Picking The Right Power Supply: What You Should Know
How does a power supply work? Why is it important to choose a sufficiently powerful and efficient model? We guide you through discussions of efficiency and tips for getting the best deal before we go on to explain why less can be more in the PSU market.
Reliability Above All: Caps And Fan
Why you can trust Tom's Hardware
Capacitors play an important role in determining a power supply's long-term reliability. The APFC (bulk) cap must be of high quality. Moreover, the electrolytic caps on the secondary side must come from a reputable vendor and have a temperature rating of 105 °C, not 85 °C.
Besides decoupling, capacitors in PSUs are used to smooth out voltage and reduce ripple. They can also be used to store charge (voltage) and to block DC current (coupling). Electrolytic capacitors are used in the APFC converter as reservoir caps, and you will also find electrolytic caps on the secondary side of most PSUs. As their name indicates, these caps contain a conductive liquid called electrolyte. If this fluid is of low quality, the capacitor will quickly lose its characteristics and in a worst-case scenario it can even explode. Many of you will still remember the capacitor plague problem that affected many electronic devices between 1999 and 2007.
During a cap’s operating life, the amount of electrolyte decreases due to evaporation. In addition, the same material can be used to heal a damaged plate inside the cap, a procedure which leads again to its depletion. As the electrolyte’s quantity drops, the cap's electrical parameters naturally change, cutting into its useful lifespan. Polymer aluminum caps use a solid electrolyte as dielectric between the plates, so they don’t have the problems described above.
So why not use polymer caps exclusively and forget about electrolytic caps and their problems? The main reason is that the increased ESR values of electrolytic caps actually help avoid unwanted oscillations, which can cause instability. Although low ESR is critical in ripple filtering, minimizing ESR in PSUs isn’t a good idea either. This is why some re-cap jobs don’t go as expected. On top of that, polymer caps have a limited voltage rating. This doesn’t affect their use on the secondary side much, but in the APFC converter, an electrolytic capacitor has to be used.
Like capacitors, fans are also critical for ensuring your PSU delivers reliable service for many years. There are a number of popular fan bearing types, but three are most common to modern PSUs:
- Sleeve bearing fans (30,000h lifetime)
- Double ball-bearing fans (40-50,000h lifetime)
- Fluid dynamic bearing (FDB) and hydro dynamic bearing (HDB) fans (50-150,000h lifetime)
The best bearing type is considered to be FDB since it combines low noise output and an increased lifetime. Double ball-bearing fans are also popular in high-end PSUs for their quality. Meanwhile, sleeve bearing fans are mostly used in budget PSUs. They just aren't designed for horizontal mounting since oil inside the bearing moves to one of the shaft's sides, providing non-uniform friction protection.
Current page: Reliability Above All: Caps And Fan
Prev Page Don't Get Burned: Safety Before Stinginess Next Page How To Determine Your Power RequirementsGet Tom's Hardware's best news and in-depth reviews, straight to your inbox.
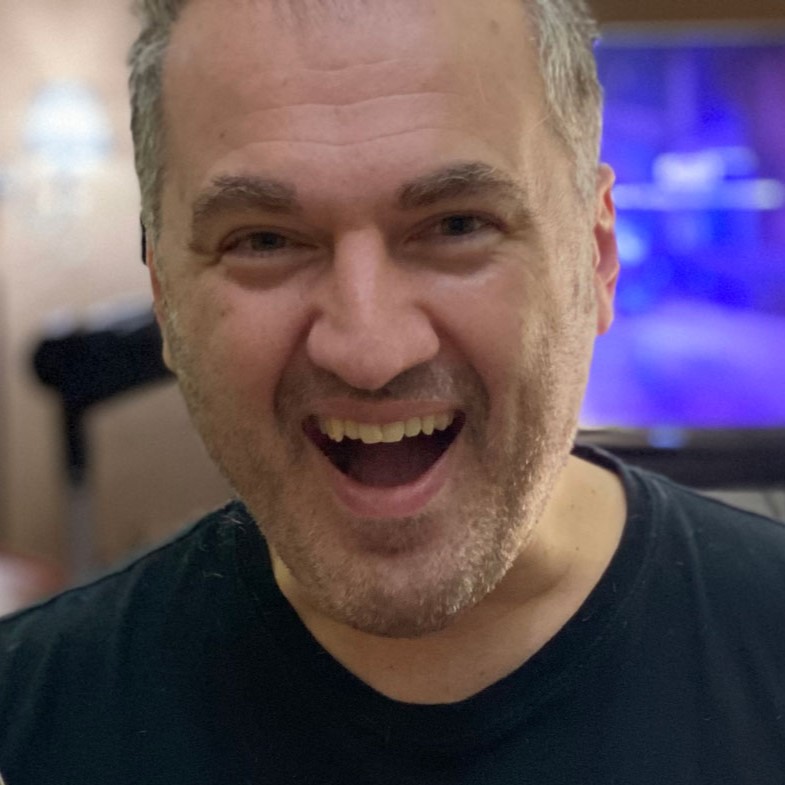
Aris Mpitziopoulos is a contributing editor at Tom's Hardware, covering PSUs.
-
abryant Archived comments are found here: http://www.tomshardware.com/forum/2916-56-picking-power-supply-knowReply -
pjmelect A few more words about active power factor correction. APFC won't save you money on your electric bill although the electric companies will love you for it as it minimizes loss over the power lines saving them money, it does however enable you to use a much lower rated battery backup system. A hypothetical example a computer that uses say 200W without APFC would require a backup system of 700W or much more to cope with the large peaks in current where as a power supply with APFC would require a backup system of 250W or so.Reply
Therefore APFC is only worthwhile if you were to use it with a battery backup system. -
turkey3_scratch Very well written article! Just one thing. You say:Reply
Regardless of whether the PC is idling or under full load, voltages may not deviate from their spec by more than five percent according to the ATX spec.
But the ATX specification seems to disagree. According to the spec, full load or "peak loading" allows 10% deviation from the nominal voltage for the 12V rail.
http://www.formfactors.org/developer/specs/Power_Supply_Design_Guide_Desktop_Platform_Rev_1_2.pdf
Also, Q about the power factor correction. It's probably the most difficult topic to understand. In this case, you say the load would be anything that used power. Are you talking about hardware like a GPU or the internals of the PSU like capacitors and such? Also, say the computer is putting load on the PSU. How is there idle current then? -
jossrik There have been quite a few instances in the past where you could get an XFX PSU 550w or so for 40$ or less with rebates. I know compared to more modern PSUs they may not stack up, but they used to be pretty decent. Ya, more often than not, the cheaper the PSU the worse the quality, but you really do need to do your homework.Reply
Budget PSU
https://www.youtube.com/watch?v=Ezk9OA7aKOE -
Aris_Mp The newest ATX spec defines 5% at peak load as well. The 10% is only for the -12V rail which is now optional. The newest ATX spec is confidential (dont know why)Reply -
cats_Paw While I can understand that having a beefy power supply on idle state wont be too efficient, its on loads where you want it as efficient as possible.Reply
Somehow, having a low efficiency under a 65W load is less expensive than low efficiency at 500W load, go figure :D.
-
cats_Paw In all fairness, a PC is not a self-maintenance Robot.Reply
If you want a PC to last a good 10-15 years you need to take care of it:
Clean dust, replace fans when they fail, replace thermalpaste, check your temperatures from time to time, not turn it on-off-on too fast, keep your Hard drives with some spare space and defraged if they are HDDs....
There is quite some work for a PC to keep their form, but its not like a human can lay down in bed eating cheese and drinking cola looking like a model either.
PSUs however have this strange aura of magic around them since some people vastly overestimate what power supply they need (I got a 700W TT one for a load of 320, go figure) and others buy things that are simply bad products, no matter how high the W are.
I did once burn a PC due to a bad PSU (and I even OCed the damn PC, went down in smoke.. I gotta say it was quite fun, but expensive), so I stay on the safe side (I just simply add an extra 20% for 12v rail amps as long as the price of a quality supply is not doubling).