Tom's Hardware Verdict
The Prusa SL1S Speed creates high-quality resin 3D prints at lightning-fast speeds, but the high cost may turn away some users.
Pros
- +
+ Native integration with PrusaSlicer app
- +
+ Unique tilting mechanism enables rapid printing
- +
+ Easy build platform leveling
- +
+ Color touchscreen LCD offers guided setup
Cons
- -
Pricey
- -
Resin vat sensor is very sensitive to overfill
Why you can trust Tom's Hardware
The $1,999 Prusa SL1S resin MSLA 3D printer is one of the priciest resin 3D printers in the consumer/prosumer market, and after spending some time printing with it, I understand exactly where all of that money goes. The SL1S uses a tilting resin vat and a monochrome LCD to achieve print speeds of under 2 seconds per layer while not sacrificing quality on printed parts. Prusa has developed an entire ecosystem for this machine, including the PrusaSlicer software for preparing models and Prusament Resin for achieving best results when printing. One of the best 3D printers, this machine impressed and surprised throughout the testing process.
The SL1S has a clear target market of prosumers and businesses that are interested in being able to rapidly create models without troubleshooting, fiddling with software, or going back and forth with a support team. The $1,999 price tag puts this machine out of reach for many home users, but there are plenty of other machines like the Elegoo Mars 3 that exist at a lower price point.
Prusa SL1S Specifications
Machine Footprint | 8.8" x 9.3" x 15.7" (22.5cm x 23.7cm x 40.0cm) |
Build Volume | 5" x 3.15" x 5.91" (127mm x 80mm x 150mm) |
Resin | DLP Photopolymer Resin |
Exposure Time | 1.3 - 2.4 seconds per layer |
UV Light | Custom Designed 405nm UV LED Panel |
Supported Layer Heights | 0.025mm - 0.1mm |
Masking LCD Resolution | 2560 x 1620 |
Masking LCD Size | 5.96-inch |
Interface | 4-inch LCD Touchscreen |
XY Axis Resolution | .049mm |
Included in the Box of Prusa SL1S
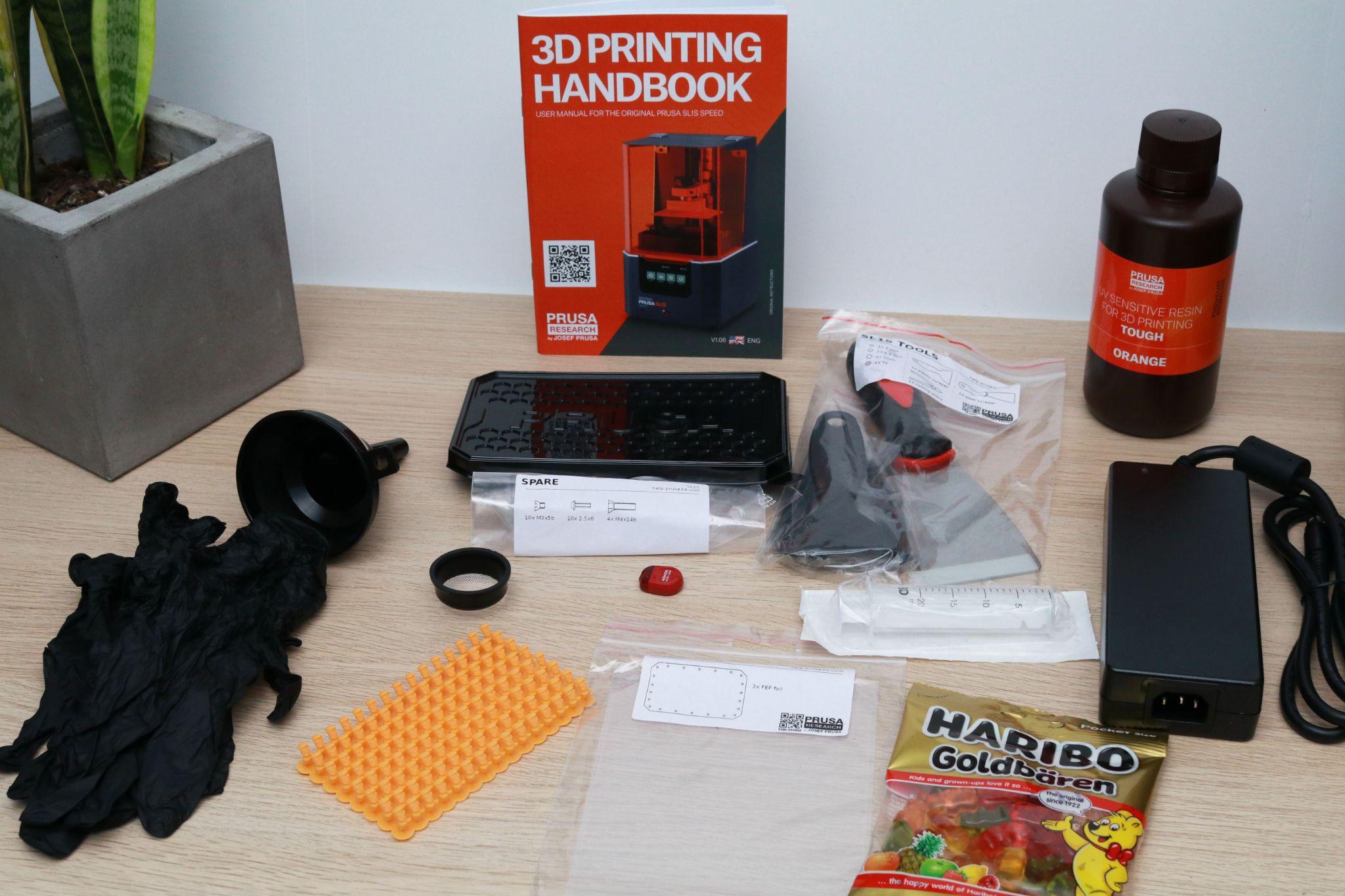
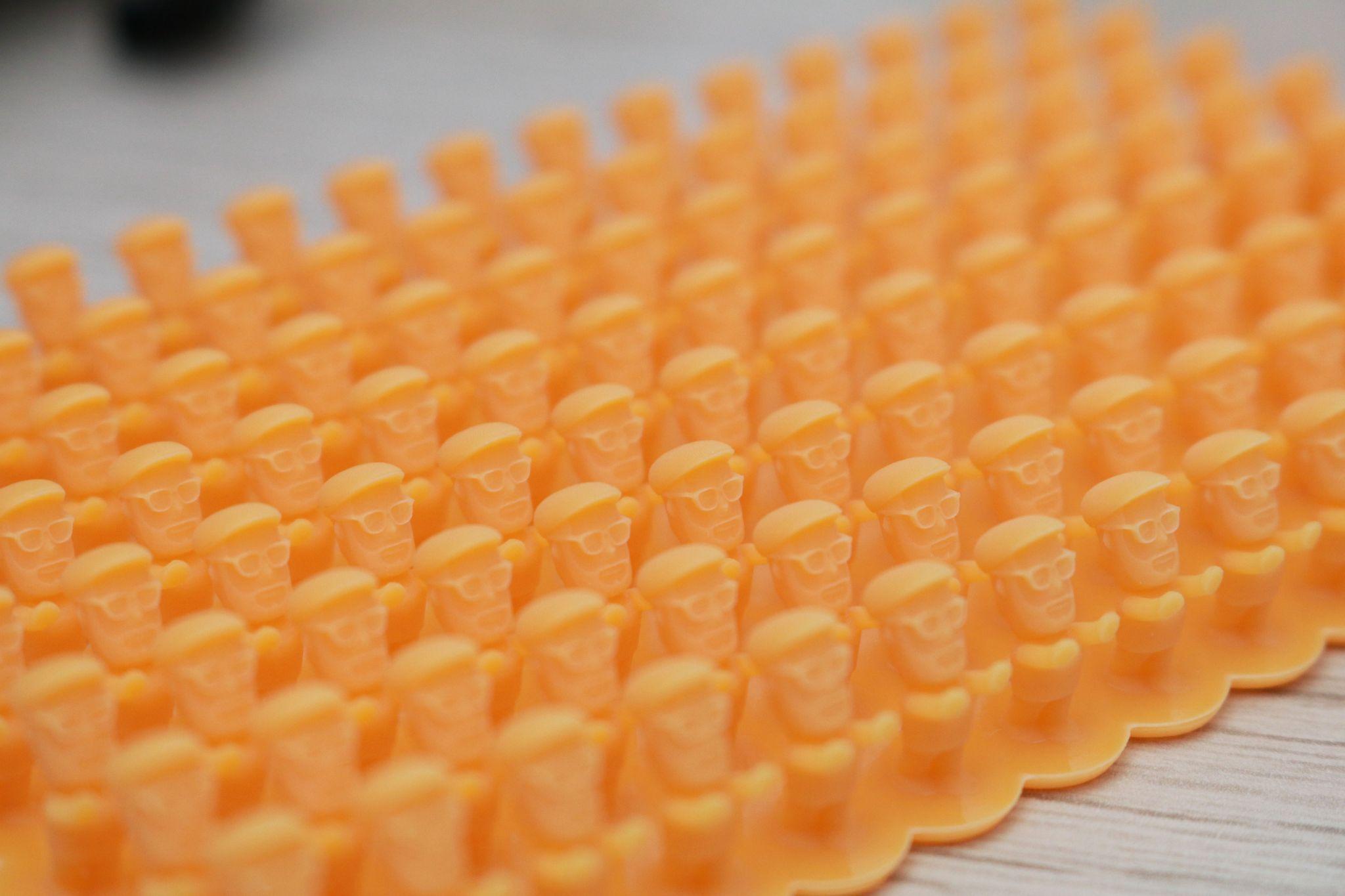
The Prusa SL1S ships with everything you need to start printing, including a 500 gram bottle of Prusa’s Orange Tough resin. Included in the accessories kit is a set of gloves, a funnel with a filter, a cover for the resin vat, a small syringe, some extra FEP film, a pair of scrapers, a bag of Haribo Goldbears (a staple for all Prusa printers), and a validation print to confirm the functionality of the printer. This print is a grid of tiny replicas of Josef Prusa himself, with a total of 120 tiny models that were all printed simultaneously.
As you would expect from a machine from Prusa, the included documentation is best-in-class and contains detailed diagrams and instructions for getting the printer up and running. Everything from how to unbox the printer to troubleshooting problems is covered in the 68 page user manual, and it should be required reading for any manufacturer currently making 3D printers.
Design of Prusa SL1S
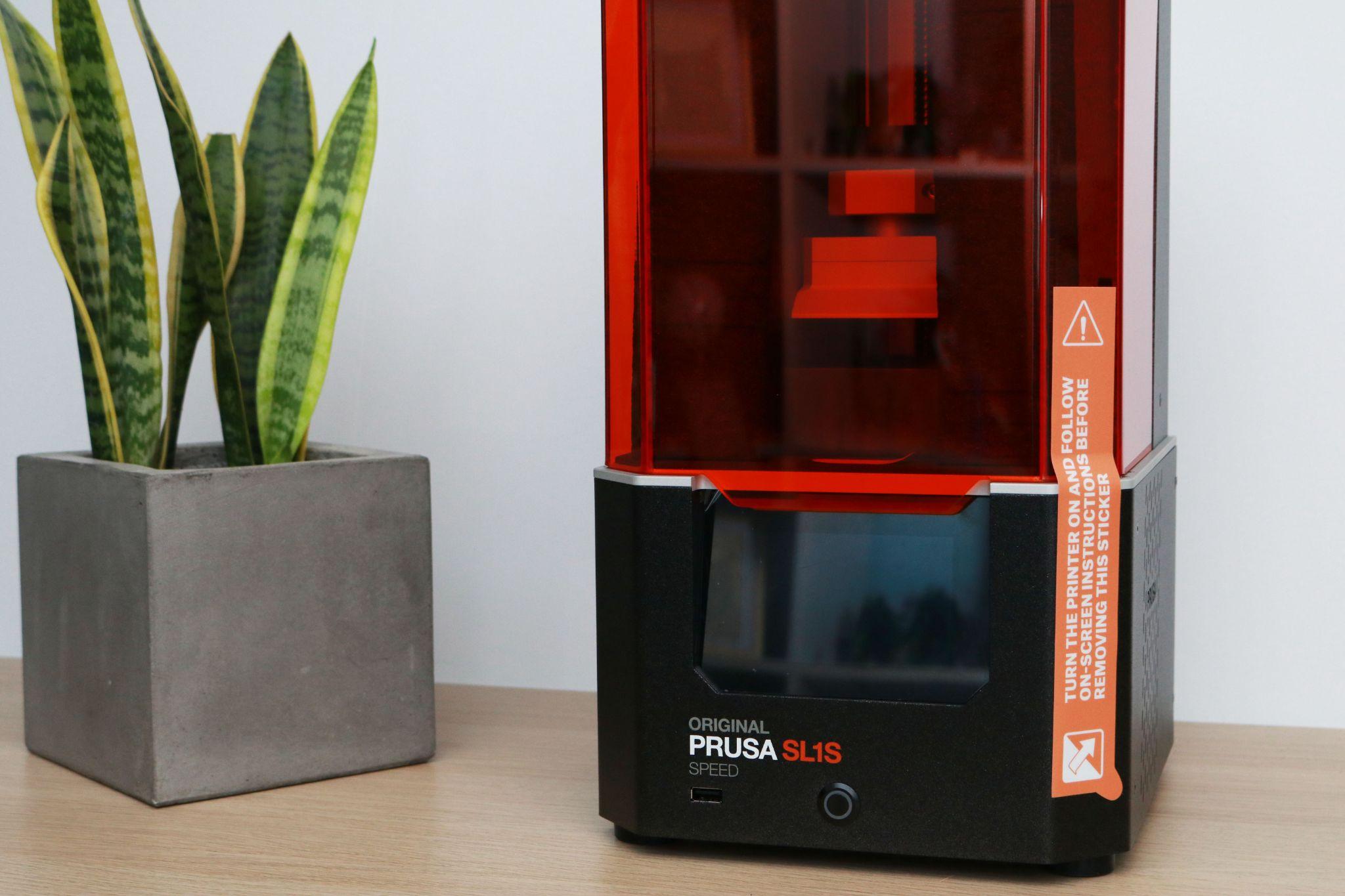
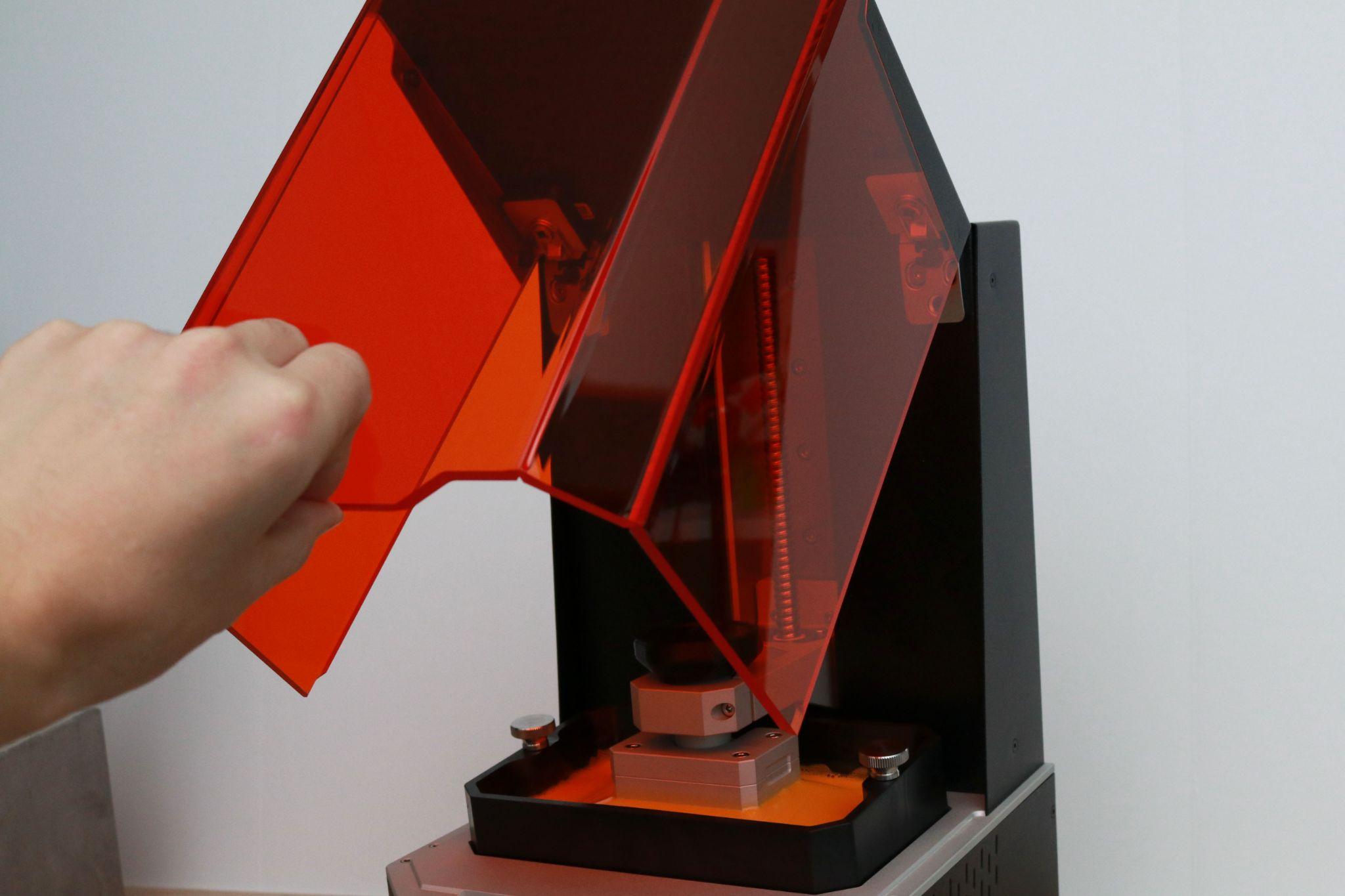
The Prusa SL1S is a familiar sight for most users of resin 3D printers; an orange UV lid perched atop a black metal base. Upon closer inspection, some of the unique design elements of the SL1S become more apparent. For one, the lid of the SL1S doesn’t lift off like the lid of the Elegoo Saturn or the Anycubic Photon Mono; the hinges on the top of the printer allow it to lift up and back without needing to be removed from the machine. This small touch means the printer can be opened without needing to remove the lid and finding a place to set it down; something anyone with a busy work area will no doubt appreciate.
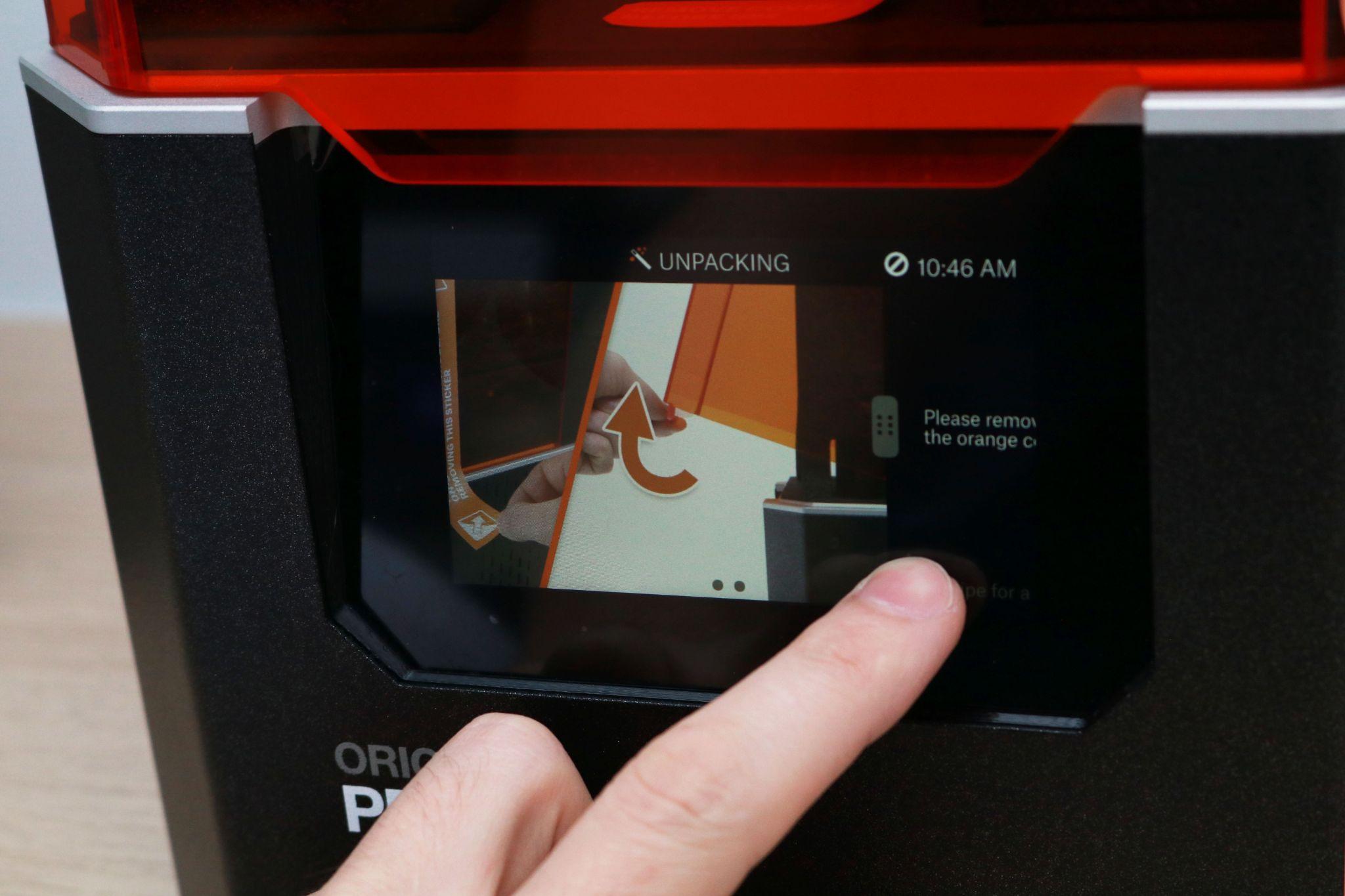
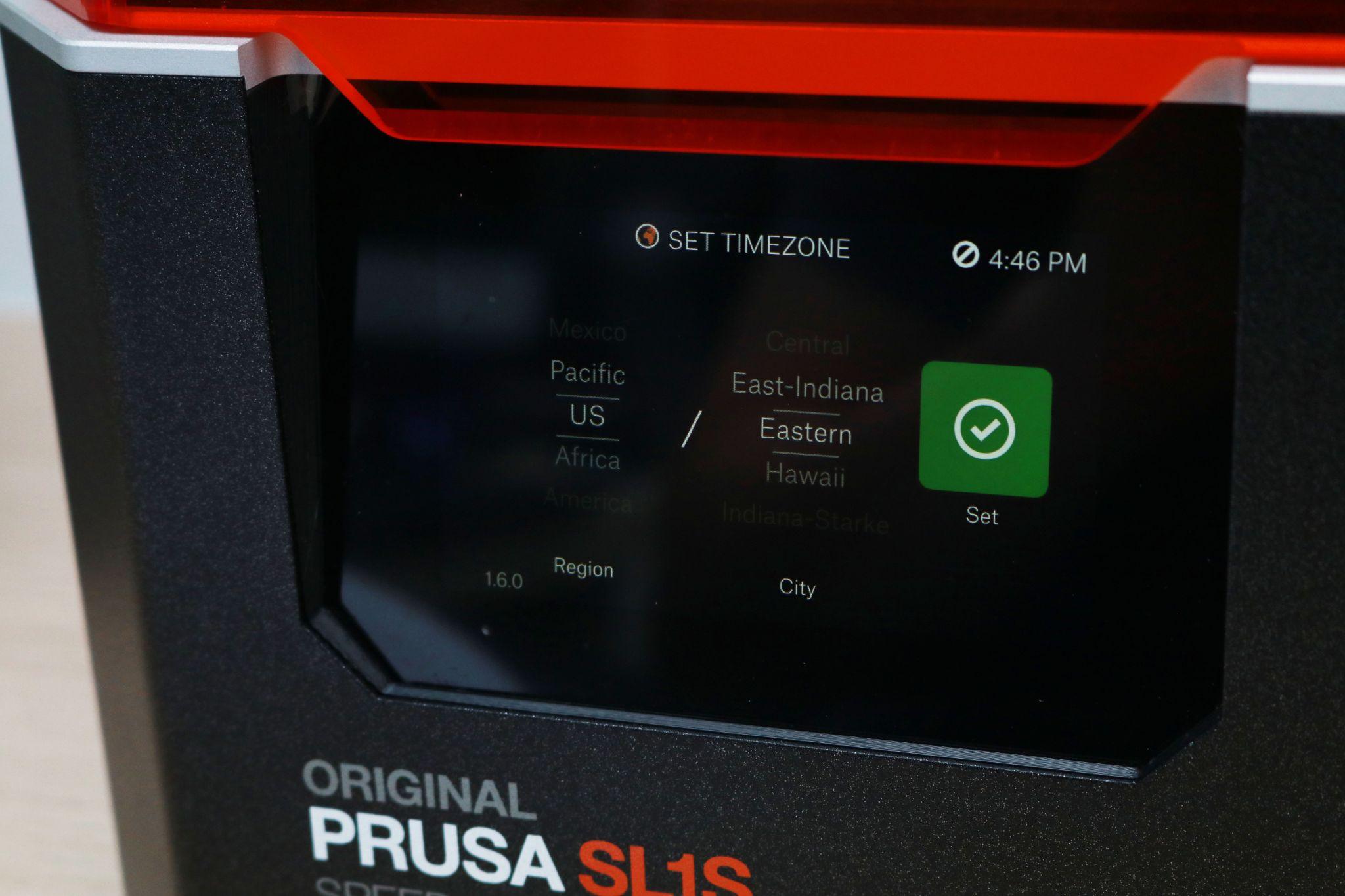
The 4-inch color touchscreen LCD interface offers a guided setup for the machine, including detailed instructions on how to calibrate the build platform. At each step of the setup, the user can swipe the screen to the right, which reveals full-color pictures detailing the process. This is an invaluable step for new users, and the additional value of this detailed user guide will result in a printer that has far fewer issues due to an improper or incomplete setup process. In fact, shortly after turning the machine on and connecting to Wi-Fi, I was prompted to update the firmware, which the printer was able to automatically download and install.
Unlike most other resin MSLA 3D printers, the SL1S uses a unique mechanism for delaminating the part from the FEP film during printing. Most resin printers like the Elegoo Mars 3 lift the part directly up from the FEP film, delaminating it in a single movement. The SLS1 uses a tilt mechanism instead, tilting the resin vat down towards the front of the printer, which causes the printed part to peel incrementally from the film. This peeling motion allows for a rapid transition between layers, due to the lack of a need to raise and lower the Z axis after each individual layer.
Get Tom's Hardware's best news and in-depth reviews, straight to your inbox.
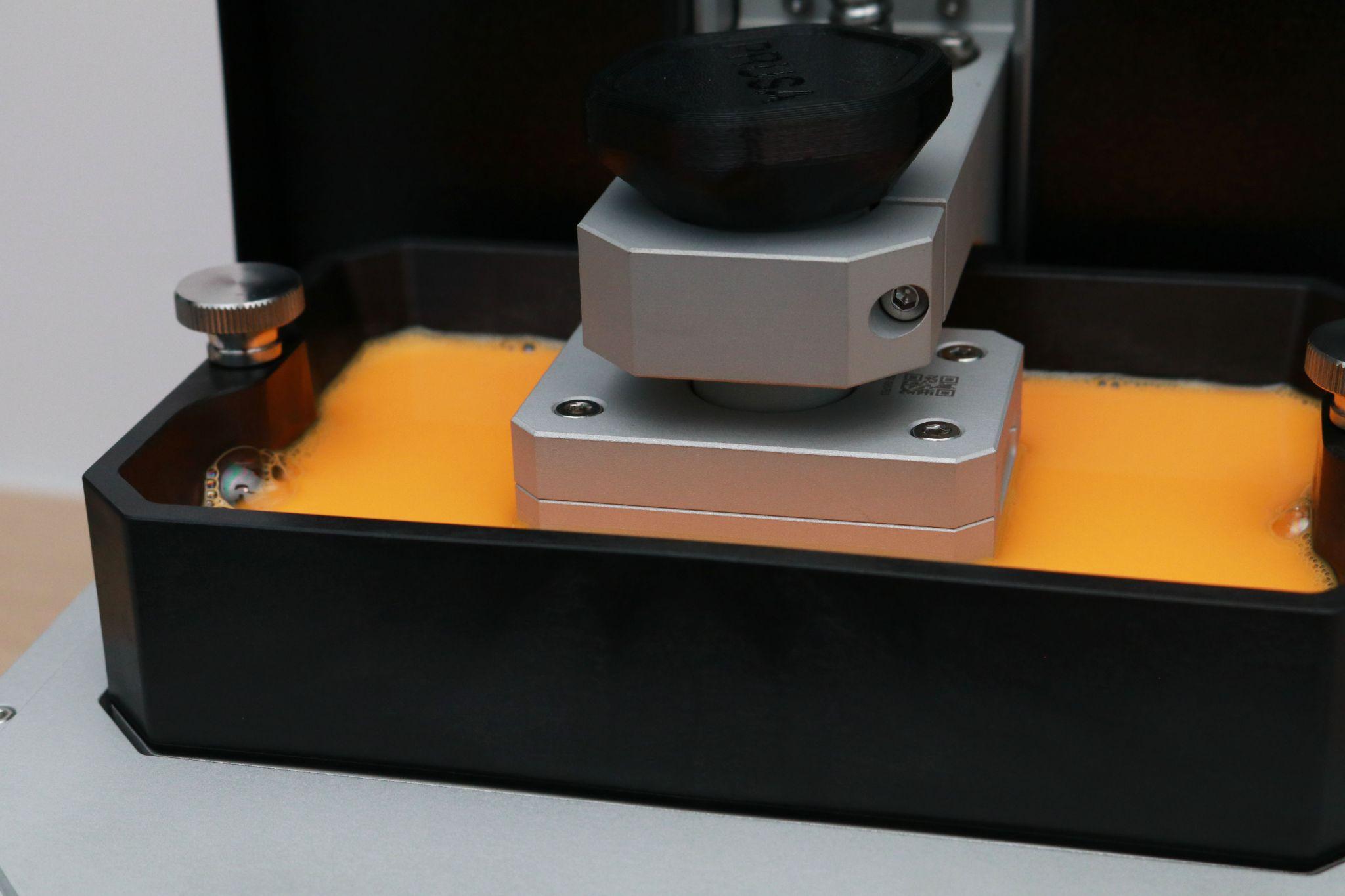
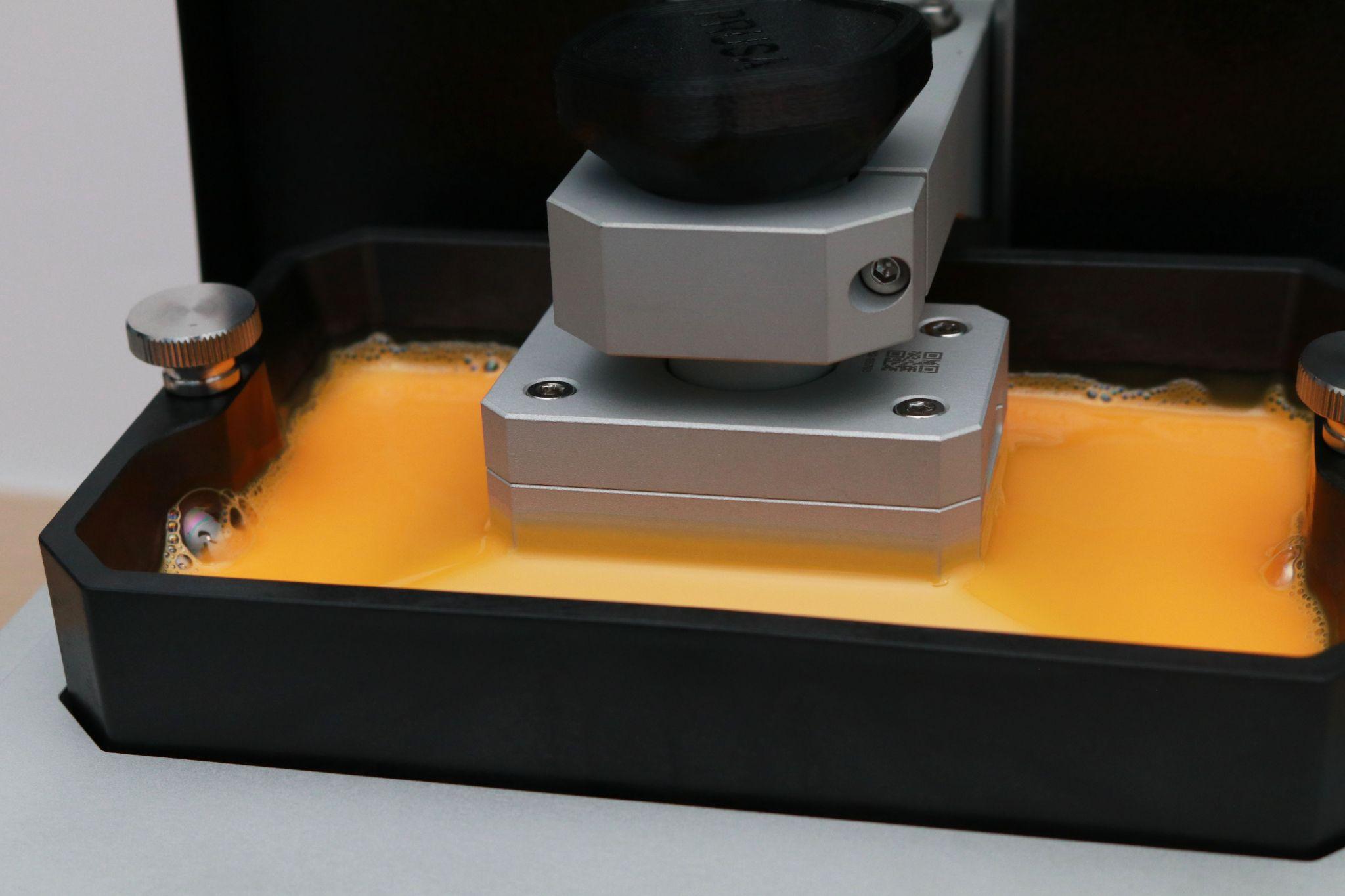
The build platform is designed with a tapered top, so resin can drip off during printing instead of pooling on the top. The platform has a slight, uniform texture that feels like bead-blasted aluminum, and the one-piece nature of the platform means cleaning after printing is a very easy process. Unlike the build platform on printers like the Anycubic Mono X, there are no nooks or crevices where uncured resin can get trapped and be difficult to clear out.
The overall build volume of the SL1S is on the small side for an MSLA resin 3D printer, measuring 5" x 3.15" x 5.91" (127mm x 80mm x 150mm). It’s clear from the name of the printer (Prusa SL1S Speed) that this machine has been designed for fast printing and not necessarily large format prints.
In addition to the FEP film already attached to the resin vat, Prusa has included three additional extra FEP film sheets to use as a replacement when the original becomes deformed or perforated. The resin vat itself has markings denoting 35%, 70%, and 100% volume. Because of the tilting mechanism of the vat, the 100% volume mark is relatively low on the vat and only allows for 200ml of resin to be filled at a time.
This was the only recurring issue I had with the machine; I consistently had overfill errors when starting a print, even when it looked like the resin was under the 100% line. Even at the 100% line, I would get a message stating the vat had 220ml or 240ml of resin in it, and I then had to extract some of the resin from the vat.
The SL1S has a fill sensor to detect when the resin vat is running low, which I used to refill the vat after the resin ran too low. I also had a minor issue with the vat itself; it feels like a glass or fiber-filled polymer material, as opposed to the machined metal vat included with Elegoo Mars 2 Pro, which feels much more substantial. This may be due to the reduced weight being easier on the tilt motor, but it does result in a vat that feels a bit more delicate.
Prusa refers to the Z-axis assembly as the ‘Tower’, and it uses a ball screw linear actuator for Z-axis movement. The build platform is suspended from this axis on a solid aluminum cantilever bracket, which feels solid and doesn’t have any noticeable play or wiggle during printing.
One of the first things I noticed about the SL1S was the number of 3D printed parts on the printer. Everything from the brackets on the hinge to the knob that locks in the build platform have been 3D printed with an FDM machine, and more parts on the inside of the machine appear to have been printed as well. The CW1S Cure/Wash station also has a 3D printed knob and other 3D printed parts across the machine.
These parts indicate that Prusa has embraced some of the core strengths of additive manufacturing, including printing high-complexity, low-volume parts for production. The printed knob on the build platform works just as well as an injection molded or machined knob would function, and there was no tooling or setup required for manufacturing, just directly printing the part on an FDM 3D printer.
Leveling the Build Platform on Prusa SL1S
Considering the high level of automation on the Prusa SL1S, it should come as no surprise that the build platform leveling process is nearly completely automated, only requiring a single bolt be loosened and then tightened. The SL1S uses an automated wizard that guides the user through the calibration process, and it only takes a few minutes to complete. After loosening the bolt that holds the build platform tight against the gantry, the SL1S drops the platform onto the FEP film of the vat, holding it flat while the user re-tightens the bolt.
Compared to the four bolt process used by printers like the Anycubic Photon Mono, this is fast, reliable, easy, and doesn’t require the same “feel” for pulling a piece of paper between the platform and the LCD. This is a very subjective process that can be difficult for new users, and the SL1S instead opts for a calibration workflow that has a higher level of automation with a lower chance of failure. The obvious trade-off is cost; the Photon Mono costs $199 and contains only a single sensor (Z-axis endstop), while the Prusa SL1S is 10x the price and contains a multiple sensors for everything from the UV lid to the weight sensor used to detect the amount of resin left.
Printing Safety with Prusa SL1S
The Prusa SL1S uses 405nm UV resin, a material that you need to handle safely when in an uncured state to avoid injury. The resin can be harmful when making contact with skin, so make sure to wear gloves when pouring, cleaning up, or handling uncured resin. I also make sure I’m wearing gloves when removing the build platform after a print, as the resin tends to pool on top of the platform and can drip off while the platform is being removed.
Make sure you use the SL1S in a well-ventilated room to minimize the danger from inhaling fumes. Any spills or uncured resin stuck to a surface should be cleaned using 99% isopropyl alcohol and the container for the resin should be kept closed and secured when not actively pouring material.
Printing the Included Test Prints on Prusa SL1S
Test prints are frequently bundled with 3D printers as a fast and easy way to validate the functionality of the machine while also giving users a chance to experience normal operation. Some manufacturers treat this as an afterthought, such as the 19-hour test print included with the Creality LD-002R, a nerve-wracking marathon for anyone who wants to see the printing process in its entirety.
The Prusa SL1S includes a test print of Josef Prusa (of course) and a hexagon that contains a multitude of features that can be used for showcasing the strengths of the printer. While the Josef model is printed solid, the hexagon features a honeycomb pattern as well as posts and holes that measure all the way down to 20 microns. These fine features demonstrate the strengths of a resin printer like the SL1S, while also having a reasonable 1 hour print time.
Washing and Curing Models with Prusa CW1S
Most of the mess typically associated with resin printing occurs in the post-processing stage, where the printed model needs to be removed from the printer, rinsed of excess resin, washed in a solvent bath to remove uncured resin, and fully polymerized in a curing chamber. This process involves multiple steps and typically requires several other machines to accomplish.
To make this an easier process for the user, Prusa has designed the Prusa CW1S, an optional accessory for the machine that combines these steps (and more) into a single unit capable of reducing the amount of time spent post-processing resin parts. Retailing for $749, this is not a cheap accessory; it costs a lot more than some other resin printers such as the Elegoo Mars 2 Pro. If you are interested in a fast workflow with a reliable machine, it’s worth investigating the CW1S to understand the benefits it can bring to your workflow.
To understand how the CW1S works, I’ll walk you through a typical workflow process for finishing a resin print. The build platform on the SL1S is easy to remove from the machine, and the tapered edges allow resin to flow off making the clean-up easy, so carefully removing the platform from the bracket can be done without spilling a single drop of resin. I usually let it sit for a while after printing to allow the model to drip-dry.
After removing the build platform, the next step is removing the part. This is typically done with the sharp metal scraper included with the printer, and can be accomplished by finding a corner, or edge, and lightly separating the model from the platform. It’s possible some resin that is stuck to the model might drip off, so you’ll want to lay down a silicone mat or other easy-to-clean surface under the platform.
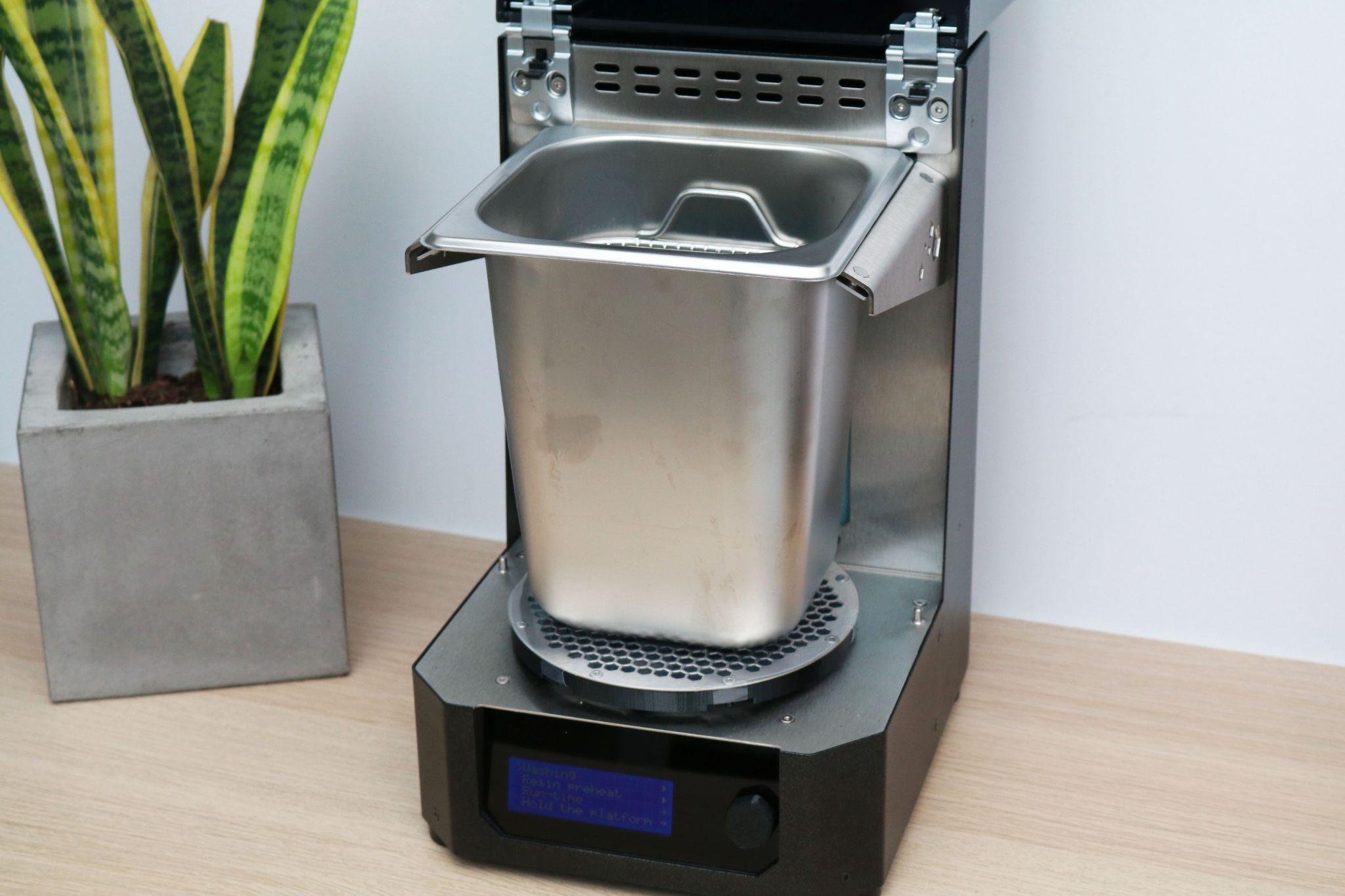
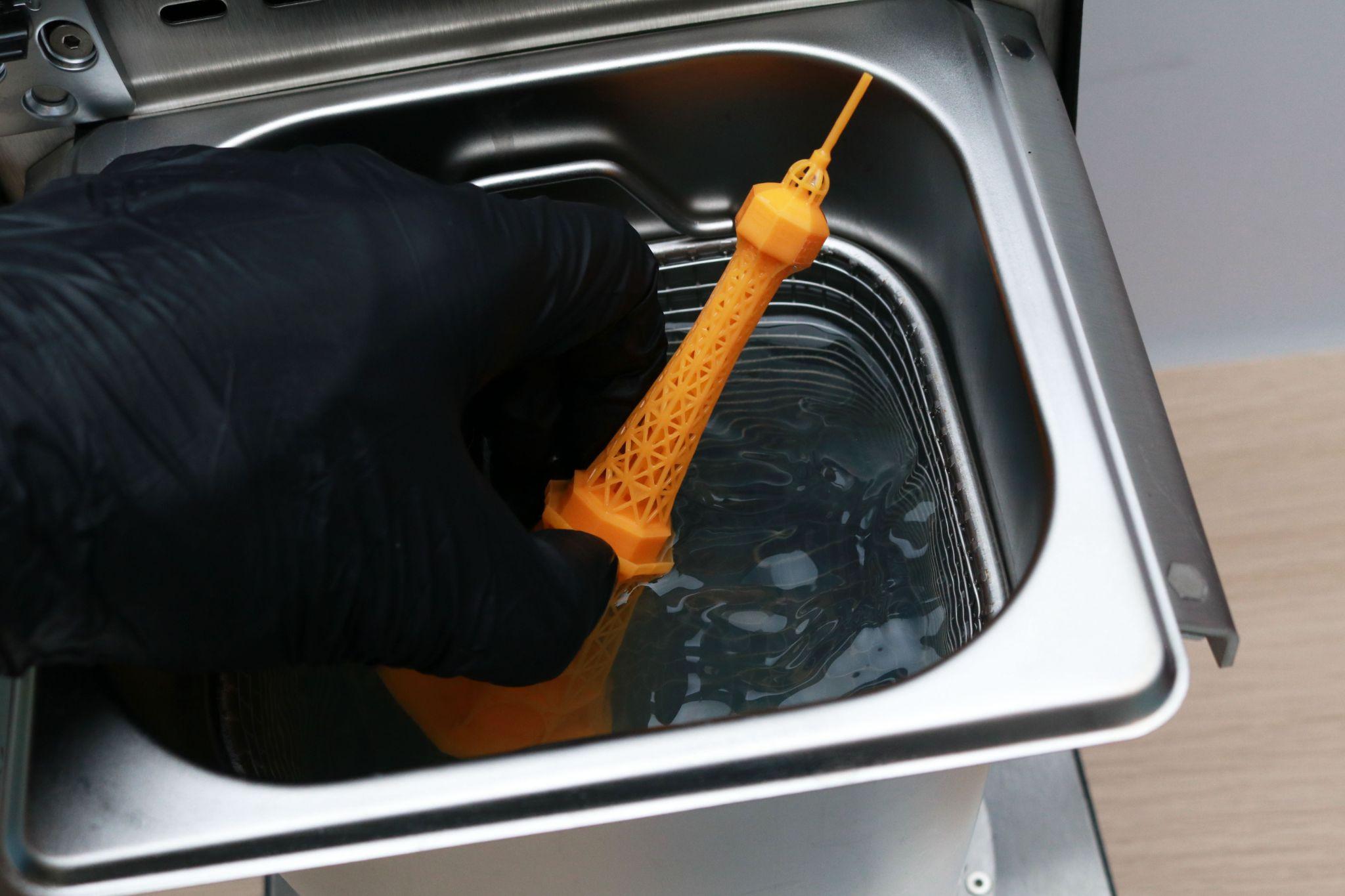
The CW1S includes a metal vat with a wire mesh basket that is used to rinse the excess resin from the part. Underneath the vat is a spinning magnetic platform that propels a plastic agitator at the bottom of the vat. This agitator creates a vortex of solvent which actively rinses excess resin from the model. For models like this tower, there are lots of small windows that can have resin stuck to them due to the surface tension of the material. By vigorously rinsing the model, this excess resin is cleared from all areas of the model.
The screen on the front of the CW1S includes an interface that automatically walks the user through the steps of post-processing. Once the washing phase is finished, I remove the part from the tub and allow it to air dry before putting it back in the CW1S. One of the unique features of the CW1S is the ‘Drying’ phase, which blows hot air over the model to speed up the evaporation of any trapped or stuck solvent.
The interface will prompt you to start the drying phase, and automatically begins the curing phase once it’s finished. The UV-resistant lid of the CW1S means the only light leakage is on the sides of the machine, through which a slightly purple glow can be seen. Once the UV curing phase is complete the model is fully polymerized and the post-processing phase is complete.
Once the processing is finished, we can take a look at the model to get a better idea of what we have accomplished through these steps. The fine lattice structure of this model is readily visible with no filled cells or holes, and there is no excess resin on the edges of the model. The beams on this model measure 0.4mm, and there is no warping, deformation, or incomplete areas on the model. Printing a model with this much detail is an accomplishment on its own, but the extra detail that is brought out in the post-processing phase helps highlight the value of a post-processing machine like the CW1S.
Preparing Files for Printing with PrusaSlicer
PrusaSlicer is a feature-rich slicer app for FDM 3D printers, developed by Prusa and compatible with a large number of filament 3D printers including the company’s own Prusa MK3S+. In addition to this functionality, PrusaSlicer is also compatible with the MSLA resin Prusa SL1S and contains just as many features as you would expect from the Prusa team. Using the PrusaSlicer software, you are able to load and fix 3D models, hollow them, add drain holes, split the model into parts, and even manually add a support structure.
These settings are laid out in a way that is approachable without being overwhelming, with a ‘Simple’ view providing the basic information needed to prepare a file, while the ‘Expert’ mode unlocks full control in the slicer. I went through the typical workflow process (hollow, drain, support) and prepared the MadCat Mk2 Mech model by Matt Mason for the SL1S. This process was straight-forwad and laid out in a linear fashion in the software, so it only took a few minutes to complete.
The typical approach to preparing a part for MSLA resin printing is angling the model to reduce cross-sectional width. This creates smaller layers that are easier to delaminate from the delicate FEP film and don’t have the suction associated with a large flat block being pulled straight-up. Interestingly enough, the tilt function on the SL1S means it’s completely possible to print large blocky objects that have dense layers due to the gradual peeling of the FEP from the part, instead of the other way around.
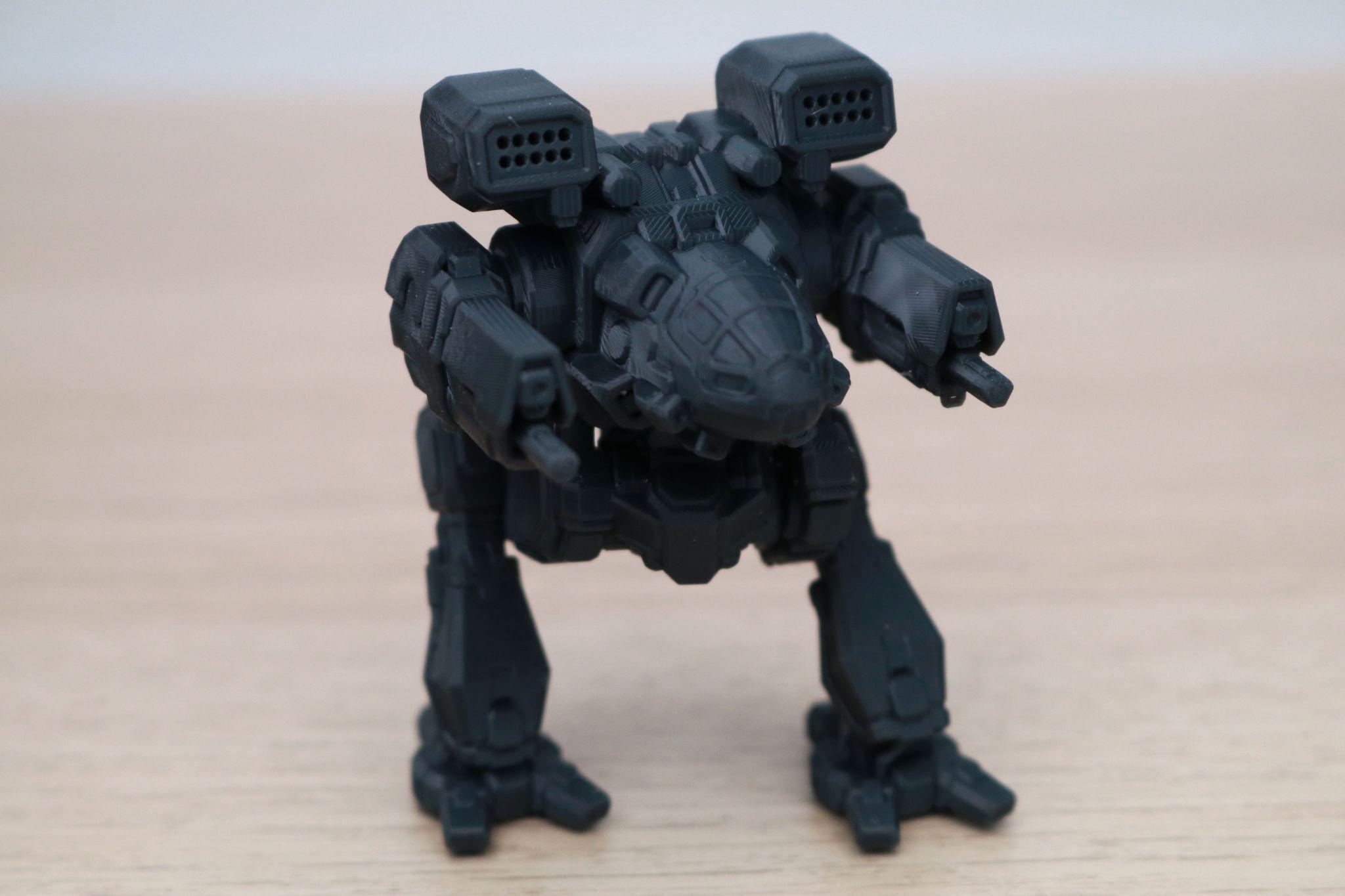
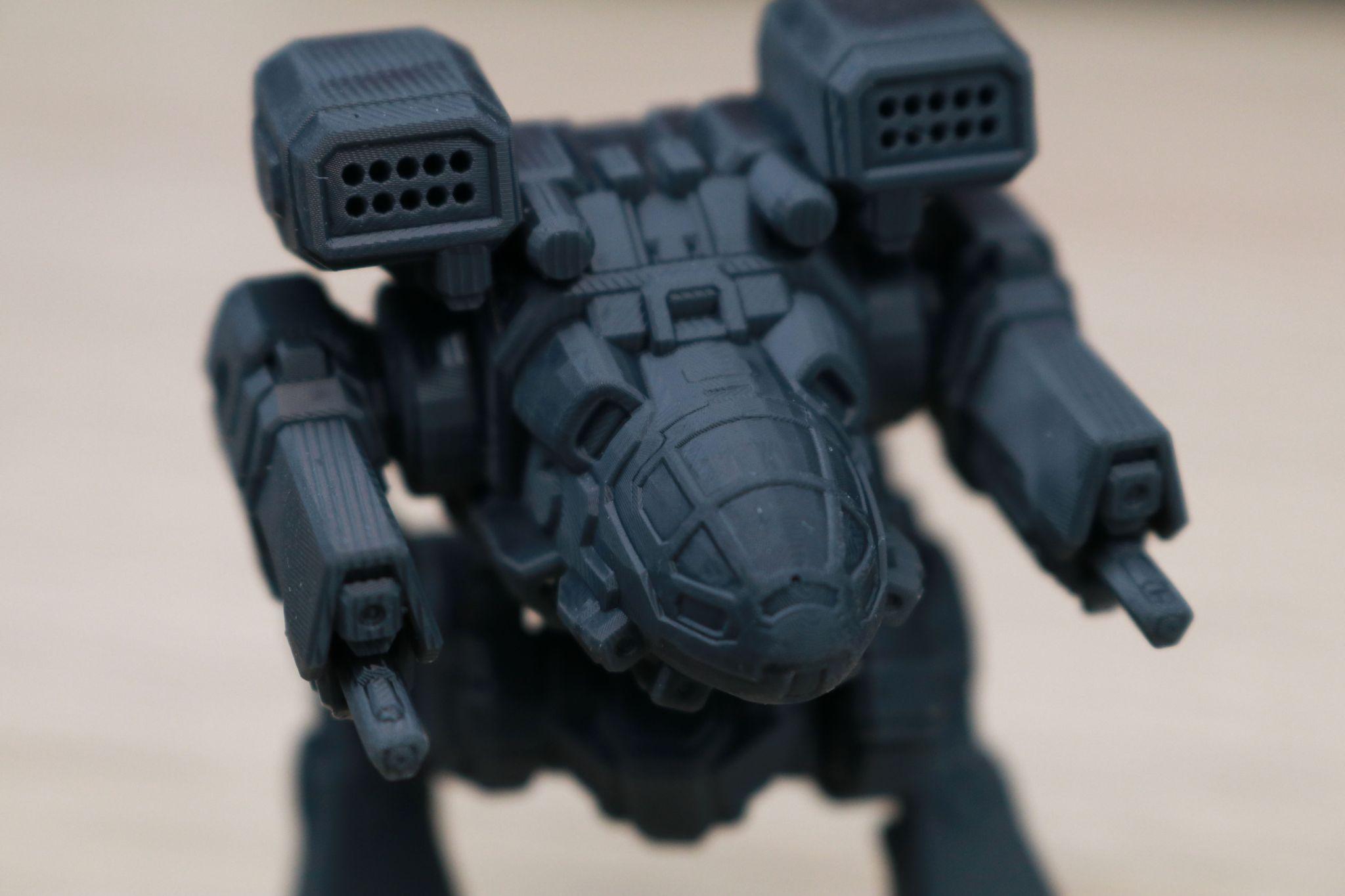
Using the support structure automatically generated by PrusaSlicer, the model printed in 1 hour and 53 minutes without any issues. When printing models that have lots of small details, it’s always possible that a small piece of cured resin will detach from the model and float away in the tank, potentially causing issues in later prints. The slicer app Chitubox has the ability to detect and remove these floating islands, but I couldn’t find a comparable feature in PrusaSlicer. This is the only improvement I could see Prusa adding to this software; the experience was otherwise straight-forward and didn’t present any surprises.
Comparison of the Prusa SL1S vs. Elegoo Mars 3
For anyone considering purchasing a resin printer, it may be difficult to understand why the price of the Prusa SL1S is so much higher than some of the other resin printers on the market. To benchmark this machine, I printed a model on both the SL1S as well as the Elegoo Mars 3, one of the best 3D printers you can buy in 2021 which happens to cost $300 or less. To understand this benchmark test, it’s worth taking a look at the specs of both machines to better understand their performance.
Row 0 - Cell 0 | Prusa SL1S | Elegoo Mars 3 |
Masking LCD Resolution | 2560 x 1620 | 4098 x 2560 |
XY Resolution | .049mm | .035mm |
Build Dimensions | 5 x 3.15 x 5.91 inches | 5.64 x 3.52 x 6.89 inches |
Build Volume | 93.08 cubic inches | 136.79 cubic inches |
Printer Dimensions | 8.8 x 9.3 x 15.7 inches | 8.93 x 8.93 x 17.28 inches |
Printer Volume | 1284 cubic inches | 1378 cubic inches |
Build / Footprint Ratio (higher is better) | 7.2% | 9.9% |
Cost | $1,999 | $300 |
Benchmark Part Time | 2 Hours 59 Minutes | 5 Hours 19 Minutes |
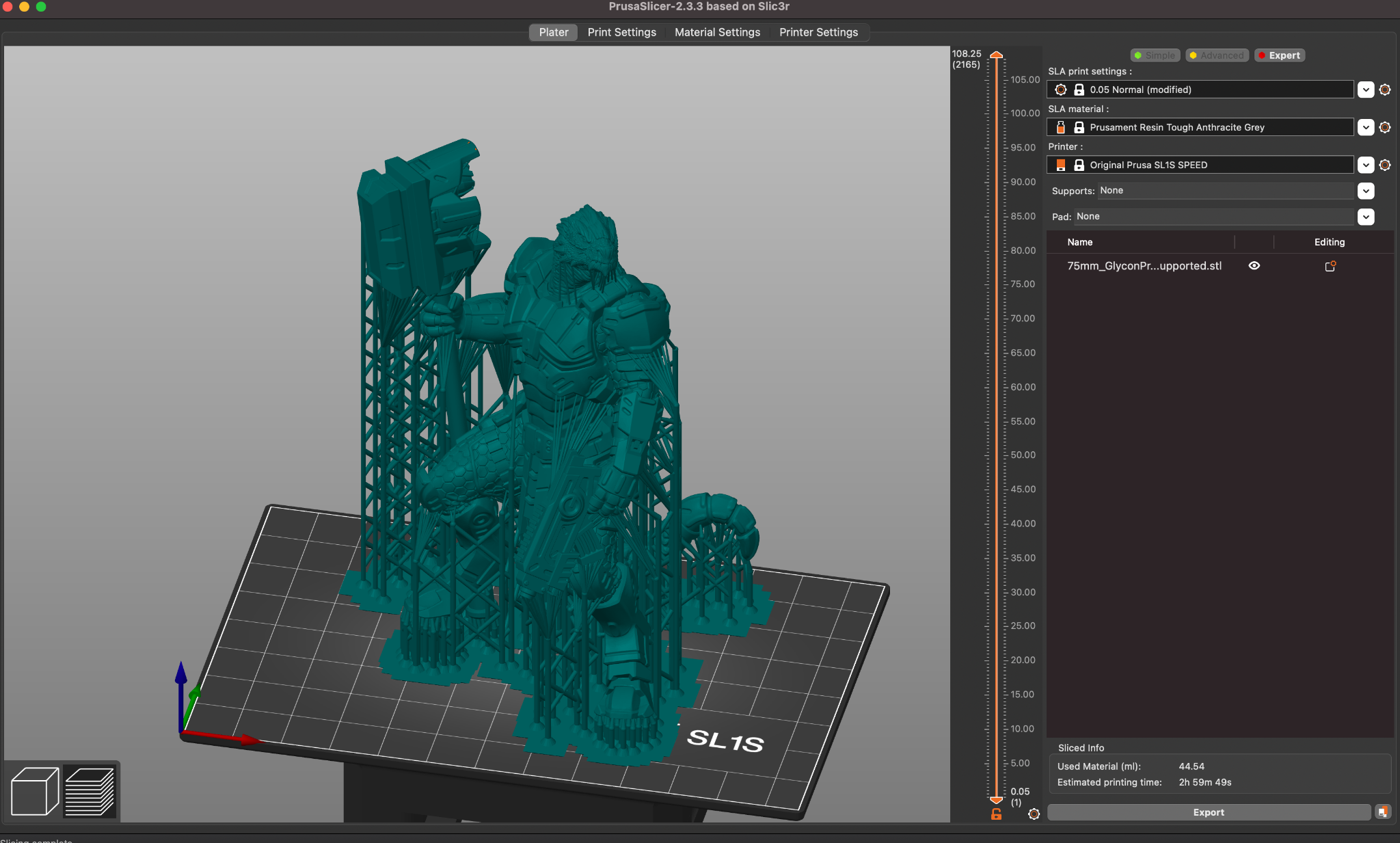
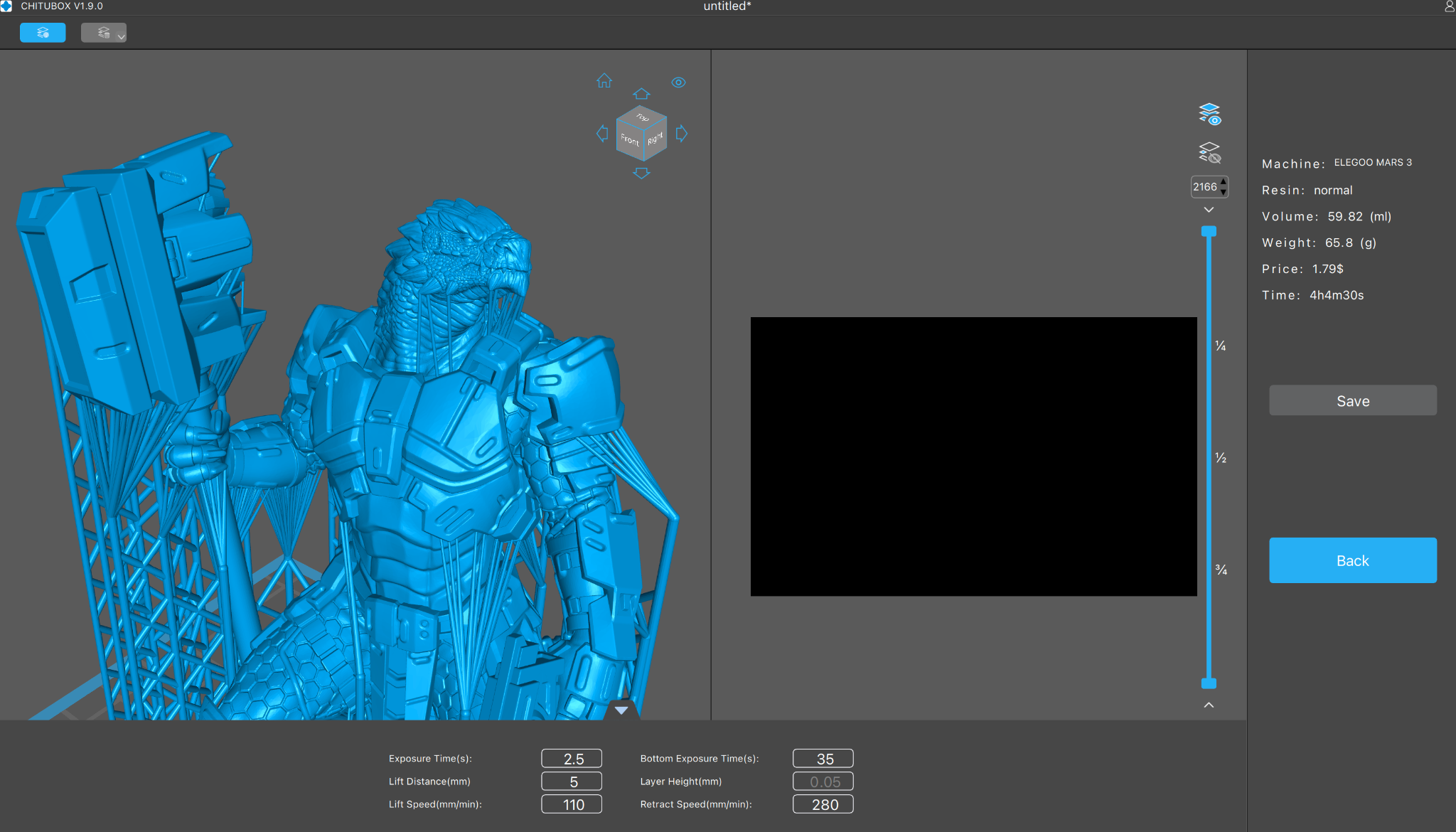
To minimize variables between the two prints, I used a pre-supported model from Loot Studios that prints hollow with an internal support structure. I used default settings on both PrusaSlicer as well as Chitubox, and used Prusament Tough Anthracite Grey resin on both the SL1S and the Mars 3. Both models were printed at a default layer height of 0.05mm (50 microns), and the exposure time for PrusaSlicer defaulted to 2.4 seconds / layer while Chitubox defaulted to 2.5 seconds / layer.
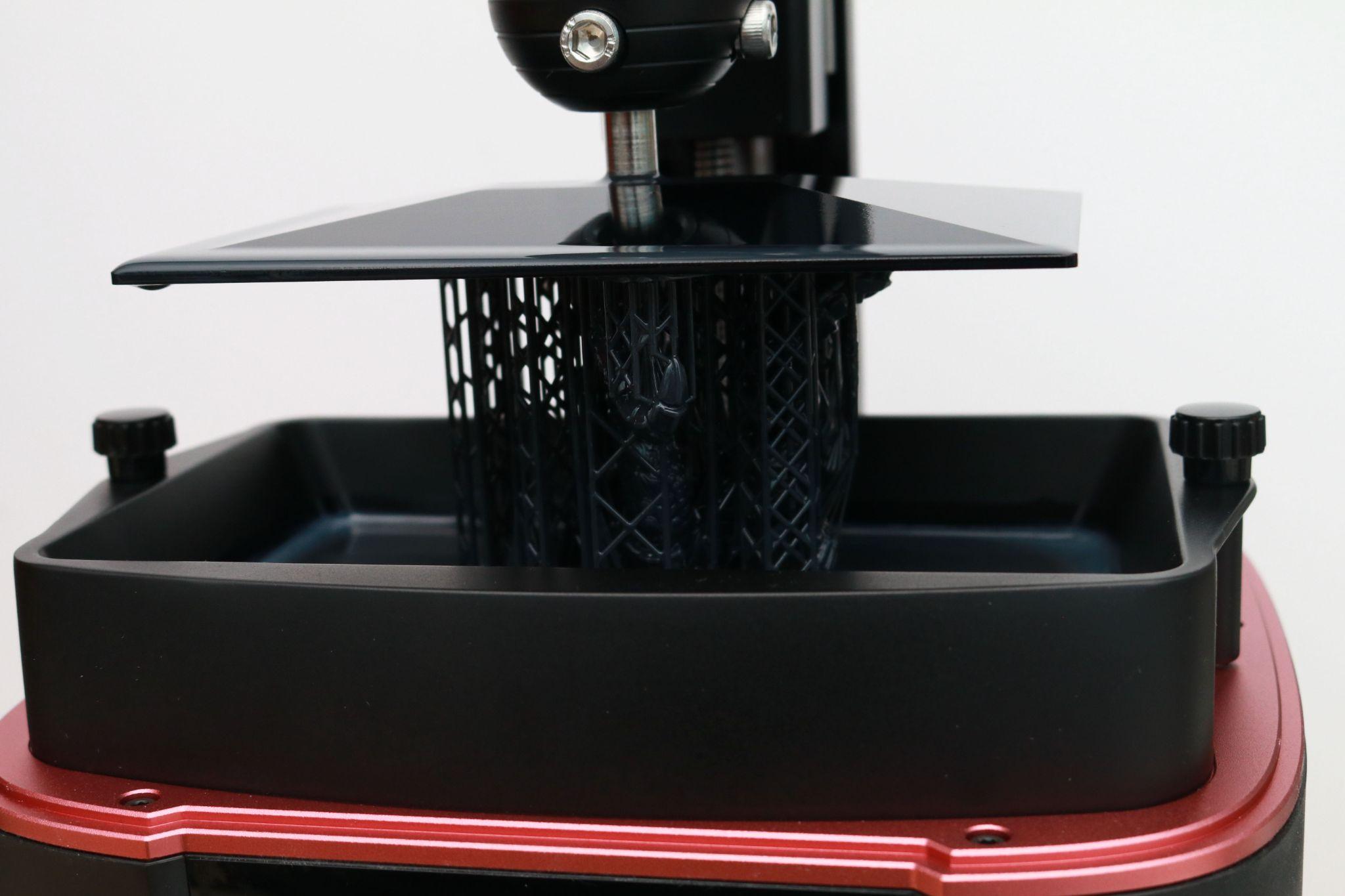
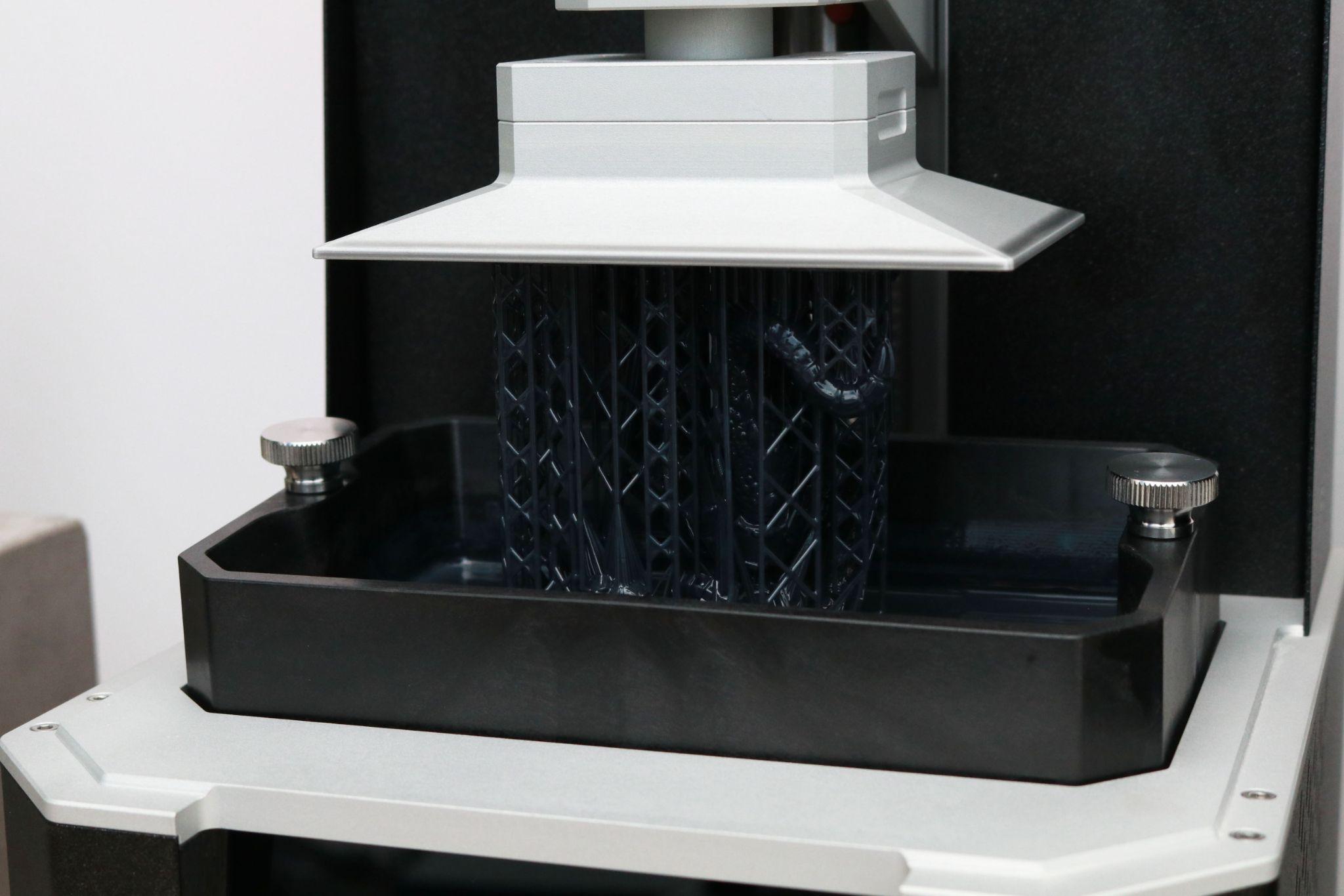
The model printed on the Mars 3 took 5 hours and 19 minutes, a large difference from the estimated 4 hour and 4 minute print time provided by Chitubox. By contrast, the model printed on the SL1 took 2 hours and 59 minutes, precisely down to the minute of the estimate provided by PrusaSlicer.
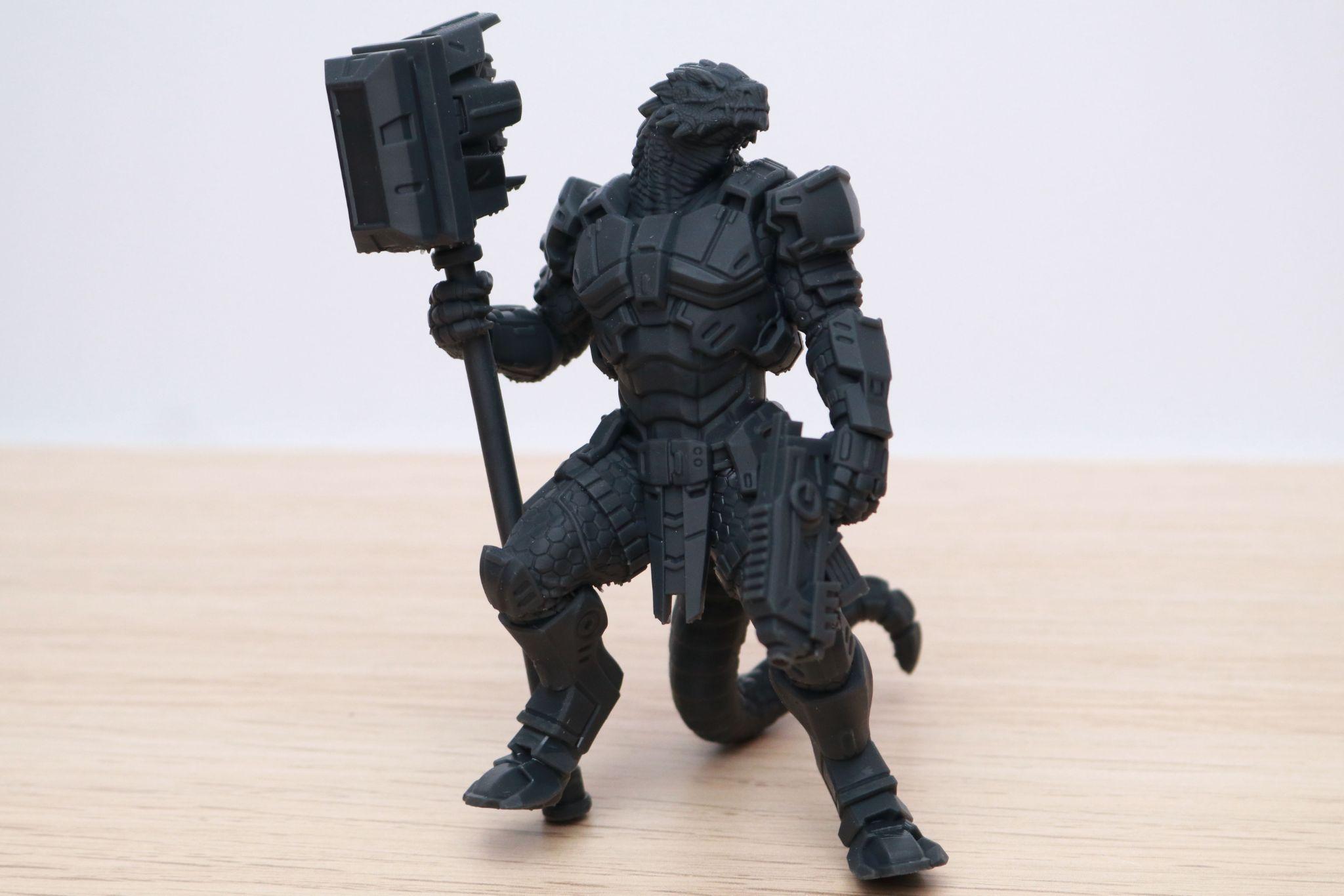
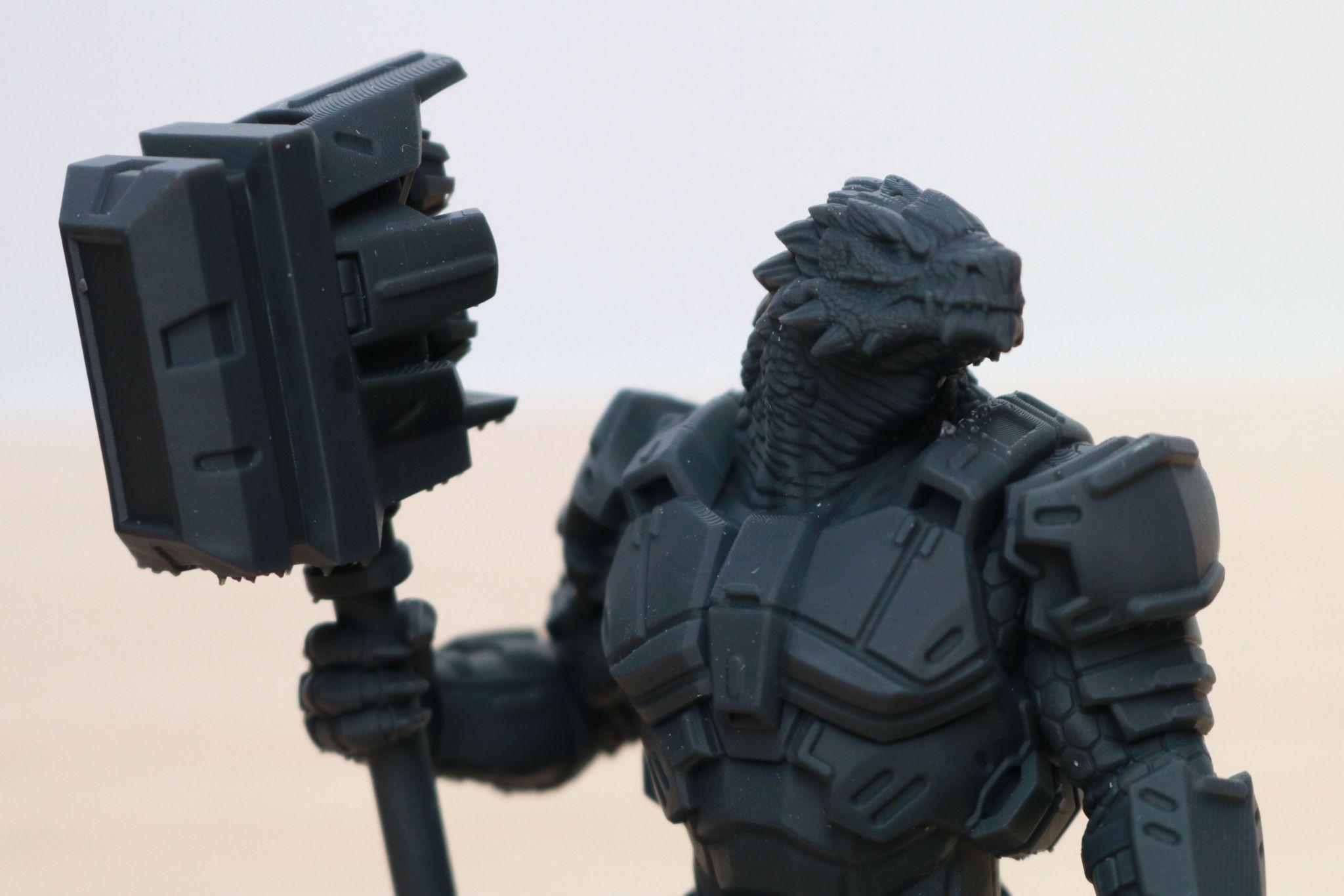
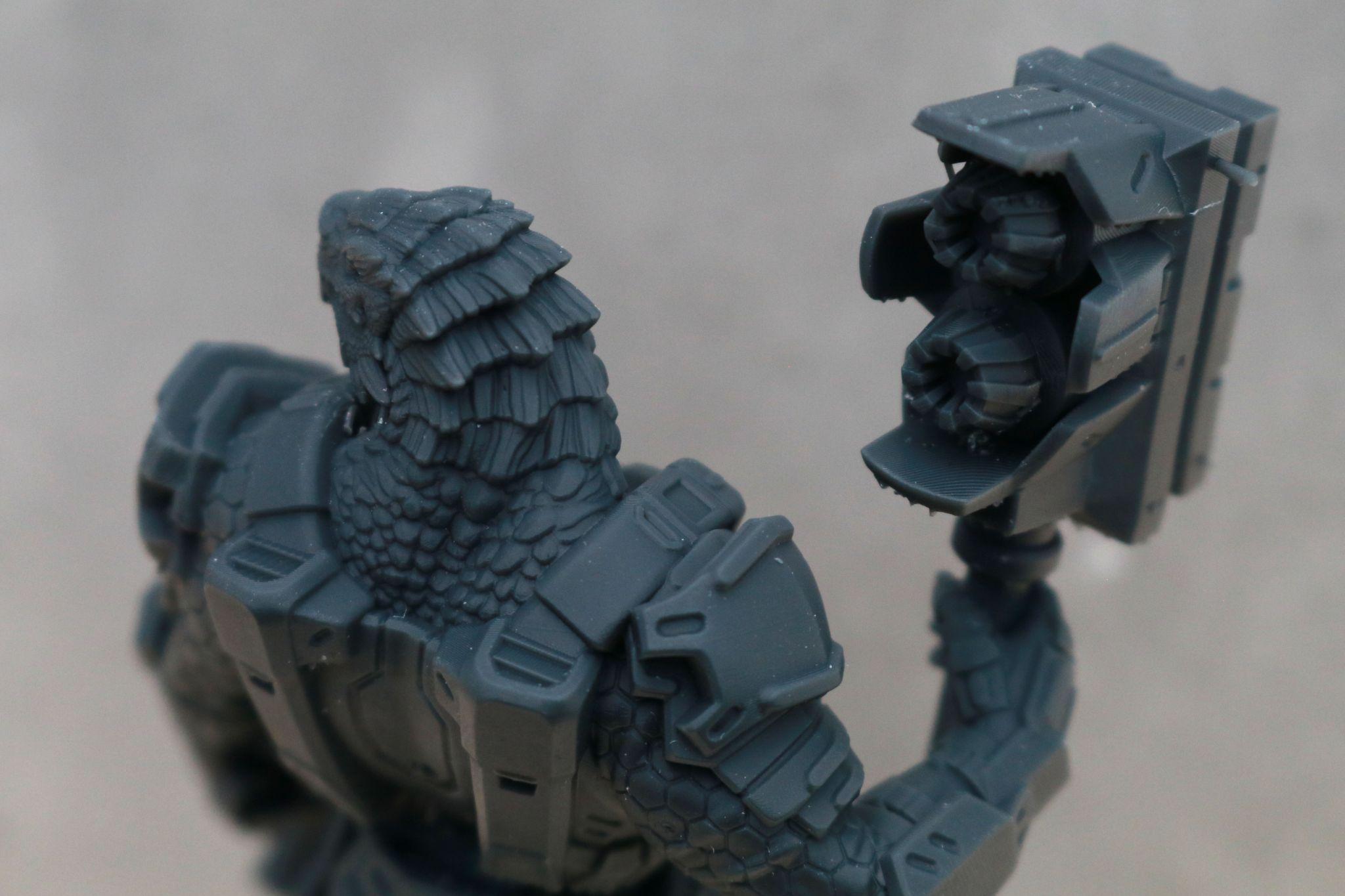
The print from the Mars 3 featured a high level of detail, and the texture on both the skin of the model was clean and well-defined, and the smooth plates on the armor had almost no visible stepping. The Mars 3 is a 4K Mono LCD with an XY resolution of .035mm, so this level of detail is about what you would expect.
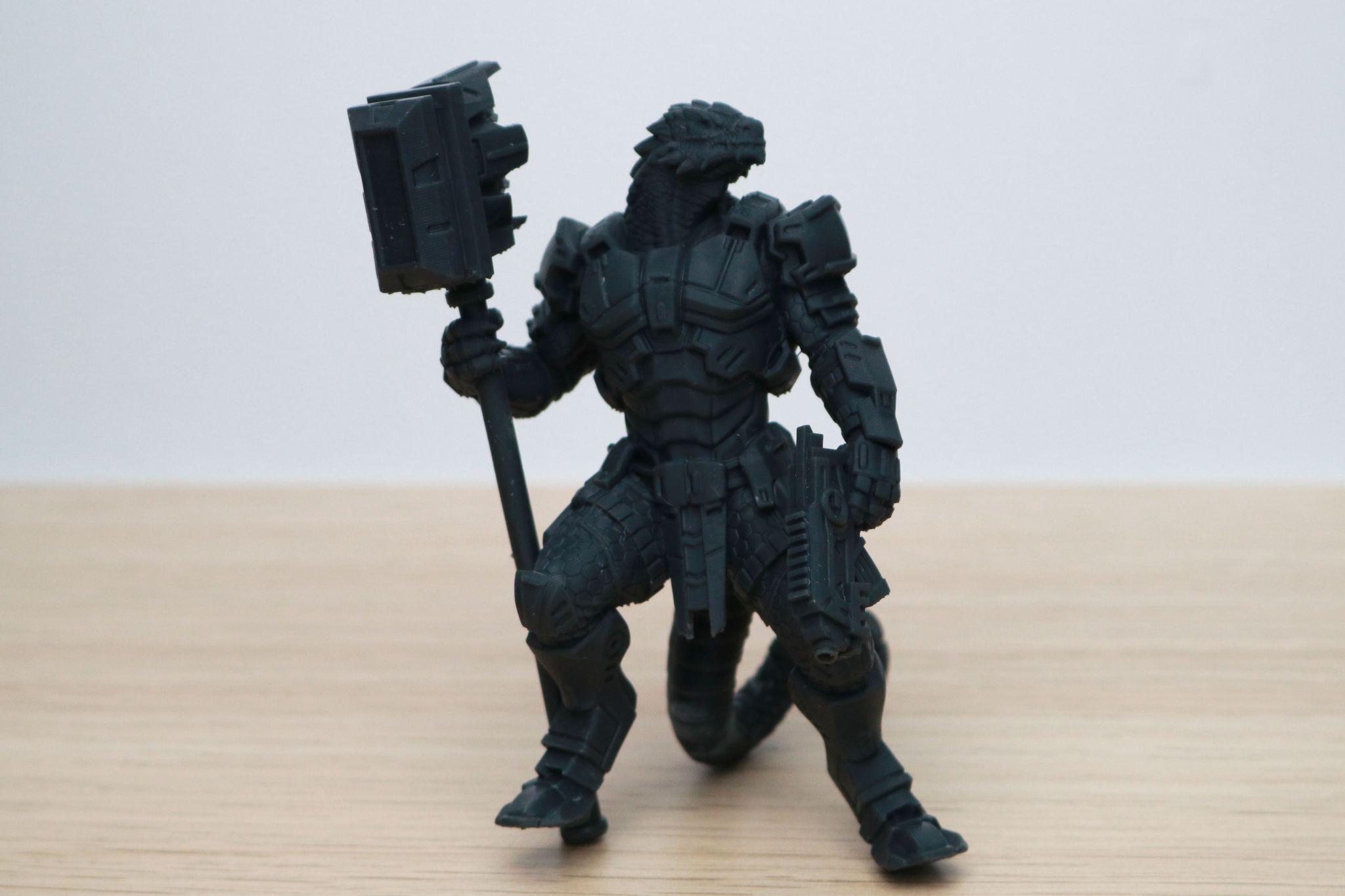
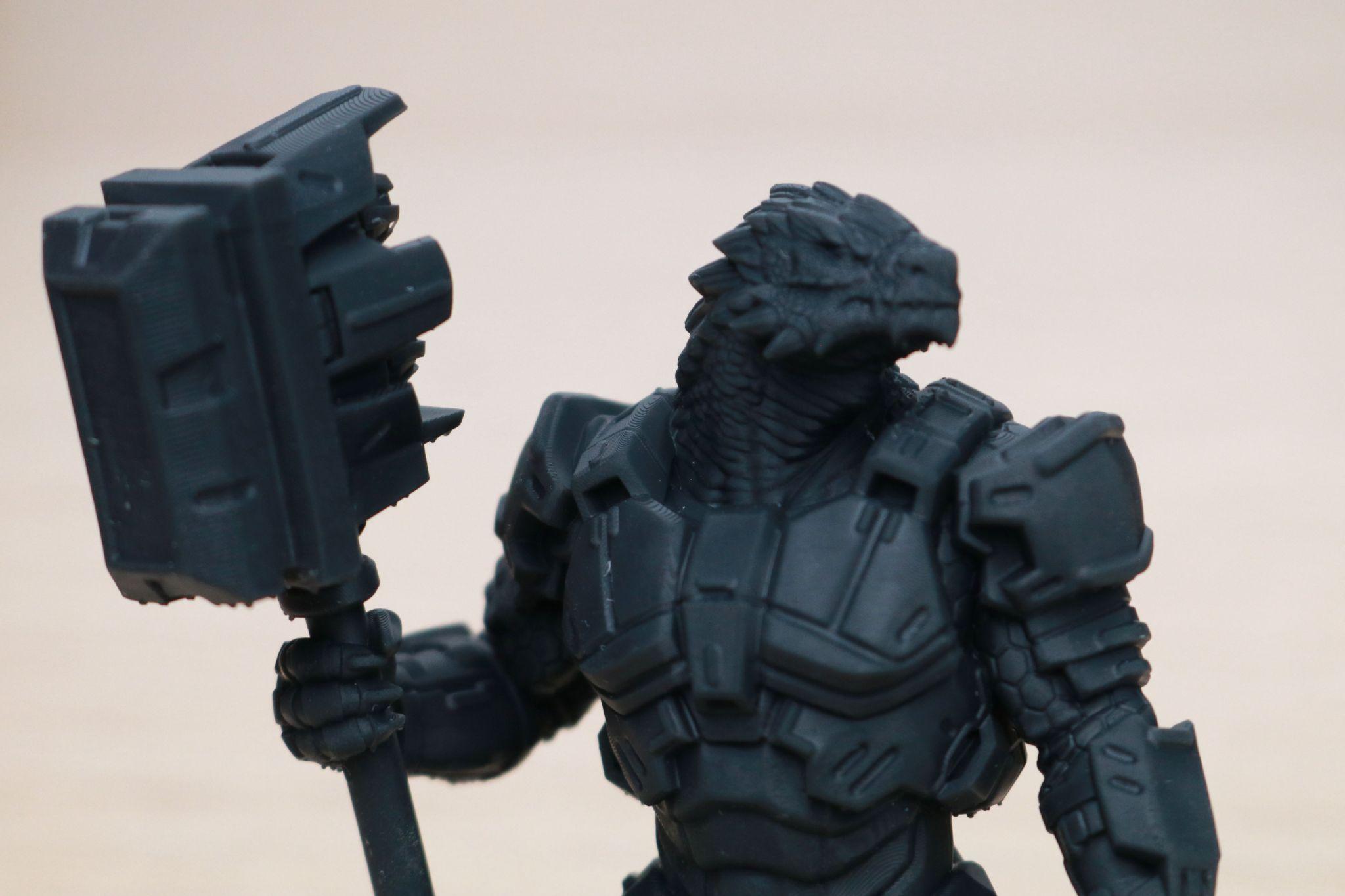
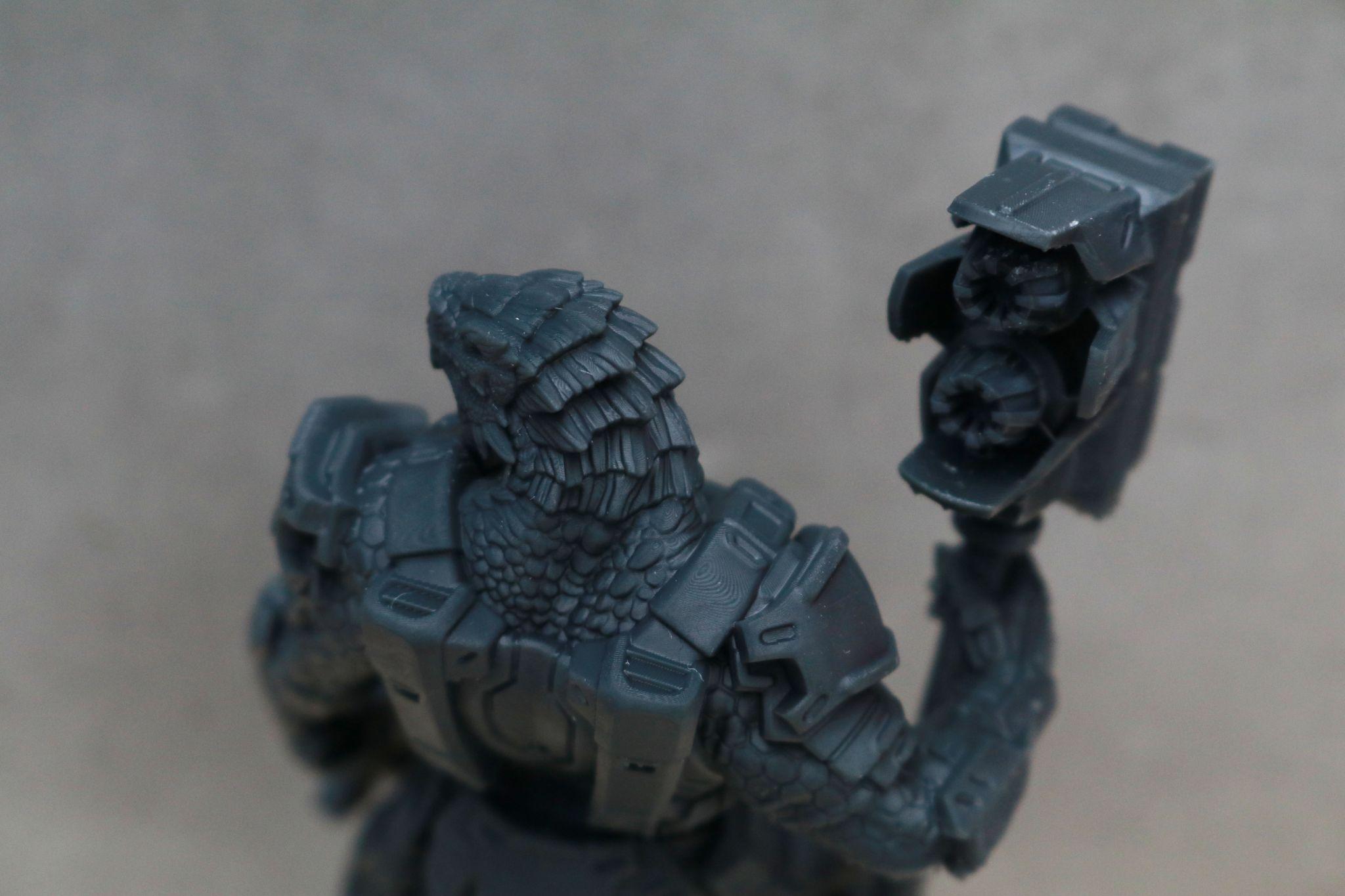
The print from the SL1S looked equally detailed, and despite a technically lower XY resolution of .049mm, the model was nearly indistinguishable from the one made with the Mars 3, and completed in less than 60% of the time needed by the Mars 3. A side-by-side comparison reveals two models that are very similar in appearance. The model on the left below was printed on the Mars 3, and the model on the right was printed on the SL1S.
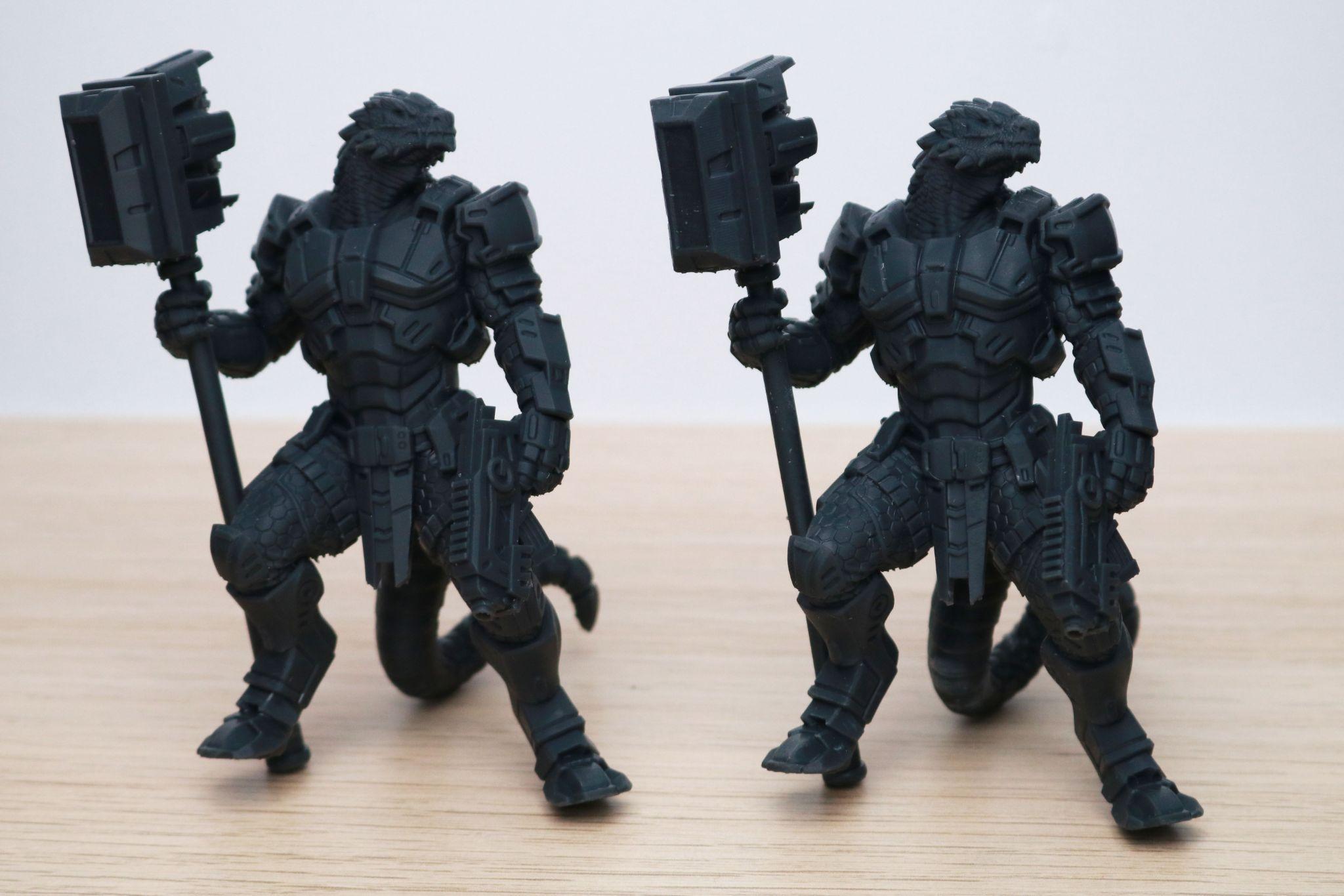
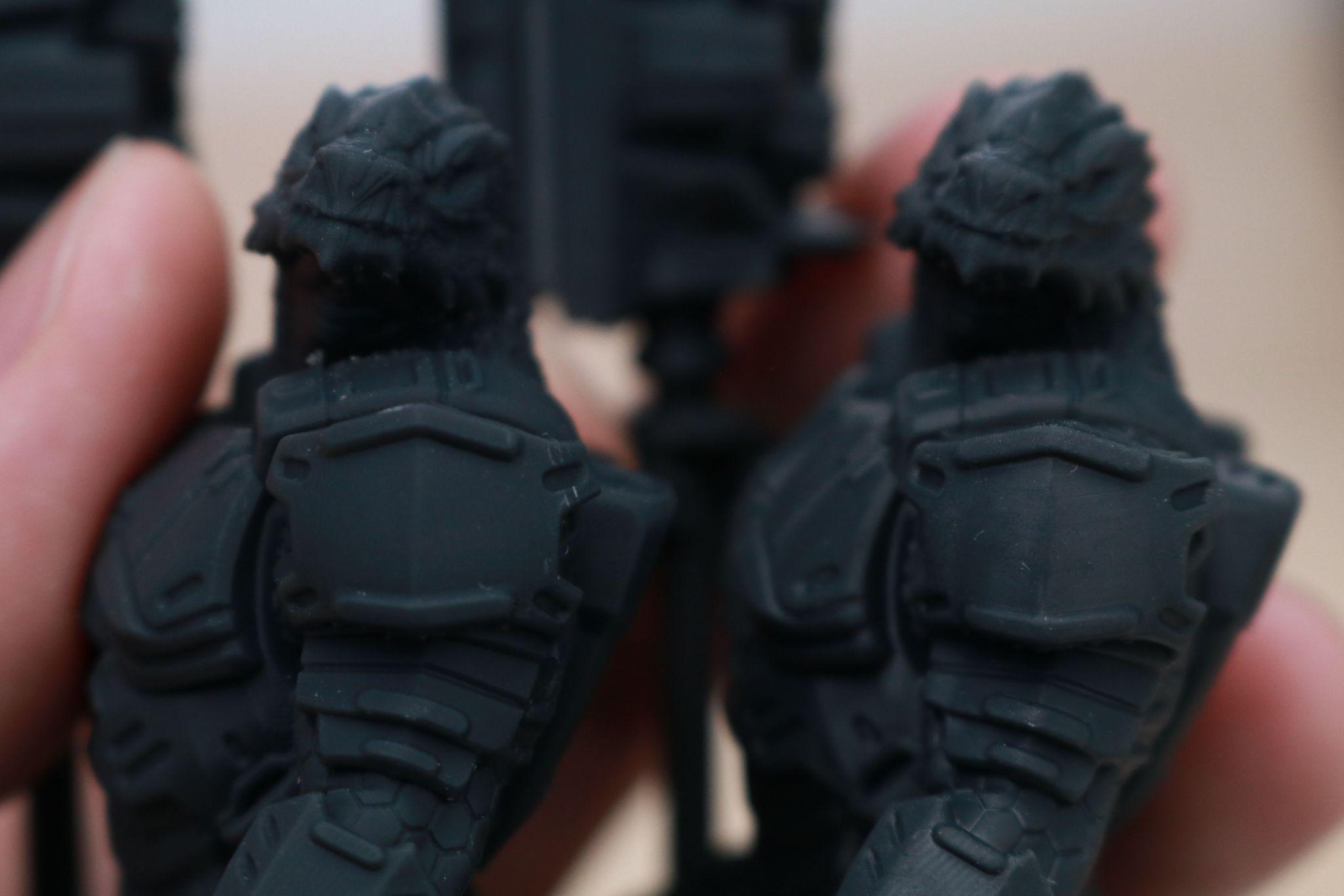
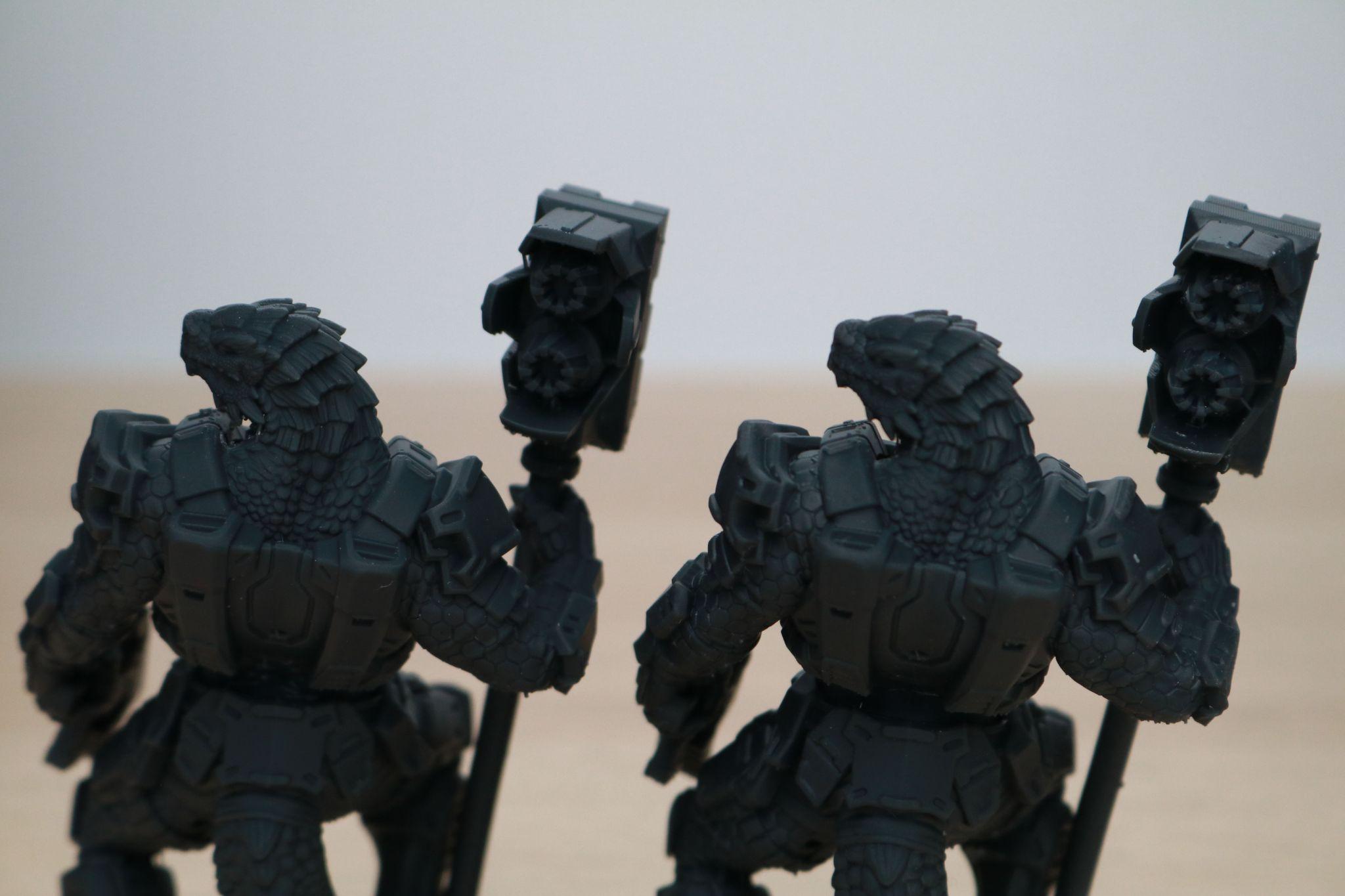
Printing a Model from prusaprinters.org
Prusa has created an online file repository called ‘PrusaPrinters’ that encourages users to upload both 3D models as well as prepared 3D files that are ready for printing. As an example of this is the ‘Wardragon’ model, which is available as a ‘.sl1s’ file format that is readily printable by the Prusa SL1S without any additional software. This type of file sharing allows users to download models that they can print without having to worry about going through the slicing process.
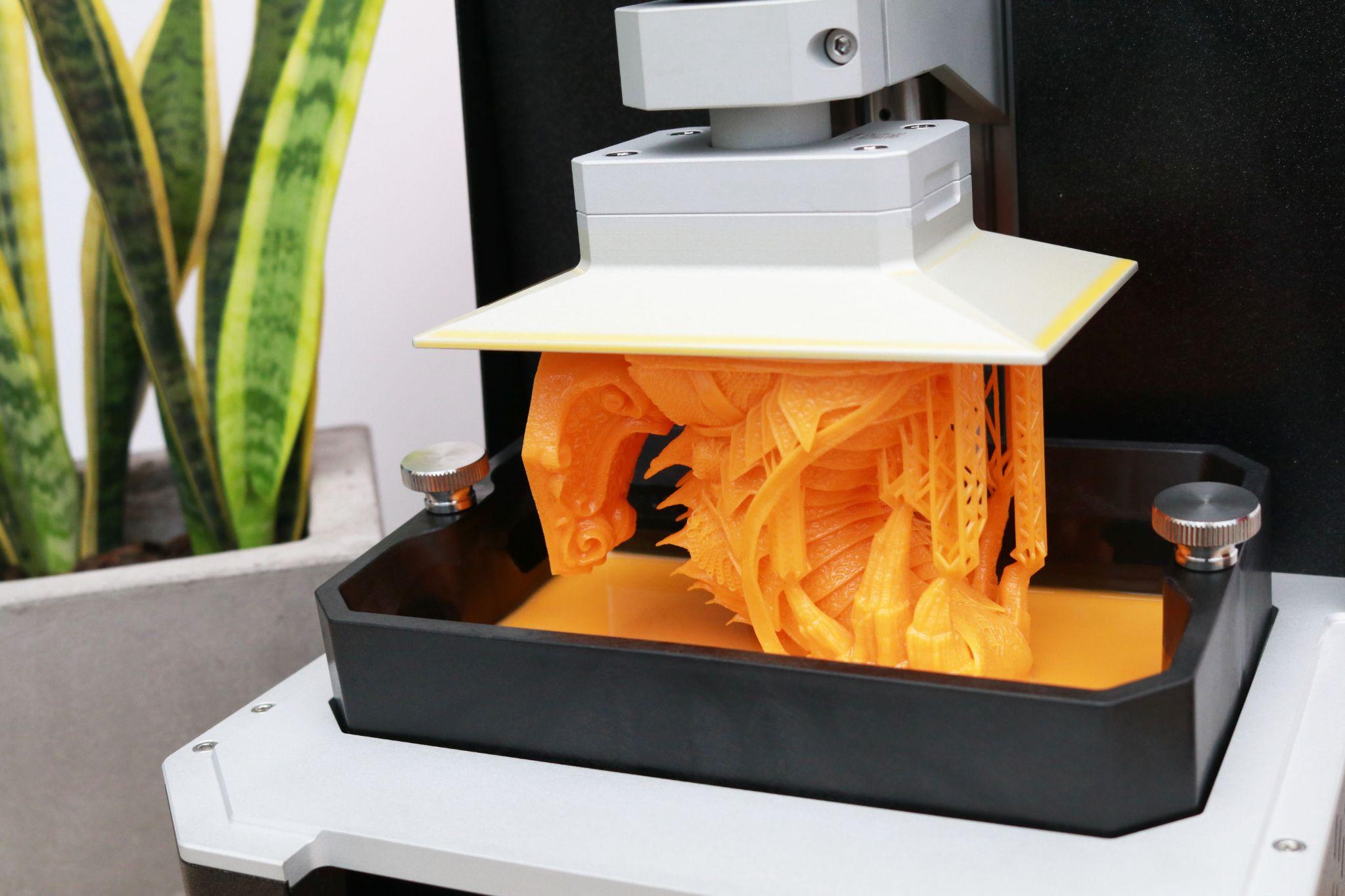
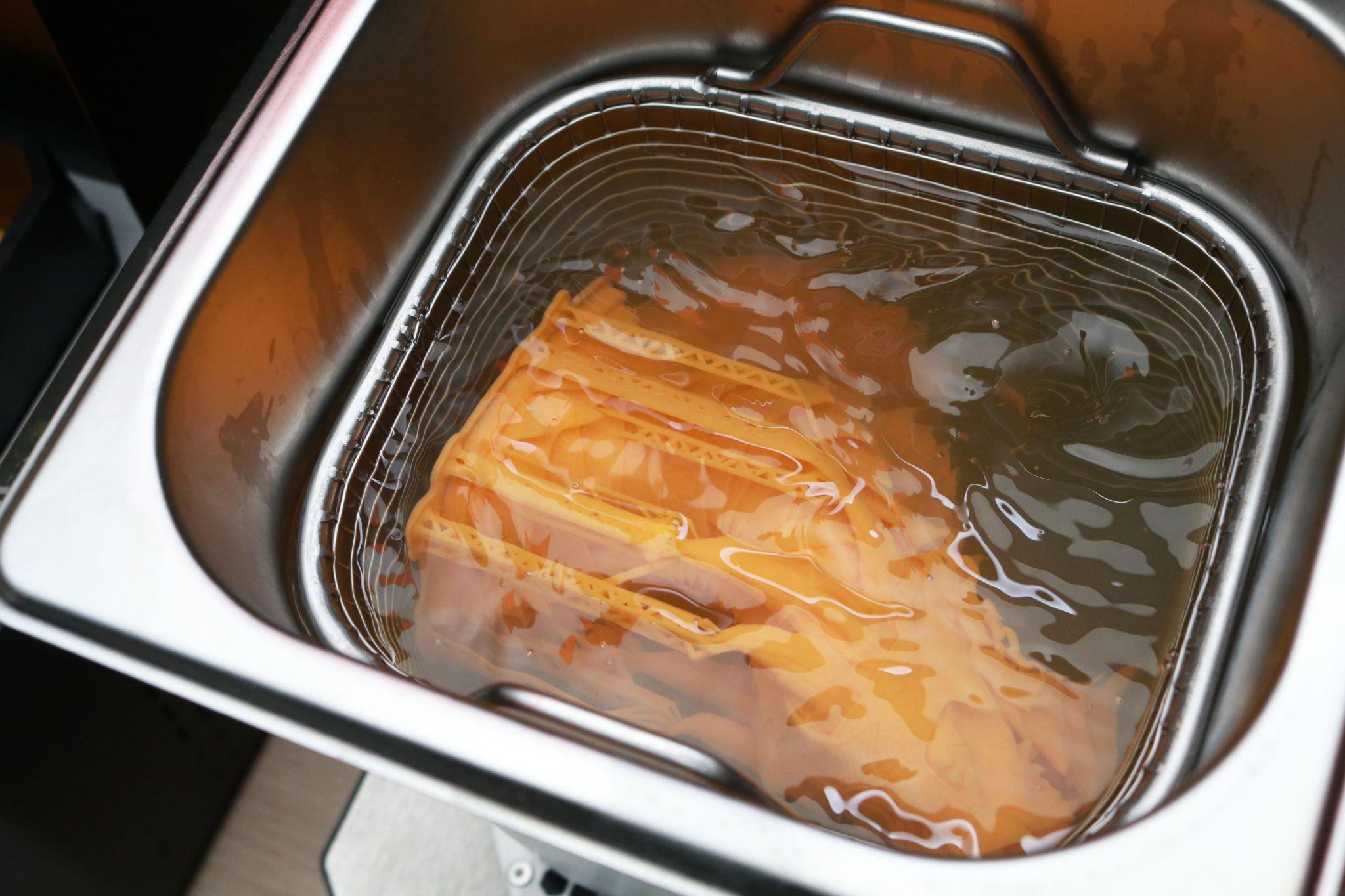
I downloaded the wardragon.sl1s file and printed it using Prusa Tough Orange material without making any modifications to either the settings or the printer.
The Wardragon model printed without any issues, and it really was as simple as downloading the .sl1s file, putting it on a thumb drive, plugging it into the printer, and hitting ‘start’. The model printed in 3 hours and 1 minute, an improvement over the estimated time on the site of 3 hours and 29 minutes. I’m used to slicer apps providing ‘optimistic’ print times which are usually 20-50% short of the actual print time, so having a printer finish before the estimated time was a pleasant surprise.
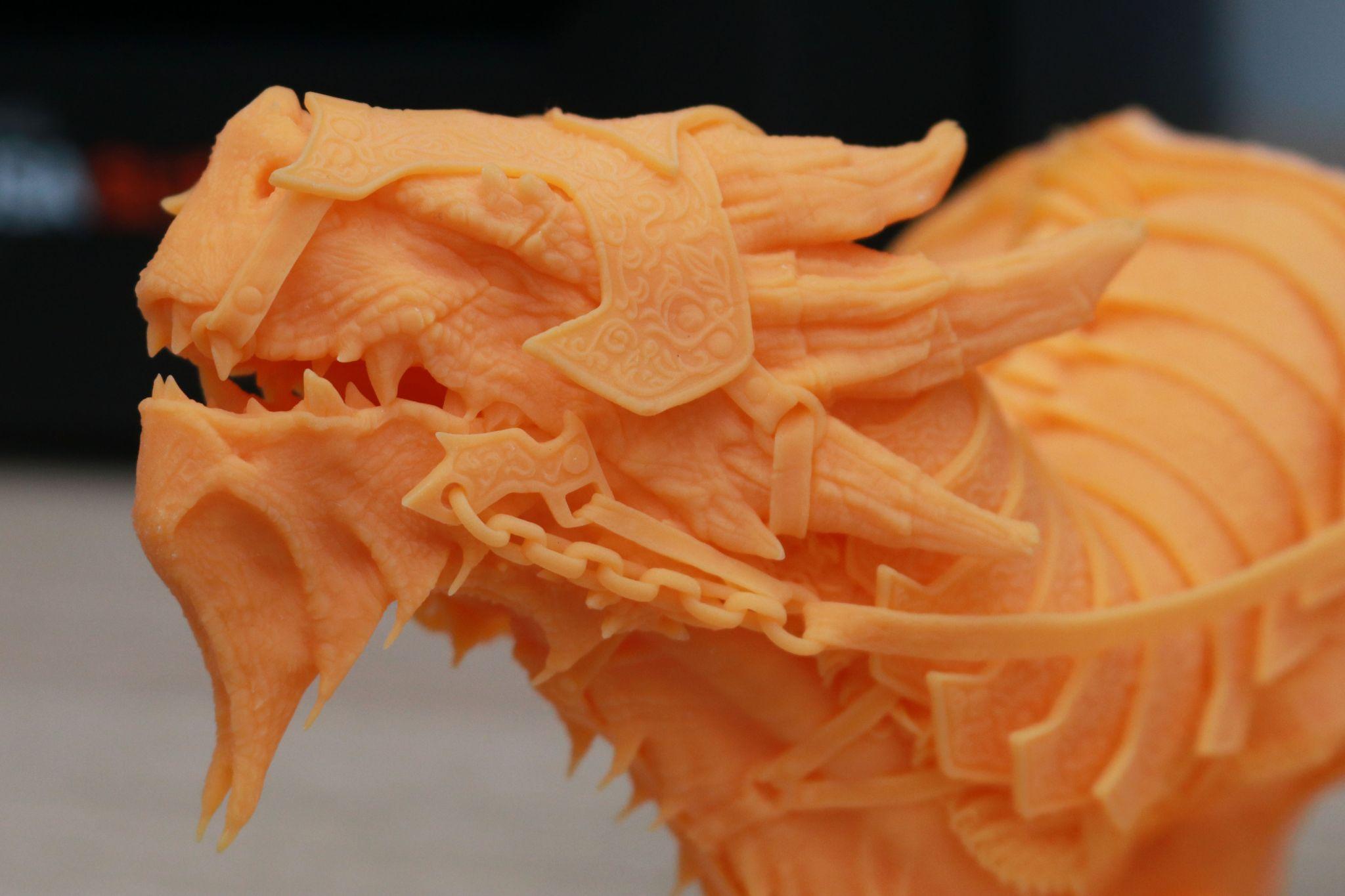
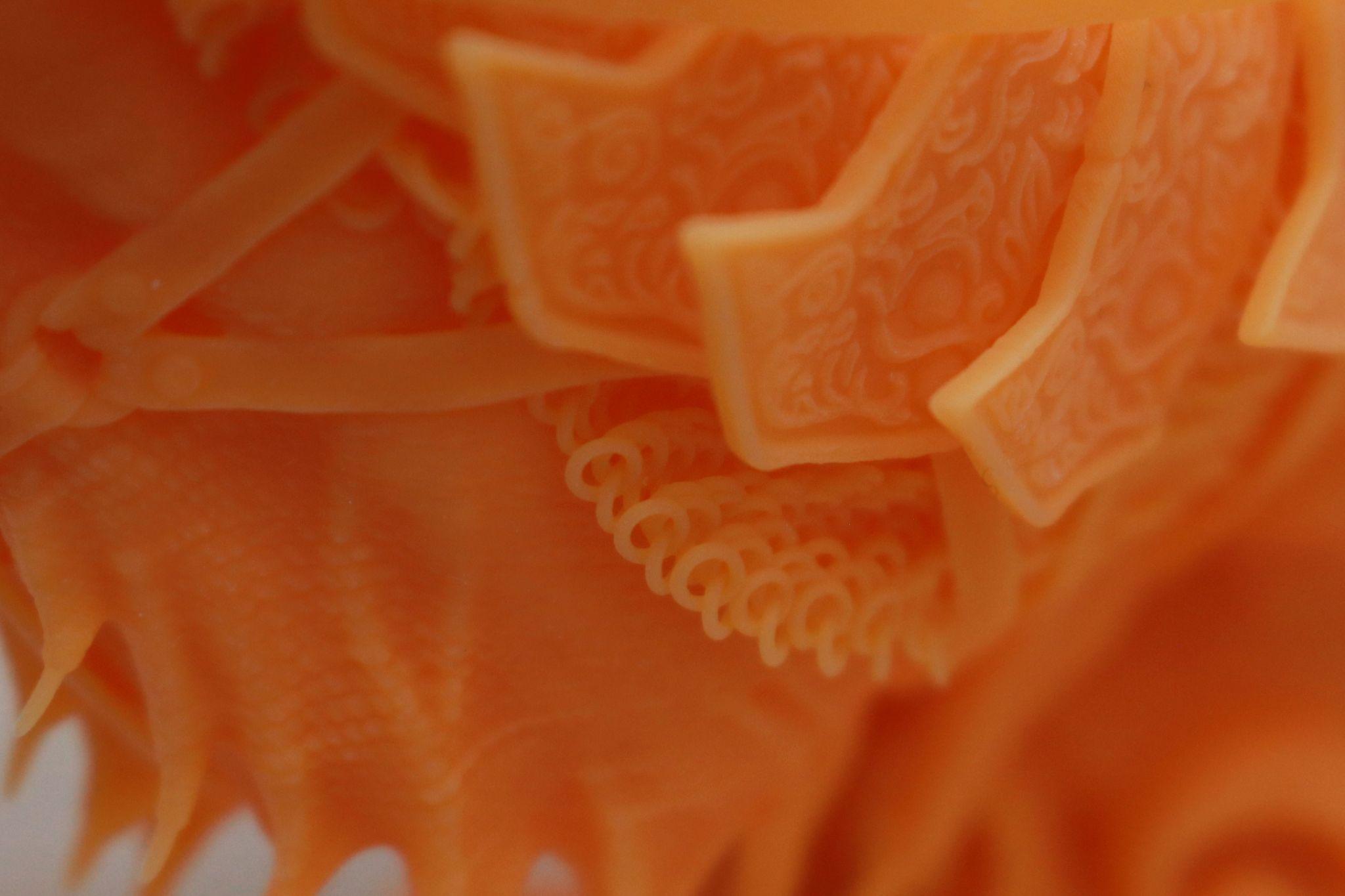
After removing the part from the build platform of the machine, I post-processed the model using the Prusa CW1S to clean up the excess resin and fully cure the part. The detail on the model is striking, with individual rings visible on the reins of the dragon and the textured skin of the model looking sharp and lifelike. I was most impressed with the chainmail rings hanging underneath the armor; they appear to almost float in air and the level of detail is far past what I would have expected from a 2K masking LCD screen.
Printing Multiple Models on Prusa SL1S
Resin MSLA 3D printers, like the Prusa SL1S, have a unique advantage over FDM 3D printers when it comes to print speed by virtue of the curing process. Each layer on a MSLA resin 3D printer has the potential to be cured across the area of the platform, so adding multiple parts doesn’t add any additional print time. As an example of this technique, I’ve loaded three copies of the same Sci-Fi Door model from Loot Studios into PrusaSlicer side-by-side on the build platform.
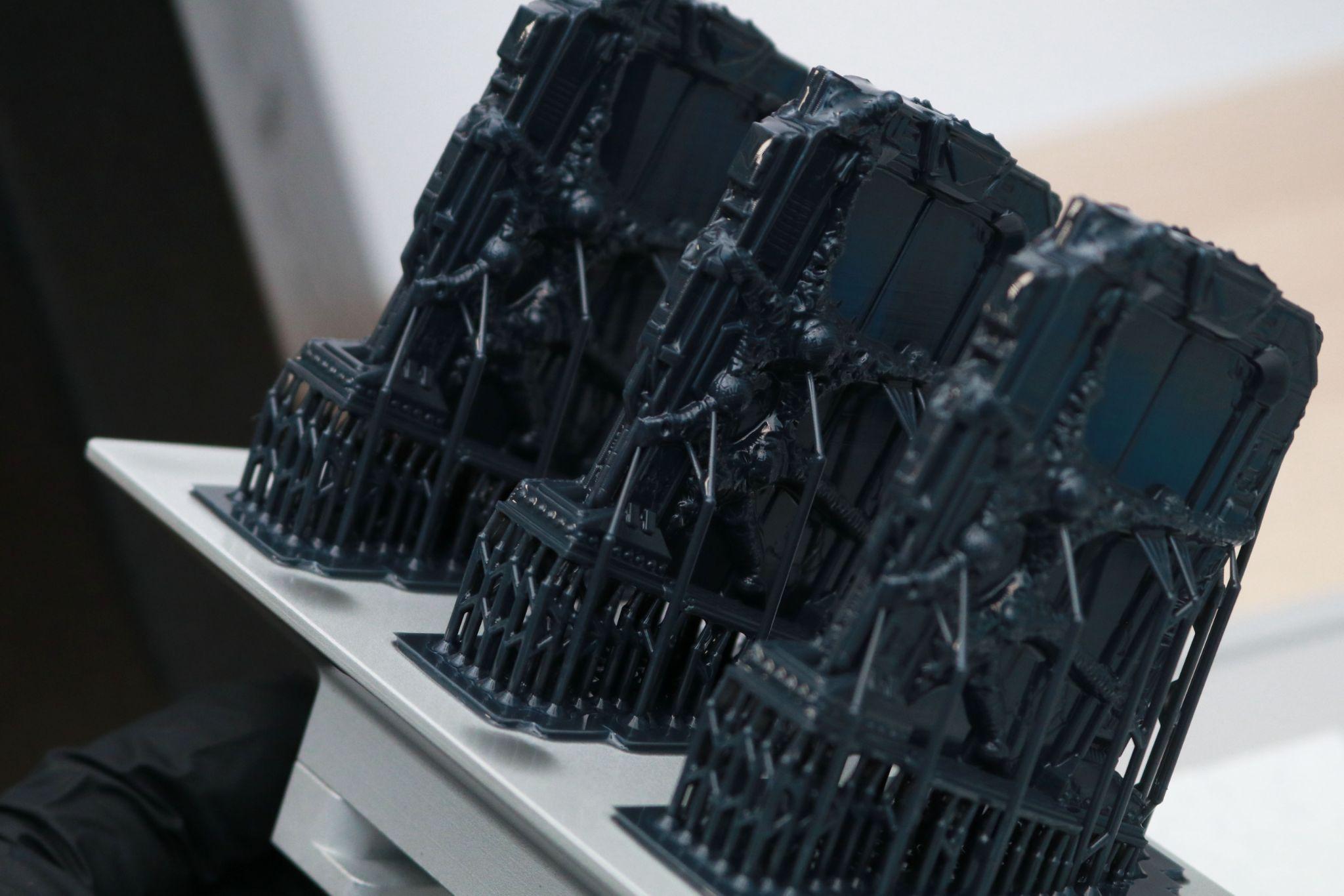
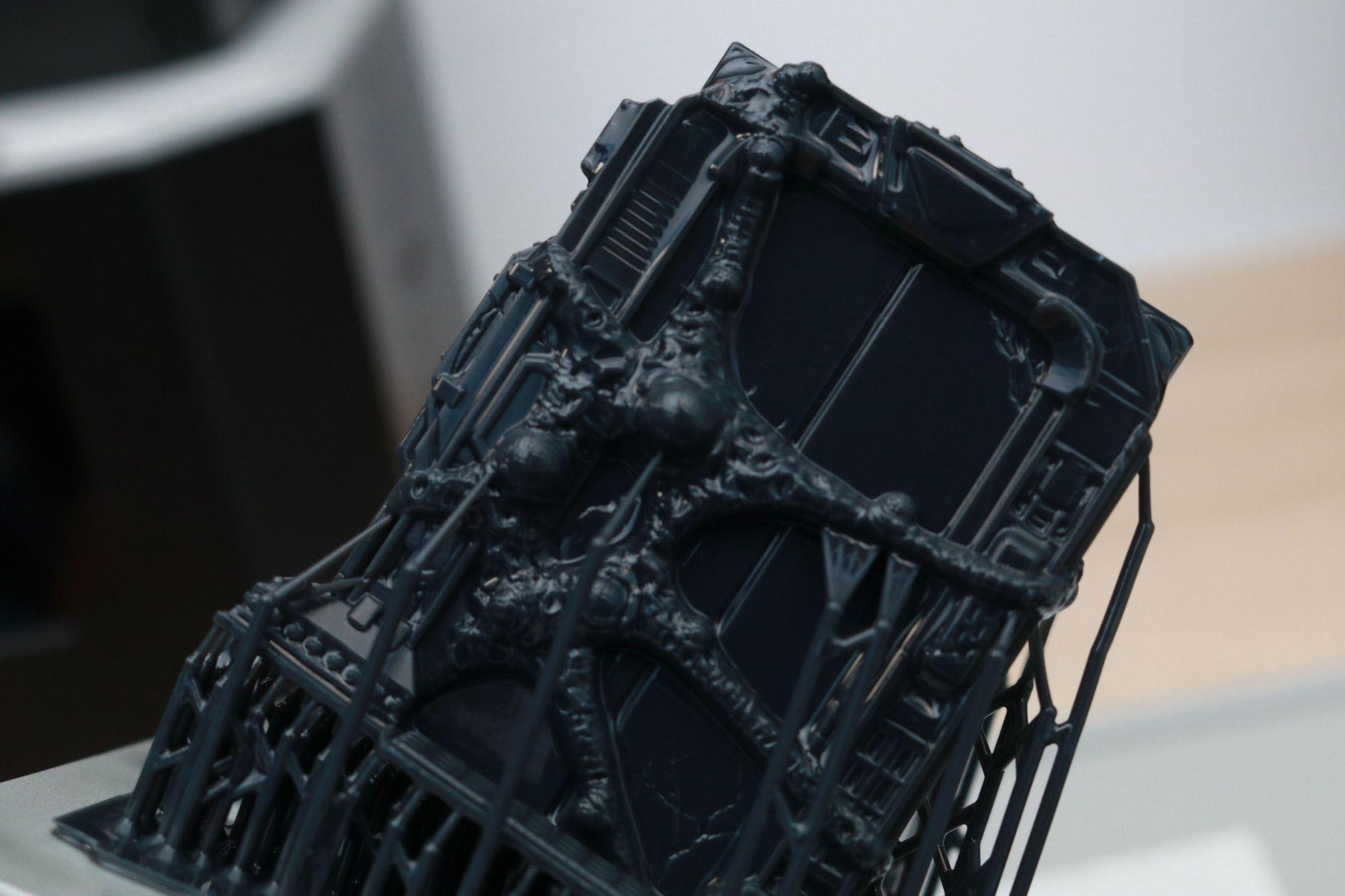
Printing three of these models simultaneously took 1 hour and 59 minutes, the exact same amount of time it would have taken to print a single one. Typically, keeping a relatively thin cross-sectional width is important to avoid causing undue stress on the FEP film, but the unique tilt-and-peel nature of the SL1S means that printing large parts in multiplies is a viable strategy.
The detail on each model is identical, and it’s impossible to tell the three apart from each other. By printing these three models simultaneously, I effectively reduced the cycle time (or time per part) to one third the amount required to print a single part. This is done with no penalty to print quality, and the models look the same as if they had been printed individually. For anyone interested in printing large quantities of small parts reliability, the SL1S has shown it is more than up for the challenge.
Bottom Line
The $1,999 price of the Prusa SL1S ($2,599 with the CW1S Cure/Wash station) is certainly high enough to raise the eyebrows of most hobbyists. This machine is not designed to compete in the race-to-the-bottom pricing of other inexpensive machines, and instead focuses very intensely at providing reliable results using sturdy, high-quality components. After spending time with this machine and testing it for a variety of applications, I can whole-heartedly recommend it for anyone interested in a reliable resin MSLA 3D printer and believe that it has earned a place among the best 3D printers.
Prusa is involved with every aspect of the ecosystem of this machine, from the hardware, to the software, even down to the consumables like the Prusament resin. This translates to a smooth, predictable printing experience that involves little to no trouble-shooting or guessing on the part of the user, so they can spend more time printing and less time tweaking.
The tilting vat, ballscrew Z axis, resin vat sensor, lightning-fast print speed and other high-end touches go a long way to justifying the cost of the machine, but at the end of the day, this machine isn’t going to be a great fit for everyone. If you’re not interested in the speed of the printer and more concerned about large build volume, it might make sense to investigate a less-expensive option such as the Elegoo Saturn as an alternative.
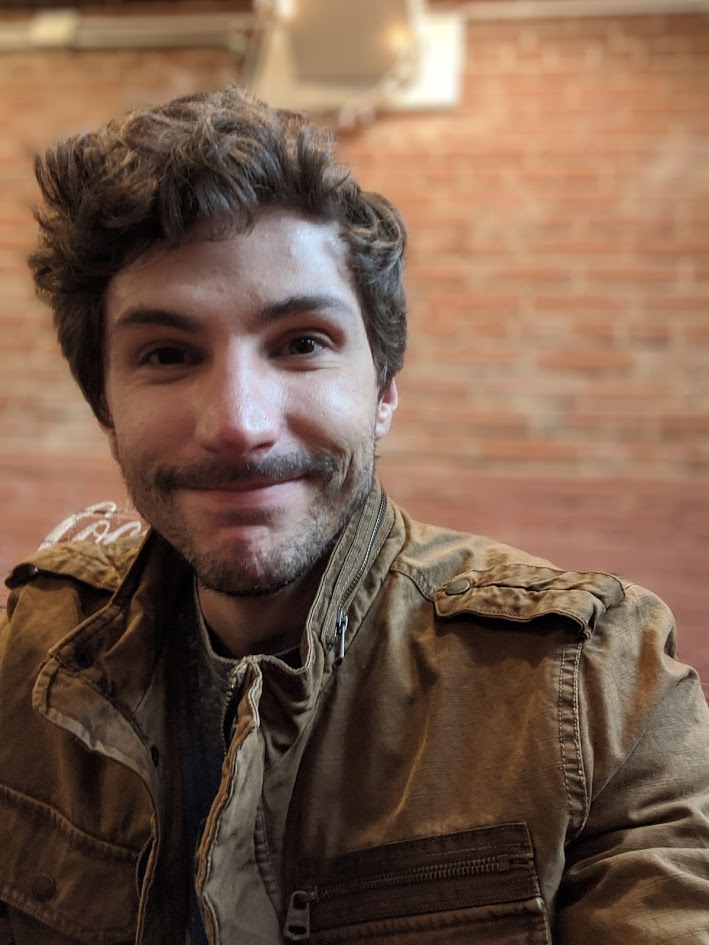
Andrew Sink first used a 3D printer in 2012, and has been enthusiastically involved in the 3D printing industry ever since. Having printed everything from a scan of his own brain to a peanut butter and jelly sandwich, he continues to dive ever more deeply into the endless applications of additive technology. He is always working on new experiments, designs, and reviews and sharing his results on Tom's Hardware, YouTube, and more.