PSUs 101: A Detailed Look Into Power Supplies
The objective of this article is to provide detailed information about the most crucial part of a personal computer (PC) system, its power supply unit. Follow us on this journey into PSU territory and we promise that you will gain valuable knowledge.
Fan Operation And Bearing Types
Fan Operation And Bearing Types
The most crucial components of every fan are its bearing and shaft, at which the fan blade is attached. The bearing is a stationary cylinder inside which the shaft rotates. To provide high reliability and decreased noise output, friction between the shaft and the bearing has to be minimized as much as possible. In most cases, oil is used as a lubricant. However, other methods can be used as well (for instance, Teflon-coated surfaces). If the oil isn't sealed properly inside the bearing, then its quantity will get lower as time passes, increasing friction, which leads to slower fan rotation and increased noise, until the fan breaks down and stops rotating.
There are three basic bearing types used in most PSU fans today:
- Sleeve bearing fans
- Double ball bearing fans
- Fluid dynamic bearing (FDB) and hydro dynamic bearing (HDB) fans
Below, we provide a brief explanation of each bearing type and a reference to its key aspects; we will also provide several photographs of the corresponding bearing types. The photos were obtained by taking several fans apart (some of which are pretty expensive), which were kindly provided by Noctua and Caseking.de.
Sleeve Bearing Fans
The most common fans found in PSUs today use a sleeve bearing, which has a decreased lifespan compared to the other two bearing types mentioned. Fans utilizing a sleeve bearing cost less and deliver low noise output levels, especially at lower speeds, compared to fans that use ball bearings. Lubricant (oil or grease) decreases friction between the bearing's inner surface and the fan's shaft. Once this lubricant evaporates, the fan's life simply ends.
A good quality sleeve bearing fan by Prolimatech, which has proper seals to keep the oil from vaporizing.
Good sleeve bearing fans can last up to 30,000 hours (and even more in some cases) at temperatures reaching 50 degrees C. Their major advantage is an affordable price, which makes them popular in low-cost PSUs. Sleeve bearing fans aren't designed for horizontal mounting since oil inside the bearing moves to one of the shaft's sides, so it doesn't provide uniform friction protection.
Ball Bearing Fans
Higher-quality fans use double ball bearings to reduce friction. This type of fan can be mounted in any orientation without affecting its longevity. This is in contrast to the sleeve bearing fans, which are seriously affected when they are mounted horizontally, as is typically the case with PSUs. The typical lifespan of a good ball bearing fan can reach, and in some cases even exceed, 50,000 hours at very high ambient temperatures. But in most cases, long before the fan stops working, its bearings will start to produce increased noise due to wear. They can become annoying at this point, so users will probably change them long before they completely break down.
A quality double ball bearing fan by ADDA. In the last photo, the two ball bearing rings are depicted.
In general, ball bearing fans have an increased noise output compared to sleeve and fluid dynamic fans, especially at low speeds, when the rotor assembly balance can be affected. Some manufacturers use magnets in order to keep the shaft balanced on all cases and avoid this issue.
Fluid Dynamic And Hydro Dynamic Bearing Fans
Fluid dynamic bearing (FDB) and hydro dynamic bearing (HDB) fans are in essence highly modified versions of the sleeve bearing fans, where the design of the bearing is different and also the lubricant fluid is kept intact with the use of seals (some good-quality sleeve bearing fans also feature seals to keep the oil intact). This means friction is kept at very low levels even after prolonged usage, which can easily exceed 50,000 hours and in some cases reach up to 300,000 hours. The lubricant in FDB fans is pumped up to the whole surface of the bearing through a spiral groove, and this feature makes these fans a better choice for horizontal mounting, since the lubricant covers the whole surface of the shaft in all cases.
An HDB fan by Cougar. In the external side of the bearing, there is only a single groove; however, in the internals, the pattern is different.
The only problem with this type of bearing, besides increased production cost, is that during the start-up phase and until the lubricant is pumped all the way up to the bearing's top, there might be increased friction, meaning that these fans aren't suitable for applications involving lots of starts and stops (in PSUs featuring a semi-passive mode).
Several manufacturers use the same principle of operation in their fans; however, they name it differently due to patent rights of the FDB bearing (which are held my Matsushita). For example, hydro dynamic bearing (HDB) shares enough similarities with FDB. But in all cases, the design of the grooves on the bearing is different from the one used in FDB.
The internal spiral grooves on the bearing of the Cougar Vortex HDB fan, which has a 300,000-hour lifespan, according to its manufacturer.
Current page: Fan Operation And Bearing Types
Prev Page PSU Cooling Next Page Other Bearing Types: SSO, Rifle, HysintGet Tom's Hardware's best news and in-depth reviews, straight to your inbox.
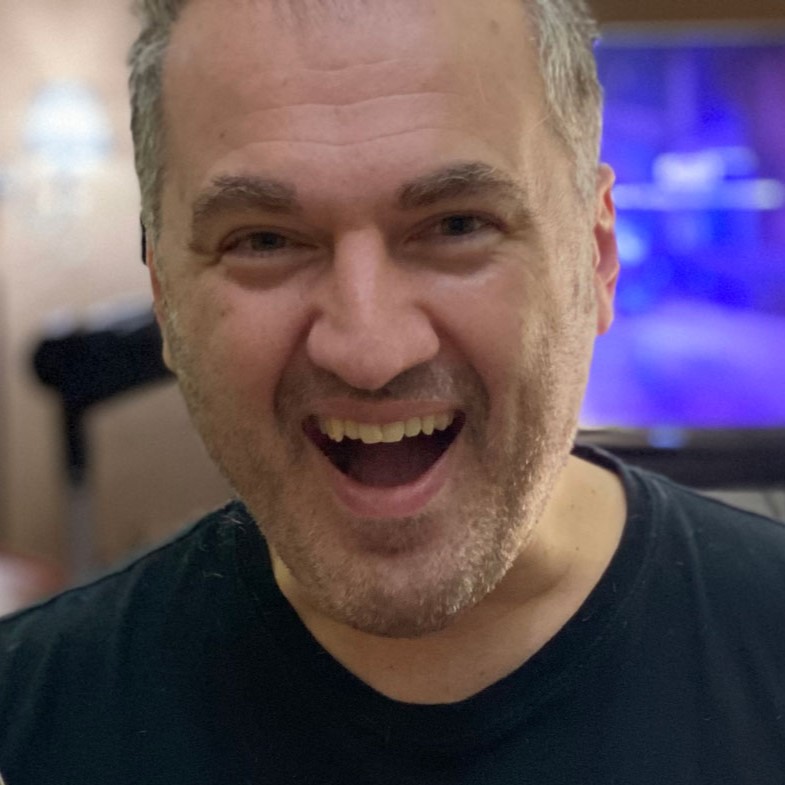
Aris Mpitziopoulos is a contributing editor at Tom's Hardware, covering PSUs.
-
Alexis Shaw In your list of top-tier capacitor manufacturers you missed out on some of the better american and european manufacturers, while these may not be used on many consumer-grade power supplies they are definitely top-tier and if you were to find them you would be happy. I suggest the addition of at least:Reply
Cornell Dubilier (USA)
Illinois Capacitor (Now owned my Cornell Dubilier)
Kemet Corporation (USA)
ELNA (Japan)
EPCOS (TDK company) (Germany)
Vishay (USA)
Würth Elektronik (Germany)
-
Aris_Mp Thank you very much for the list you provided. I am aware of almost all cap brands that you mentioned but unfortunately so far I found none of them inside a desktop/consumer grade PSU. I will think about it however (and also make a research on these cap brands), if I should include them as well inside my list.Reply
-
InvalidError
There is a very high probability you have seen PSUs with several Kemet capacitors in them. You never noticed them simply because SMD capacitors are too small to carry logos, brand name or even value designations.16585466 said:Thank you very much for the list you provided. I am aware of almost all cap brands that you mentioned but unfortunately so far I found none of them inside a desktop/consumer grade PSU.
The other brands are mostly found in specialty applications such as lab instruments, industrial machines and high-end audio. -
Math Geek very interesting read. more in depth than i need to know yet for the most part understandable and with careful reading it did not leave me confused.Reply
nice article. -
TallestJon96 I only read 2/3 of it, but it's a good article.Reply
I basically have committed PC heresy with my cx600m. However I think that I'm in the clear with my 65w CPU and 145w CPU. I'd bet my total power draw is actually below 300w, the supposed highest efficiency point of a PSU.
As a gamer, not a professional, I think it is better to get low power parts, and get a higher rating than you need, rather than get high power parts and high quality PSUs.
Additionally, if you compare power consumption of a typical system from today to one from 5 years ago, power draw is considerably lower, with the exception of certain graphics cards. *cough* 390x *cough* -
powernod I decided to sign up at Tom's forum, and the only reason was to state how excellent is Aris's article!!!Reply
Thanks Aris for this very useful article on behalf of us all who want to learn the basic knowledge for PSUs.
Haven't finished it yet, but i'm very anxious for it !!! -
traumadisaster I'm glad there are people dedicated to this but I'm not. I can't even read all of the chapter titles in this article. I disagree with the importance you place on this and all of the references you made to this being crucial knowledge.Reply
PSU and MB are insignificant to me and I can blindly pick one by reviewing user comments from newegg in about 5 min, and it will last for years. For less than $100 each I'm set for nearly a decade.
CPU and gfx card now that affects fps and is over $1000, actually the most important part to me. -
Alexis Shaw 16589602 said:I'm glad there are people dedicated to this but I'm not. I can't even read all of the chapter titles in this article. I disagree with the importance you place on this and all of the references you made to this being crucial knowledge.
PSU and MB are insignificant to me and I can blindly pick one by reviewing user comments from newegg in about 5 min, and it will last for years. For less than $100 each I'm set for nearly a decade.
CPU and gfx card now that affects fps and is over $1000, actually the most important part to me.
I heartily dissagree, user are not the best way to judge reliability, and a bad powersupply is at fult most of the time there is a hardware issue. Further a power supply should last more than one system build, and in general I keep mine for a decade at a time at least. So an investment in a good power supply is not a waste, and a bad one will kill that precious $1000 GPU or CPU. The demo dart power supply on the motherboard is a similar story, however in general they are of higher quality than a cheap mains supply.
-
Alexis Shaw 16585679 said:
There is a very high probability you have seen PSUs with several Kemet capacitors in them. You never noticed them simply because SMD capacitors are too small to carry logos, brand name or even value designations.16585466 said:Thank you very much for the list you provided. I am aware of almost all cap brands that you mentioned but unfortunately so far I found none of them inside a desktop/consumer grade PSU.
The other brands are mostly found in specialty applications such as lab instruments, industrial machines and high-end audio.
As well as SMT ceramic capacitors, Kemet makes through hole aluminium electrolytic capacitors. These are of high quality, though not as well known as their SMT capacitors. They also make high quality polymer SMT capacitors that are used as bulk capacitors on the power distribution circuitry on laptops and other devices.