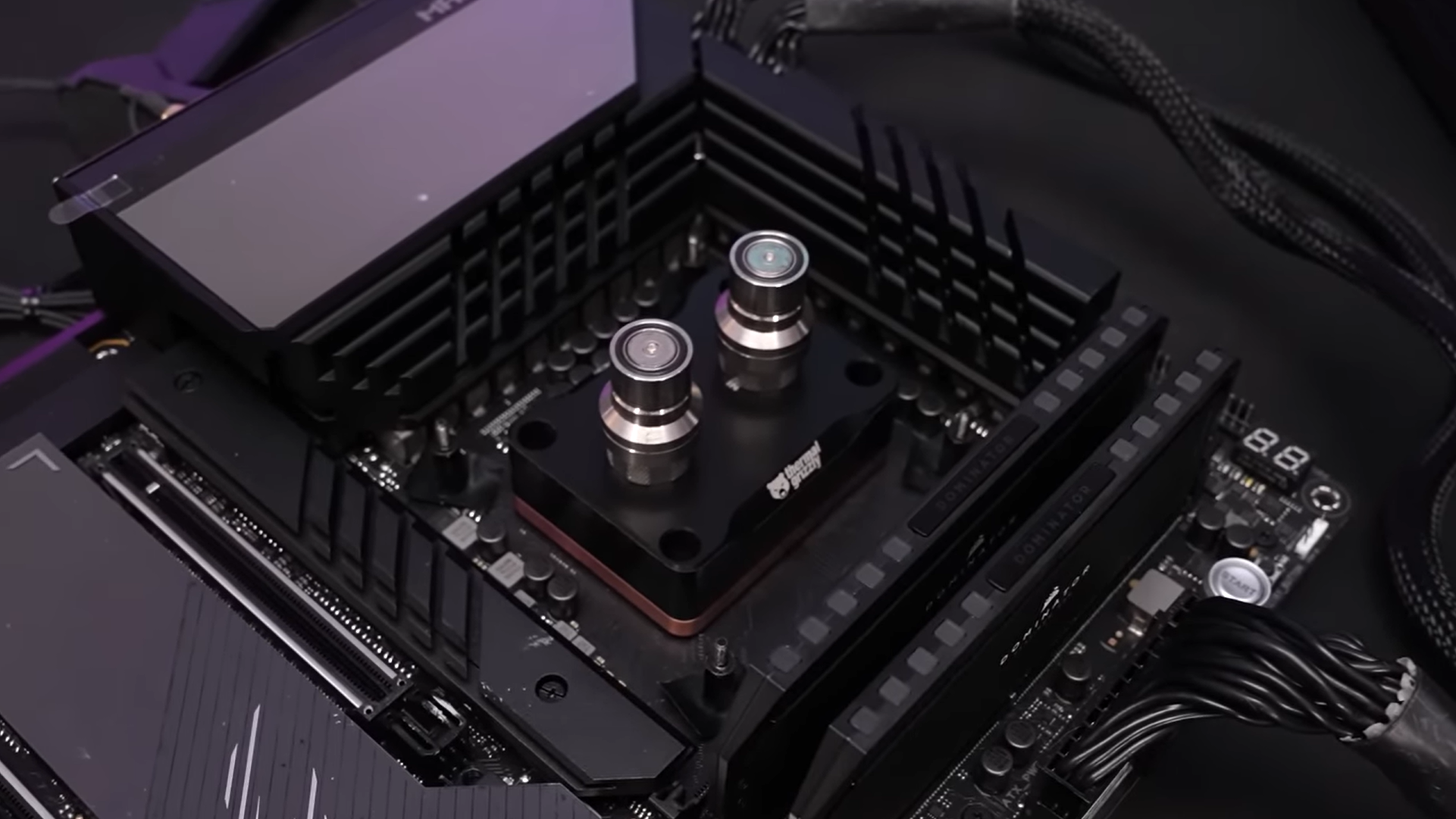
Overclocker and tech YouTuber Roman 'Der8auer' Hartung has demonstrated how direct die cooling can enable a 6 GHz overclock on all eight P-cores of an Intel Core i9-14900KS, without thermal throttling. Der8auer used a custom liquid cooling loop that relied on a delidded 14900KS, a CPU water block making direct contact with the CPU die, and liquid metal to get the processor so cool that even nearly 400 watts of power consumption wasn't an issue.
Although Intel's Special Edition Core i9-14900KS can hit its incredibly high clock speeds in part thanks to more selective binning, another part of the equation is the processor's power consumption. Its extreme power profile calls for 320 watts, much higher than the 253 watts the 14900K's extreme power profile is rated for. In our testing, we saw the 14900KS consume significantly more power than the 14900K, to the point where even a top-end 360mm AIO liquid cooler couldn't prevent thermal throttling.
Der8auer had a very similar experience and showed how performance tapered off over a long period of time with the Core i9-14900KS with a 5.8 GHz overclock on an AIO cooler. Only with a custom water cooler was consistent performance possible, but the overclocking specialist wanted to go further by putting his 14900KS under direct die cooling.
Normally, a CPU's die (the actual silicon chip itself) is under a metal heat spreader or IHS, and heat is transferred via a thermal interface material (TIM). Sometimes the TIM is a thermal paste, but the 14900KS uses indium. Removing the IHS and cooling the die directly can cool things down more directly. While direct die cooling may sound exotic, it is standard practice for GPUs and non-socketed CPUs such as those used in laptops.
Using an upcoming water block Der8auer developed with Thermal Grizzly, he demonstrated the process of delidding the 14900KS, scraping off leftover material from the IHS, and installing the CPU and water block onto the motherboard. This water block isn't all that different from one Der8auer showcased last year for Ryzen 7000 CPUs, which was also made in partnership with Thermal Grizzly.
With the original 5.8 GHz P-core overclock, the direct die liquid cooler dropped temperatures by more than 20 degrees Celsius. Power consumption also slightly decreased by 12 watts on average, as heat actually causes processors to consume more power even if clock speed hasn't changed. The extra cooling capacity from direct die cooling gave Der8auer enough headroom to hit 6 GHz on all P-cores while only hitting 95 degrees, just short of thermal throttling.
The Thermal Grizzly direct die CPU waterblock will have an MSRP of $99 according to Der8auer, and an RGB version with slightly better cooling performance will be available for "around $140." There isn't a precise launch date for either water block, but Der8auer says it will only be released when there's enough stock, which he hopes is in "about two to three weeks."
Get Tom's Hardware's best news and in-depth reviews, straight to your inbox.
Matthew Connatser is a freelancing writer for Tom's Hardware US. He writes articles about CPUs, GPUs, SSDs, and computers in general.
-
bit_user I often wonder how much direct-die cooling would benefit normal air coolers.Reply
On a related point, does anyone know if the efficiency of heat pipes drops, as you go past a certain number of Watts? Because that's about the only reason I can see why air coolers might not also benefit from this approach. -
taz-nz
With any modern heatpipe cooler, you need some form of heat spreader between the small CPU die and the heatpipes, otherwise only a couple of heatpipes would be in contract with the heat source and the rest would offer almost no cooling. There are some coolers that used a vapor chamber to spread heat evenly across heatpipes, but this gets complex and expensive to manufacture.bit_user said:I often wonder how much direct-die cooling would benefit normal air coolers.
On a related point, does anyone know if the efficiency of heat pipes drops, as you go past a certain number of Watts? Because that's about the only reason I can see why air coolers might not also benefit from this approach.
Yes you can stall a heatpipe if you exceed it's thermal capacity, but you have to force heat into the heatpipe faster than the rest of the heatsink can extract that heat from it for this to happen, so the CPU will normally thermal throttle long before this is possible.
But in extremely hot environments the heatsink can become so inefficient that whole heatsink becomes heat soaked and the body of the heatpipe raises to the point that all of it is above the boiling point of the working fluid, and the working fluid therefore stays in it's gaseous state, stalling the phase change heat cycle that make the heatpipe work, at this point the heatpipe is just a very inefficient shaped piece of copper. -
bit_user
Most air coolers do seem to have a base. I had bought into Cooler Master's "Direct Touch" pitch, but either they patented the heck out of it and refuse to license it to just about anyone else, or it's not such an advantage, even if you do have a heatspreader.taz-nz said:With any modern heatpipe cooler, you need some form of heat spreader between the small CPU die and the heatpipes, otherwise only a couple of heatpipes would be in contract with the heat source and the rest would offer almost no cooling.
Yes, and this is what high-end GPUs do. Also, server heatsinks.taz-nz said:There are some coolers that used a vapor chamber to spread heat evenly across heatpipes,
Yes, good point. I think/hope we're not talking about such an extreme situation.taz-nz said:the body of the heatpipe raises to the point that all of it is above the boiling point of the working fluid,
Do you know what the boiling point typically is, for PC heatsink heat pipes? It seems like there should be a nonlinear bump in cooling efficiency, as you cross this threshold. If one did a careful test of power vs. temperature, there should be a distinct uptick, especially on coolers with just a couple heat pipes. -
taz-nz bit_user said:Most air coolers do seem to have a base. I had bought into Cooler Master's "Direct Touch" pitch, but either they patented the heck out of it and refuse to license it to just about anyone else, or it's not such an advantage, even if you do have a heatspreader.
The Coolermaster direct touch relies on the CPUs IHS to spread the heat across the heatpipes, but the IHS isn't the ideal thickness to spread the heat efficiently, so the direct touch heatsink preforms worse if mounted with the heatpipes mounted parallel with the die vs across the die. The uneven surface would destroy a CPU in direct die application.
bit_user said:Yes, and this is what high-end GPUs do. Also, server heatsinks.
Cooler master did it on their V8 series of desktop coolers, but they cost as much as a cheap 240 AIO, with worse performance. Vapor chambers are most commonly used where space and form factor matter more than cost.
bit_user said:Yes, good point. I think/hope we're not talking about such an extreme situation.
Some case setups are so bad that the temperature in the case is 20degC about the ambient air temp, add dust clogged heatsinks and vents and you can get into the extreme end of things fast, that's how people cook their PCs.
bit_user said:Do you know what the boiling point typically is, for PC heatsink heat pipes? It seems like there should be a nonlinear bump in cooling efficiency, as you cross this threshold. If one did a careful test of power vs. temperature, there should be a distinct uptick, especially on coolers with just a couple heat pipes.
It's tuned by the manufacture, the working fluid is typically distilled water or alcohol or a mix of the two, sealed under a part vacuum to lower the boiling point, the fluid mix and the vacuum pressure can be changed to tune the boiling point to the desired operating temperature. It one of those trade secrets, but it's probably in the 30-40 deg range, with the heatsink relying on standard conduction at lower loads. -
bit_user
Yes, one possible explanation I considered.taz-nz said:The Coolermaster direct touch relies on the CPUs IHS to spread the heat across the heatpipes, but the IHS isn't the ideal thickness to spread the heat efficiently,
Agreed.taz-nz said:so the direct touch heatsink preforms worse if mounted with the heatpipes mounted parallel with the die vs across the die. The uneven surface would destroy a CPU in direct die application.
Someone also made a 3D vapor chamber with 2x 120 mm fans side-by-side. I forget the name, but I recall it weighs a ton.taz-nz said:Cooler master did it on their V8 series of desktop coolers, but they cost as much as a cheap 240 AIO, with worse performance.
Windows don't help, either. It's too bad anodized aluminum is no longer trendy. I have a set of Lian Li windowless aluminum cases (with dust filters) I'll probably keep as long as I continue building my own PCs.taz-nz said:Some case setups are so bad that the temperature in the case is 20degC about the ambient air temp, add dust clogged heatsinks and vents and you can get into the extreme end of things fast, that's how people cook their PCs.
It would have to be far enough above ambient that you'd always be able to condense it with heated case air. So, my bet would be in the realm of 50 - 60 degrees C, in order to avoid the breakdown scenario you outlined, where the fluid converts fully to gas. That said, the more of it boils, the higher the vapor pressure and thus the boiling point should rise - perhaps not by much, but it should give some range between when the heatpipe starts to work efficiently and when it stops.taz-nz said:it's probably in the 30-40 deg range, with the heatsink relying on standard conduction at lower loads. -
das_stig Dropping 20c shows how inefficient todays IHA and TIM used by manufacturers are and they need to improve there development.Reply -
TerryLaze
Intel can't sell these as 6Ghz all core though because not all of them will be able to do that, their cooling is focused on the actual product that they can produce and sell and not on an extreme overclock that might be stable enough, or might not be.das_stig said:Dropping 20c shows how inefficient todays IHA and TIM used by manufacturers are and they need to improve there development. -
thestryker The delidded temperature drops are why I wish Intel/AMD would be willing to sell a line of CPUs without IHS. While I wouldn't use liquid metal personally a phase change pad or one of the graphene pads should still get most of the advantage. All of the delids Roman has done show a bit of power consumption reduction on top of the temp for both Intel and AMD CPUs.Reply
EK has a direct die AIO which has a pretty big benefit over using an AIO with IHS so it isn't limited to just custom loops. It would be really interesting to see if an air cooler with a vapor chamber would have similar benefits. -
taz-nz
A lot of the temperature difference is caused by number of different materials layers the heat has to traverse and the total thickness of those layers combined.das_stig said:Dropping 20c shows how inefficient todays IHA and TIM used by manufacturers are and they need to improve there development.
In stock config the heat conducts through:
The silicon of the die.
The indium solder.
The copper IHS. (I'll ignore the super thin nickel plating)
The thermal interface material.
The copper of the water block
To reach the water to be conducted away.
Delidded in a direct die water block config, the heat conducts through:
The silicon of the die.
The liquid metal thermal interface material
The copper of water block.
To reach the water to be conducted away.
But that's not all, the thinner each layer is the less thermal resistance there is, so while liquid metal thermal paste is slightly less conductive than indium solder, the layer is much thinner so allows more heat transfer, the copper of a direct die water block can also be thinner, as it doesn't need to resist the bending force cause by mounting pressure required in stock config.
There is very little CPU manufactures can do to improve the thermal transfer of the stock config, without going back to naked dies like we had in the late 90s early 2000s, when people would chip or shatter their CPU die installing a heatsink. -
Amdlova Direct touch heat pipes its a nightmare...Reply
Need to put a whole thermal paste tube to fill the gaps and heights of the base.
I see some people making cooper pipes with acetone start boil at 50°c and goes critical at 250°c
(long time ago need to remove the ihs from a atlhon x2 with stock cooler have drooped almost 20°c.)