PSUs 101: A Detailed Look Into Power Supplies
The objective of this article is to provide detailed information about the most crucial part of a personal computer (PC) system, its power supply unit. Follow us on this journey into PSU territory and we promise that you will gain valuable knowledge.
SMPS Parts Description
Any PSU that powers a PC nowadays utilizes switching power conversion (SPC) technology. The principle of SPC is quite simple, but for those who are still having a hard time understanding it, here's what it comes down to: energy is drawn from the power grid, and then it's chopped with a high-frequency rate into smaller energy packets with the use of some fast switches (FETs), and finally, it's transferred with the help of components like capacitors and inductors. In the end, all of the energy packets are merged, and after some rectification processes, energy flows smoothly from the output.
So, the PSUs in today's PCs use a 100 to 230VAC power stream as input (alternating current, or AC, main input differs according to country or region) and several regulated DC (direct current) outputs (these, of course, are always the same regardless of the country or region). As the switching frequency rises, the size of the energy packets gets smaller, thereby reducing the size of the components (inductors and capacitors) that store and transfer them. Any PSU that utilizes SPC is called a switching mode power supply, or SMPS, and with the abbreviation PSU in PCs, we assume that it is also an SMPS.
The figure above shows the block diagram of an SMPS used in a contemporary system. The first stage is the EMI/transient filter, followed by the active power correction factor (APFC) converter, the main switchers and the power transformer, and finally the output rectification and filtering stage. Between the DC outputs and the main switchers is a voltage feedback loop that constantly checks the output voltages (rails) and makes the necessary corrections by controlling the duty cycle of the main switchers. The pulse-width modulated (PWM) control is implemented by an integrated circuit (IC) that, in some cases (mostly in low-end PSUs) also controls the APFC switchers. However, in some resonant topologies, PWM is used only at light loads and forward modulation (FM) is utilized for higher loads. So, for the APFC switchers, an independent PWM controller has to be used. The part of an SMPS before the power transformer is called the primary side, and the part after it is the secondary side. These two sides must be isolated, but there must still be a type of connection between them in order to pass feedback signals. Usually, optoisolators or optocouplers are used for this purpose.
The two major advantages an SMPS has over a linear power supply (or linear regulator) is that its design is much smaller and lighter, and more efficient. The best SMPS designs can easily exceed 90 percent efficiency and, in some cases, reach up to 95 percent efficiency with 230VAC input. On the other hand, the most significant drawbacks of an SMPS are its complexity and its production of EMI, or radio frequency interference (RFI), that requires an EMI filter (also called the "transient filtering stage" because its role is twofold) and RFI shielding.
In the following sections, we will analyze all of the individual stages of an SMPS, or PSU as we call it from now on.
Current page: SMPS Parts Description
Prev Page SMPS Vs. Linear Regulators Next Page EMI/Transient Filtering StageGet Tom's Hardware's best news and in-depth reviews, straight to your inbox.
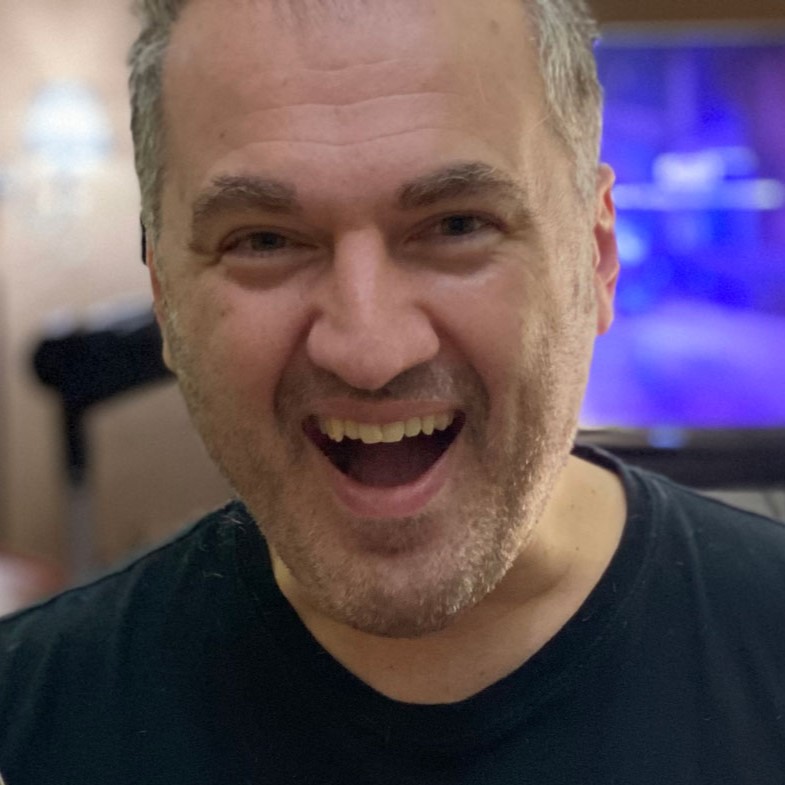
Aris Mpitziopoulos is a contributing editor at Tom's Hardware, covering PSUs.
-
Alexis Shaw In your list of top-tier capacitor manufacturers you missed out on some of the better american and european manufacturers, while these may not be used on many consumer-grade power supplies they are definitely top-tier and if you were to find them you would be happy. I suggest the addition of at least:Reply
Cornell Dubilier (USA)
Illinois Capacitor (Now owned my Cornell Dubilier)
Kemet Corporation (USA)
ELNA (Japan)
EPCOS (TDK company) (Germany)
Vishay (USA)
Würth Elektronik (Germany)
-
Aris_Mp Thank you very much for the list you provided. I am aware of almost all cap brands that you mentioned but unfortunately so far I found none of them inside a desktop/consumer grade PSU. I will think about it however (and also make a research on these cap brands), if I should include them as well inside my list.Reply
-
InvalidError
There is a very high probability you have seen PSUs with several Kemet capacitors in them. You never noticed them simply because SMD capacitors are too small to carry logos, brand name or even value designations.16585466 said:Thank you very much for the list you provided. I am aware of almost all cap brands that you mentioned but unfortunately so far I found none of them inside a desktop/consumer grade PSU.
The other brands are mostly found in specialty applications such as lab instruments, industrial machines and high-end audio. -
Math Geek very interesting read. more in depth than i need to know yet for the most part understandable and with careful reading it did not leave me confused.Reply
nice article. -
TallestJon96 I only read 2/3 of it, but it's a good article.Reply
I basically have committed PC heresy with my cx600m. However I think that I'm in the clear with my 65w CPU and 145w CPU. I'd bet my total power draw is actually below 300w, the supposed highest efficiency point of a PSU.
As a gamer, not a professional, I think it is better to get low power parts, and get a higher rating than you need, rather than get high power parts and high quality PSUs.
Additionally, if you compare power consumption of a typical system from today to one from 5 years ago, power draw is considerably lower, with the exception of certain graphics cards. *cough* 390x *cough* -
powernod I decided to sign up at Tom's forum, and the only reason was to state how excellent is Aris's article!!!Reply
Thanks Aris for this very useful article on behalf of us all who want to learn the basic knowledge for PSUs.
Haven't finished it yet, but i'm very anxious for it !!! -
traumadisaster I'm glad there are people dedicated to this but I'm not. I can't even read all of the chapter titles in this article. I disagree with the importance you place on this and all of the references you made to this being crucial knowledge.Reply
PSU and MB are insignificant to me and I can blindly pick one by reviewing user comments from newegg in about 5 min, and it will last for years. For less than $100 each I'm set for nearly a decade.
CPU and gfx card now that affects fps and is over $1000, actually the most important part to me. -
Alexis Shaw 16589602 said:I'm glad there are people dedicated to this but I'm not. I can't even read all of the chapter titles in this article. I disagree with the importance you place on this and all of the references you made to this being crucial knowledge.
PSU and MB are insignificant to me and I can blindly pick one by reviewing user comments from newegg in about 5 min, and it will last for years. For less than $100 each I'm set for nearly a decade.
CPU and gfx card now that affects fps and is over $1000, actually the most important part to me.
I heartily dissagree, user are not the best way to judge reliability, and a bad powersupply is at fult most of the time there is a hardware issue. Further a power supply should last more than one system build, and in general I keep mine for a decade at a time at least. So an investment in a good power supply is not a waste, and a bad one will kill that precious $1000 GPU or CPU. The demo dart power supply on the motherboard is a similar story, however in general they are of higher quality than a cheap mains supply.
-
Alexis Shaw 16585679 said:
There is a very high probability you have seen PSUs with several Kemet capacitors in them. You never noticed them simply because SMD capacitors are too small to carry logos, brand name or even value designations.16585466 said:Thank you very much for the list you provided. I am aware of almost all cap brands that you mentioned but unfortunately so far I found none of them inside a desktop/consumer grade PSU.
The other brands are mostly found in specialty applications such as lab instruments, industrial machines and high-end audio.
As well as SMT ceramic capacitors, Kemet makes through hole aluminium electrolytic capacitors. These are of high quality, though not as well known as their SMT capacitors. They also make high quality polymer SMT capacitors that are used as bulk capacitors on the power distribution circuitry on laptops and other devices.